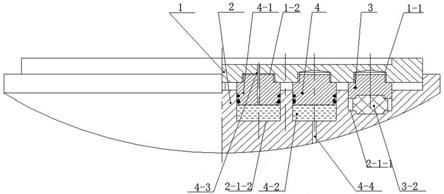
1.本发明涉及桥梁支座技术领域,具体说的是一种具有补充润滑脂功能的减振球冠衬板。
背景技术:
2.球冠衬板,又称中座板,作为实现球型支座的转动及平面运动的关键部件。球冠衬板球面部分作为硬质对磨面,直接暴漏在工作环境中,既要具有良好耐磨性,又要具有良好的耐蚀性,才能满足长期稳定服役的设计要求。
3.目前球冠衬板主体多采用低合金钢、铝合金等材料。为保证硬质对磨面的耐蚀性能、耐磨性,低合金钢球冠衬板的球面处还需要包覆不锈钢板或者镀铬处理,铝合金球冠衬板需选用耐蚀体系,球面处还需进行特殊表面处理工艺。低合金钢球冠衬板包覆不锈钢板成型工艺实施难度极高,经常出现不锈钢板与球冠衬板贴合不紧密、结合处焊缝出现腐蚀等问题;而球冠衬板表面镀铬存在严重的污染问题,不符合当前低碳环保的要求。采用铝合金成本高且工艺复杂。
4.球冠衬板通常采用实心结构、单一材料制造而成,其结构简单、重量较重,实际使用应力偏低,不能充分发挥材料的力学特性。
5.此外传统球冠衬板结构过于单一,功能简单,没能完全发挥在该部件在支座中的结构位置优势。目前,球型支座内润滑脂多存储在滑板的储脂坑内,当处置坑润滑脂全部流失,滑板将进入干摩擦状态,严重影响滑板的使用寿命,完全可以利用支座球冠衬板为支座的摩擦副提供补脂作用。另外,桥梁减振隔振功能已成为市政,城际项目必要选项,目前减振支座,多需要在支座结构外,另设一层减振材料或结构,增加了支座的高度,复杂度。球冠衬板是支座传力路径的关键环节,完全可以通过新型结构设计实现较量减振。
技术实现要素:
6.为解决上述技术问题,本发明提供一种具有补充润滑脂功能的减振球冠衬板,不仅具有减震效果,并且在使用过程中具有补充润滑脂的功能。
7.为实现上述技术目的,所采用的技术方案是:一种具有补充润滑脂功能的减振球冠衬板,包括顶板、球面板、减振体和补脂体,球面板的底面为球面或曲面,球面板上表面上开设有用于安装顶板的安装槽,顶板的下表面上开设有多个用于安装减振体和补脂体上端的减振上凹槽和补脂上凹槽,在安装槽的槽底开设有多个用于安装减振体和补脂体下端的减振下凹槽和补脂下凹槽,所述的减振体由上部的减振导柱和下部的弹性元件组成,弹性元件设置在减振下凹槽的槽底,弹性元件与减振下凹槽的槽壁之间设有用于弹性元件径向变形的间隙,减振导柱的下端相配合的插入减振下凹槽内,并放置在弹性元件上,减振导柱的上端插入减振上凹槽内,使顶板与安装槽的槽底面之间设有竖向间隙,所述的补脂体由上部的补脂导柱和下部的存储有润滑脂的储脂变形元件组成,储脂变形元件设置在补脂下凹槽的槽底,补脂导柱的下端相配合的插入补脂下凹槽内,并放置在储脂变形元件上,补脂
导柱的上端插入补脂上凹槽内,在补脂导柱和顶板内开设有使顶板的顶面与补脂导柱的底面相连通的平面摩擦副引脂流道,球面板的底部开设有使补脂下凹槽与球面板的底面相连通的球面摩擦副引脂流道。
8.减振体和补脂体均匀分布安装在球面板上。
9.减振导柱的上端与减振上凹槽采用螺纹连接、焊接或插接进行连接。
10.补脂导柱的上端与补脂上凹槽采用螺纹连接、焊接或插接进行连接。
11.补脂导柱和补脂下凹槽之间设有密封结构。
12.弹性元件采用的材料为高阻尼聚氨酯弹性体或高阻尼橡胶。
13.储脂变形元件为开孔泡软的聚氨脂材料或高弹海绵。
14.顶板和球面板采用双相不锈钢制成。
15.本发明的有益效果是:1、内部材料采用减振材料如:高阻尼聚氨酯材料、高阻尼橡胶,可以大幅提升支座的减振性能。内部材料采用能够存储润滑脂的空隙材料或者储脂结构,根据设计可以持续或定期释放润滑脂,保证支座的摩擦副始终处于油润滑摩擦状态。内部材料同时采用集成减振材料和存储润滑脂的空隙材料,即可实现既有储脂缓释又有减振功能的球冠衬板。
16.2、球冠衬板采用为分体式的顶板和球面板,在两者之间开孔,加入减振体和补脂体,减小球冠衬板质量,降低支座总重,如顶板上的非金属滑板磨损严重,可以对顶板进行更换,并且更换内部的减振体和补脂体。由于双相不锈钢具有较高的强度和耐蚀性,在设计球冠衬板时可以通过减薄构件的厚度以及合理的结构设计减轻球冠衬板的重量,从而达到降低成本的目的。同时,可根据需要的减震及补脂效果,合理安排减振体和补脂体的个数及大小。
17.3、球冠衬板材料选用双相不锈钢,与以往zg20mn、zg270-500等材质球冠衬板相比,双相不锈钢具有更高的强度和疲劳强度,采用双相不锈钢作为球冠衬板的材料,不仅可以提高桥梁支座的安全性,而且还可以提高其使用寿命。
附图说明
18.图1为本发明的结构示意图;图2为本发明的球面板的结构示意图;图3为本发明的顶板、减振体和补脂体的结构示意图;图中:1、顶板,1-1、减振上凹槽,1-2、补脂上凹槽,2、球面板,2-1、安装槽,2-1-1、减振下凹槽,2-1-2、减振下凹槽,3、减振体,3-1、减振导柱,3-2、弹性元件,4、补脂体,4-1、补脂导柱,4-2、储脂变形元件。
具体实施方式
19.如图1所示,一种具有补充润滑脂功能的减振球冠衬板,该结构重量轻,球型摩擦面的耐磨性好,材料整体耐蚀性能优异,具有补充润滑脂的功能。其包括顶板1、球面板2、减振体3和补脂体4,球面板2的底面为球面或曲面,用于实现转动功能,顶板1的上表面为平面,其上可开设用于安装非金属滑板的镶嵌槽,用于实现平面滑动功能。
20.如图1、图2、图3所示,球面板2上表面上开设有用于安装顶板1的安装槽2-1,安装
槽2-1的横向形状与顶板1的横向形状相匹配,该匹配为间隙配合,顶板1的下表面上开设有多个用于安装减振体3和补脂体4上端的减振上凹槽1-1和补脂上凹槽1-2,减振上凹槽1-1和补脂上凹槽1-2的形状可以为圆柱形或多棱体,在安装槽2-1的槽底开设有多个用于安装减振体3和补脂体4的减振下凹槽2-1-1和补脂下凹槽2-1-2,减振下凹槽2-1-1和补脂下凹槽2-1-2的形状可以为圆柱体或多棱体,优选圆柱体,减少减振体和补脂体4在凹槽内移动的摩擦力。减振体3和补脂体4的数量比以设计要求为准。
21.减振体3作为支撑与减振部件使用,当有载荷通过支座时,顶板1与减振导柱3-1组合挤压球面板2内的弹性元件3-2,从而实现减震功能。减振体3由上部的减振导柱3-1和下部的弹性元件3-2组成,弹性元件3-2设置在减振下凹槽2-1-1的槽底,弹性元件3-2与减振下凹槽2-1-1的槽壁之间设有用于弹性元件3-2径向变形的间隙,弹性元件3-2受压径向变形,当压力变小时回复原状,实现复位,减振导柱3-1的下端相配合的插入减振下凹槽2-1-1内,并放置在弹性元件3-2上,该配合为间隙配合,方便减振导柱3-1在减振下凹槽2-1-1内的竖向移动,减振导柱3-1的上端插入减振上凹槽1-1内,使顶板1与安装槽2-1的槽底面之间设有竖向间隙,该竖向间隙用于顶板1在安装槽2-1内竖向移动,当顶板1受压下移,同时减振导柱3-1也沿减振下凹槽2-1-1下移,挤压弹性元件变形,实现减振,减振体3的排布为均匀规律排布,例如按圆周环形排布。
22.补脂体4受到不超过减振体的支撑力时,不对摩擦副补充润滑脂,补脂体4由上部的补脂导柱4-1和下部的存储有润滑脂的储脂变形元件4-2组成,储脂变形元件4-2设置在补脂下凹槽2-1-2的槽底,储脂变形元件4-2受到挤压可将内部的润滑脂排出,补脂导柱4-1的下端相配合的插入补脂下凹槽2-1-2内,并放置在储脂变形元件4-2上,补脂导柱4-1的上端插入补脂上凹槽1-2内,在补脂导柱4-1和顶板1内开设有使顶板1的顶面与补脂导柱4-1的底面相连通的平面摩擦副引脂流道4-3,平面摩擦副引脂流道4-3穿通补脂导柱和顶板进行补脂,球面板2的底部开设有使补脂下凹槽2-1-2与球面板2的底面相连通的球面摩擦副引脂流道4-4。当支座上部载荷放生变化时,顶板组合体将挤压存储有润滑脂的储脂变形元件4-2,使其释放润滑脂,并通过平面摩擦补脂引流通道4-3及球面摩擦副补脂通道4-4补充到平面摩擦与球面摩擦副中,实现补脂功能。而在受压补脂过多时,储脂变形元件4-2回弹可将多余的润滑脂回吸,防止润滑脂浪费。补脂体4的排布为均匀规律排布,例如按圆周环形排布。
23.减振体3和补脂体4均匀分布安装在球面板2上,排布方式要保证整个球冠衬板的承载平衡。减振体3和补脂体4可按照同心圆的形式排布。
24.减振导柱3-1的上端与减振上凹槽1-1采用螺纹连接、焊接或插接进行连接。
25.补脂导柱4-1的上端与补脂上凹槽1-2采用螺纹连接、焊接或插接进行连接。
26.补脂导柱4-1和补脂下凹槽2-1-2之间设有密封结构,该密封结构实现动密封与静密封,静密封防止储存在储脂变形元件内的润滑脂从补脂下凹槽2-1-2内流出,动密封防止储存在储脂变形元件内的润滑脂受压从补脂下凹槽2-1-2内流出。
27.弹性元件3-2采用的材料为高阻尼聚氨酯弹性体或高阻尼橡胶,两种材料均具有高阻尼效应。
28.储脂变形元件4-2为开孔泡软的聚氨脂材料或高弹海绵,储脂变形元件4-2采用浸润的方式储存润滑脂,或者增加开孔储润滑脂。
29.球冠衬板材料选用s32101、s32304、4a、5a等牌号双相不锈钢,例如:顶板、球面板、减振导柱和补脂导柱选用双相不锈钢,其成分如表1所示。与以往zg20mn、zg270-500等材质球冠衬板相比,双相不锈钢具有更高的强度和疲劳强度,屈服强度是18-8型奥氏体不锈钢(316、316l)的两倍;耐蚀性更好,耐腐蚀疲劳和磨损腐蚀以及耐氯化物应力腐蚀,耐蚀性能优于18-8型奥氏体不锈钢;焊接性良好、热裂倾向小;双相不锈钢可在-50℃~300℃间使用。采用双相不锈钢作为球冠衬板的材料,不仅可以提高桥梁支座的安全性,而且还可以提高其使用寿命。
30.表1球冠衬板用双相不锈钢成分(w%)