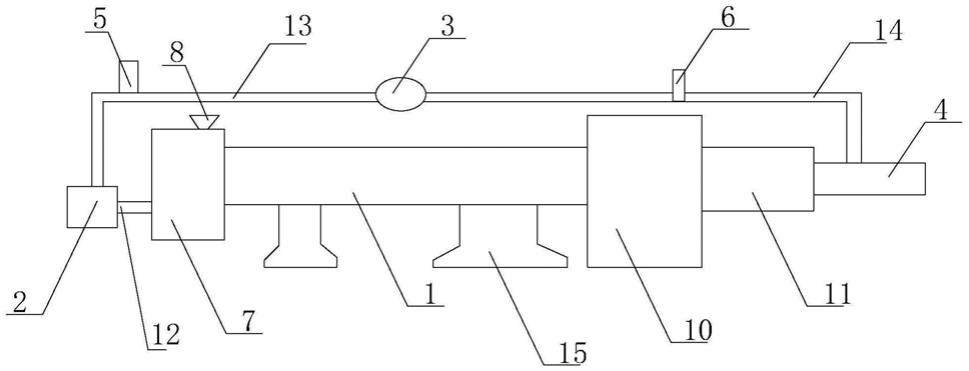
1.本技术涉及活性炭生产加工领域,尤其涉及一种活性炭炭化炉尾气余热回收利用装置。
背景技术:
2.在煤质活性炭的生产过程中,炭化是主要的热处理工序之一,炭化过程中大部分非炭元素-氢和氧因原料的高温分解首先以气体形式被排除,而获释的元素碳原子则组合成通称为基本石墨微晶的有序结晶生成物。
3.在利用炭化炉对物料进行碳化处理时,通常需要在焚烧室处用天然气点火干烘到1000-1200℃之后,通过引风机将高温热源和烟气一同引至炭化炉中,使炭化炉从炉头到炉尾形成温度梯度,来满足炭化工艺的需求,但是,现有的炭化炉在使用的过程中,产生的高温烟气大多都是经脱硫处理后直接排放到大气中,烟气热量利用率低,且存在燃气资源浪费和活性炭生产能耗高的问题。
技术实现要素:
4.本技术提供了一种活性炭炭化炉尾气余热回收利用装置,解决了现有技术中在利用炭化炉对物料进行碳化的过程中,烟气热量利用率低,且存在燃气资源浪费和活性炭生产能耗高的问题。
5.为解决上述技术问题,本技术提供了一种活性炭炭化炉尾气余热回收利用装置,包括:
6.通过第一烟气管道与炭化炉的沉降室下部出口连通的除焦池,所述除焦池出口处通过连接管道连通有后置焚烧室,所述除焦池出口处通过第二烟气管道连通有耐高温高压风机,所述耐高温高压风机的出口处通过第三烟气管道连通有点火装置,所述点火装置的一侧设置有前置焚烧室,所述前置焚烧室的一侧连通设置有蓄热室,所述蓄热室与所述炭化炉连通,所述炭化炉靠近所述蓄热室的一端下侧设置有出料管,所述沉降室的上侧倾斜设置有进料管。
7.优选地,所述第二烟气管道上还设置有防爆阀,所述第三烟气管道上还设置有气体止回阀。
8.优选地,所述蓄热室的内侧壁还设置有孔状格子砖。
9.优选地,所述点火装置包括点火总成、与所述第三烟气管道连通的气体混合室和螺旋风机,所述气体混合室与所述前置焚烧室连通设置,所述螺旋风机设置于所述气体混合室和所述前置焚烧室之间,所述点火总成设置于所述气体混合室外。
10.优选地,所述炭化炉通过支撑底座进行支撑固定。
11.优选地,所述前置焚烧室和所述点火装置的连接处还连通设置有供氧风机。
12.优选地,所述后置焚烧室的出口处连通设置有余热锅炉,所述余热锅炉的排烟管道上连通设置有引风机,所述引风机的出口处连通设置有湿法脱硫塔,所述湿法脱硫塔的
出口处连通设置有湿电除尘器。
13.相比于现有技术,本技术所提供的一种活性炭炭化炉尾气余热回收利用装置,包括通过第一烟气管道与炭化炉的沉降室下部出口连通的除焦池,除焦池出口处通过连接管道连通有后置焚烧室,除焦池出口处通过第二烟气管道连通有耐高温高压风机,耐高温高压风机的出口处通过第三烟气管道连通有点火装置,点火装置的一侧设置有前置焚烧室,前置焚烧室的一侧连通设置有蓄热室,蓄热室与炭化炉连通,炭化炉靠近蓄热室的一端下侧设置有出料管,沉降室的上侧倾斜设置有进料管。
14.由此可见,应用本装置,在实际使用时,炭化炉运行过程中产生的尾气(可燃烟气)可通过第一烟气管道进入到除焦池,通过除焦池对烟气中的粉尘进行降尘处理,降尘处理后的一部分可燃烟气可通过耐高温高压风机经第二烟气管道和第三烟气管道引至点火装置中,通过点火装置将可燃烟气和空气混合点火后输送至前置焚烧室进行焚烧,经过焚烧后的烟气形成高温热能进入蓄热室以便对燃烧不充分的烟气进一步焚烧,蓄热室中的高温热能可以返回炭化炉参与炭化,可实现对一部分烟气的回收利用,提高烟气热量利用率,减少燃气燃料的使用,实现环保生产和活性炭生产低能耗。降尘处理后的另一部分烟气可通过连接管道进入后置焚烧室进行换热处理后排放。
附图说明
15.为了更清楚的说明本技术的技术方案,下面将对实施例中所需要使用的附图作简要的介绍,显而易见地,对于本领域普通技术人员而言,在不付出创造性的前提下,还可以根据这些附图获得其他的附图。
16.图1为本实用新型实施例所提供的一种活性炭炭化炉尾气余热回收利用装置结构示意图;
17.图2为本实用新型实施例所提供的一种活性炭炭化炉尾气余热回收利用装置剖面结构示意图;
18.图3为本实用新型实施例所提供的一种第二烟气管道与耐高温高压风机和除焦池的连接结构示意图;
19.图中,1炭化炉,2除焦池,3耐高温高压风机,4点火装置,5防爆阀,6气体止回阀,7沉降室,8进料管,9出料管,10蓄热室,11前置焚烧室,12第一烟气管道,13第二烟气管道,14第三烟气管道,15支撑底座。
具体实施方式
20.为了使本技术领域的人员更好地理解本技术中的技术方案,下面将结合附图,对本技术实施例中的技术方案进行清楚完整的描述。
21.本技术的核心是提供一种活性炭炭化炉尾气余热回收利用装置,可以解决现有技术中在利用炭化炉对物料进行碳化的过程中,烟气热量利用率低,且存在燃气资源浪费和活性炭生产能耗高的问题。
22.图1为本实用新型实施例所提供的一种活性炭炭化炉尾气余热回收利用装置结构示意图,图2为本实用新型实施例所提供的一种活性炭炭化炉尾气余热回收利用装置剖面结构示意图,图3为本实用新型实施例所提供的一种第二烟气管道与耐高温高压风机和除
焦池的连接结构示意图,如图1至图3所示,该装置包括:
23.通过第一烟气管道12与炭化炉1的沉降室7下部出口连通的除焦池2,除焦池2出口处通过连接管道连通有后置焚烧室,除焦池2出口处通过第二烟气管道13连通有耐高温高压风机3,耐高温高压风机3的出口处通过第三烟气管道14连通有点火装置4,点火装置4的一侧设置有前置焚烧室11,前置焚烧室11的一侧连通设置有蓄热室10,蓄热室10与炭化炉1连通,炭化炉1靠近蓄热室10的一端下侧设置有出料管9,沉降室7的上侧倾斜设置有进料管8。
24.具体地,使用时,可以将需要炭化的活性炭经进料管8送入炭化炉1中,经过处理的活性炭可以经出料管9排出。炭化炉1的结构以及工作原理均可参见现有技术,本实施例再次不再赘述。作为优选地实施方式,炭化炉1通过支撑底座15进行支撑固定。第一烟气管道12连接至炭化炉1的沉降室7的尾气出口处,用于对来自炭化炉1中尾气中的粉尘等颗粒物进行收集;除焦池2用于对炭化炉1运行过程中产生的可燃烟气进行除尘处理,耐高温高压风机3和点火装置4用于将炭化炉1中的尾气引入前置焚烧室11中;前置焚烧室11用于对来自炭化炉1尾气中的可燃物质进行燃烧。前置焚烧室11是由耐火材料砌筑而成并设有防爆装置,前置焚烧室11的作用是以满足烟气在此区间完全燃烧为基本条件,通过计算,炭化炉1产生烟气量的三分之一用于二次返回焚烧,剩余三分之二进入后置焚烧室进行换热,后置焚烧室在图中未画出。燃烧后的热源引入蓄热室10。蓄热室10的作用是将稳定的高温热源送入炭化炉1内、满足炭化料的热分解反应。通过调整耐高温高压风机3速率,形成良好的炭化温度梯度。
25.在上述实施例的基础上,作为优选地实施方式,点火装置4包括点火总成、与第三烟气管道14连通的气体混合室和螺旋风机,气体混合室与前置焚烧室11连通设置,螺旋风机设置于气体混合室和前置焚烧室11之间,点火总成设置于气体混合室外。经第三烟气管道14后的可燃烟气进入气体混合室后被再次加温、加压形成高温烟气与空气混合后,通过点火总成点火后通过螺旋风机将混合后的烟气旋转式吹到前置焚烧室11燃烧,形成旋转火焰。
26.在上述实施例的基础上,作为优选地实施方式,蓄热室10的内侧壁还设置有孔状格子砖。经过焚烧后的烟气形成高温热能进入蓄热室10。当烟气在前置焚烧室11燃烧不充分时可进入蓄热室10进一步燃烧。孔状格子砖的作用是吸收热量和释放热量,当前置焚烧室11内的尾气量减少时,孔状格子砖释放热量以使前置焚烧室11内的温度保持大体稳定。当然,还可以采用高铝砖、黏土砖耐火砖筑成蓄热室10。
27.为了防止由于耐高温高压风机3停止运行(比如因突发事故停电),导致点火装置4回火,造成气体管路爆炸。在上述实施例的基础上,作为优选地实施方式,在第二烟气管道13上还设置有防爆阀5,在第三烟气管道14上还设置有气体止回阀6。防爆阀5用于防止气体在管道内爆燃和关闭气体管路;气体止回阀6用于防止可燃尾气倒流。
28.在上述实施例的基础上,作为优选地实施方式,在前置焚烧室11和点火装置4的连接处还连通设置有供氧风机。当炭化尾气量增加时,通过控制供氧风机可以增加点火装置4中的氧气供应,当炭化尾气量减少时,通过控制供氧风机可以减少加点火装置4中的氧气供应,使尾气中的可燃物经前置焚烧室11充分燃烧,热量返回炭化炉1得到充分利用。为了将未回收燃烧的三分之二的尾气进行处理后排放,
29.在实际使用时,第一:在前置焚烧室点火口处用天然气点火干烘到1000-1200℃之后,经沉降室上侧的下料管向炭化炉内投入炭化料;第二:炭化料遇热产生的可燃烟气经第一烟气管道进入除焦池进行降尘处理;第三:降尘处理后的三分之一可燃烟气通过耐高温高压风机经第二烟气管道和第三烟气管道引入前置焚烧室内,并通过点火装置向前置焚烧室内加入空气和可燃烟气混合燃烧;第四:燃烧产生的热能进入蓄热室蓄热燃烧后进入炭化炉内参与炭化;第五:降尘处理后的三分之二可燃烟气通过连接管道进入后置焚烧室进行换热处理后排放。
30.在上述实施例的基础上,作为优选地实施方式,后置焚烧室的出口处连通设置有余热锅炉,余热锅炉的排烟管道上连通设置有引风机,引风机的出口处连通设置有湿法脱硫塔,湿法脱硫塔的出口处连通设置有湿电除尘器。经后置焚烧室换热产生的烟气进入余热锅炉使用后,通过引风机将余热锅炉排烟管道产生的烟气引入湿法脱硫塔进行脱硫处理;脱硫处理后的烟气进入湿电除尘器除尘后排入大气。
31.以单炉年产量5000吨炭化炉1例,其尾气温度为550~650℃,尾气中可燃气体含量约为35%~45%,尾气在前置焚烧室11中燃烧升温至800-1200℃,升温后的尾气进入炭化炉1与炭化过程。按照设计,生产线年运行时间约为8000h,按物价局现行燃料煤价格430元/t计算,每小时可减少燃料消耗40元,年降耗可达32万元,创造了经济效益。
32.本技术所提供的一种活性炭炭化炉尾气余热回收利用装置,在实际使用时,炭化炉运行过程中产生的尾气(可燃烟气)可通过第一烟气管道进入到除焦池,通过除焦池对烟气中的粉尘进行降尘处理,降尘处理后的一部分可燃烟气可通过耐高温高压风机经第二烟气管道和第三烟气管道引至点火装置中,通过点火装置将可燃烟气和空气混合点火后输送至前置焚烧室进行焚烧,经过焚烧后的烟气形成高温热能进入蓄热室以便对燃烧不充分的烟气进一步焚烧,蓄热室中的高温热能可以返回炭化炉参与炭化,可实现对一部分烟气的回收利用,提高烟气热量利用率,减少燃气燃料的使用,实现环保生产和活性炭生产低能耗。降尘处理后的另一部分烟气可通过连接管道进入后置焚烧室进行换热处理后排放。
33.本领域技术人员在考虑说明书及实践这里公开的申请后,将容易想到本技术的其他实施方案。本技术旨在涵盖本技术的任何变型、用途或者适应性变化,这些变型、用途或者适应性变化遵循本技术的一般性原理并包含本技术公开的本技术领域中的公知常识或惯用技术手段。说明书和实施例仅被视为实例性的,本技术的真正范围由权利要求指出。
34.应当理解的是,本技术并不局限于上面已经描述并在附图中示出的精确结构,并且可以在不脱离其范围进行各种修改和改变。以上所述的本技术实施方式并不构成对本技术保护范围的限定。