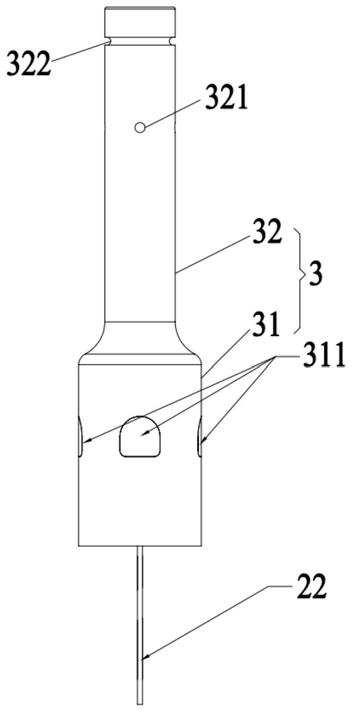
1.本实用新型涉及陶瓷发热体技术领域,具体涉及一种带外壳体陶瓷雾化芯。
背景技术:
2.目前电子烟雾化器用的多孔陶瓷发热体主要是采用金属发热丝和多孔陶瓷基体一体成型的工艺,电子烟雾化器发热体组合时多孔陶瓷发热体表面还需要包棉,组装不方便,多孔陶瓷发热体无法直接与烟油接触,影响吸油速度,导热慢。
技术实现要素:
3.为了克服现有技术中存在的缺点和不足,本实用新型的目的在于提供一种带外壳体陶瓷雾化芯,该陶瓷雾化芯结构新颖,吸油快,陶瓷雾化芯直接与烟油接触,导热更快,经多孔陶瓷基体加热雾化后烟雾通过气流道进入金属外壳的伸出部并从气孔流出,提升了该陶瓷雾化芯的雾化效率,另外,该陶瓷雾化芯不需人工包棉、组装方便、生产效率高、实用性强、节能和安全环保。
4.本实用新型的目的通过下述技术方案实现:一种带外壳体陶瓷雾化芯,包括多孔陶瓷基体、内发热件和金属外壳,所述金属外壳包括发热部和伸出部,所述多孔陶瓷基体的内部设有气流道,且所述气流道贯穿多孔陶瓷基体的上表面和下表面,所述发热部套设于所述多孔陶瓷基体的外壁;所述内发热件的中部嵌设于所述多孔陶瓷基体内并绕设于气流道的周向,内发热件的端部突伸出多孔陶瓷基体外,所述伸出部的侧壁设有若干气孔,所述气孔贯穿伸出部的侧壁与所述伸出部内部连通。
5.进一步的,所述伸出部的外侧设有环形限位槽,所述环形限位槽位于远离发热部的一端。
6.进一步的,所述发热部的侧壁设有多个供油孔。
7.进一步的,所述供油孔的孔径为0.6
‑
2.5
㎜
。
8.进一步的,所述多孔陶瓷基体的孔隙率为35
‑
65%,孔隙的孔径为1
‑
60μm。
9.进一步的,所述内发热件包括发热丝内嵌部、与发热丝内嵌部的两端连接的发热丝延伸部,所述发热丝内嵌部呈螺旋状内嵌设于多孔陶瓷基体内并绕设于气流道的周向,所述发热丝延伸部的一端延伸出多孔陶瓷基体外。
10.进一步的,所述发热丝内嵌部的中间部位与供油孔的中心对齐。
11.进一步的,所述发热部和伸出部一体成型。
12.更进一步的,所述带外壳体陶瓷雾化芯在保护氛围为还原h2气氛或n2气氛或h2和n2混合气体气氛中,在烧结800
‑
1400℃的温度下烧结1
‑
3h制得;所述金属外壳呈现银白色。
13.本实用新型的有益效果在于:本实用新型的陶瓷雾化芯结构新颖,吸油快,陶瓷雾化芯直接与烟油接触,导热更快,经多孔陶瓷基体加热雾化后烟雾通过气流道进入金属外壳的伸出部并从气孔流出,提升了该陶瓷雾化芯的雾化效率,另外,该陶瓷雾化芯不需人工包棉、组装方便、生产效率高、实用性强、节能和安全环保。
附图说明
14.图1是本实用新型的立体图;
15.图2是本实用新型的剖面结构示意图;
16.图3是本实用新型的仰视图。
17.附图标记为:1
‑
多孔陶瓷基体、11
‑
气流道、2
‑
内发热件、21
‑
发热丝内嵌部、22
‑
发热丝延伸部、3
‑
金属外壳、31
‑
发热部、311
‑
供油孔、32
‑
伸出部、321
‑ꢀ
气孔和322
‑
环形限位槽。
具体实施方式
18.为了便于本领域技术人员的理解,下面结合实施例及附图1
‑
3对本实用新型作进一步的说明,实施方式提及的内容并非对本实用新型的限定。
19.见图1
‑
3,一种带外壳体陶瓷雾化芯,包括多孔陶瓷基体1、内发热件2和金属外壳3,所述金属外壳3包括发热部31和伸出部32,所述发热部31和伸出部32一体成型,所述多孔陶瓷基体1的内部设有气流道11,且所述气流道11 贯穿多孔陶瓷基体的上表面和下表面,所述发热部31套设于所述多孔陶瓷基体1的外壁;所述内发热件2的中部嵌设于所述多孔陶瓷基体1内孔壁并绕设于气流道11的周向,内发热件2的端部突伸出多孔陶瓷基体1外,所述伸出部 32的侧壁设有若干气孔321,所述气孔321贯穿伸出部32的侧壁与所述伸出部 32内部连通。所述带外壳体陶瓷雾化芯在保护氛围为还原h2气氛或n2气氛或 h2和n2混合气体气氛中,在烧结800
‑
1400℃的温度下烧结1
‑
3h制得;所述金属外壳3呈现银白色。
20.本实施例的多孔陶瓷基体1与金属外壳3经过高温烧结制作,金属外壳3 呈现银白色,外观漂亮,有效的解决了因金属氧化造成的烟油变色的问题,而采用800
‑
1400℃高温烧结强度更好,使多孔陶瓷基体1结合得更加紧密,减少漏油风险,也不易氧化;本实施例中的陶瓷雾化芯结构新颖,吸油快,陶瓷雾化芯直接与烟油接触,导热更快,经多孔陶瓷基体1加热雾化后烟雾通过气流道11进入金属外壳3的伸出部32并从气孔321流出,提升了该陶瓷雾化芯的雾化效率,另外,该陶瓷雾化芯不需人工包棉、组装方便、生产效率高、实用性强、节能和安全环保。
21.本实施例中,所述伸出部32的外侧设有环形限位槽322,所述环形限位槽322位于远离发热部31的一端。所述发热部31的侧壁设有多个供油孔311;所述供油孔311的孔径为0.6
‑
2.5
㎜
,其中孔径优选0.6
㎜
、2.0
㎜
或2.5
㎜
。
22.本实施例通过在伸出部32的外侧设置环形限位槽322,便于陶瓷雾化芯与外接组装件进行组装时限位固定,提升了该陶瓷雾化芯组装时的稳定性以及密封性;而在金属外壳3的发热部31设置的多个不同形状的供油孔311,供油孔 311越多,吸油越均匀,雾化量越大、雾化效果越好。
23.本实施例中,所述多孔陶瓷基体1的孔隙率为35
‑
65%,孔隙的孔径为 1
‑
60μm,其中孔隙率优选35%、50%或65%,孔径优选1μm、10μm、20μm、30μm、 40μm、50μm或60μm。
24.本实施例的采用多孔陶瓷基体1,使得烟油通过供油孔311进入多孔陶瓷基体1,并与多孔陶瓷基体1直接接触,通过孔隙向内渗透再进一步加热雾化为气体,提高了雾化效率,另外。还需严格控制孔隙率和孔隙的孔径,能保证液体的烟油稳定、均匀地渗透至多孔陶瓷基体1的内部进一步加热雾化成气体。
25.本实施例中,所述内发热件2包括发热丝内嵌部21、与发热丝内嵌部21的两端连接的发热丝延伸部22,所述发热丝内嵌部21呈螺旋状内嵌设于多孔陶瓷基体1内孔壁并绕设于气流道11的周向,所述发热丝延伸部22的一端延伸出多孔陶瓷基体1外。所述发热丝内嵌部21的中间部位与供油孔311的中心对齐。
26.本实施例中发热丝内嵌部21为主要的加热部位,而连接在发热丝内嵌部 21的两端连接的发热丝延伸部22起到接线柱或导线的作用,与电源连接,使得螺旋状发热丝内嵌部21接电后产生热量,进而对多孔陶瓷基体1进行加热,提高了多孔陶瓷基体1升温速率;而螺旋状发热丝内嵌部21沿着气流道11的中心轴线延伸,螺旋式设置发热均匀可对多孔陶瓷基体1均匀导热,对通过多孔陶瓷基体1向内渗透的烟油进行均匀加热,使得烟油受热雾化为气体后从气流道11内吸入,实用性高。
27.上述实施例为本实用新型较佳的实现方案,除此之外,本实用新型还可以其它方式实现,在不脱离本实用新型构思的前提下任何显而易见的替换均在本实用新型的保护范围之内。