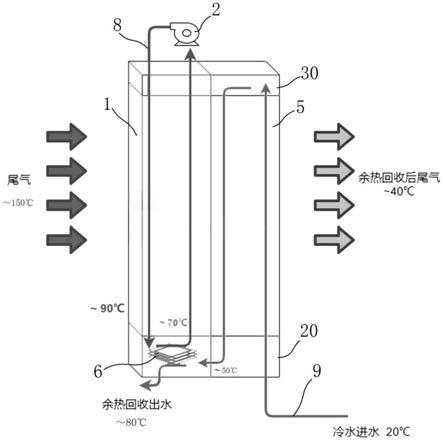
1.本实用新型涉及一种余热回收系统及锅炉系统。
背景技术:
2.随着我国节能减排政策的不断深化,为企业或居民提供蒸汽的原有燃煤锅炉逐渐被天然气为燃料的燃气锅炉取代,以某工业园为例,3台燃气锅炉每小时能够产生蒸汽150吨,其消耗能力巨大,而燃烧后的尾气温度在110
‑
150℃附近,天然气的主要成分为甲烷ch4,根据其燃烧化学式:ch4+2o2=co2+2h2o,1m3天然气充分燃烧后,在不考虑冷凝时的热值约为35.88mj。在考虑冷凝放热时,由于水蒸气冷凝时会大量放热,该热值可以高达39.82mj,可见,燃烧的尾气中包含大量的热能。
3.根据单台锅炉50t/h蒸发量和4586.48nm3/h的燃气消耗量,其生成的水蒸气约为:1.6137kg/s,通过查询焓值表可知,按照降温至50℃的饱和湿度尾气计算,由于冷凝可释放的热功率约为1827kw,尾气中释放的热功率约为,1015kw,合计约2850kw。该功率约可以将50t/h(13.88kg/s)的水升温2850/(13.88
×
4.2)=48.9k,即如果给水温度为20℃,通过余热回收系统,可直接获得约70℃的热水。按照经济性分析,该2850kw的余热回收能源,即回收2.85mj/s相当于2.85/35.88=0.079m3的天然气所释放的热值。每小时可节省0.079
×
3600=284.4m3天然气。按照2.5元/m3的天然气价计算,每小时相当于节省2.5
×
0.079
×
3600=714.9元的燃料费。按照每天20小时运转,即可节省714.9
×
20=14298元/天。另一方面,如果考虑碳排放,每天可减少碳排放8.2吨。
4.由此可见,提高尾气的热能的回收利用率意义巨大。
5.然而现有技术中的尾气余热回收效率低下且余热回收系统投入巨大,为了提高余热回收效率,则需要降低介质温度,这就会导致低于露点温度而导致露点腐蚀问题,因此,现有技术余热回收的效率不高;若要解决腐蚀问题则会投入巨大,导致经济性差,供汽单位考虑到成本问题,对于余热回收系统不看好,严重限制了余热回收系统的推广。
技术实现要素:
6.本实用新型的目的在于提供一种余热回收系统,用以解决现有燃气锅炉尾气热能回收利用率低、余热回收系统成本高的技术问题;本实用新型的目的还在于提供一种可解决燃气锅炉尾气热能回收利用率低、余热回收成本高的技术问题的锅炉系统。
7.本实用新型的余热回收系统的技术方案如下:
8.一种余热回收系统,包括:
9.第一换热器,设置在烟道内,第一换热器为空水换热器,内部具有第一内部管路;第一换热器可实现对尾气(烟气)中热量的第一次回收,回收热量的同时也可以提高第一换热介质的温度,使得第一换热介质的温度高于尾气中水蒸气的冷凝温度,避免尾气中的水蒸气在第一换热器外表面冷凝,从而起到了重要的预防性的防腐,从本质上进行防腐的作用;
10.第二换热器,设置在烟道内,位于第一换热器后方,第二换热器为空水换热器,具有第二内部管路,第二内部管路具有冷却水进口和冷却水出口;第二换热器可实现对尾气中热量的第二次回收,由于第二换热器中通入的为第二换热介质(冷却水),低于尾气中水蒸气的冷凝温度,尾气中的水蒸气可以在第二换热器外表面大量冷凝,冷凝为剧烈的相变过程,会产生大量的热量,因此第二换热器也能够快速高效的收集尾气中的热量;
11.第三换热器,为水水换热的板式换热器,内部具有相互交叉贴合的热端管路和冷端管路,冷端管路的进口与所述冷却水出口连通,冷端管路的出口用于与燃气锅炉的进水管路连通;第三换热器可实现对第一换热介质中的热量的回收,使得第一换热介质中的热量可以传递给作为输出介质的第二换热介质,间接的对热量进行了第三次回收,使得尾气中的热量尽可能多的能够输出到第二换热介质中,以便后续的使用;另一方面,第三换热器在实现第一换热介质与第二换热介质换热的同时,也是对第一换热介质温度的一种控制方式,使得第一换热介质维持在略高于露点温度的范围内,在能够防腐的前提下尽可能的提高了第一换热器的换热效率;而且,第三换热器选用板式换热器,板式换热器两换热介质之间的接触面积更大,接触时间更长,因此,板式换热器可更好、更高效的实现第一换热介质与第二换热介质的换热效率;
12.内循环管路,所述第一内部管路和热端管路通过水管连通构成内循环管路,内循环管路还包括驱动模块,内循环管路内充填有在驱动模块驱动下循环流动的第一换热介质,内循环管路上还设置有用于监测第一内部管路中的第一换热介质温度的温度检测模块;内循环管路的设置可以方便的控制第一换热介质的温度,并实现第一换热器、第三换热器的有效运行,该结构设计十分巧妙,实现回热高效的同时还不会增加太多成本;
13.控制器,与温度检测模块和驱动模块控制连接,根据温度检测模块反馈控制驱动模块,以调整第一换热介质流量的方式控制第一换热介质的温度处于设定温度范围内;控制器、驱动模块以及温度检测模块的设置使得温度控制自动进行,确保第一换热介质时刻处于高效换热状态,提高热回收效率;
14.第二换热介质,自所述冷却水进口进入第二内部管路与烟气进行第一次换热,从所述冷却水出口流向第三换热器的冷端管路以便与热端管路中流动的第一换热介质进行第二次换热。第二换热介质作为工作介质或者叫输出介质,其作用是吸收尾气中的热量并将热量输送出去进行二次利用;通过将第二换热介质导入至蒸汽锅炉的进水管路,使得燃气锅炉在加热生产蒸汽时,起点温度提高,生产蒸汽所消耗的热量显著降低,从而提高了能源的利用率。
15.在上述方案的基础上,进一步改进如下,所述第一换热器的第一内部管路的横截面为椭圆形,椭圆形的长度方向沿烟气的流向设置。
16.在上述方案的基础上,进一步改进如下,所述第一换热器为翅片管换热器。
17.在上述方案的基础上,进一步改进如下,所述驱动模块为设置在内循环管路上的循环水泵。循环水泵的设置可方便控制器以控制其频率的方式控制循环水泵的转速。
18.本实用新型的锅炉系统的技术方案如下:
19.锅炉系统,包括锅炉本体、与锅炉本体相连的烟道和进水管,还包括:
20.第一换热器,设置在烟道内,第一换热器为空水换热器,内部具有第一内部管路;第一换热器可实现对尾气(烟气)中热量的第一次回收,回收热量的同时也可以提高第一换
热介质的温度,使得第一换热介质的温度高于尾气中水蒸气的冷凝温度,避免尾气中的水蒸气在第一换热器外表面冷凝,从而起到了重要的本质防腐作用;
21.第二换热器,设置在烟道内,位于第一换热器后方,第二换热器为空水换热器,具有第二内部管路,第二内部管路具有冷却水进口和冷却水出口;第二换热器可实现对尾气中热量的第二次回收,由于第二换热器中通入的为第二换热介质(冷却水),低于尾气中水蒸气的冷凝温度,尾气中的水蒸气可以在第二换热器外表面大量冷凝,冷凝为剧烈的相变过程,会产生大量的热量,因此第二换热器也能够快速高效的收集尾气中的热量;
22.第三换热器,为水水换热的板式换热器,内部具有相互交叉贴合的热端管路和冷端管路,冷端管路的进口与所述冷却水出口连通,冷端管路的出口用于与燃气锅炉的进水管路连通;第三换热器可实现对第一换热介质中的热量的回收,使得第一换热介质中的热量可以传递给作为输出介质的第二换热介质,间接的对热量进行了第三次回收,使得尾气中的热量尽可能多的能够输出到第二换热介质中,以便后续的使用;另一方面,第三换热器在实现第一换热介质与第二换热介质换热的同时,也是对第一换热介质温度的一种控制方式,使得第一换热介质维持在略高于露点温度的范围内,在能够防腐的前提下尽可能的提高了第一换热器的换热效率;而且,第三换热器选用板式换热器,板式换热器两换热介质之间的接触面积更大,接触时间更长,因此,板式换热器可更好、更高效的实现第一换热介质与第二换热介质的换热效率;
23.内循环管路,所述第一内部管路和热端管路通过水管连通构成内循环管路,内循环管路还包括驱动模块,内循环管路内充填有在驱动模块驱动下循环流动的第一换热介质,内循环管路上还设置有用于监测第一内部管路中的第一换热介质温度的温度检测模块;内循环管路的设置可以方便的控制第一换热介质的温度,并实现第一换热器、第三换热器的有效运行,该结构设计十分巧妙,实现回热高效的同时还不会增加太多成本;
24.控制器,与温度检测模块和驱动模块控制连接,根据温度检测模块反馈控制驱动模块,以调整第一换热介质流量的方式控制第一换热介质的温度处于设定温度范围内;控制器、驱动模块以及温度检测模块的设置使得温度控制自动进行,确保第一换热介质时刻处于高效换热状态,提高热回收效率;
25.第二换热介质,自所述冷却水进口进入第二内部管路与烟气进行第一次换热,从所述冷却水出口流向第三换热器的冷端管路以便与热端管路中流动的第一换热介质进行第二次换热。第二换热介质作为工作介质或者叫输出介质,其作用是吸收尾气中的热量并将热量输送出去进行二次利用;通过将第二换热介质导入至蒸汽锅炉的进水管路,使得燃气锅炉在加热生产蒸汽时,起点温度提高,生产蒸汽所消耗的热量显著降低,从而提高了能源的利用率。
26.在上述方案的基础上,进一步改进如下,所述第一换热器的第一内部管路的横截面为椭圆形,椭圆形的长度方向沿烟气的流向设置。
27.在上述方案的基础上,进一步改进如下,所述第一换热器为翅片管换热器。
28.本实用新型的有益效果:本实用新型具有热回收效率高、并可以尽可能的提高能源利用率,首先,第一换热器中通过对第一换热介质的温度的控制,使得其温度在满足高于露点而使不易腐蚀的前提下尽可能的低,这样在与尾气进行第一次换热时的换热效率比较高;其次,第一换热器采用横截面为椭圆形的翅片管,椭圆形的翅片管在满足风阻比较小的
前提下,因为沿风向的方向翅片管的宽度较宽,因此换热时间较长、换热面积较大,所以换热效率也进一步提高;另外,第一换热器由于不会发生冷凝,因此选用了带有翅片的换热器,翅片的换热效率较高,也提高了热回收效率;再者,第一换热介质还通过第三换热器实现了与第二换热介质的热交换,从而进一步提高作为输出产物的第二换热介质的温度,从而进一步提高了热回收效率;更重要的,被加热后的第一换热介质作为燃气锅炉的原料水,使得燃气锅炉再对第一换热介质进行加热时所需要的燃料比原有冷却水作为原料时所需要的燃料的量显著降低,即不仅避免后续长距离输送时的能量耗散,而且使得燃气锅炉在生产蒸汽时起点温度提高,从而提高了能量利用率;由此可见,本实用新型的余热回收系统和余热回收方法具有很高的热回收效率,可以尽可能提高燃气锅炉的能量利用率。
附图说明
29.图1为本实用新型的余热回收系统实施例1的工作原理示意图;
30.图2为余热回收系统的主视结构示意图;
31.图3为第一换热器和第二换热器的主视图;
32.图4为图3的左视图;
33.图5为本实用新型的余热回收系统实施例2的工作原理示意图;
34.图中:1
‑
第一换热器,11
‑
循环水进口,12
‑
循环水出口,2
‑
循环水泵,3
‑
定压罐,4
‑
喷淋管,41
‑
喷嘴,42
‑
喷淋水进口,43
‑
排水口,44
‑
集水槽,5
‑
第二换热器,51
‑
冷却水进口,52
‑
冷却水出口,6
‑
第三换热器,7
‑
第四换热器;8
‑
第一换热介质,9
‑
第二换热介质,20
‑
换热器前水室,30
‑
换热器后水室,40
‑
壳体。
具体实施方式
35.为了使本实用新型的目的、技术方案及优点更加清楚明白,以下结合附图及实施例,对本实用新型进行进一步详细说明。应当理解,此处所描述的具体实施例仅用以解释本实用新型,并不用于限定本实用新型,即所描述的实施例仅仅是本实用新型一部分实施例,而不是全部的实施例。通常在此处附图中描述和示出的本实用新型实施例的组件可以以各种不同的配置来布置和设计。
36.因此,以下对在附图中提供的本实用新型的实施例的详细描述并非旨在限制要求保护的本实用新型的范围,而是仅仅表示本实用新型的选定实施例。基于本实用新型的实施例,本领域技术人员在没有做出创造性劳动的前提下所获得的所有其他实施例,都属于本实用新型保护的范围。
37.需要说明的是,术语“第一”和“第二”等之类的关系术语仅仅用来将一个实体或者操作与另一个实体或操作区分开来,而不一定要求或者暗示这些实体或操作之间存在任何这种实际的关系或者顺序。而且,术语“包括”、“包含”或者其任何其他变体意在涵盖非排他性的包含,从而使得包括一系列要素的过程、方法、物品或者设备不仅包括那些要素,而且还包括没有明确列出的其他要素,或者是还包括为这种过程、方法、物品或者设备所固有的要素。在没有更多限制的情况下,由语句“包括一个
……”
限定的要素,并不排除在包括所述要素的过程、方法、物品或者设备中还存在另外的相同要素。
38.以下结合实施例对本实用新型的特征和性能作进一步的详细描述。
39.本实用新型的余热回收系统的实施例1:
40.余热回收系统用于燃气锅炉或者燃煤锅炉的尾气的余热回收,其具有壳体40,壳体40为管道状,串接在尾气管道中,即两端分别与尾气管密封对接,以使得锅炉的尾气可以经过余热回收系统,在进行热交换后尾气排走,尾气内的热量传递给余热回收系统的传热介质,利用传热介质的热量进行供暖等,实现热量的二次利用。更具体地:
41.如图1
‑
4所示,余热回收系统包括壳体40以及安装在壳体40内的第一换热器1、第二换热器5和第三换热器6。其中:
42.第一换热器1为普通碳钢材质的管翅式空水换热器,其管翅为椭圆翅片管,其迎风面较小、换热面积较大,在保证换热效率的前提下送可以充分降低管外风阻,整体结构更符合场协同原理,其传热系数优于一般圆形翅片管。同时,为了确保该区域换热器的防腐蚀能力,翅片管外采用镀锌处理。通过高温热镀锌,使翅片和基管同时被锌层包裹,锌层的保护可以使其在保持金属间高效传热的同时,具有防锈和防腐蚀性能。下表为椭圆翅片管换热器(第一换热器1)性能参数表:
[0043][0044]
第一换热器1的本体上具有循环水进口11和循环水出口12,与第一换热器1匹配的有一个内循环管路,内循环管路包括循环水泵2、定压罐3、变频器以及管路等,其中定压罐3的设置是为了稳定水压。管路与第一换热器1的循环水进口11和循环水出口12连接为一个闭环的内循环管路,循环水泵2、定压罐3等设置在内循环管路上,在变频器的控制下,循环水泵2按照设定的转速运行,使得内循环管路内的换热介质(一般为水,称为第一换热介质8)按照设定的流量(流速)循环流动,在流经第一换热器1区域时与本体外经过的高温烟气(一般为110
‑
150℃附近)换热,吸收尾气中的热量。与此同时,内循环管路还与第三换热器6连接,在与第三换热器6内的另一换热介质(经过第二换热器5加热后的冷却水,称为第二换热介质9)进行热量交换,将热量传递给第二换热介质9,实现第一换热介质8的温度控制;即通过变频器和循环水泵2对第一换热介质8流速(流量)的控制以及其与第二换热介质9的热
量交换,实现了对第一换热介质8温度的控制,使得第一换热介质8的温度略高于露点温度(尾气中的水蒸气在第一换热器1外管壁上的冷凝温度),确保尾气在水蒸气中不会冷凝的同时,第一换热介质8的温度尽可能的低,从而提高第一换热器1的换热效率。
[0045]
为了方便控制内循环管路内的水温,在内循环管路上设置有温度检测传感器,设定一个既能确保会导致尾气中的水蒸气冷凝、也能确保具有比较高的换热效率的温度范围,例如设定65
‑
75℃为该温度范围,那么当温度传感器检测到实际温度低于65℃时,就需要控制循环水泵2的转速,使得流动慢一些,以使得第一换热介质8与高温尾气的换热时间加长,从而提高第一换热介质8的温度,反之,若检测到实际温度高于75℃时,就需要控制循环水泵2的转速,使流动快一些,减少第一换热介质8与高温尾气的换热时间,从而实现将第一换热介质8的水温控制在设定范围内的目的。
[0046]
需要说明的是:之所以要防止尾气中的水蒸气在第一换热器1的外表面冷凝,是因为天然气经过充分燃烧后,其尾气中含有较多的氮氧化物和水蒸气。当经过第一换热器1器时,若第一换热器1内的第一换热介质8的温度低于露点温度,则会由于冷凝导致尾气中的水蒸气析出,并与氮氧化物结合生成硝酸溶液。该酸性腐蚀性溶液,由于翅片的结构作用,液滴聚集在换热器翅片管外,导致翅片逐渐发生腐蚀,生成金属氧化物(铁锈)。这些蓬松的氧化物,在第一换热器1外堆积,进而逐步堵塞风道,增大了管道内出风阻力,使得尾气风机的性能工作点发生变化,风量明显降低。而本实用新型的方案通过内循环管路以及第三换热器6的设置使得第一换热介质8的温度控制在略高于露点的温度,使得第一换热器1外表面不会冷凝出酸性腐蚀溶液,从而避免了第一换热器1的腐蚀问题发生,当然,为了确保意外,第一换热器1外表面也进行了热镀锌或者是电镀处理,从而具有一定程度的防腐性能。
[0047]
高防腐材料,例如不锈钢或带特殊镀层的换热管,可以有效耐稀硝酸腐蚀,但由于其价格较贵,如果全部使用高防腐材质制造换热器,可能导致换热器投资成本远远超出预算。考虑到成本,第一换热器1本身可以选用不耐腐蚀的普通碳钢材质,由于通过第一换热介质8温度的控制避免了第一换热器1外表面腐蚀,再不担心防腐问题的前提下,为了提高换热效率,选用横截面为椭圆形的翅片管结构的换热器。换句话说,根据软件模拟,计算出尾气在通过冷凝器时整个流场的温度。并在不同的温度区间,选用不同的材质换热管材质,实现一种换热管材料与温度场耦合的换热器结构。在冷凝器的高温区,由于无水分析出,可以采用普通材质的翅片管结合一般防腐措施来抑制酸性腐蚀,在本实用新型的方案中,我们采用椭圆翅片管这种低风阻防腐换热管来设计制造高温区的冷凝器。而在低温区,由于大量水分会在此处析出,形成大量稀硝酸溶液。因此,在此区间,我们选用耐腐蚀但成本较高的不锈钢光管来设计制造该区间的冷凝器模块(详细描述见后面)。
[0048]
高温烟气在经过第一换热器1后进一步进入第二换热器5。如图3所示,第二换热器5采用不锈钢材质的光管式空水换热器,该换热器的本体上具有冷却水进口51和冷却水出口52,用于供第二换热介质9流过,其目的主要是将第二换热介质9加热至所需温度,第二换热介质9即为该余热回收系统的输出品,可用于供暖或者用于燃气锅炉的供水系统,使得燃气锅炉生产蒸汽时可以少消耗一些燃料。在第二换热器5内,由于其内的第二换热介质9的温度低于露点温度,烟气内的水蒸气将通过冷凝大量放热,全部冷凝时的发热功率最多能占到天然气全热值的11%左右。此次为确保工程可靠实施,留有一定余量,设计将烟气温度回收到50℃。在第二换热器5中,由于此时的烟气中主要是以饱和水蒸气为主,大量热量随
冷凝现象放出,并伴随着大量冷凝水的析出。此时换热管外会产生大量的酸性溶液。
[0049]
第二级换热器处为冷凝换热核心区域,由于冷凝换热的相变剧烈,换热量大,因此无需采用翅片增大换热效率,考虑到成本和防腐的要求,直接采用不锈钢或玻璃的光管即可。下表为光管换热器(第二换热器5)的性能参数表:
[0050][0051][0052]
如图3、4所示,由于第二换热器5表面会有酸液形成,酸液在换热器表面对换热器不利,而且也容易积攒灰尘,因此在第一换热器1与第二换热器5之间设置有喷淋管4,喷淋管4上间隔设置多个喷嘴41,喷嘴41朝向第二换热器5设置,通过外部供水泵提供高压水,通过喷淋水进口42供给给喷淋管4,经过喷嘴41呈锥形范围喷射出高压水雾对第二换热器5的外表面进行在线冲洗,以将第二换热器5表面的灰尘和酸液冲洗下来,而在第二换热器5对应的壳体40部分的下部设置有类似漏斗的集水槽44结构,在集水槽结构的下部设置有排水口43,以用于排出冲洗后的水,由于冲洗后的水中含有酸性溶液,因此可以考虑经过过滤、提纯等操作后形成纯度更高的酸性溶液以便后续使用。在其他实施例中,光管的材质也可以替换为玻璃、陶瓷等耐腐蚀材料。
[0053]
同时由于冷凝水的析出,该区域中也极易沾染灰尘和杂质,所以设计上采用抽屉式芯体,方便进行维护清洗,以提高换热管效率和区域中的清洁度。
[0054]
第三换热器6为用于将第一换热器1与第二换热器5的内部换热介质(第一换热介质8和第二换热介质9)进行换热的辅助换热器,其采用多层板片叠加结构的板式换热器,为水水换热器,其不参与与尾气的换热,该换热器的主要作用是配合内循环管路系统以方便控制第一换热介质8的温度,其次还可以为第二换热介质9进行二次加热,进一步提高第二换热介质9的温度。
[0055]
换个角度去说,第一换热器1和第三换热器6其实可以认为是一个一级换热器,而第二换热器5为二级换热器,一级换热器是自带内循环介质温控制的(就是自带了一个板式
换热器,即第三换热器6),也就是说,在一级换热器里面,存在三股流体,热介质(第一换热介质8)、冷介质(第二换热介质9)、高温烟气,三者之间形成两个传热状态。如图1所示,三个换热器整合为一个一体式结构。为了满足设备现场转运限制、考虑设备搬运和安装的便利性,设备拆分为至少两个模板。
[0056]
另一方面,系统还设置有漏水报警和缺水报警模块,当检测到管路漏水或换热器内缺水时要分别进行报警提示,以确保维保人员可以及时收取消息提醒。
[0057]
在使用时:如图1所示,从燃气锅炉燃烧后排出的高温尾气(110
‑
150℃)在烟道内流动首先经过第一换热器1的翅片管的外表面,与翅片管内流动的第一换热介质8进行热交换,此时烟气的温度降低至60℃左右,而第一换热介质8的温度升高90℃左右,然后尾气(60℃)经过第二换热器5的光管的外表面与第二换热器5内的第二换热介质9(20℃的冷却水)进行热交换,由于发生冷凝(露点60℃左右),放出大量的热量,尾气温度降低至40℃左右,而第二换热介质9的温度升至30
‑
50℃左右,而第一换热介质8(90℃)与第二换热介质9(30
‑
50℃)进入至第三换热器6中进行热量交换,并与此同时控制内循环管路的水循环的速度,使得第一换热介质8降低至70℃,该温度在与上述高温尾气(110
‑
150℃)进行换热时才能确保既不会冷凝,也确保具有最高的换热效率;而第二换热介质9的温度升高至80℃左右,此时的第二换热介质9即可导入至燃气锅炉的供水管路上,从而降低燃气锅炉的燃气消耗量,也可导入城市供暖管路以实现供暖,也可用于其他用途。
[0058]
本实用新型的余热回收系统具有以下特点:
[0059]
1、热回收效率高,可以尽可能提高燃气锅炉的能量利用率,首先,第一换热器1中通过对第一换热介质8的温度的控制,使得其温度在满足高于露点而使不易腐蚀的前提下尽可能的低,这样在与尾气进行第一次换热时的换热效率比较高;其次,第一换热器1采用横截面为椭圆形的翅片管,椭圆形的翅片管在满足风阻比较小的前提下,因为沿风向的方向翅片管的宽度较宽,因此换热时间较长、换热面积较大,所以换热效率也进一步提高;另外,第一换热器1由于不会发生冷凝,因此选用了带有翅片的换热器,翅片的换热效率较高,也提高了热回收效率;再者,第一换热介质8还通过第三换热器6实现了与第二换热介质9的热交换,从而进一步提高作为输出产物的第二换热介质9的温度,从而进一步提高了热回收效率;更重要的,被加热后的第一换热介质8作为燃气锅炉的原料水,使得燃气锅炉再对第一换热介质8进行加热时所需要的燃料比原有冷却水作为原料时所需要的燃料的量显著降低,即不仅避免后续长距离输送时的能量耗散,而且使得燃气锅炉在生产蒸汽时起点温度提高,从而提高了能量利用率;由此可见,本实用新型的余热回收系统具有很高的热回收效率,可以尽可能提高燃气锅炉的能量利用率。
[0060]
2、防腐、防风道堵塞,首先,对于第一换热器1,通过调整内部第一换热介质8的温度,使其温度高于尾气中水蒸气冷凝的露点温度,使得水蒸气在第一换热器1处不会出现冷凝现象,并在第一换热器1的外表面采用热镀锌或者是电镀等一般防腐方案,实现了第一换热器1的防腐目的,从而可以放心的选用普通碳钢材质的翅片管换热器,由于不会冷凝,也就不会形成酸性溶液,所以第一换热器1的表面不会发生生锈现象,也就解决了防止烟道堵塞的情况发生;其次,对于第二换热器5,由于第二换热器5处于低温区,其内的第二换热介质9的温度较低,因此第二换热器5是冷凝换热的核心区域,在第二换热器5的外表面不可避免的会有大量的冷凝水产生,从而会形成大量的稀硝酸溶液,因此,第二换热器5为发生腐
蚀的核心区域,其防腐要做好,本技术通过将第二换热器5整体采用不锈钢等耐腐蚀的材质起到主要的防腐作用;另外,为了防止酸性溶液集聚在第二换热器5的表面上,选用了表面光滑无凹槽的光管换热器,使得酸性溶液不会在换热器的表面长时间聚集;再者,为了防止酸性溶液与灰尘结合后粘接在第二换热器5的表面,设置了喷淋管4,下部还设置有排水口43,从而定期对第二换热器5外表面进行冲洗,从而将灰尘和酸性溶液冲洗下来并从排水口43排出,避免第二换热器5外表面和烟道内壁面的腐蚀;以上几项防腐措施的设计,在满足成本低、结构简单、换热效率高的前提下,具有优良的防腐、防烟道堵塞的优点;余热回收装置的腐蚀,主要是电化学腐蚀,各类锅炉及燃气轮机的所排出气体中含量的不同,环境压力不同,其露点(产生冷凝的温度)不同,当换热装置某一点温度低于冷凝温度时会产生结露,从而对换热器产生腐蚀,通过对热回收装置冷侧介质温度的控制使得换热器的所有温度均大于露点温度,可以用普通材料来最大限度地降低普通换热器的热回收量。
[0061]
在以上两个特点的基础上,还具有产品寿命长,能长久使用、经济性好、可减少其投资回收周期。
[0062]
本实用新型的余热回收系统的实施例2:如图5所示,与实施例1的不同之处在于,在第二换热器5之后还设置有第四换热器7用来解决脱白问题,具体为:第四换热器7为空水换热器,由于此处基本不存在冷凝,因此也可以采用普通碳钢材质+镀锌处理的换热器以降低成本,第四换热器7内的换热介质为第二换热介质9,即第二换热介质9在第三换热器6中换热后一部分导入至第四换热器7内,以实现对尾气的反向加热,简称回热,回热后可实现对尾气的脱白效果。
[0063]
此处脱白的工作原理如下:经过第二换热器5后,尾气中的大部分水分已经冷凝析出,尾气的温度约40℃,若将尾气直接通过烟囱排出,由于尾气此时的温度比较低(低于露点),在与烟囱的内壁接触时,由于烟囱的内壁温度较低,已经饱和的水蒸气会进一步冷凝,从而会在烟囱的内壁上生成酸性溶液,容易导致烟囱内壁的腐蚀,而且在尾气处于烟囱排烟口附近时,与冷空气接触也会冷凝形成白雾;而本方案中通过在第二换热器5后面再设置一个第四换热器7,可将被加热后的第二换热介质9导过来一部分为尾气加热,使得尾气温度高于露点温度,即使得尾气温度在烟囱以及烟囱的排烟口附近时均高于露点温度,因此不会发生冷凝,而当尾气进一步扩散在至大气中后,虽然尾气的温度低于露点温度,但是由于扩散后的水蒸气比较分散,无法形成水雾,因此也不会出现白雾,因此实现了脱白的目的。该方案无需利用额外的能源为尾气加热,而是利用尾气本身的温度经过换热后反过来为尾气加热,从而实现了脱白。
[0064]
需要说明的是:本方案中尾气从150℃降低至40℃后又经过回热加热至高于60℃,回热过程并非是重复过程,该方案与尾气直接从150℃降低至60℃的方案是不同的,因为前者是在降低至40℃的过程中在第二换热器5处进行的大量的冷凝过程,该过程将尾气中的大部分水汽冷凝析出,因此后续回热时只是对空气加热,其加热消耗的能量比较低,可以有效降低尾气湿度。可见在本方案中由60℃降低至40℃和由40℃加热至60℃是不可逆的过程,因为两过程中尾气中的水分含量是不同的,前者能量变化较大,后者因为涉及很少的水的相变过程,能量变化较小。这也是本方案的巧妙之处。
[0065]
通过本方案,可以实现保护后端烟囱内壁面材质不被腐蚀,降低排烟湿度,防止水蒸气析出,而实现脱白。而且该方案中对于热量的回收做到了极致,在满足脱白的前提下尽
可能的增加了热量的利用率。
[0066]
在使用时,如图5所示,与实施例1的不同之处在于,经过第三换热器6后的第二换热介质9(约80℃)不是直接导入蒸汽锅炉供水,而是经过第四换热器7为尾气(温度40℃,湿度100%)进行加热,加热后得到尾气温度50℃左右,湿度70%左右,而第二换热介质9的温度降低至75℃左右,第二换热介质9(75℃左右)随后导入至蒸汽锅炉供水。
[0067]
对上述第一个实施例进行运营经济性对比:
[0068]
(1)热力学基本原理:
[0069]
通过化学方程:ch4+2o2=co2+2h2o,可知,1mol甲烷燃烧后消耗2mol氧气,生成1mol二氧化碳和2mol水蒸气。
[0070]
按照目前现场实时测定烟气含氧量0.3%,以及一般环境空气中氧的摩尔数为20.95%,可知锅炉入口天然气和空气体积比约为1:11.5。
[0071]
(2)原有设计与本技术新改造后的热性能设计对比:
[0072]
原设计出风温度55℃,本技术新改造后的出风温度可低于50℃,具体见下表:
[0073]
指标原设计本技术方案单位出风温度5550℃进风温度155155℃冷凝水析出量0.310.74kg/s显热回收16221703kw潜热回收792.61893kw总热回收2414.63596.2kw锅炉能效99.29101.54%
[0074]
从上表可以看出,本技术方案的余热回收系统,比原设计理想状态下的余热回收系统能多回收3596.2
‑
2414.6=1181.6kw,将该新增部分的能量带入原锅炉的能效数据,则改造后锅炉能效可达101.51%。
[0075]
(3)本技术对应改造前后性能对比及投资周期分析
[0076]
目前原有设备运行出风温度70℃,本技术方案改造后出风温度可低于50℃,具体如下表:
[0077]
[0078][0079]
从上表可看出,按照目前的燃料利用情况计算,在改造后锅炉50%的利用率的状态下,通过本次改造后所节省的燃料成本,可实现在半年内回收改造投资成本。
[0080]
(4)改造后整体余热回收性能及经济效益分析
[0081]
改造后不同进风温度时余热回收对比如下表:
[0082][0083]
本实用新型的锅炉系统的具体实施例:以燃气锅炉系统为例,系统包括锅炉本体、软水器、水箱、除氧器、分汽缸、给水泵、除氧泵、连续排污扩容器、燃烧器、烟道、管线以及余热回收系统,余热回收系统的具体结构与上述实施例中的结构相同,不再赘述。
[0084]
以上所述,仅为本实用新型的较佳实施例,并不用以限制本实用新型,本实用新型
的专利保护范围以权利要求书为准,凡是运用本实用新型的说明书及附图内容所作的等同结构变化,同理均应包含在本实用新型的保护范围内。