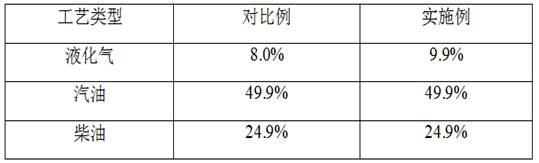
1.本实用新型属于甲醇回收设备技术领域,具体涉及一种资源化回收污甲醇的装置。
背景技术:
2.在mtbe制备工艺中,以甲醇和异丁烯为原料生产mtbe,会产生大量含杂质的污甲醇,先经过甲醇萃取塔,除去不溶于水的杂质后再进入甲醇回收塔,经过甲醇回收塔出来的污甲醇含有酚类,硫类等杂质,如果再次进入mtbe装置会毒害催化剂,若排放则造成极大的浪费,且污染环境。
技术实现要素:
3.有鉴于此,有必要提供一种资源化回收污甲醇的装置以解决污甲醇含有酚类,硫类等杂质,如果再次进入mtbe装置会毒害催化剂,若排放则造成极大的浪费,且污染环境。
4.一种资源化回收污甲醇的装置,该装置包括:提升管反应器,用于进行重油催化裂化反应,所述提升管反应器底部设置有预提升气进料管和重油入口管,所述预提升气进料管设置有甲醇进料管,所述甲醇进料管设置雾化组件,所述雾化组件用于对污甲醇进行雾化。
5.优选的,所述预提升气进料管还设置有干气进料管和蒸气进料管,所述甲醇进料管位于干气进料管和蒸气进料管上方。
6.优选的,所述干气进料管倾斜设置且与蒸气进料管形成锐角,所述蒸气进料管和干气进料管通过比例控制器控制。
7.优选的,所述预提升气进料管的拐角为弧形拐角,所述干气进料管设置于预提升气进料管的弧形拐角外壁上。
8.优选的,所述提升管反应器的重油入口管、甲醇进料管、干气进料管和蒸气进料管均设置有流量控制阀。
9.优选的,所述催化裂化装置还包括沉降器,所述沉降器用于气固分离,设置有油剂混合物入口、油气出口和催化剂出口,所述沉降器的油剂混合物入口连接所述提升管反应器的油剂混合物出口。
10.优选的,所述催化裂化装置还包括再生器,所述再生器用于催化剂再生,设置在沉降器下部,所述再生器的催化剂入口连接沉降器的催化剂出口,所述再生器的催化剂出口连接提升管反应器的催化剂入口。
11.优选的,所述再生器下端设置催化剂输送管,所述催化剂输送管上设置有控制阀。
12.本实用新型采用上述技术方案,其有益效果在于:
13.将污甲醇通入重油催化裂化装置中,污甲醇先经过雾化,然后进入提升管反应器中,此同时重油也通入提升管反应器中,在提升管反应器中发生反应,反应生成的油气中液化气含量大幅度提升。此过程使90%~95%的污甲醇转换为液化气,避免造成浪费,污染环境,
既将污甲醇回收利用又提高了催化裂化反应中液化气的收率,避免污甲醇用于mtbe反应造成催化剂中毒,大幅节约成本,产生了较大的经济收益。
附图说明
14.图1为资源化回收污甲醇的装置的结构示意图。
15.图中:提升管反应器100、沉降器200、再生器300、预提升气进料管110、催化剂输送管310、甲醇进料管111、干气进料管112、蒸气进料管113。
具体实施方式
16.为了更清楚地说明本实用新型实施例的技术方案,下面将对实施例中所需要使用的附图作简单的介绍,显而易见地,下面描述中的附图是本实用新型的一些实施例,对于本领域普通技术人员来讲,在不付出创造性劳动的前提下,还可以根据这些附图获得其他的附图。
17.请参看图1一种资源化回收污甲醇的装置,包括提升管反应器100,用于重油催化裂化反应,所述提升管反应器100底部设置有预提升气进料管110和重油入口管,所述预提升气进料管110设置有甲醇进料管111,所述甲醇进料管111为雾化组件,所述雾化组件用于对甲醇进行雾化。
18.污甲醇自甲醇进料管111进入预提升气进料管110中,形成雾化污甲醇,雾化污甲醇在预提升气的带动下进入提升管反应器100,与此同时重油从重油入口管进入提升管反应器100中,发生反应,生成的油气中液化气的含量大幅度增加,此过程将污甲醇转化为液化气,降低成本且提高经济效益。
19.进一步的,所述预提升气进料管还设置有干气进料管和蒸气进料管,所述甲醇进料管111位于干气进料管112和蒸气进料管113的上方。
20.进一步的,所述干气进料管112倾斜设置且与蒸气进料管113形成锐角,所述蒸气进料管113和干气进料管112通过比例控制器控制,所述比例控制器可以控制干气和蒸气的进料比。
21.进一步的,预提升气进料管110的拐角为弧形拐角,所述干气进料管112设置于预提升气进料管110的弧形拐角外壁上,以便于蒸气流过弧形拐角时将干气吸入预提升气进料管110。
22.进一步的,所述提升管反应器100的重油入口管、甲醇进料管111、干气进料管112和蒸气进料管113均设置有流量控制阀,便于控制进料量。
23.进一步的,所述催化裂化装置还包括沉降器200,所述沉降器200用于气固分离,设置有油剂混合物入口、油气出口和催化剂出口,所述沉降器200的油剂混合物入口连接所述提升管反应器100的油剂混合物出口。
24.进一步的,所述催化裂化装置还包括再生器300,所述再生器300用于催化剂再生,设置在沉降器200下部,所述再生器300的催化剂入口连接沉降器200的催化剂出口,所述再生器300的催化剂出口连接提升管反应器100的催化剂入口。
25.进一步的,所述再生器300下端设置催化剂输送管310,所述催化剂输送管310上设置有控制阀,以便于控制进入提升管反应器100中的催化剂的量。
26.以下通过具体实施例进一步详细说明本实用新型的技术效果:
27.实施例1
28.向预提升气进料管110中通入1.5t/h的蒸气作为预提升气,从mtbe装置中出来的污甲醇混合物经过水洗进入甲醇回收塔,甲醇回收塔中的污甲醇进入甲醇进料管111,污甲醇的通入量为0.5t/h,污甲醇进入预提升气进料管110被雾化,并在提升管反应器100中向上流动,通过提升管反应器100的下部重油入口管通入22.8t/h的重油,同时催化剂自再生器200的出口进入提升管反应器100,并由预提升气带动向上流动接触污甲醇和重油,在提升管反应器100内进行反应,反应温度为520~620℃,反应压强为0.1mpa。
29.生成的油剂混合物进入沉降器200实现气固分离,催化剂自沉降器200的催化剂出口流出并进入再生器300再生,再生催化剂由再生器300出口流出再次进入提升管反应器100,实现催化剂的重复利用。油气自沉降器200的油气出口流出,经过后处理得到汽油、柴油、液化气和干气等。
30.为验证本实用新型的效果,采用图1所述的装置和工艺流程,进行多次试验得到产品分布的平均值与对比例得到产品分布的平均值比较可见表1,其中对比例是不通污甲醇,其他条件均与实施例1相同。
31.表1产品分布
[0032][0033]
由表1可以看出,对比不加污甲醇的实验结果,本实用新型的方法得到产物中液化气的产率增加量为1.9%,平均24小时增加液化气产量为0.456t,增加经济收益1459元。
[0034]
实施例2
[0035]
向预提升气进料管110中通入1.5t/h的蒸气为预提升气,从mtbe装置中出来的污甲醇混合物经过水洗进入甲醇回收塔,甲醇回收塔中的污甲醇进入甲醇进料管111,污甲醇的通入量为1t/h,污甲醇进入预提升气进料管110被雾化,并在提升管反应器100中向上流动,通过提升管反应器100的下部重油入口管通入22.8t/h的重油,同时催化剂自再生器200的出口进入提升管反应器100,并由预提升气带动向上流动接触污甲醇和重油,在提升管反应器100内进行反应,反应温度为520~620℃,反应压强为0.1mpa。
[0036]
生成的油剂混合物进入沉降器200实现气固分离,催化剂自沉降器200的催化剂出口流出并进入再生器300再生,再生催化剂由再生器300出口流出再次进入提升管反应器100,实现催化剂的重复利用。油气自沉降器200的油气出口流出,经过后处理得到汽油、柴油、液化气和干气等。
[0037]
为验证本实用新型的效果,采用图1所述的装置和工艺流程,进行多次试验得到产品分布的平均值与对比例得到产品分布的平均值比较可见表2,其中对比例是不通污甲醇,其他条件均与实施例2相同。
[0038]
表2产品分布
[0039][0040]
由表2可以看出,对比不加污甲醇的实验结果,本实用新型的方法得到产物中液化气的产率增加量为4.2%,平均24小时增加液化气产量为1.008t,增加经济收益3225元。
[0041]
实施例3
[0042]
向预提升气进料管110中通入1.5t/h的预提升气,其中干气为0.22 t/h,蒸气为1.28 t/h,从mtbe装置中出来的污甲醇混合物经过水洗进入甲醇回收塔,甲醇回收塔中的污甲醇进入甲醇进料管111,污甲醇的通入量为1t/h,污甲醇进入预提升气进料管110被雾化,并在提升管反应器100中向上流动,通过提升管反应器100的下部重油入口管通入22.8t/h的重油,同时催化剂自再生器200的出口进入提升管反应器100,并由预提升气带动向上流动接触污甲醇和重油,在提升管反应器100内进行反应,反应温度为520~620℃,反应压强为0.1mpa。
[0043]
生成的油剂混合物进入沉降器200实现气固分离,催化剂自沉降器200的催化剂出口流出并进入再生器300再生,再生催化剂由再生器300出口流出再次进入提升管反应器100,实现催化剂的重复利用。油气自沉降器200的油气出口流出,经过后处理得到汽油、柴油、液化气和干气等。
[0044]
为验证本实用新型的效果,采用图1所述的装置和工艺流程,进行多次试验得到产品分布的平均值与对比例得到产品分布的平均值比较可见表3,其中对比例是以蒸气为预提升气,其他条件均与实施例3相同。
[0045]
表3产品分布
[0046][0047]
由表3可以看出,对比以蒸气为预提升气的实验结果,本实用新型的方法得到的产品中汽油收率提高0.54%,柴油收率提高了0.36%,液化气收率提高了0.1%,平均每天可节约催化剂270kg,减少成本2700元,并且减少了污水排放量。
[0048]
实施例4
[0049]
向预提升气进料管110中通入1.5t/h的预提升气,其中干气0.27t/h,蒸气1.23t/h,从mtbe装置中出来的污甲醇混合物经过水洗进入甲醇回收塔,甲醇回收塔中的污甲醇进入甲醇进料管111,污甲醇的通入量为1t/h,污甲醇进入预提升气进料管110被雾化,并在提升管反应器100中向上流动,通过提升管反应器100的下部重油入口管通入22.8t/h的重油,
同时催化剂自再生器200的出口进入提升管反应器100,并由预提升气带动向上流动接触污甲醇和重油,在提升管反应器100内进行反应,反应温度为520~620℃,反应压强为0.1mpa。
[0050]
生成的油剂混合物进入沉降器200实现气固分离,催化剂自沉降器200的催化剂出口流出并进入再生器300再生,再生催化剂由再生器300出口流出再次进入提升管反应器100,实现催化剂的重复利用。油气自沉降器200的油气出口流出,经过后处理得到汽油、柴油、液化气和干气等。
[0051]
为验证本实用新型的效果,采用图1所述的装置和工艺流程,进行多次试验得到产品分布的平均值与对比例得到产品分布的平均值比较可见表4,其中对比例是以蒸气为预提升气,其他条件均与实施例4相同。
[0052]
表4产品分布
[0053][0054]
由表4可以看出,对比以蒸气为预提升气的实验结果,本实用新型的方法得到的产品中汽油收率提高0.6%,柴油收率提高了0.4%,液化气收率提高了0.1%,平均每天可节约催化剂289kg,减少成本2890元,并且减少了污水排放量。
[0055]
以上装置通入纯净的甲醇也可达到上述效果。
[0056]
以上所揭露的仅为本实用新型较佳实施例而已,当然不能以此来限定本实用新型之权利范围,本领域普通技术人员可以理解实现上述实施例的全部或部分流程,并依本实用新型权利要求所作的等同变化,仍属于实用新型所涵盖的范围。