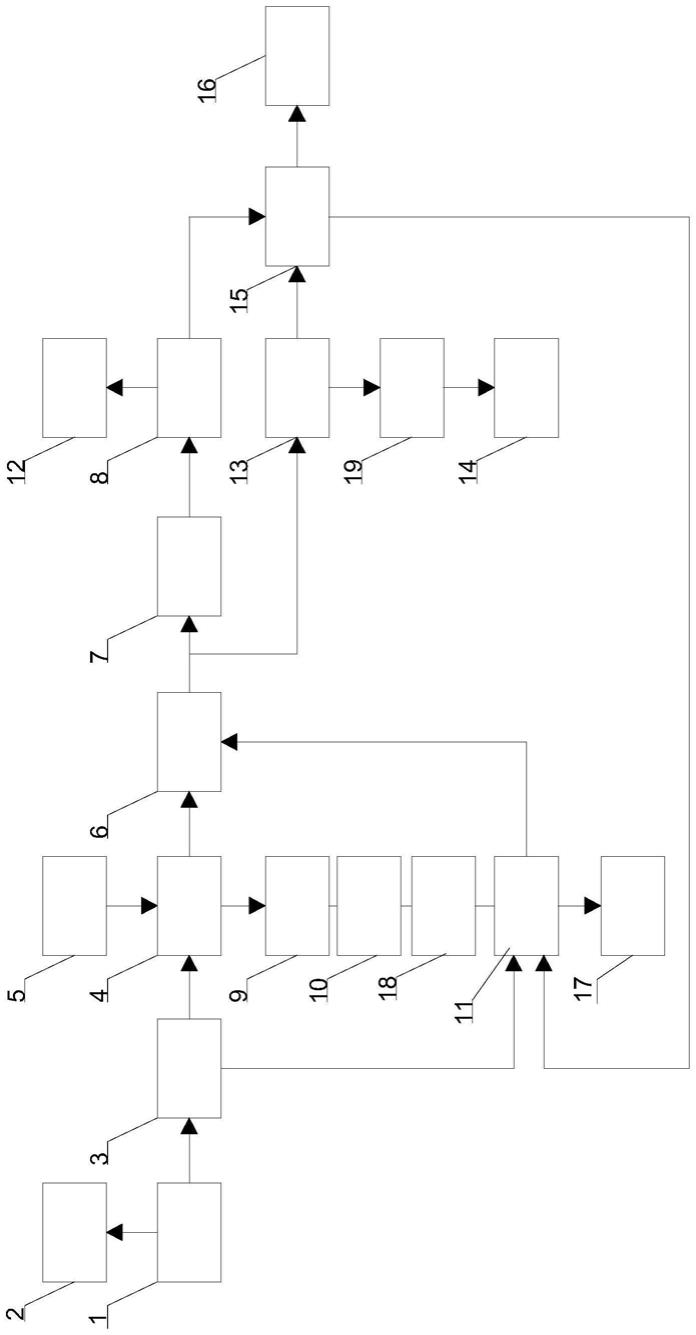
1.本发明属于煤气化技术领域,具体涉及一种煤气化废渣资源化利用的生产装置以及生产方法。
背景技术:
2.在“碳中和”“碳达峰”的大背景下,每一份的用煤指标都弥足珍贵,节煤、节能、减排是未来煤化工发展的大趋势。在时代的大背景下大多煤化工企业还存在用煤损失、用煤浪费等现象,煤化工企业以煤为原料或采用水煤浆工艺或采用粉煤工艺得到一氧化碳、氢气、二氧化碳等工艺气,制得工艺气的同时,气化反应器(气化炉)排出大量的废渣,废渣中还含有10
‑
45%的残碳。上述废渣在生产过程中被直接外排,造成了用煤浪费的问题。
技术实现要素:
3.本发明的目的在于克服现有技术中的缺陷,而提供一种结构简单、设计合理、并以二氧化碳作为气化剂,实现废渣中的残碳完全反应,不仅有效的回收了废渣中的残碳避免了原料煤的损失,且提高了co工艺气量的煤气化废渣资源化利用的生产装置以及生产方法。
4.本发明的目的是这样实现的:
5.一种煤气化废渣资源化利用的生产装置,包括空气分离装置,二氧化碳管网,空气分离装置分别于氮气管网和氧气管网,所述氧气管网分别与第一气化炉和第二气化炉的气相进口相连;所述第一气化炉的固体进口与气化原料储罐相连,第一气化炉的固体出口通过废渣处理单元与第二气化炉相连;所述第一气化炉的气相出口与工艺气处理单元相连;所述二氧化碳管网与第二气化炉的气相进口相连;第二气化炉的气相出口与工艺气处理单元相连。
6.优选的,所述废渣处理单元包括与第一气化炉的固体出口相连的集渣罐,集渣罐通过废渣烘干机和粉碎机与第二气化炉的固体进口相连;第二气化炉的固体出口与无碳废渣储罐相连。
7.优选的,所述工艺气处理单元包括工艺气分配站,工艺气分配站通过一氧化碳变换装置与第一低温甲醇洗装置相连,第一低温甲醇洗装置的分别与氢气管网和二氧化碳管网相连。
8.优选的,所述工艺气分配站和一氧化碳变换装置之间设有三通,三通的第三端与第二低温甲醇洗装置相连,第二低温甲醇洗装置分别与一氧化碳管网和二氧化碳管网相连;第二低温甲醇洗装置和一氧化碳管网之间设有一氧化碳提纯装置。
9.优选的,所述二氧化碳管网与二氧化碳用户配给站相连。
10.优选的,所述第二气化炉的气相出口与工艺气分配站的气相进口相连。
11.优选的,所述第一气化炉和第二气化炉为水煤浆气化炉或粉煤气化炉。
12.一种煤气化废渣资源化利用的生产装置的生产方法,包括如下步骤:
13.步骤1:空气分离装置产出的氮气进入氮气管网内,其产出的氧气进入氧气管网中;所述氧气纯度大于99.5%;所述氧气管网分别向第一气化炉和第二气化炉供给氧气;
14.步骤2:气化原料储罐中的气化原料进入第一气化炉内和步骤1中进入的氧气充分反应得到的工艺气进入工艺气分配站内;
15.步骤3:第一气化炉内充分反应后的炉渣进入集渣罐内,所述的炉渣固废碳含量10
‑
45%,水分含量15
‑
40%;
16.步骤4:集渣罐内的炉渣依次进入废渣烘干机和粉碎机内进行烘干及粉碎,烘干及粉碎后的废渣含水率小于0.5%,粒径小于200μm;
17.步骤5:烘干及粉碎后的废渣进入第二气化炉中,和来自氧气管网3的氧气以及来自二氧化碳管网15的二氧化碳充分反应生成一氧化碳,并将其送入工艺气分配站中;上述在第二气化炉内充分反应后的废渣为无碳废渣,无碳废渣通过第二气化炉的固体出口进入到无碳废渣储罐内;所述无碳废渣的碳含量小于1%;
18.步骤6:工艺气分配站中的一部分工艺气进入一氧化碳变换装置中将co转化为氢气,并进入第一低温甲醇洗装置脱除其中的酸性气后进入氢气管网,第一低温甲醇洗装置中解析的二氧化碳进入二氧化碳管网中;
19.步骤7:工艺气分配站中的另一部分工艺气在第二低温甲醇洗装置中脱除其中的酸性气后通过一氧化碳提纯装置进行提纯后进入一氧化碳管网中;第二低温甲醇洗装置解析的二氧化碳进入二氧化碳管网;
20.步骤8:二氧化碳管网分别向第二气化炉和二氧化碳用户配给站供给二氧化碳。
21.优选的,所述步骤2中第一气化炉的操作温度为1000
‑
1500℃。
22.优选的,所述步骤5中第二气化炉的操作温度为850
‑
1500℃。
23.按照上述方案制成的一种煤气化废渣资源化利用的生产装置以及生产方法,该装置以及方法利用了空分装置中产生的氧气分别进入第一气化炉和第二气化炉作为助燃剂,氧气进入第一气化炉中与来自气化原料储罐中的水、煤等原料发生充分反应,不仅为工艺气处理单元的运行奠定了基础,同时还为第二气化炉提供了原料;炉渣在进入第二气化炉前还进行了烘干和粉碎的预处理,以达到对残碳进行充分回收的特点,在第二气化炉中二氧化碳作为气化剂,将废渣中的残碳完全反应得到co工艺气;具有结构简单、设计合理、并以二氧化碳作为气化剂,实现废渣中的残碳完全反应,不仅有效的回收了废渣中的残碳避免了原料煤的损失,且提高了co工艺气量的优点。
附图说明
24.图1为本发明的结构示意图。
25.上图中:1、空气分离装置;2、氮气管网;3、氧气管网;4、第一气化炉;5、气化原料储罐;6、工艺气分配站;7、一氧化碳变换装置;8、第一低温甲醇洗装置;9、集渣罐;10、废渣烘干机;11、第二气化炉;12、氢气管网;13、第二低温甲醇洗装置;14、一氧化碳管网;15、二氧化碳管网;16、二氧化碳用户配给站;17、无碳废渣储罐;18、粉碎机;19、一氧化碳提纯装置。
具体实施方式
26.为了对本发明的技术特征、目的和效果有更加清楚的理解,现对照附图说明本发
明的具体实施方式,在各图中相同的标号表示相同的部件。为使图面简洁,各图中只示意性地表示出了与发明相关的部分,它们并不代表其作为产品的实际结构。
27.如图1所示,本发明为一种煤气化废渣资源化利用的生产装置以及生产方法,该生产装置包括空气分离装置1,二氧化碳管网15,空气分离装置1分别于氮气管网2和氧气管网3,所述氧气管网3分别与第一气化炉4和第二气化炉11的气相进口相连;所述第一气化炉4的固体进口与气化原料储罐5相连,第一气化炉4的固体出口通过废渣处理单元与第二气化炉11相连;所述第一气化炉4的气相出口与工艺气处理单元相连;所述二氧化碳管网15与第二气化炉11的气相进口相连;第二气化炉11的气相出口与工艺气处理单元相连。本发明中氧气管网3为第一气化炉4和第二气化炉11提供氧气,气化原料储罐5为第一气化炉4提供水、煤等原料与氧气充分反应得到工艺气,其废渣在第二气化炉11内以二氧化碳为气化剂,进一步的充分反应生成一氧化碳;上述过程中不仅提高了煤的利用率,还增加了一氧化碳的产量;上述第一气化炉4制备的工艺气以及第二气化炉11生成的一氧化碳进入工艺气处理单元中进行后续处理。
28.进一步地,所述废渣处理单元包括与第一气化炉4的固体出口相连的集渣罐9,集渣罐9通过废渣烘干机10和粉碎机18与第二气化炉11的固体进口相连;第二气化炉11的固体出口与无碳废渣储罐17相连。本发明中的废渣处理单元是对废渣进行烘干以及粉碎的预处理过程中,该预处理过程中不仅能够满足第二气化炉11的反应需要,还能够提高煤的回收率,具体的是通过集渣罐9对第一气化炉4内产生的废渣进行收集,并通过废渣烘干机10对其进行烘干,在烘干的基础上通过粉碎机对废渣进行粉碎,上述粉碎的过程中能够在对废渣进行粉碎的同时实现了煤粉和炉渣粉在干燥的情况下进行均匀混合,该均匀混合为第二气化炉11中的充分反应,并尽可能的为提高煤粉反应效率奠定了基础。
29.进一步地,所述工艺气处理单元包括工艺气分配站6,工艺气分配站6通过一氧化碳变换装置7与第一低温甲醇洗装置8相连,第一低温甲醇洗装置8的分别与氢气管网12和二氧化碳管网15相连。本发明中的工艺气分配站6用于向第一低温甲醇洗装置8和第二低温甲醇洗装置13供给工艺气,一部分工艺气通过一氧化碳变换装置7中进行变换,在第一低温甲醇洗装置8中脱除其中的酸性气后进入使氢气进入氢气管网12中,在对第一低温甲醇洗装置8进行解析时产生二氧化碳并进入二氧化碳管网15内;
30.进一步地,所述工艺气分配站6和一氧化碳变换装置7之间设有三通,三通的第三端与第二低温甲醇洗装置13相连,第二低温甲醇洗装置13分别与一氧化碳管网14和二氧化碳管网15相连;第二低温甲醇洗装置13和一氧化碳管网14之间设有一氧化碳提纯装置19。一部分工艺气进入第二低温甲醇洗装置13中脱除其中的酸性气后进入使一氧化碳进入一氧化碳提纯装置19进行提纯后进入一氧化碳管网14中,在对第二低温甲醇洗装置13进行解析时产生二氧化碳并进入二氧化碳管网15内。
31.进一步地,所述二氧化碳管网15与二氧化碳用户配给站16相连。本发明中所述的二氧化碳管网15主要用于为二氧化碳用户配给站16供给二氧化碳,并通过二氧化碳用户配给站16向个企业用户输送二氧化碳。
32.进一步地,所述第二气化炉11的气相出口与工艺气分配站6的气相进口相连。通过上述设置能够使第二气化炉11内产生的一氧化碳进入工艺气分配站6内进行分配再处理。
33.进一步地,所述第一气化炉4和第二气化炉11为水煤浆气化炉或粉煤气化炉。
34.一种煤气化废渣资源化利用的生产装置的生产方法,包括如下步骤:
35.步骤1:空气分离装置1产出的氮气进入氮气管网2内,其产出的氧气进入氧气管网3中;所述氧气纯度大于99.5%;所述氧气管网3分别向第一气化炉4和第二气化炉11供给氧气;
36.步骤2:气化原料储罐5中的气化原料进入第一气化炉4内和步骤1中进入的氧气充分反应得到的工艺气进入工艺气分配站6内;
37.步骤3:第一气化炉4内充分反应后的炉渣进入集渣罐9内,所述的炉渣固废碳含量10
‑
45%,水分含量15
‑
40%;
38.步骤4:集渣罐9内的炉渣依次进入废渣烘干机10和粉碎机18内进行烘干及粉碎,烘干及粉碎后的废渣含水率小于0.5%,粒径小于200μm;
39.步骤5:烘干及粉碎后的废渣进入第二气化炉11中,和来自氧气管网3的氧气以及来自二氧化碳管网15的二氧化碳充分反应生成一氧化碳,并将其送入工艺气分配站6中;上述在第二气化炉11内充分反应后的废渣为无碳废渣,无碳废渣通过第二气化炉11的固体出口进入到无碳废渣储罐17内;所述无碳废渣的碳含量小于1%;
40.步骤6:工艺气分配站6中的一部分工艺气进入一氧化碳变换装置7中将co转化为氢气,并进入第一低温甲醇洗装置8脱除其中的酸性气后进入氢气管网12,第一低温甲醇洗装置8中解析的二氧化碳进入二氧化碳管网15中;
41.步骤7:工艺气分配站6中的另一部分工艺气在第二低温甲醇洗装置13中脱除其中的酸性气后通过一氧化碳提纯装置19进行提纯后进入一氧化碳管网14中;第二低温甲醇洗装置13解析的二氧化碳进入二氧化碳管网15;
42.步骤8:二氧化碳管网15分别向第二气化炉11和二氧化碳用户配给站16供给二氧化碳。
43.进一步地,所述步骤2中第一气化炉4的操作温度为1000
‑
1500℃。
44.进一步地,所述步骤5中第二气化炉11的操作温度为850
‑
1500℃。
45.本发明是通过第二气化炉11对第一气化炉4中排出的炉渣进行再次燃烧以达到提高煤利用率的目的,同时为了进一步地提高煤利用率以及节省成本,本发明通过烘干和粉碎的预处理装置,并配合自身系统中的氧气与二氧化碳进一步制成一氧化碳;上述装置及工艺不仅能够提高煤的利用率,减少煤的损耗,同时能够提高工艺气的量;尤其是本发明中通过对炉渣的预处理,使煤粉和炉渣粉在干燥的情况下进行均匀混合,上述的均匀混合为在第二气化炉11内实现充分反应,以及提高煤粉利用率奠定了基础。
46.为了更加详细的解释本发明,现结合实施例对本发明做进一步阐述。具体实施例如下:
47.实施例1
48.一种煤气化废渣资源化利用的生产装置,包括空气分离装置1,二氧化碳管网15,空气分离装置1分别于氮气管网2和氧气管网3,所述氧气管网3分别与第一气化炉4和第二气化炉11的气相进口相连;所述第一气化炉4的固体进口与气化原料储罐5相连,第一气化炉4的固体出口通过废渣处理单元与第二气化炉11相连;所述第一气化炉4的气相出口与工艺气处理单元相连;所述二氧化碳管网15与第二气化炉11的气相进口相连;第二气化炉11的气相出口与工艺气处理单元相连。所述废渣处理单元包括与第一气化炉4的固体出口相
连的集渣罐9,集渣罐9通过废渣烘干机10和粉碎机18与第二气化炉11的固体进口相连;第二气化炉11的固体出口与无碳废渣储罐17相连。所述工艺气处理单元包括工艺气分配站6,工艺气分配站6通过一氧化碳变换装置7与第一低温甲醇洗装置8相连,第一低温甲醇洗装置8的分别与氢气管网12和二氧化碳管网15相连。所述工艺气分配站6和一氧化碳变换装置7之间设有三通,三通的第三端与第二低温甲醇洗装置13相连,第二低温甲醇洗装置13分别与一氧化碳管网14和二氧化碳管网15相连;第二低温甲醇洗装置13和一氧化碳管网14之间设有一氧化碳提纯装置19。所述二氧化碳管网15与二氧化碳用户配给站16相连。所述第二气化炉11的气相出口与工艺气分配站6的气相进口相连。所述第一气化炉4和第二气化炉11为水煤浆气化炉或粉煤气化炉。
49.一种煤气化废渣资源化利用的生产装置的生产方法,包括如下步骤:
50.步骤1:空气分离装置1产出的氮气进入氮气管网2内,其产出的氧气进入氧气管网3中;所述氧气纯度大于99.5%;所述氧气管网3分别向第一气化炉4和第二气化炉11供给氧气;
51.步骤2:气化原料储罐5中的气化原料进入第一气化炉4内和步骤1中进入的氧气充分反应得到的工艺气进入工艺气分配站6内;
52.步骤3:第一气化炉4内充分反应后的炉渣进入集渣罐9内,所述的炉渣固废碳含量10
‑
45%,水分含量15
‑
40%;
53.步骤4:集渣罐9内的炉渣依次进入废渣烘干机10和粉碎机18内进行烘干及粉碎,烘干及粉碎后的废渣含水率为0.4%,粒径为180μm;
54.步骤5:烘干及粉碎后的废渣进入第二气化炉11中,和来自氧气管网3的氧气以及来自二氧化碳管网15的二氧化碳充分反应生成一氧化碳,并将其送入工艺气分配站6中;上述在第二气化炉11内充分反应后的废渣为无碳废渣,无碳废渣通过第二气化炉11的固体出口进入到无碳废渣储罐17内;所述无碳废渣的碳含量为0.8%;
55.步骤6:工艺气分配站6中的一部分工艺气进入一氧化碳变换装置7中将co转化为氢气,并进入第一低温甲醇洗装置8脱除其中的酸性气后进入氢气管网12,第一低温甲醇洗装置8中解析的二氧化碳进入二氧化碳管网15中;
56.步骤7:工艺气分配站6中的另一部分工艺气在第二低温甲醇洗装置13中脱除其中的酸性气后通过一氧化碳提纯装置19进行提纯后进入一氧化碳管网14中;第二低温甲醇洗装置13解析的二氧化碳进入二氧化碳管网15;
57.步骤8:二氧化碳管网15分别向第二气化炉11和二氧化碳用户配给站16供给二氧化碳。
58.所述步骤2中第一气化炉4的操作温度为1000℃。所述步骤5中第二气化炉11的操作温度为850℃。
59.实施例2
60.一种煤气化废渣资源化利用的生产装置,包括空气分离装置1,二氧化碳管网15,空气分离装置1分别于氮气管网2和氧气管网3,所述氧气管网3分别与第一气化炉4和第二气化炉11的气相进口相连;所述第一气化炉4的固体进口与气化原料储罐5相连,第一气化炉4的固体出口通过废渣处理单元与第二气化炉11相连;所述第一气化炉4的气相出口与工艺气处理单元相连;所述二氧化碳管网15与第二气化炉11的气相进口相连;第二气化炉11
的气相出口与工艺气处理单元相连。所述废渣处理单元包括与第一气化炉4的固体出口相连的集渣罐9,集渣罐9通过废渣烘干机10和粉碎机18与第二气化炉11的固体进口相连;第二气化炉11的固体出口与无碳废渣储罐17相连。所述工艺气处理单元包括工艺气分配站6,工艺气分配站6通过一氧化碳变换装置7与第一低温甲醇洗装置8相连,第一低温甲醇洗装置8的分别与氢气管网12和二氧化碳管网15相连。所述工艺气分配站6和一氧化碳变换装置7之间设有三通,三通的第三端与第二低温甲醇洗装置13相连,第二低温甲醇洗装置13分别与一氧化碳管网14和二氧化碳管网15相连;第二低温甲醇洗装置13和一氧化碳管网14之间设有一氧化碳提纯装置19。所述二氧化碳管网15与二氧化碳用户配给站16相连。所述第二气化炉11的气相出口与工艺气分配站6的气相进口相连。所述第一气化炉4和第二气化炉11为水煤浆气化炉或粉煤气化炉。
61.一种煤气化废渣资源化利用的生产装置的生产方法,包括如下步骤:
62.步骤1:空气分离装置1产出的氮气进入氮气管网2内,其产出的氧气进入氧气管网3中;所述氧气纯度大于99.5%;所述氧气管网3分别向第一气化炉4和第二气化炉11供给氧气;
63.步骤2:气化原料储罐5中的气化原料进入第一气化炉4内和步骤1中进入的氧气充分反应得到的工艺气进入工艺气分配站6内;
64.步骤3:第一气化炉4内充分反应后的炉渣进入集渣罐9内,所述的炉渣固废碳含量10
‑
45%,水分含量15
‑
40%;
65.步骤4:集渣罐9内的炉渣依次进入废渣烘干机10和粉碎机18内进行烘干及粉碎,烘干及粉碎后的废渣含水率为0.45%,粒径为155μm;
66.步骤5:烘干及粉碎后的废渣进入第二气化炉11中,和来自氧气管网3的氧气以及来自二氧化碳管网15的二氧化碳充分反应生成一氧化碳,并将其送入工艺气分配站6中;上述在第二气化炉11内充分反应后的废渣为无碳废渣,无碳废渣通过第二气化炉11的固体出口进入到无碳废渣储罐17内;所述无碳废渣的碳含量为0.9%;
67.步骤6:工艺气分配站6中的一部分工艺气进入一氧化碳变换装置7中将co转化为氢气,并进入第一低温甲醇洗装置8脱除其中的酸性气后进入氢气管网12,第一低温甲醇洗装置8中解析的二氧化碳进入二氧化碳管网15中;
68.步骤7:工艺气分配站6中的另一部分工艺气在第二低温甲醇洗装置13中脱除其中的酸性气后通过一氧化碳提纯装置19进行提纯后进入一氧化碳管网14中;第二低温甲醇洗装置13解析的二氧化碳进入二氧化碳管网15;
69.步骤8:二氧化碳管网15分别向第二气化炉11和二氧化碳用户配给站16供给二氧化碳。
70.所述步骤2中第一气化炉4的操作温度为1500℃。所述步骤5中第二气化炉11的操作温度为1500℃。
71.实施例3
72.一种煤气化废渣资源化利用的生产装置,包括空气分离装置1,二氧化碳管网15,空气分离装置1分别于氮气管网2和氧气管网3,所述氧气管网3分别与第一气化炉4和第二气化炉11的气相进口相连;所述第一气化炉4的固体进口与气化原料储罐5相连,第一气化炉4的固体出口通过废渣处理单元与第二气化炉11相连;所述第一气化炉4的气相出口与工
艺气处理单元相连;所述二氧化碳管网15与第二气化炉11的气相进口相连;第二气化炉11的气相出口与工艺气处理单元相连。所述废渣处理单元包括与第一气化炉4的固体出口相连的集渣罐9,集渣罐9通过废渣烘干机10和粉碎机18与第二气化炉11的固体进口相连;第二气化炉11的固体出口与无碳废渣储罐17相连。所述工艺气处理单元包括工艺气分配站6,工艺气分配站6通过一氧化碳变换装置7与第一低温甲醇洗装置8相连,第一低温甲醇洗装置8的分别与氢气管网12和二氧化碳管网15相连。所述工艺气分配站6和一氧化碳变换装置7之间设有三通,三通的第三端与第二低温甲醇洗装置13相连,第二低温甲醇洗装置13分别与一氧化碳管网14和二氧化碳管网15相连;第二低温甲醇洗装置13和一氧化碳管网14之间设有一氧化碳提纯装置19。所述二氧化碳管网15与二氧化碳用户配给站16相连。所述第二气化炉11的气相出口与工艺气分配站6的气相进口相连。所述第一气化炉4和第二气化炉11为水煤浆气化炉或粉煤气化炉。
73.一种煤气化废渣资源化利用的生产装置的生产方法,包括如下步骤:
74.步骤1:空气分离装置1产出的氮气进入氮气管网2内,其产出的氧气进入氧气管网3中;所述氧气纯度大于99.5%;所述氧气管网3分别向第一气化炉4和第二气化炉11供给氧气;
75.步骤2:气化原料储罐5中的气化原料进入第一气化炉4内和步骤1中进入的氧气充分反应得到的工艺气进入工艺气分配站6内;
76.步骤3:第一气化炉4内充分反应后的炉渣进入集渣罐9内,所述的炉渣固废碳含量10
‑
45%,水分含量15
‑
40%;
77.步骤4:集渣罐9内的炉渣依次进入废渣烘干机10和粉碎机18内进行烘干及粉碎,烘干及粉碎后的废渣含水率为0.38%,粒径为165μm;
78.步骤5:烘干及粉碎后的废渣进入第二气化炉11中,和来自氧气管网3的氧气以及来自二氧化碳管网15的二氧化碳充分反应生成一氧化碳,并将其送入工艺气分配站6中;上述在第二气化炉11内充分反应后的废渣为无碳废渣,无碳废渣通过第二气化炉11的固体出口进入到无碳废渣储罐17内;所述无碳废渣的碳含量小于1%;
79.步骤6:工艺气分配站6中的一部分工艺气进入一氧化碳变换装置7中将co转化为氢气,并进入第一低温甲醇洗装置8脱除其中的酸性气后进入氢气管网12,第一低温甲醇洗装置8中解析的二氧化碳进入二氧化碳管网15中;
80.步骤7:工艺气分配站6中的另一部分工艺气在第二低温甲醇洗装置13中脱除其中的酸性气后通过一氧化碳提纯装置19进行提纯后进入一氧化碳管网14中;第二低温甲醇洗装置13解析的二氧化碳进入二氧化碳管网15;
81.步骤8:二氧化碳管网15分别向第二气化炉11和二氧化碳用户配给站16供给二氧化碳。
82.所述步骤2中第一气化炉4的操作温度为1250℃。所述步骤5中第二气化炉11的操作温度为1175℃。
83.实验例
84.以日投煤3000t的气化炉为例,日排干基废渣450
‑
600t,残碳率15
‑
40%;以本发明的实施例三为基础,实施本发明后日排干基废渣总量降低10
‑
35%,回收利用残碳67.5
‑
240吨/天,日增产有效气(co)252000nm3‑
896000nm3。
85.在本发明的描述中,需要说明的是,除非另有明确的规定和限定,术语“连接”、“相连”等等应做广义理解,例如,可以是固定连接,一体地连接,也可以是可拆卸连接;也可以是两个元件内部的连通;可以是直接相连,也可以通过中间媒介间接相连,对于本领域的普通技术人员而言,可以根据具体情况理解上述术语在本发明中的具体含义。上文的示例仅仅是针对本发明的可行性实施方式的具体说明,它们并非用以限制本发明的保护范围,凡未脱离本发明技艺精神所作的等效实施方式、变更和改造均应包含在本发明的保护范围之内。