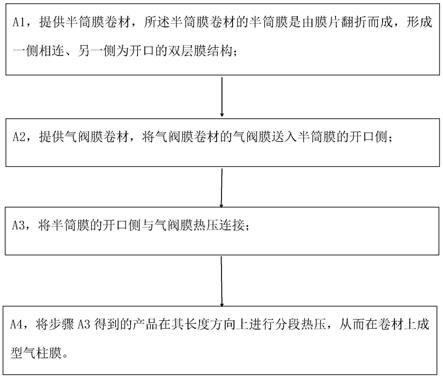
1.本发明涉及气柱膜的生产工艺领域,具体涉及一种气柱膜的制备工艺和实现该制备工艺的制备装置。
背景技术:
2.气柱膜又称气柱袋,是使用自然空气填充的新式包装材料。目前市场上气柱袋的生产均为上下两层卷料片膜进行上料制袋,此种方式设备需配备双层上料架,因是两单卷,会出现上下膜长度不一的情况,导致生产浪费,且生产过程中两层片膜不可避免出现错位、上下膜拉伸程度不同等情况,严重时出现底部未热封到的情况,导致大批量的不合格产品。
技术实现要素:
3.为此,本发明为解决上述问题,提供一种气柱膜的制备工艺和实现该制备工艺的制备装置。
4.为实现上述目的,本发明提供的技术方案如下:
5.一种气柱膜的制备工艺,包括如下步骤:
6.a1,提供半筒膜卷材,所述半筒膜卷材的半筒膜是由膜片翻折而成,形成一侧相连、另一侧为开口的双层膜结构;
7.a2,提供气阀膜卷材,将气阀膜卷材的气阀膜送入半筒膜的开口侧;
8.a3,将半筒膜的开口侧与气阀膜热压连接;
9.a4,将步骤a3得到的产品在其长度方上进行分段热压,从而在卷材上成型气柱膜。
10.进一步的,在步骤a4之后,还包括步骤a5,在相邻二个气柱膜之间进行折痕。
11.进一步的,步骤a5中,通过热压的方式在相邻二个气柱膜之间进行热压形成折痕点。
12.进一步的,在步骤a2中,提供开口打开机构,所述开口打开机构具有并列设置的上传导辊和下传导辊,所述半筒膜的开口侧的上膜和下模分别绕过上传导辊的上表面和下传导辊的下表面,所述气阀膜穿过上传导辊和下传导辊的中间位置,进而实现将气阀膜送入半筒膜的开口侧。
13.一种气柱膜的制备装置,包括机架以及设置在机架上的半筒膜放料架、气阀膜放料架、开口打开机构、开口热压机构和分段热压机构;所述开口打开机构设置在半筒膜放料架和气阀膜放料架的传输后端,所述开口打开机构具有并列设置的上传导辊和下传导辊,所述开口热压机构设置在开口打开机构的传输后端,所述分段热压机构设置在开口热压机构的传输后端。
14.进一步的,所述开口打开机构与半筒膜放料架处于同一平面;所述气阀膜放料架与开口打开机构所在平面不相同,所述气阀膜放料架与开口打开机构之间还设置有转角机构。
15.进一步的,所述开口打开机构与半筒膜放料架之间还设置有位于同一平面的半筒
膜输送辊组件,所述半筒膜输送辊组件具有交错设置的二排输送辊,所述半筒膜输送辊组件的相邻二个输送辊之间设置有纠偏感应器。
16.进一步的,所述转角机构与气阀膜放料架之间设置有位于同一平面的气阀膜输送辊组件,所述气阀膜输送辊组件具有交错设置的二排输送辊。
17.进一步的,所述分段热压机构的传输后端还设置有折痕热压机构。
18.进一步的,所述机架上还设置有收料辊,所述收料辊设置在折痕热压机构的传输后端。
19.通过本发明提供的技术方案,具有如下有益效果:
20.本工艺采用由膜片翻折而成半筒膜,半筒膜自带双层膜且单边开口,有效避免双层膜单独送料导致的上下膜长度不一、错位以及拉伸程度不同等导致的异常情况,且底部不需要进行热封,减去产品底部热封及毛边尺寸,在同款产品可节省原膜宽幅5-10毫米左右。
21.同时,在制备装置上,可至少省去原制备装置中的放料架一套、送料电机一套以及边封设备一套的投入,使得结构更为简单,制备成本更低。
附图说明
22.图1所示为实施例中气柱膜的制备工艺的流程框图;
23.图2所示为实施例中气柱膜的制备装置的结构示意图;
24.图3所示为实施例中气柱膜的制备装置的部分结构示意图。
具体实施方式
25.为进一步说明各实施例,本发明提供有附图。这些附图为本发明揭露内容的一部分,其主要用以说明实施例,并可配合说明书的相关描述来解释实施例的运作原理。配合参考这些内容,本领域普通技术人员应能理解其他可能的实施方式以及本发明的优点。图中的组件并未按比例绘制,而类似的组件符号通常用来表示类似的组件。
26.现结合附图和具体实施方式对本发明进一步说明。
27.实施例一
28.参照图1所示,本实施例提供的一种气柱膜的制备工艺,包括如下步骤:
29.a1,提供半筒膜卷材,所述半筒膜卷材的半筒膜是由膜片翻折而成,形成一侧相连、另一侧为开口的双层膜结构。该半筒膜自带双层膜,且一侧为封闭结构。
30.a2,提供气阀膜卷材,将气阀膜卷材的气阀膜送入半筒膜的开口侧。
31.具体的,本实施例中,为了便于将气阀膜卷材的气阀膜送入半筒膜的开口侧,需要对半筒膜的开口侧先进行打开。为此,本步骤中,提供开口打开机构,具体如图3所示,所述开口打开机构具有并列设置的上传导辊111和下传导辊112,所述半筒膜1的开口侧的上膜和下模分别绕过上传导辊111的上表面和下传导辊112的下表面,所述气阀膜2穿过上传导辊111和下传导辊112的中间位置,进而实现将气阀膜2送入半筒膜1的开口侧。如此,就可以很好的将半筒膜1的开口侧打开,便于气阀膜2的送入。
32.a3,将半筒膜的开口侧与气阀膜热压连接;使得气阀膜装配至半筒膜的开口侧。具体的,该连接结构以及热压方式为现有技术,在此不再详细描述。
33.a4,将步骤a3得到的产品在其长度方向上进行分段热压,从而在卷材上成型气柱膜。具体的,该分段热压的方式也为现有技术,在此不再详细描述。
34.如此,就实现了气柱膜的成型。
35.再具体的,本实施例的产品是以卷材的方式进行收集,为此,为了后续更便于获取单个的气柱膜,本实施例中,在步骤a4之后还包括步骤a5,在相邻二个气柱膜之间进行折痕。完成折痕操作后,再进行收卷。增加折痕结构,后续便于分离操作。采用该种以卷材收卷的方式,便于收纳和运输;在需要使用时再将单个气柱膜进行裁剪。
36.再具体的,通过热压的方式在相邻二个气柱膜之间进行热压形成折痕点,热压操作简单,容易实现。当然的,在其它实施例中,也可以通过冲头冲压等方式进行操作。
37.参照图2和图3所示,本实施例还提供一种用于实现上述工艺的气柱膜的制备装置,包括机架100以及设置在机架100上的半筒膜放料架11、气阀膜放料架21、开口打开机构、开口热压机构401和分段热压机构402;所述开口打开机构设置在半筒膜放料架11和气阀膜放料架21的传输后端,所述开口打开机构具有并列设置的上传导辊111和下传导辊112,所述开口热压机构401设置在开口打开机构的传输后端,所述分段热压机构402设置在开口热压机构401的传输后端。
38.具体的,上述的传输后端是指在卷材的传输时,先经过的位置为传输前端,后经过的位置为传输后端;如卷材先经过开口打开机构、再经过开口热压机构401,因此,所述开口热压机构401设置在开口打开机构的传输后端,以此类推。
39.进行作业时,半筒膜卷材放置在半筒膜放料架11上,半筒膜1经过开口打开机构,半筒膜1的开口侧的上膜和下模分别绕过上传导辊111的上表面和下传导辊112的下表面,进而将开口撑开。气阀膜卷材放置在气阀膜放料架21上,气阀膜2穿过上传导辊111和下传导辊112的中间位置,进而实现将气阀膜2送入半筒膜1的开口侧。之后,经开口打开机构输出的膜层传输至开口热压机构401内,开口热压机构401将半筒膜1的开口侧与气阀膜2进行热压连接;使得气阀膜2装配至半筒膜1的开口侧。经开口热压机构401输出的膜层传输至分段热压机构402,并通过分段热压机构402进行分段热压,从而在卷材上成型气柱膜。
40.具体的,机架100上还设置有折痕热压机构403和收料辊13,折痕热压机构403设置在分段热压机构402的传输后端,经分段热压机构402输出的产品进入折痕热压机构403,折痕热压机构403在相邻二个气柱膜之间进行热压形成折痕点。之后经折痕热压机构403输出的产品通过收料辊13进行收料。
41.进一步的,本实施例中,所述半筒膜放料架11和气阀膜放料架21均采用气胀轴固定膜卷,固定牢固,且操作简便。当然的,在其它实施例中,也可以采用其它结构替代。
42.进一步的,为了防止在复合前半筒膜1与气阀膜2的传输有干涉,本实施例中,所述开口打开机构与半筒膜放料架11处于同一平面;所述气阀膜放料架21与开口打开机构所在平面不相同,所述气阀膜放料架21与开口打开机构之间还设置有转角机构209。如此,半筒膜1与气阀膜2就能够在不同平面进行传输,如半筒膜1在位于前方的竖直平面上进行传输,而气阀膜2在位于后方的竖直平面上进行传输;相互之间不干涉。当需要进入开口打开机构时,气阀膜2通过转角机构209的转向进入半筒膜1所在平面,从而穿过上传导辊111和下传导辊112的中间位置,与半筒膜1的开口侧相配合。
43.再具体的,本实施例中,所述开口打开机构与半筒膜放料架11之间还设置有位于
同一平面的半筒膜输送辊组件,所述半筒膜输送辊组件具有交错设置的二排输送辊,半筒膜1在二排输送辊之间往复传输,如图3中,四个输送辊103、105、107和109为一排,四个输送辊104、106、108和110为另一排,半筒膜1经卷材输出后,依次经过输送辊101、102、103、104、105、106、107、108、109以及110,形成m型缠绕张力结构,张力更好。之后进入开口打开机构的上传导辊111和下传导辊112。
44.进一步的,所述半筒膜输送辊组件的相邻二个输送辊之间(本具体实施例中为输送辊101和102之间)设置有纠偏感应器12,m型缠绕张力结构配合纠偏感应器12,使得半筒膜1的传输更为精准。
45.同样的,所述转角机构209与气阀膜放料架21之间设置有位于同一平面的气阀膜输送辊组件,所述气阀膜输送辊组件具有交错设置的二排输送辊,气阀膜2在二排输送辊之间往复传输,如图3中,气阀膜输送辊组件包括输送辊201、202、203、204、205、206、207和208;其中,三个输送辊201、203和205为一排,三个输送辊202、204和206为另一排;气阀膜2经卷材输出后,依次经过输送辊201、202、203、204、205和206形成m型缠绕张力结构,张力更好;之后再经过输送辊207和208进入转角机构209。
46.当然的,在其它实施例中,半筒膜1和气阀膜2的传输方式不局限于此。
47.再具体的,在折痕热压机构403和收料辊13之间设置有收料传输辊组件,收料传输辊组件也具有二排输送辊,产品膜在二排输送辊之间往复传输,如图2中,气阀膜输送辊组件包括输送辊120、121、122、123、124、125、126、127、128、129、130和131,其中,输送辊121、123、125、127、129和131为一排,输送辊120、122、124、126、128和130为另一排;由折痕热压机构403输出的产品膜依次经过输送辊120、121、122、123、124、125、126、127、128、129、130和131形成m型缠绕张力结构,保持收卷的张力。最后进入收料辊13收卷。
48.本工艺采用由膜片翻折而成半筒膜1,半筒膜1自带双层膜且单边开口,有效避免双层膜单独送料导致的上下膜长度不一、错位以及拉伸程度不同等导致的异常情况,且底部不需要进行热封,减去产品底部热封及毛边尺寸,在同款产品可节省原膜宽幅5-10毫米左右。
49.同时,在制备装置上,可至少省去原制备装置中的放料架一套、送料电机一套以及边封设备一套的投入,使得结构更为简单,制备成本更低。
50.实施例二
51.本实施例提供的一种气柱膜的制备工艺,与实施例一提供的气柱膜的制备工艺大致相同,不同之处在于:本实施例中,当完成步骤a4形成气柱膜之后,进入步骤a5’,直接通过分切的方式将单个气柱膜冲切分离,得到单个的气柱膜。而卷材上的废料通过收料辊进行收集。
52.本实施例提供的一种气柱膜的制备装置,与实施例一提供的气柱膜的制备装置大致相同,不同之处在于:本实施例中,在分段热压机构402的传输后端设置的是分切机构(未示出),所述分切机构进行分切将单个气柱膜切除分离,得到单个的气柱膜。
53.当然的,在其它实施例中,在分段热压机构402的传输后端也可以设置其它的作业机构,可以直接进行收卷。
54.尽管结合优选实施方案具体展示和介绍了本发明,但所属领域的技术人员应该明白,在不脱离所附权利要求书所限定的本发明的精神和范围内,在形式上和细节上可以对
本发明做出各种变化,均为本发明的保护范围。