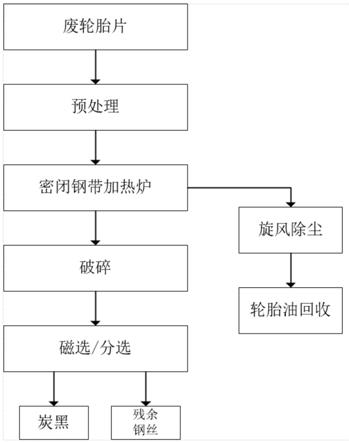
1.本发明涉及固废综合利用技术领域,尤其涉及一种废轮胎处理回收方法。
背景技术:
2.中国资源环境压力日益突出,绿色化是国家重点方向,提高资源回收利用率是国家主要方针政策。根据国家统计局数据,2020年中国橡胶轮胎产量8亿多条。每年产生废轮胎约3亿条,折合重量约1000万吨。废轮胎回收引起的环境污染、资源浪费问题越发突出。因此,利用国内外先进技术,装备废轮胎利用产业,提升废轮胎回收技术和工业化水平,是目前发展的主要方向。
3.轮胎热解产物主要是热解气、热解油和热解胎渣。热解气主要是氢气及烃类化合物,热值26~33mj/m3,常作为燃料使用。热解油热值40~43mj/kg,可以作为生产汽油、柴油及重油组分的原料油;也可以作为能源直接燃烧或发电,应用广泛、市场需求量大、价格稳定。热解胎渣主要是炭黑以及橡胶加工助剂。热解气与热解油和热解胎渣比例分别为10%、55%、35%。
4.目前热裂解技术以及研究成果大部分都还局限于实验室研究,还有很多难题没有解决(裂解设备、工艺条件等),无法大规模的投入工业生产,并且裂解产品杂质多、质量低,必须经过深加工处理,研究方向也多为产品产率。例如热解的主要方法是回转窑法,通过简单破碎后与低温硫转移催化剂一起送入热裂解器经常压低温热裂解裂化反应,分馏得到燃料油与少量可燃气,热裂解所得的粗炭黑经磁选、研磨等,钢丝做废钢回收;由于采用回转窑,常压空气进入升温会造成爆炸,因安全问题,目前还只能间歇式生产,造成热解能耗高、作业率低,翻滚产生粉尘混进热裂解产物,造成油品质量较差(含尘率可达4
‑
5wt.%)等问题。再如微波热解还在实验室开发,特别是微波如何在高油气氛下长时间工作还需要攻关。
5.随着汽车工业的发展,废轮胎这一废弃物的数量越来越多,这是一个必须解决的世界性难题,其核心是生产装备的连续化、安全性和产品的高质量。
技术实现要素:
6.鉴于上述的分析,本发明旨在提供一种废轮胎处理回收方法,至少解决现有废轮胎处理方法的问题之一:(1)生产设备的连续化、安全性低;(2)裂解产品杂质多、质量低。
7.本发明提供了一种废轮胎处理回收方法,包括以下步骤:
8.步骤1:将废轮胎进行预处理,得到钢丝和废轮胎片;
9.步骤2:在密闭钢带加热炉中,对废轮胎片在表压力100pa~3000pa下进行无催化热裂解,得到残余固体和气体;
10.步骤3:回收残余固体,回收气体冷凝得到油气;
11.步骤4:回收残余固体经过机械打碎,除去残余的钢丝得到炭黑粉。
12.进一步地,上述步骤1中,所述预处理依次包括清洗、去除钢丝和破碎,破碎至粒度50mm以下。
13.进一步地,上述步骤2中,所述热裂解的温度为400℃~550℃。
14.进一步地,上述步骤2中,所述热裂解持续时间为30min~300min。
15.进一步地,上述步骤2之后,步骤3之前还包括将残余固体进行冷却至60℃以下。
16.进一步地,上述步骤2中,所述废轮胎片铺在钢带炉的钢带上,铺料厚度为3cm~10cm。
17.进一步地,上述步骤2中,热裂解过程中,密闭钢带加热炉内处于正压状态。
18.进一步地,上述步骤3中,所述油气包括重油、轻油和可燃气,在200℃~370℃的冷凝温度区间回收得到重油,在130℃~200℃的冷凝温度区间回收得到轻油。
19.进一步地,上述步骤3中,净化后的可燃气循环用于密闭钢带加热炉的加热热源。
20.进一步地,上述步骤4中,通过磁选或风选分离钢丝和炭黑粉。
21.与现有技术相比,本发明至少可实现如下有益效果之一:
22.1、本发明提供的废轮胎处理回收方法,通过将废轮胎片在连续化的密闭钢带加热炉中,在表压力100pa~3000pa下进行无催化热裂解,得到热解油气和残余固体。由于保证热解过程在正压下进行,实现了在安全状态下连续热解废轮胎,代替了周期性、间歇式小批量的生产方式,大幅度提高了生产能力与处理效率,同时提高了资源利用率,节能减排。
23.2、本发明使用钢带加热炉作为连续化热解装备,钢带在循环运转,废轮胎是随着钢带整体移动,可以实现一端进料,一端出料,连续化生产。现有技术的热解炉是进料与出料是同一个地方,出料后需要给热解炉降温,热解炉热量损失大,热解炉的耐火砖等温度变化大,寿命比较低。
24.3、本发明采用密闭钢带加热炉,钢带上的废轮胎在热解过程中是处于静止状态,而现有技术的外热式回转装置中废轮胎是处于不停的翻滚状态,粉尘进入油气中,使油品含尘率可达4~5wt.%;本发明密闭钢带加热炉内不会产生大量粉尘,废轮胎热解产生的油气中就会夹杂极少的粉尘,这样收集到的热解油和热解气含尘率为0.3~0.4wt.%,节省后续的除尘成分,油气品质大大提升,进一步提高回收的经济价值。
25.4、本发明采用密闭钢带加热炉,上下加热,传热速率快、热量集中,使废轮胎裂解效率高,与现有技术对比,不需加分散剂、催化剂等,节约成本,环保减排,适合广泛推广。
26.5、本发明提供的废轮胎处理回收方法,可将裂解产生的油气经冷凝处理转化为裂解油,最终得到四类产品:裂解气作为补充能源用于钢带炉的加热;裂解油品包括轻油、重油;炭黑可作为胶制品的补强剂和填充剂;钢丝作为废钢回收出售;回收可达99%以上,与现有技术相比,大大提高了废轮胎的经济价值。
27.本发明中,上述各技术方案之间还可以相互组合,以实现更多的优选组合方案。本发明的其他特征和优点将在随后的说明书中阐述,并且,部分优点可从说明书中变得显而易见,或者通过实施本发明而了解。本发明的目的和其他优点可通过说明书以及附图中所特别指出的内容中来实现和获得。
附图说明
28.附图仅用于示出具体实施例的目的,而并不认为是对本发明的限制,在整个附图中,相同的参考符号表示相同的部件。
29.图1为本发明处理废轮胎片热解总体工艺流程图。
具体实施方式
30.下面结合附图来具体描述本发明的优选实施例,其中,附图构成本技术一部分,并与本发明的实施例一起用于阐释本发明的原理,并非用于限定本发明的范围。
31.本发明公开了一种废轮胎处理回收方法,具体步骤如下:
32.步骤1:将废轮胎进行预处理,得到钢丝和废轮胎片;
33.步骤2:在连续化的密闭钢带加热炉中,对废轮胎在表压力100pa~3000pa下进行无催化热裂解,得到残余固体和气体;
34.步骤3:回收残余固体,回收气体冷凝得到油气;
35.步骤4:残余固态经过机械打碎,然后通过磁选或风选除去残余的钢丝得到炭黑粉。
36.具体地,上述步骤1中,所述废轮胎预处理,直接破碎至粒度50mm以下。
37.预处理包括依次进行清洗、去除钢丝和破碎。
38.具体地,粉碎采用轮胎粉碎设备,采用抽钢丝设备进行抽钢丝。热解过程中,钢丝会在热解炉内吸收热量,去除钢丝可以节省钢丝升高温度,再降温出炉的热量。
39.具体地,上述步骤2中,热裂解的温度为400℃~550℃。
40.废轮胎是由天然橡胶、合成橡胶、炭黑、化纤帘布和橡胶助剂等材料组成的一种高热值材料。其热值比煤炭高约5%~10%,与天然气接近,在400℃~550℃时,可发生热裂解。热裂解过程在缺氧或惰性气体中进行,可产生热解气、热解油和固体残余等。
41.具体地,上述步骤2中,热裂解持续时间为30min~300min。
42.根据密闭钢带加热炉上的物料厚度,以及钢带的运行速度确定热解时间,示例性地,物料厚度为5cm,钢带的运行速度为0.2m/min时,钢带炉加热段为10m,热裂解持续时间为50min。
43.具体地,上述步骤2中,所述废轮胎铺在钢带炉的钢带上,轮胎铺料厚度为3cm~10cm。
44.轮胎片铺在钢带上,采用上、下加热方式,能够有效改善加热条件。经反复试验研究表明,轮胎片铺料厚度3cm~10cm;炉内加热段温度400~550℃,在炉内加热段停留30min~300min可以热解分离98%以上的气态油气。
45.钢带上的废轮胎在热解过程中是处于静止状态,而传统的外热式回转装置中废轮胎是处于不停的翻滚状态,热解油气含尘率可高达4~5wt.%。密闭钢带加热炉内不会产生大量粉尘,废轮胎热解产生的油气中含尘率仅为0.3~0.4wt.%,这样收集到的热解油和热解气品质大大提升。
46.具体地,上述步骤2中,为保证密闭钢带加热炉处于正压状态,密闭钢带加热炉的各个进、出口进行密封,示例性地,可采用氮气密封、水密封,例如:在钢带进出口利用多排气孔向钢带吹喷大量氮气,形成气帘;同时,在钢带进出炉口设置水槽,钢带进出炉经过水槽,形成水封,从而达到密封的目的。密闭钢带加热炉内压力为表显压力100pa~3000pa。
47.进一步保证密闭钢带加热炉的密封性,持续处于正压,在进料仓,则采用三级料仓,示例性地,一级料仓是敞开的,二级料仓有调节压力设备,三级料仓和密闭钢带加热炉内联通并用氮气进行密封;三个料仓之间采用阀门连接。
48.废旧轮胎经过热解后可产生co、h2、ch4、c
n
h
m
等可燃成分,现有技术采用微负压、常
压,空气很容易进入热解炉内,当热解工艺中co、h2、ch4、c
n
h
m
等达到一定浓度,与空气中的o2混合会形成爆炸气体。本发明保证密闭钢带加热炉处于正压状态,进出口密封状态,保证炉内不混入含氧空气,因此不会出现爆炸问题。
49.为保证压力保持在100pa~3000pa范围内,在生产中可通过炉内压力监测设备和加压机协调作用,具体地,在实际工作中,影响压力的因素有:设备的密封性、进料速度、废轮胎裂解产生气体量;其中废轮胎在热解炉内热解会产生大量气体,这些气体增加了密闭钢带加热炉内的压力,可以通过调低进料速度和提高加压机工作频率保证炉内压力平衡。
50.密闭钢带加热炉的起始热源可以是电加热,也可以是天然气等可燃气体烧嘴加热;废轮胎热解产生的不凝可燃气可通入加热设备,为密闭钢带炉提供后续热源,从而节约能源。
51.具体地,上述步骤2中,还包括在无催化热裂解后钢带上残余的固体进行冷却,示例性地,间接水冷却,冷却后残余固体温度为60℃以下。
52.残余固体主要是炭黑,另外还有一些轮胎制备过程中的硫化剂、添加剂、催化剂等复合成分,这些成分一般为可燃物,冷却至60℃是为了防止这些残余固体自燃。
53.具体地,上述步骤3中,冷凝得到的油气包括重油、轻油和可燃气。
54.需要说明的是,最终冷凝得到的油气成分很复杂,成分和轮胎种类有关,分为重油、轻油和可燃气。
55.具体地,上述步骤3中,在200℃~370℃的冷凝温度区间回收得到重油,在130℃~200℃的冷凝温度区间回收得到轻油。
56.具体地,上述步骤3中,回收热解气后冷凝前,还包括除尘。
57.一般地,除尘设备主要是高温旋风除尘,如果热解气内含有大量粉尘,净化成本会很高。本发明采用密闭钢带加热炉,轮胎密闭钢带加热炉内是静止状态,热解过程中也处于静止状态,不会产生大量的粉尘,这样收集到的热解油和热解气品质会有大的提升,得到的油气质量高,除尘成本低。
58.与现有技术对比,现有技术中的热解炉,进料口与出料口相同,出料后需要给热解炉降温,热解炉热量损失大,热解炉的耐火砖等温度变化大,寿命比较低,本发明密闭钢带加热炉的钢带循环运转,一端进料一端出料,装置处于连续化状态,代替了间歇式小批量的生产方式,极大的提高了生产效率。
59.与现有技术比,密闭钢带加热炉的各个进出口密封,炉内采用正压操作,保证了空气不会进入炉内混入油气中而存在的安全隐患。为了实现密封技术,钢带进入热解炉的两侧用水密封技术,实现100pa~3000pa的正压操作,在进料仓,则采用三级料仓,并用氮气进行密封。
60.本发明利用气体净化系统及余热循环利用系统,净化后的可燃气作为燃料用于供热系统,余热得到充分利用,实现了裂解所需热能基本上来自于回收的可燃不凝气,仅需补充少量天然气或者液化气,大大降低运行成本。另外,本发明的密闭钢带加热炉也可采用电加热,这样装备更简单,炉内温控更平稳,此时热解产生的气体需要在其它地方利用。
61.本发明采用连续化的密闭钢带加热炉,轮胎片铺在钢带上,采用上、下加热方式,能够有效改善加热条件。经过反复试验研究表明,轮胎片铺料厚度3cm~10cm;炉内高温段温度400~550℃,在炉内加热段停留30min~300min可以热解分离98%以上的气态油气。
62.本发明的密闭钢带加热炉热解产生的气态油气,首先经过粗除尘,然后经过油气分段冷凝即可分离重油、轻油和不凝可燃气,重油冷凝回收温度为200~370℃、轻油回收温度为130~200℃比较适宜。
63.与现有技术对比,本发明的密闭钢带加热炉内不会产生大量粉尘,废轮胎热解产生的油气中就会夹杂极少的粉尘,这样收集到的热解油和热解气品质会有大的提升,得到的油气质量高,除尘成本低。
64.本发明还可以处置带钢丝的废轮胎片,冷却后的炭黑和钢丝需要通过机械打碎后再通过磁选或风选等方式分离钢丝和炭黑粉。
65.实施例1
66.本实施例提供了一种废轮胎处理回收方法,工艺流程如图1所示,采用该方法处理100kg的废轮胎,具体细节如下:
67.s1:将100kg废轮胎经破碎、磁选得到去除钢丝后的废轮胎片,粒度在35mm以下。
68.s2:裂解炉为密闭钢带加热炉,密闭钢带加热炉的钢带进出口采用水槽密封。进料仓用三级料仓,料仓内通氮气密封,将热解炉内的压力控制在正压500
±
100pa(表压),将去除钢丝后的废轮胎粉末送入密闭钢带加热炉内,炉内加热段温度510℃,加热段停留时间60min,冷却段停留时间60min。
69.s3:热解产生的油气,经过旋风除尘,然后在重油冷凝回收塔内回收重油,出口温度控制在200
±
10℃;然后油气进入轻油冷凝回收塔内进一步脱除轻油,出口温度控制在130
±
20℃,油气分离后,不凝可燃气经储罐调整压力后回用至热解炉加热,冷凝的重油、轻油分别进入各自的储油罐。
70.s4:热解剩余产物采用破碎机打碎,将残余的钢丝通过两级磁选分离,再经过造粒、干燥后送至成品仓库。
71.再生炭黑可作为橡胶制品的补强剂和填充剂。活化造粒后的再生炭黑具备常规橡胶用炭黑的性质,可部分替代用于轮胎生产过程中的n550、n660炭黑。
72.实施例1针对100kg废轮胎,采用上述方法处理回收,最终得到40kg重油,10kg轻油,37kg炭黑,12kg钢丝;回收率可达99%。
73.实施例1得到的重油和轻油含尘率为0.33wt.%。
74.实施例2
75.本实施例提供了一种废轮胎处理回收方法,工艺流程如图1所示,采用该方法处理100kg的废轮胎,具体细节如下:
76.s1:将100kg废轮胎经破碎、磁选得到去除钢丝后的废轮胎片,粒度在40mm以下。
77.s2:裂解炉为密闭钢带加热炉,密闭钢带加热炉两端采用水密封。进料仓用三级料仓,通氮气密封,将热解炉内的压力控制在正压1500
±
100pa(表压),将去除钢丝后的废轮胎粉末送入密闭钢带加热炉内,炉内加热段温度420℃,加热段停留时间120min,冷却段停留时间60min。
78.s3:热解产生的油气,经过旋风除尘,然后在重油冷凝回收塔内回收重油,出口温度控制在200
±
10℃;然后油气进入轻油冷凝回收塔内进一步脱除轻油,出口温度控制在130
±
20℃,油气分离后,不凝可燃气经储罐调整压力后回用至热解炉加热,冷凝的重油、轻油分别进入各自的储油罐。
79.s4:热解剩余产物采用破碎机打碎,将残余的钢丝通过两级磁选分离,再经过造粒、干燥后送至成品仓库。
80.再生炭黑可作为橡胶制品的补强剂和填充剂。活化造粒后的再生炭黑具备常规橡胶用炭黑的性质,可部分替代用于轮胎生产过程中的n550、n660炭黑。
81.实施例2针对100kg废轮胎,采用上述方法处理回收,最终得到39kg重油,11kg轻油,37kg炭黑,12kg钢丝;回收率可达99%。
82.实施例2得到的重油和轻油含尘率为0.31wt.%。
83.实施例3
84.本实施例提供了一种废轮胎处理回收方法,工艺流程如图1所示,采用该方法处理100kg的废轮胎,具体细节如下:
85.s1:将100kg废轮胎直接破碎成带钢丝的废轮胎片,破碎粒度在50mm以下。
86.s2:裂解炉为密闭钢带加热炉,密闭钢带加热炉两端采用水密封。进料仓用两级料仓,通氮气密封,将热解炉内的压力控制在正压1000
±
100pa(表压),将带钢丝后的废轮胎片送入密闭钢带加热炉内,热解炉采用电加热,炉内高温段温度490℃,高温段停留时间90min,冷却段停留时间90min。
87.s3:热解产生的油气,经过旋风除尘,然后在重油冷凝回收塔内回收重油,出口温度控制在200
±
10℃;然后油气进入轻油冷凝回收塔内进一步脱除轻油,出口温度控制在130
±
20℃,油气分离后,不凝可燃气进入储罐,冷凝的重油、轻油分别进入各自的储油罐。
88.s4:热解剩余产物采用破碎机打碎,再通过风选方式分离钢丝和炭黑粉,炭黑粉再经过造粒、干燥后送至成品仓库。
89.实施例3针对100kg废轮胎,采用上述方法处理回收,最终得到38kg重油,12kg轻油,37.5kg炭黑,钢丝12kg;回收率可达99.5%。
90.实施例3得到的重油和轻油含尘率为0.36wt.%。
91.实施例1~3表明,本发明提供的废轮胎处理回收方法,可将裂解产生的油气经冷凝处理转化为裂解油,最终得到四类产品:裂解气体作为补充能源用于钢带炉的加热;裂解油品包括轻油、重油;炭黑可作为胶制品的补强剂和填充剂;钢丝作为废钢回收出售;回收可达99%以上,与现有技术相比,大大提高了废轮胎的经济价值。
92.以上所述,仅为本发明较佳的具体实施方式,但本发明的保护范围并不局限于此,任何熟悉本技术领域的技术人员在本发明揭露的技术范围内,可轻易想到的变化或替换,都应涵盖在本发明的保护范围之内。