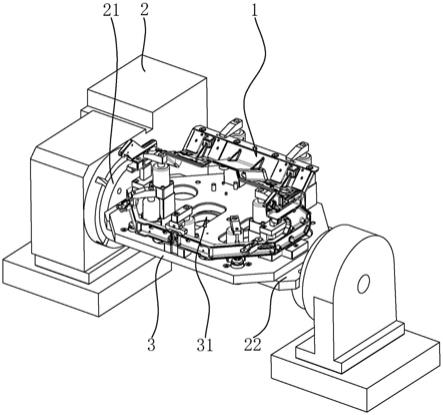
1.本技术涉及机械零件加工的技术领域,尤其是涉及一种机械零件多点加固夹具。
背景技术:
2.机械零件(machine element)又称机械元件(machine part)是构成机械的基本元件,是组成机械和机器的不可分拆的单个制件。现有的一种机械零件(以下简称工件)包括呈类环状设置,同时工件为轴对称图形。工件包括第一连接杆、第二连接杆、第三连接杆和第四连接杆,第一连接杆、第二连接杆、第三连接杆和第四连接杆依次固定连接并且一体成型。第一连接杆、第二连接杆和第三连接杆的数量均为两根,并且两根第一连接杆、两根第二连接杆和两根第三连接杆均关于对称轴呈相对设置。第四连接杆的相对两端分别固定连接于两个第三连接杆之间,对称轴与第四连接杆的长度方向相垂直,并且对称轴位于第四连接杆长度方向的中点位置处。
3.工件还设置有若干个通孔和定位孔,若干个定位孔分别为第一定位孔和两个第二定位孔,第一定位孔位于第四连接杆,两个第二定位孔分别位于两根第二连接杆。若干个通孔分别分布于第一连接杆、第二连接杆、第三连接杆和第四连接杆。
4.在生产工件的过程中,工作人员利用模具对第一连接杆和、第二连接杆、第三连接杆和第四连接杆进行浇注成型,同时第一定位孔和第二定位孔通过浇注成型设置在第四连接杆和第二连接杆处,再利用数控机床加工通孔。
5.现有的数控加工机床包括机主体、旋转盘以及支撑板,旋转盘的数量为两个,两个旋转盘呈相对设置,支撑板螺栓连接于两个旋转盘之间。支撑板用于供工件安装,旋转盘用于带动支撑板转动,进而支撑板带动工件转动,进而便于机主体对工件的进行多方位加工。
6.在现有的工件固定的方式中,工作人员现在支撑板处安装若干个快速夹具,并将工件放置在支撑板表面,进而利用快速夹具对工件表面进行快速夹紧;数控机床对工件进行钻孔加工时,旋转盘会对带动工件进行转动,同时快速夹具的压头一般情况下是自上而下移动并抵紧于工件表面,即快速夹具只抵紧于工件的其中一侧,随着支撑板带动工件和快速夹具的转动,进而容易导致快速夹具对工件的夹紧出现松动的情况发生,导致工件的稳定性降低,进而会降低数控机床对工件通孔的加工精度。
技术实现要素:
7.为了提高工件固定于安装板的稳定性的稳定性,本技术提供一种机械零件多点加固夹具。
8.本技术提供的一种机械零件多点加固夹具,采用如下的技术方案:
9.一种机械零件多点加固夹具,包括安装板、按压机构和支撑机构,所述安装板固定安装于支撑板,所述安装板用于供工件放置,所述按压机构和所述支撑机构均安装于所述安装板,所述按压机构和所述支撑机构均用于抵紧工件,所述按压机构和所述支撑机构分别抵紧于工件的相对两侧。
10.通过采用上述技术方案,当需要对工件进行通孔加工时,工作人员将工件放置在安装板上,利用按压机构,使得按压机构抵紧于工件的其中一侧,利用支撑机构,使得支撑机构抵紧于工件的另一侧,按压机构和支撑机构抵紧于工件的相对两侧,进而实现对工件的夹紧作用,减少工件在转动的过程中出现松动的情况发生,进而提高了工件固定于安装板的稳定性。
11.优选的,所述按压机构包括均安装于所述安装板的第一转角气缸、第二转角气缸、第三转角气缸以及第四转角气缸,所述第一转角气缸的输出轴连接有第一压块,所述第二转角气缸的输出轴连接有第二压块,所述第三转角气缸的输出轴连接有第三压块,所述第四转角气缸的输出轴连接有第四压块;所述支撑机构包括均安装于所述安装板的第一支撑缸、支撑组件,第三支撑缸和支撑块,所述第一支撑杆的输出轴和第一压块分别抵紧于第一连接杆的相对两侧,所述支撑组件用于支撑第二连接杆,所述支撑组件和所述第二压块分别抵紧于所述第二连接杆的相对两侧,所述第三支撑杆的输出轴和所述第三压块分别抵紧于第三连接杆的相对两侧,所述支撑块用于支撑第四连接杆,所述支撑块和所述第四压块分别抵紧于所述第四连接杆的相对两侧。
12.通过采用上述技术方案,当需要夹持工件时,工作人员将工件放置安装板处,同时支撑机构和按压机构分别朝向工件的相对两侧,工作人员启动第一转角气缸、第二转角气缸、第三转角气缸和第四转角气缸,工作人员还启动第一支撑缸以及第三支撑缸,使得第一压块和第一支撑缸输出轴分别抵紧于第一连接杆的相对两侧,进而对第一连接杆实现夹持作用,第二压块和支撑组件分别抵紧于第二连接杆的相对两侧,进而对第二连接杆实现夹持作用,第三压块和第三支撑缸输出轴分别抵紧于第三连接杆的相对两侧,进而对第三连接杆实现夹持作用,第四压块和支撑块分别抵紧于第四连接杆的相对两侧,进而对第四连接杆实现夹持作用,进而支撑机构和按压机构对工件实现夹持作用。
13.优选的,所述第一转角气缸数量为两个,两个第一转角气缸分别用于抵紧两根第一连接杆,所述第一支撑缸的数量和所述第一转角气缸的数量相同;所述第二转角气缸的数量为两个,两个第二转角气缸分别用于抵紧两根第二连接杆,所述支撑组件的数量与所述第二转角气缸的数量相同;所述第三转角气缸的数量为两个,两个第三转角气缸的分别抵紧于两根第三连接杆,所述第三支撑缸的数量与所述第三转角气缸的数量相同。
14.通过采用上述技术方案,利用两个第一转角气缸和两个第一支撑缸,进而均提高了两根第一连接杆在安装板的稳定性;利用两组支撑组件和两个第二转角气缸,进而对两根第二连接杆均实现夹持作用;利用两个第三转角气缸和两个第三支撑缸,进而对两根第三连接杆均实现夹持作用,进而提高了工件的稳定性。
15.优选的,所述第一支撑缸的输出轴固定连接有第一顶块,所述第一顶块用于抵紧所述第一连接杆。
16.通过采用上述技术方案,当需要第一支撑缸抵紧于第一连接杆的一侧时,工作人员启动第一支撑缸的输出轴,进而第一支撑缸带动第一顶块滑移,直至第一顶块抵紧于第一连接杆的一侧,利用第一顶块,进而增大了第一连接杆承受压力的接触面积,进而降低了压强,减少了工件在夹持的过程中,出现损坏的情况发生。
17.优选的,所述支撑组件包括第二顶块,所述第二顶块固定连接于所述安装板,所述第二顶块与所述第二压块分别抵紧于所述第二连接杆的相对两侧。
18.通过采用上述技术方案,当需要夹持第二连接杆时,工作人员握持并移动工件,使得第二连接杆放置在第二顶块背离安装板的一侧,进而第二顶块抵紧于第二连接杆的一侧,工作人员启动第二转角气缸,第二转角气缸驱动第二压块,直至第二压块抵紧于第二连接杆背离第二顶块的一侧,进而对第二连接杆实现支撑作用。
19.优选的,所述支撑组件还包括第三固定块和第二定位销,所述第三固定块固定安装于所述安装板,所述第三固定块设置有第二插孔,所述第二插孔与所述第二定位孔相连通,所述第二定位销的相对两端分别与第二插孔和第二定位孔插接配合。
20.通过采用上述技术方案,当需要将第二连接杆放置在安装板时,工作人员握持并移动第二连接杆,使得第二连接杆的第二定位孔与第二定位销相连通,进而工作人员移动第二连接杆,使得第二定位孔与第二定位销插接配合,进而对第二连接杆的安装位置实现定位作用,同时第二连接杆的一侧与第二顶块向相抵接,便于后期支撑组件抵紧于第二连接杆的一侧。
21.优选的,所述第三压块螺纹连接有抵接螺栓,所述抵接螺栓的螺帽用于抵紧所述第三连接杆。
22.通过采用上述技术方案,当第三连接杆与第三支撑缸相抵接时,由于第三连接杆与安装板之间的距离小于第三压块与安装板的最小距离,利用与第三压块螺纹连接的抵接螺栓,抵接螺栓的螺帽可与第三连接杆相抵接,便于第三压块对第三连接杆实现抵紧作用,进而便于后期夹持第三连接杆。
23.优选的,所述按压机构还包括按压组件,所述按压组件包括抵紧块,所述抵紧块与所述第四压块相连接,所述抵紧块和所述支撑块分别抵紧于第四连接杆的相对两侧,所述抵紧块设置有第一让位槽,所述支撑块设置有第二让位槽,所述第一让位槽和所述第二让位槽分别位于第四连接杆的相对两侧。
24.通过采用上述技术方案,当机主体需要对第四连接杆进行通孔加工时,工作人员将第四连接杆放置在支撑块处,支撑块对第四连接杆实现支撑作用,第四连接杆与安装板之间的距离小于第四压块与安装板之间的最小距离,利用抵紧块,使得第四压块可对第四连接杆传递压力,进而便于后期对第四连接杆的夹持作用;通孔位于按压组件和支撑块之间,进而机主体会在按压组件和支撑块之间对第四连接杆进行切削加工,利用第一让位槽和第二让位槽,进而减少了机主体对第四连接杆进行加工的过程中对按压组件和支撑块造成损害。
25.优选的,所述支撑块插接配合有第二定位销,所述支撑块设置有第二插孔,所述第二插孔与第一定位孔相连通,所述第二定位销的相对两端分别与第二插孔、第一定位孔插接配合。
26.通过采用上述技术方案,当需要将第四连接杆放置在安装板时,工作人员先把第一定位销插入第一插孔内,工作人员握持并移动第四连接杆,使得第一定位孔与第一插孔相连通,进而工作人员继续移动第四练连接杆,使得第四连接杆的第一插孔与第一定位销插接配合,直至第四连接杆与支撑块相抵接,进而实现了对第四连接杆的定位作用,便于提高后期机主体对工件的加工精度。
27.优选的,所述安装板设置有穿孔,所述穿孔用于供机主体内的切削液流出。
28.通过采用上述技术方案,当机主体对工件进行加工时,机主体会对工件进行通孔
加工的同时,机主体还会喷出切削液,利用穿孔,使得切削液经穿孔流出,减少切削液积聚在安装板处的情况发生,同时利用穿孔,进而对安装板实现减重的效果。
29.综上所述,本技术包括以下至少一种有益技术效果:
30.1.通过工作人员将工件放置在安装板上,利用按压机构,使得按压机构抵紧于工件的其中一侧,利用支撑机构,使得支撑机构抵紧于工件的另一侧,按压机构和支撑机构抵紧于工件的相对两侧,进而实现对工件的夹紧作用,减少工件在转动的过程中出现松动的情况发生,进而提高了工件固定于安装板的稳定性;
31.2.通过工作人员将工件放置安装板处,同时支撑机构和按压机构分别朝向工件的相对两侧,工作人员启动第一转角气缸、第二转角气缸、第三转角气缸和第四转角气缸,工作人员还启动第一支撑缸以及第三支撑缸,使得第一压块和第一支撑缸输出轴分别抵紧于第一连接杆的相对两侧,进而对第一连接杆实现夹持作用,第二压块和支撑组件分别抵紧于第二连接杆的相对两侧,进而对第二连接杆实现夹持作用,第三压块和第三支撑缸输出轴分别抵紧于第三连接杆的相对两侧,进而对第三连接杆实现夹持作用,第四压块和支撑块分别抵紧于第四连接杆的相对两侧,进而对第四连接杆实现夹持作用,进而支撑机构和按压机构对工件实现夹持作用;
32.3.通过利用两个第一转角气缸和两个第一支撑缸,进而均提高了两根第一连接杆在安装板的稳定性;利用两组支撑组件和两个第二转角气缸,进而对两根第二连接杆均实现夹持作用;利用两个第三转角气缸和两个第三支撑缸,进而对两根第三连接杆均实现夹持作用,进而提高了工件的稳定性。
附图说明
33.图1是现有一种数控机床的部分结构示意图;
34.图2是本实施例中一种机械零件多点加固夹具的整体结构示意图;
35.图3是本实施例中第一连接杆、按压机构和支撑机构的部分结构示意图;
36.图4是图3中a处的放大图;
37.图5是本实施例中第二连接杆、按压机构和支撑机构的部分结构示意图;
38.图6是本实施例中第三连接杆、第四连接杆、支撑机构和按压机构的部分结构示意图;
39.图7是图6中b处的放大图。
40.图中,1、工件;11、第一连接杆;111、第一抵接面;112、第一支撑面;12、第二连接杆;121、第二抵接面;122、第二支撑面;123、第二定位孔;13、第三连接杆;131、第三抵接面;132、第三支撑面;14、第四连接杆;143、第一定位孔;2、机主体;21、旋转盘;22、支撑板;3、安装板;31、穿孔;32、安装孔;41、第一转角气缸;411、第一压块;412、第一垫块;42、第二转角气缸;421、第二压块;422、第二垫块;43、第三转角气缸;431、第三压块;432、抵接螺栓;44、第四转角气缸;441、第四压块;45、按压组件;451、抵紧块;452、第一让位槽;453、插块;454、安装块;455、插槽;456、固定销;51、第一支撑缸;511、第一顶块;512、承托块;52、支撑组件;521、第二顶块;522、第一固定块;523、第二固定块;524、第三固定块;525、第二插孔;526、第二定位销;53、第三支撑缸;54、支撑块;541、第二让位槽;542、第一插孔;543、第一定位销。
具体实施方式
41.以下结合附图1-7对本技术作进一步详细说明。
42.现有的一种机械零件(以下简称工件1)包括呈类环状设置,同时工件1为轴对称图形。工件1包括第一连接杆11、第二连接杆12、第三连接杆13和第四连接杆14,第一连接杆11、第二连接杆12、第三连接杆13和第四连接杆14依次固定连接并且一体成型。第一连接杆11、第二连接杆12和第三连接杆13的数量均为两根,并且两根第一连接杆11、两根第二连接杆12和两根第三连接杆13均关于对称轴呈相对设置。第四连接杆14的相对两端分别固定连接于两个第三连接杆13之间,对称轴与第四连接杆14的长度方向相垂直,并且对称轴位于第四连接杆14长度方向的中点位置处。
43.工件1还设置有若干个通孔和定位孔,若干个定位孔分别为第一定位孔143和两个第二定位孔123,第一定位孔143位于第四连接杆14,两个第二定位孔123分别位于两根第二连接杆12。若干个通孔分别分布于第一连接杆11、第二连接杆12、第三连接杆13和第四连接杆14。
44.在生产工件1的过程中,工作人员利用模具对第一连接杆11和、第二连接杆12、第三连接杆13和第四连接杆14进行浇注成型,同时第一定位孔143和第二定位孔123通过浇注成型设置在第四连接杆14和第二连接杆12处,再利用数控机床加工通孔。
45.参照图1,现有的数控加工机床包括机主体2、旋转盘21以及支撑板22,旋转盘21的数量为两个,两个旋转盘21呈相对设置,支撑板22螺栓连接于两个旋转盘21之间。支撑板22用于供工件1安装,旋转盘21用于带动支撑板22转动,进而支撑板22带动工件1转动,进而便于机主体2对工件1的进行多方位加工。
46.当需要对工件1加工通孔时,工作人员将工件1连接于支撑板22的一侧,工作人员启动数控机床,机主体2对工件1进行打孔,根据不同的加工位置,旋转盘21带动支撑板22转动,进而支撑板22带动工件1转动,便于调整机主体2在工件1的不同位置进行加工。
47.本技术实施例公开一种机械零件多点加固夹具。参照图2,一种机械零件多点加固夹具包括安装板3、按压机构和支撑机构。安装板3螺栓连接于支撑板22的一侧,安装板3与支撑板22之间相平行,进而支撑板22可带动安装板3转动,安装板3用于供按压机构和支撑机构安装,同时安装板3用于供工件1放置。安装板3设置有穿孔31,穿孔31贯穿安装板3厚度方向的相对两侧。优选的,在本实施例中,穿孔31的数量为六个,六个穿孔31间隔分布与安装板3。当机主体2对工件1进行通孔加工时,机主体2会对工件1喷射出切削液,利用穿孔31,进而便于安装板3上的切削液流出,同时利用穿孔31,进而可减轻安装板3的重量,降低旋转盘21对安装板3的支撑压力。
48.参照图3,第一连接杆11背离工件1内部的一端设置有第一抵接面111和第一支撑面112,第一抵接面111与第一支撑面112呈相对设置。第一抵接面111位于第一连接杆11背离安装板3的一侧,第一支撑面112位于第一连接杆11朝向安装板3的一侧,第一抵接面111和第一支撑面112均与安装板3相平行。
49.参照图3,具体的,按压机构包括第一转角气缸41,优选的,在本实施例中,第一转角气缸41的数量为两个,两个第一转角气缸41分别作用与两根第一连接杆11。第一转角气缸41的输出轴螺栓连接有第一压块411,第一压块411始终位于第一抵接面111背离第一支撑面112的一侧,第一转角气缸41用于驱动第一压块411滑移,第一压块411用于抵紧第一抵
接面111。第一转角气缸41背离输出轴的一端螺栓连接有第一垫块412,第一垫块412螺栓连接于安装板3。第一垫块412对第一转角气缸41实现支撑作用,并且增大了第一转角气缸41与安装板3的距离,使得第一转角气缸41输出轴与安装板3之间的最小距离大于第一抵接面111与安装板3之间的距离,进而便于第一压块411按压并抵紧第一连接杆11。
50.参照图3,具体的,支撑机构包括第一支撑缸51,优选的,在本实施例中,第一支撑缸51的数量为两个,两个第一支撑缸51分别作用与两根第一连接杆11。第一支撑缸51位于第一支撑面112与安装板3之间,第一支撑缸51的输出轴连接有第一顶块511,第一顶块511与第一支撑面112相平行,进而第一顶块511与第一压块411之间呈相对设置。第一支撑缸51的输出轴与第一顶块511背离第一支撑面112的一侧螺栓连接,第一支撑缸51用于带动第一顶块511滑移并抵紧于第一支撑面112,利用第一顶块511,进而增大了第一支撑缸51与第一支撑面112的接触面积,减少了第一支撑面112因承受压强过大而导致出现损坏的情况发生。第一支撑缸51背离第一顶块511的一端螺栓连接有承托块512,承托块512与安装板3螺栓连接,承托块512对第一支撑缸51实现支撑作用,便于第一支撑缸51驱动第一顶块511滑移并抵紧第一支撑面112。
51.当需要夹持第一连接杆11时,工作人员将工件1放置在安装板3处,使得第一抵接面111朝向第一压块411,第一支撑面112朝向第一顶块511,进而工作人员启动第一转角气缸41和第一支撑缸51,第一转角气缸41输出轴移动并带动第一压块411滑移,第一支撑缸51输出轴移动并带动第一顶块511滑移,直至第一压块411抵紧于第一抵接面111、第一顶块511抵紧于第一支撑面112,进而第一压块411和第一顶块511分别抵紧于第一连接杆11的相对两侧,对第一连接杆11实现夹持作用。
52.当需要对第一连接杆11加工通孔时,旋转盘21带动支撑板22转动,支撑板22带动安装板3转动,安装板3带动工件1转动,利用第一转角气缸41和第一支撑缸51对第一连接杆11实现夹持作用,进而减少了第一连接杆11在转动的过程中出现松动的情况发生,提高了第一连接杆11的稳定性。
53.第二连接杆12朝向工件1内部的一端设置有第二抵接面121和第二支撑面122,第二抵接面121位于第二连接杆12背离安装板3的一侧,第二支撑面122位于第二连接杆12背离安装板3的一侧。
54.参照图4,具体的,支撑组件52包括第三固定块524和第二定位销526。第三固定块524螺栓连接于安装板3,第三固定块524背离安装板3的一侧设置有第二插孔525,第二插孔525与第二定位孔123相连通。第二定位销526的相对两端分别插接配合于第二定位孔123和第二插孔525,利用第二定位销526,便于对第二连接杆12的安装位置实现定位作用。
55.参照图5,具体的,按压机构包括第二转角气缸42,优选的,在本实施例中,第二转角气缸42的数量为两个,两个第二转角气缸42分别作用与两根第二连接杆12。第二转角气缸42的输出轴螺栓连接有第二压块421,第二压块421始终位于第二抵接面121背离安装板3的一侧。第二转角气缸42用于驱动第二压块421滑移,第二压块421用于抵紧于第二抵接面121。第二转角气缸42背离输出轴的一侧螺栓连接有第二垫块422,第二垫块422螺栓连接于安装板3。利用第二垫块422,使得第二压块421与安装板3之间的最小距离大于第二抵接面121与安装板3之间的距离,进而便于第二压块421抵紧于第二抵接面121。
56.参照图5,具体的,支撑机构还包括支撑组件52,支撑组件52用于抵紧第二支撑面
122。优选的,在本实施例中,支撑组件52的数量为两个,两个支撑组件52分别作用与两根第二连接杆12。具体的,支撑组件52包括第一固定块522、第二固定块523和第二顶块521,第一固定块522、第二固定块523和第二顶块521均位于工件1的内部。第一固定块522螺栓连接于安装板3,第二固定块523螺栓连接于第一固定块522背离安装板3,第二顶块521的一端与第二固定块523背离第一固定块522的一端焊接固定,第二顶块521背离第二固定块523的一端用于抵紧于第二支撑面122。第二顶块521和第二压块421分别抵紧于第二连接杆12的相对两侧。
57.当需要对第二连接杆12进行通孔加工时,工作人员握持并移动工件1,使得第二连接杆12的第二定位孔123与第二插孔525相连通,进而工作人员继续移动第二连接杆12,使得第二定位孔123与第二定位销526插接配合,直至第二连接杆12与第三固定块524相抵接,进而对第二连接杆12的安装位置实现定位作用,同时第二顶块521抵接于第二支撑面122,工作人员启动第二转角气缸42,第二转角气缸42驱动第二压块421滑移,直至第二压块421抵紧于第二抵接面121,进而第二顶块521和第二压块421分别抵紧于第二连接杆12的相对两侧,对第二连接杆12实现支撑作用。
58.当需要对第二连接杆12加工通孔时,旋转盘21带动支撑板22转动,支撑板22带动安装板3转动,安装板3带动工件1转动,利用第二转角气缸42和第二支撑缸对第二连接杆12实现夹持作用,同时利用第二定位销526与第二定位孔123的插接配合,进而减少了第二连接杆12在转动的过程中出现松动的情况发生,提高了第二连接杆12的稳定性。
59.参照图6,第三连接杆13朝向安装板3的一侧设置有第三支撑面132,第二连接杆12背离安装板3的一侧设置有第三抵接面131,第三支撑面132和第三抵接面131分别位于第二连接杆12的相对两侧。
60.参照图6,具体的,按压机构包括第三转角气缸43,优选的,在本实施例中,第三转角气缸43的数量为两个,两个第三转角气缸43分别抵紧于两根第三连接杆13。第三转角气缸43螺栓连接于安装板3,第三转角气缸43的输出轴螺栓连接有第三压块431,第三压块431位于第三抵接面131背离安装板3的一侧。第三压块431螺栓连接有抵接螺栓432,抵接螺栓432的螺帽朝向安装板3,抵接螺栓432的螺帽用于与第三抵接面131相抵紧。
61.参照图6,具体的,支撑机构包括第三支撑缸53,优选的,在本实施例中,第三支撑缸53的数量为两个,两个第三支撑缸53分别用于抵紧两根第三连接杆13。第三支撑缸53螺栓连接于安装板3,第三支撑缸53的输出轴朝向第三支撑面132,第三支撑缸53用于抵紧于第三支撑面132。安装板3设置有供第三支撑缸53贯穿的安装孔32,使得第三支撑缸53输出轴与安装板3之间的最大距离小于第三支撑面132与安装板3之间的距离,便于第三支撑缸53的输出轴抵紧于第三支撑面132。
62.当需要夹持第三连接杆13时,工作人员将第三支撑缸53贯穿安装孔32,并且第三支撑缸53螺栓连接于安装板3,进而工作人员启动第三支撑缸53和第三转角气缸43,进而第三转角气缸43驱动抵接螺栓432滑移,直至抵接螺栓432的螺帽抵紧于第三抵接面131,第三支撑缸53的输出轴滑移,直至第三支撑缸53的输出轴抵紧于第三支撑面132,进而第三支撑缸53和第三转角气缸43抵紧于第三连接杆13的相对两侧,提高了第三连接杆13在支撑板22中的稳定性。
63.参照图6,第四连接杆14朝向安装板3的一侧设置有安装板3的一侧设置有第四支
撑面,第四连接杆14背离安装板3的一侧设置有第四抵接面,第四抵接面和第四支撑面分别位于第四连接杆14的相对两侧。
64.参照图6,具体的,按压机构包括第四转角气缸44和按压组件45,第四转角气缸44和按压组件45均位于第四连接杆14的中点位置处。第四转角气缸44螺栓连接于安装板3,第四转角气缸44的输出轴螺栓连接有第四压块441,所述第四压块441位于第四抵接面背离安装板3的一侧。
65.参照图6,具体的,按压组件45包括安装块454、抵紧块451和固定销456,所述安装块454与所述第四压块441之间螺栓连接,抵紧块451的一侧焊接固定有插块453,插块453与安装块454之间插接配合,同时安装块454设置有供插块453插接配合的插槽455。固定销456同时贯穿安装块454和插块453,使得插块453和安装块454之间固定连接。抵紧块451背离安装块454的一侧可抵紧于第四抵接面,进而抵紧于第四连接杆14的一侧。
66.参照图6和图7,具体的,支撑机构包括螺栓连接于安装板3的支撑块54,支撑块54与第四支撑面相抵紧,支撑块54用于支撑第四连接杆14。支撑块54朝向第四连接杆14的一侧设置有第一插孔542,第一插孔542与位移第四连接杆14的第一定位孔143相连通。支撑块54插接配合有第一定位销543,第一定位销543的相对两端分别与第一插孔542和第一定位孔143插接配合,进而对第一连接杆11的安装位置实现定位作用。
67.参照图6和图7,抵紧块451的长度方向设置有第一让位槽452,第一让位槽452与第四连接杆14相连通,第一让位槽452位于抵紧块451长度方向的中点位置处,进而抵紧块451长度方向的相对两端分别抵紧于第四连接杆14。支撑块54设置有第二让位槽541,第二让位槽541同时与第一让位槽452、第四连接杆14相连通。第四连接杆14的通孔位于按压组件45和支撑块54之间,利用第一让位槽452和第二让位槽541,进而便于机主体2加工第四连接杆14的通孔,减少机主体2在加工的过程中对支撑块54造成损害。
68.当需要夹持第四连接杆14时,工作人员将第一定位销543的一端插入第一插孔542内,工作人员握持并移动第四连接杆14,使第四连接杆14的第一定位孔143朝向第一插孔542,并且第一定位孔143与第一插孔542之间相连通,进而工作人员继续移动第四连接杆14,使得第一定位孔143与第一定位销543之间插接配合,直至第四连接杆14与支撑块54相抵接,进而对第四连接杆14的安装位置实现定位作用,进而工作人员再启动第四转角气缸44,第四转角气缸44的输出轴带动抵紧块451滑移,直至抵紧块451抵紧于第四抵接面,同时支撑块54抵紧于第四支撑面,进而支撑块54和抵紧块451分别抵紧于第四连接杆14的相对两侧,进而对第四连接杆14实现支撑作用。
69.本技术实施例一种机械零件多点加固夹具的实施原理为:
70.当需要夹持工件1时,工作人员先将第一定位销543插接配合与第一插孔542内,第二定位销526插接配合与第二插孔525内,工作人员握持并移动工件1,使得第一定位孔143与第一定位销543插接配合,第二定位孔123与第二定位销526插接配合,直至第二连接杆12与第三固定块524相抵接,第四连接杆14与支撑块54相抵接,进而对工件1的安装位置实现了定位作用;工作人员启动第一转角气缸41和第一支撑缸51,第一转角气缸41带动第一压块411抵紧于第一抵接面111,第一支撑缸51带动第一顶块511抵紧于第一支撑面112,进而对第一连接杆11的相对两侧实现夹持作用;工作人员启动第二转角气缸42,第二转角气缸42带动第二压块421滑移,直至第二压块421抵紧于第二抵接面121,同时第二连接杆12还与
第二顶块521相抵接配合,进而对第二连接杆12实现夹持作用;工作人员启动第三转角气缸43和第三支撑缸53,第三转角气缸43驱动第三压块431滑移,使得第三压块431抵紧于第三抵接面131,同时第三支撑缸53抵接于第三支撑面132,进而对第三连接杆13实现夹持作用;工作人员启动第四转角气缸44,第四转角气缸44驱动抵紧块451滑移,直至抵紧块451抵紧于第四抵接面,同时支撑块54抵紧于第四支撑面,进而对第四连接杆14实现夹持作用。
71.以上均为本技术的较佳实施例,并非依此限制本技术的保护范围,故:凡依本技术的结构、形状、原理所做的等效变化,均应涵盖于本技术的保护范围之内。