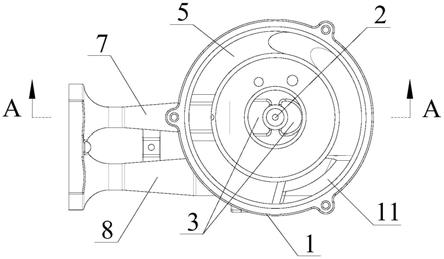
1.本实用新型涉及厨房燃气用具技术领域,尤其涉及一种双通道中心燃气通道结构及其燃烧器。
背景技术:
2.燃烧器,又称燃气灶,是一种以液化石油气(液态)、人工煤气、天然气等气体燃料进行直火加热的厨房日常生活用具。目前市场上的燃烧器包括炉头座头,燃气灶头用于集成燃气和空气并燃烧,从而产生点火加热的烹饪效果。随着社会进步和科学技术的发展,越来越多的燃烧器产品进入了普通大众家庭,并得到广泛应用。
3.然而,现有技术中的燃烧器存在以下技术缺陷和不足:传统燃烧器炉头座的中心燃气通道直喷处的燃气和中心侧部的燃气压力、气流量大小一致,而在烹饪弧形锅具时,中心燃气通道直喷处离锅底部较近,中心侧部则离锅底部较远,从而容易引起中心燃气通道直喷处的燃气燃烧不充分,一方面会影响对锅具的烹饪效果,另一方面也会使中心处的火焰呈黄色,导致燃气燃烧能效低且废气排放量高。
4.因此,现有技术中亟需发明一种燃烧充分、燃烧能效高且废气排放低的燃烧器。
技术实现要素:
5.为了克服上述现有技术所述的至少一种缺陷,本实用新型提供一种双通道中心燃气通道结构及其燃烧器,该双通道中心燃气通道结构及其燃烧器结构设计简单合理、燃气燃烧充分、燃气燃烧能效高以及废气排放低的特点。
6.本实用新型为解决其问题所采用的技术方案是:
7.一种双通道中心燃气通道结构,其包括:
8.一环通道,所述一环通道的底部和顶部分别设有第一底部通孔和顶部通孔;
9.二环通道,所述二环通道环绕设置在所述一环通道的外侧,且所述二环通道的底部设有第二底部通孔;
10.其中,所述第一底部通孔的大小小于所述第二底部通孔的大小;
11.并且,所述顶部通孔的大小大于所述第一底部通孔的大小,以使所述一环通道呈底部小、顶部大的通道结构。
12.进一步地,所述第一底部通孔为锥形孔,且所述锥形孔的顶部开口大于其底部开口。
13.基于同一种设计思路,本实用新型还提供了一种包括以上所述的双通道中心燃气通道结构的燃烧器,该燃烧器还包括炉头座,所述炉头座的中部设有所述双通道中心燃气通道结构。
14.进一步地,所述炉头座还设有中心腔体,所述中心腔体和所述一环通道、所述二环通道相连通,且所述中心腔体中设有向上延伸形成的第一圆弧形侧壁。
15.进一步地,还包括外环燃气通道结构,所述外环燃气通道结构包括外环通道,所述
外环通道设置在所述炉头座的外周侧。
16.进一步地,所述外环燃气通道结构还包括外环腔体,所述外环腔体和所述外环通道相连通,且所述外环腔体设有沿所述外环通道倾斜向上延伸形成的第二圆弧形侧壁。
17.进一步地,还包括燃气分流片,所述燃气分流片设置在所述外环通道中,且和所述外环腔体相对应设置。
18.进一步地,还包括和所述炉头座固定装配连接的中心引射管和外环引射管,所述中心引射管和所述双通道中心燃气通道结构相连通,所述外环引射管和所述外环燃气通道结构相连通;
19.并且,所述外环引射管避开所述外环腔体设置,以使二者互不干涉。
20.进一步地,所述中心引射管、所述外环引射管和所述炉头座的连接部设置在所述炉头座的正下方区域。
21.进一步地,所述中心引射管和所述外环引射管的端部均设有子母槽,所述炉头座插入所述子母槽设置,以使所述中心引射管、所述外环引射管和所述炉头座固定装配连接在一起
22.综上所述,本实用新型提供的双通道中心燃气通道结构及其燃烧器相比于现有技术,至少具有以下技术效果:
23.1)本实用新型提供的双通道中心燃气通道结构及其燃烧器,其中一环通道的第一底部通孔小于二环通道的第二底部通孔,从而使一环通道处(也即中心处)的燃气气压和出气量小于二环通道处的燃气气压和出气量,实现燃气通道中心处的燃气充分燃烧;
24.2)本实用新型提供的双通道中心燃气通道结构及其燃烧器,其中通过控制第一底部通孔的直径大小,即可实现对一环通道和二环通道中的燃气气压、出气量的比例控制,从而使该中心燃气通道结构可适配于不同弧度大小的锅具,满足用户的不同使用需求;
25.3)本实用新型提供的双通道中心燃气通道结构及其燃烧器,其中一环通道中的第一底部通孔小于其顶部通孔,使其整体呈顶部大、底部小的通道结构,可确保进入一环通道中的燃气和空气能够充分混合,从而进一步提高中心处燃气的燃烧效果,提高其燃烧能效,废气排放量低;
26.4)本实用新型提供的双通道中心燃气通道结构及其燃烧器,其中通过设置中心腔体和外环腔体,可使中心引射管和一环通道、二环通道之间,以及外环引射管和外环通道之间平缓过渡,上升坡度小,从而使燃气充分混合且燃气流通更顺畅,负荷大、能效高且废气排放量低;
27.5)本实用新型提供的双通道中心燃气通道结构及其燃烧器,其中引射管和炉头座的连接部设置在炉头座的正下方区域,也即设置在炉头座的直径范围内,可有效延长引射管的长度,强化引射性能,确保流入引射管的燃气和空气可在引射管中充分混合,强化燃气混合效果。
附图说明
28.图1为本实用新型的燃烧器的第一结构示意图;
29.图2为图1所示的a-a剖面示意图;
30.图3为本实用新型的炉头座的第一结构示意图;
31.图4为本实用新型的炉头座的第二结构示意图;
32.图5为本实用新型的燃烧器的第二结构示意图;
33.图6为本实用新型的中心引射管和外环引射管的结构示意图;
34.其中,附图标记含义如下:
35.1、炉头座;2、一环通道;21、第一底部通孔;22、顶部通孔;3、二环通道;31、第二底部通孔;4、中心腔体;41、第一圆弧形侧壁;5、外环通道;6、外环腔体;61、第二圆弧形侧壁;7、中心引射管;8、外环引射管;9、连接部;10、子母槽;11、燃气分流片。
具体实施方式
36.为了更好地理解和实施,下面将结合本实用新型实施例中的附图,对本实用新型实施例中的技术方案进行清楚、完整地描述。
37.在本实用新型的描述中,需要说明的是,术语“上”、“下”、“前”、“后”、“左”、“右”、“竖直”、“水平”、“顶”、“底”“内”、“外”等指示的方位或位置关系为基于附图所示的方位或位置关系,仅是为了便于描述本实用新型和简化描述,而不是指示或暗示所指的装置或元件必须具有特定的方位、以特定的方位构造和操作,因此不能理解为对本实用新型的限制。
38.除非另有定义,本文所使用的所有的技术和科学术语与属于本实用新型的技术领域的技术人员通常理解的含义相同。本文中在本实用新型的说明书中所使用的术语只是为了描述具体的实施例的目的,不是旨在限制本实用新型。
39.参见图1和图2所示,根据本实用新型的实施例,双通道中心燃气通道结构包括:
40.一环通道2,所述一环通道2的底部和顶部分别设有第一底部通孔21 和顶部通孔22。
41.二环通道3,所述二环通道3环绕设置在所述一环通道2的外侧,且所述二环通道3的底部设有第二底部通孔31。
42.在该实施例的技术方案中,所述第一底部通孔21的大小小于所述第二底部通孔31的大小。具体来说,由于一环通道2的第一底部通孔21小于二环通道3的第二底部通孔31,从而使一环通道2处(也即该中心燃气通道结构的中心处)的燃气气压和出气量均小于二环通道3处的燃气气压和出气量,也即降低了一环通道2处(也即中心处)的燃气气压和出气量,使比较靠近弧形锅具底部的中心处的燃气燃烧更充分,燃烧热量更加聚集。通过该结构设计方式,一方面可以提高中心处燃气的燃烧效率,提高对锅具的烹饪效果;另一方面,中心处火焰燃烧充分,可提高燃气燃烧的能效,负荷高且减少其废气排放量。
43.更进一步来说,通过对一环通道2的第一底部通孔21直径大小的具体设置,即可实现第一底部通孔21和第二底部通孔31比例大小的控制,也即实现对一环通道2和二环通道3中的燃气气压、出气量的比例控制,从而使该中心燃气通道结构可适配于不同弧度大小的锅具,进而满足用户的不同使用需求。
44.此外,在该实施例的技术方案中,所述顶部通孔22的大小大于所述第一底部通孔21的大小,以使所述一环通道2呈底部小、顶部大的通道结构。具体而言,通过一环通道2的整体呈顶部大、底部小的结构设计方式,可确保在实现降低一环通道2的燃气气压、燃气量的同时,还能使进入一环通道2中的燃气和空气能够充分混合,实现两环一控(也即由同一中心引射管引出),从而进一步提高中心处燃气的燃烧效果,提高其燃烧能效,废气排放量
低。
45.参见图2所示,该实施例的进一步方案中,所述第一底部通孔21为锥形孔,且所述锥形孔的顶部开口大于其底部开口。在该进一步的技术方案中,通过将第一底部通孔21设置为下小上大的锥形孔,可使一环通道2的底部至顶部平缓过渡,在确保减少进入一环通道2的燃气量以及降低一环通道2中燃气气压的同时,还能确保进入一环通道2中的燃气和空气能够在足够的空间中充分混合,提高中心燃气通道中心处的燃烧效果,燃烧能效高且废气排放量低。
46.基于同一种设计思路,本实用新型还提供了一种燃烧器的实施例,该燃烧器包括以上实施例所述的双通道中心燃气通道结构。
47.参见图1和图2所示,在该实施例的技术方案中,燃烧器还包括炉头座1,所述双通道中心燃气通道结构设置在所述炉头座1的中部,用于对锅具的中部进行加热。
48.参见图2、图3和图5所示,在该实施例的进一步方案中,所述炉头座 1还设有中心腔体4,所述中心腔体4和所述一环通道2、所述二环通道3 相连通,且所述中心腔体4中设有向上延伸形成的第一圆弧形侧壁41。在该进一步的技术方案中,中心腔体4中设有和一环通道2、二环通道3相连通且向上延伸形成的第一圆弧形侧壁41,也即中心腔体4形成圆弧过渡,确保从中心引射管引入的燃气和空气混合更充分、流通更顺畅且负荷高,降低燃烧产生的废气排放量。
49.参见图1和图2所示,在该实施例的优选方案中,该燃烧器还包括外环燃气通道结构,所述外环燃气通道结构包括外环通道5,所述外环通道5 设置在所述炉头座1的外周侧。具体来说,外环燃气通道结构中的外环通道5设置在炉头座1的外周侧,也即环绕一环通道2和二环通道3设置,用于对锅具的外侧部进行加热。
50.参见图3、图4和图5所示,在该实施例的进一步方案中,所述外环燃气通道结构还包括外环腔体6,所述外环腔体6和所述外环通道5相连通,且所述外环腔体6设有沿所述外环通道5倾斜向上延伸形成的第二圆弧形侧壁61。在现有技术的技术方案中,外环引射管通常和炉头座的环形通道干涉,严重影响外环引射管的引射能力;并且,外环引射管和环形通道连接处的上升坡道大,容易引起燃气直接上升,导致燃气混合不充分,燃烧效果差。而在该进一步的技术方案中,通过在外环引射管和外环通道5之间设置沿外环通道5倾斜向上延伸的外环腔体6,可使外环引射管和外环通道5之间平缓过渡,二者互不干涉,燃气上升坡度小,提高引射管的引射能力,从而使燃气充分混合;并且,沿外环通道5倾斜向上延伸的外环腔体6容易使燃气形成螺旋式环形上升,从而进一步强化燃气混合效果,提高燃烧效率。
51.参见图1所示,在该实施例的更进一步方案中,燃烧器还包括燃气分流片11,所述燃气分流片11设置在所述外环通道5中,且和所述外环腔体 61相对应设置。具体而言,在外环通道5上设置和外环腔体61相对应的燃气分流片11,可起到在竖直方向起到阻挡燃气的作用,防止外环腔体61流出的燃气直接上升,从而进一步确保外环腔体61流入外环通道5的燃气形成螺旋式环形上升。此外,燃气分流片11可对燃气起到扰流、分流效果,使燃气混合更充分,并使火盖火焰四周更均匀。
52.参见图1和图5所示,在本实用新型的另一个实施例中,燃烧器还包括和所述炉头座1固定装配连接的中心引射管7和外环引射管8,所述中心引射管7和所述双通道中心燃气通道结构相连通,所述外环引射管8和所述外环燃气通道结构相连通。在该实施例的技术方
案中,中心引射管7用于为一环通道2、二环通道3输送燃气,外环引射管8用于为外环通道5输送燃气。二者用于喷入燃气和空气,从而使燃气和空气气流在内部充分混合,起到良好的引射效果。更为具体来说,中心引射管7和双通道中心燃气通道结构中的中心腔体4相连通,从而通过中心腔体4向一环通道2、二环通道3输送燃气;外环引射管8和外环燃气通道结构中的外环腔体6相连通,从而通过外环腔体6向外环通道5输送燃气。
53.更为具体来说,所述外环引射管8避开所述外环腔体61设置,以使二者互不干涉。其中,外环引射管8和外环燃气通道结构中的环形设置的外环腔体61互不干涉,从而可以显著提高外环引射管8的引射能力,进而确保该燃烧器的负荷大,能效高,且可降低其废气排放量。
54.参见图5所示,在该实施例的优选技术方案中,所述中心引射管7、所述外环引射管8和所述炉头座1的连接部9设置在所述炉头座1的正下方区域。在现有技术的技术方案中,由于空间狭小,传统引射管和炉头座之间的连接处设置在炉头座的直径外侧,从而导致整个引射管长度较短,引射管内的燃气和空气无法充分混合,引射性能差,燃气混合效果差。而在该优选技术方案中,将中心引射管7、外环引射管8和炉头座1的连接部9 (也即二者的固定连接位置)设置在炉头座1的正下方区域,也即设置在炉头座1的直径范围内,可有效延长中心引射管7和外环引射管8的长度,强化引射性能,确保流入引射管的燃气和空气可在引射管中充分混合,强化燃气混合效果。
55.参见图6所示,在该实施例的另一个优选技术方案中,所述中心引射管7和所述外环引射管8的端部均设有子母槽10,所述炉头座1插入所述子母槽10设置,以使所述中心引射管7、所述外环引射管8和所述炉头座 1固定装配连接在一起。在该优选技术方案中,子母槽10即为中心引射管 7和外环引射管8的端部朝向内侧凹进且具有一定深度的凹腔。具体装配中心引射管7、外环引射管8和炉头座1时,将炉头座1对准子母槽10并插入,以完成三者的初步装配操作;然后再通过外部连接部件(如螺栓、螺丝或者螺钉等)分别穿过中心引射管7和炉头座1、外环引射管8和炉头座1,即可最终完成中心引射管7和炉头座1、外环引射管8和炉头座1的固定装配连接,结构设计简单合理且操作简便。
56.综上所述,本实用新型提供的双通道中心燃气通道结构及其燃烧器,其中一环通道2的第一底部通孔21小于二环通道3的第二底部通孔31,从而使一环通道2处(也即中心处)的燃气气压和出气量小于二环通道3处的燃气气压和出气量,实现燃气通道中心处的燃气充分燃烧;进一步地,通过控制第一底部通孔21的直径大小,即可实现对一环通道2和二环通道 3中的燃气气压、出气量的比例控制,从而使该中心燃气通道结构可适配于不同弧度大小的锅具,满足用户的不同使用需求;更进一步地,一环通道2 中的第一底部通孔21小于其顶部通孔22,使其整体呈顶部大、底部小的通道结构,可确保进入一环通道2中的燃气和空气能够充分混合,从而进一步提高中心处燃气的燃烧效果,提高其燃烧能效,废气排放量低。并且,本实用新型提供的双通道中心燃气通道结构及其燃烧器,其中通过设置中心腔体4和外环腔体6,可使中心引射管7和一环通道2、二环通道3之间以及外环引射管8和外环通道5之间平缓过渡,上升坡度小,从而使燃气充分混合且燃气流通更顺畅,负荷大、能效高且废气排放量低。此外,本实用新型通过将中心引射管7、外环引射管8和炉头座1的连接部设置在炉头座1的正下方区域,也即设置在炉头座1的直径范围内,可有效延长中心引射管7和外环引射管8的长度,强化引射性能,确保流入引射管的燃气和空气可在引射管中充分混
合,强化燃气混合效果。
57.本实用新型方案所公开的技术手段不仅限于上述实施方式所公开的技术手段,还包括由以上技术特征任意组合所组成的技术方案。应当指出,对于本技术领域的普通技术人员来说,在不脱离本实用新型原理的前提下,还可以做出若干改进和润饰,这些改进和润饰也视为本实用新型的保护范围。