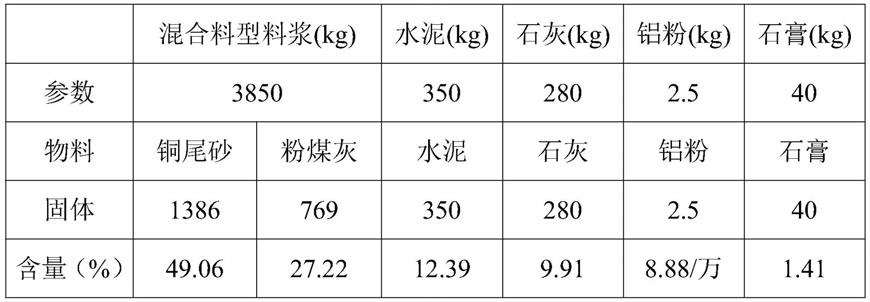
1.本发明涉及加气混凝土砌块的加工技术领域,尤其涉及高强度铜尾砂加气混凝土砌块的加工方法。
背景技术:
2.加气混凝土砌块是一种轻质多孔、保温隔热、防火性能良好、可钉、可锯、可刨和具有一定抗震能力的新型建筑材料。加气混凝土砌块的适应性强,可根据当地不同原材料,不同条件来量身定造。原材料可选择河砂、粉煤灰、矿砂等多种,因地制宜。并且可以废物利用,有利环保,真正的变废为宝。
3.加气混凝土砌块的原材料中,河砂、江砂的成本较高,造成以砂石为主要原料的加气混凝土砌块的造价较高;铜尾矿又称铜尾砂,是由矿石经粉碎、精选后所剩下的细粉砂粒组成,这些铜尾砂除少量作为旧矿井的填充料之外,其余绝大多数还以填充洼地或筑坝堆放的方式储存,堆置的铜尾砂占用了大量土地,覆盖了原有的植被,生态系统遭到破坏。铜尾砂因随风飞扬、雨水流失,对周边地区的居民生活环境造成污染。同时,铜尾砂的价格便宜,可以将铜尾砂充分利用至混凝土砌块中。
4.针对上述问题,设计一种高强度铜尾砂加气混凝土砌块的加工方法。
技术实现要素:
5.本发明针对现有技术的不足,提供了高强度铜尾砂加气混凝土砌块的加工方法。
6.本发明通过以下技术手段实现解决上述技术问题的:
7.高强度铜尾砂加气混凝土砌块的加工方法,包括以下步骤:
8.s1:料浆制作:粉煤灰:铜尾砂=35:65,将铜尾砂投入湿法球磨机中进行球磨形成铜尾砂砂浆,铜尾砂砂浆固体份为48%,扩散度35
±
1cm;将铜尾砂砂浆通过渣浆泵抽至第一搅拌罐中和粉煤灰混合形成料浆,料浆固体份为56%,扩散度在27
±
1cm;
9.s2:配料搅拌:按料浆:水泥:石灰:石膏=76.28:12.39:9.91:1.41 的比例第二搅拌罐中搅拌混合形成初级原浆;
10.s3、浇筑:将搅拌均匀后的初级原浆通蒸汽加热至47℃,加入铝粉悬浮液,形成成品原浆,成品原浆扩散度在19
±
1cm,0.5-1分钟后浇筑在模具中;
11.s4、养护成型。
12.作为上述技术方案的改进,所述步骤s1中,铜尾砂砂浆中铜尾砂的细度过0.08mm,筛余≤25%。
13.作为上述技术方案的改进,所述步骤s3中,铝粉悬浮液的原料为铝粉,铝粉采用外掺法计算,料浆:水泥:石灰:石膏:铝粉=76.28:12.39:9.91: 1.41:0.0888。
14.作为上述技术方案的改进,所述步骤s4中,包括,s4.1预养切割:浇注后的模具进入温度设置为40℃、湿度设置为65%的预养室中预养;
15.预养至105min后,将预养完成后的胚体脱模后进行胚体切割;
16.s4.2蒸汽养护:切割后的胚体由吊具吊至蒸养小车,由蒸养小车将胚体送至蒸养釜中进行高温蒸养;
17.3小时的进气时间后,进入6小时的恒压状态,压力为1.0mpa,温度 185℃;恒压状态结束后导气排气;
18.s4.3烘干:对养护完成的胚体进行烘干。
19.作为上述技术方案的改进,所述步骤s4.1预养切割中,切割后形成的胚体规格为600mmx240mmx100mm、600mmx240mmx200mm两种中的任意一种。
20.本发明的有益效果:
21.通过本发明中的高强度铜尾砂加气混凝土砌块的加工方法加工出的高强度铜尾砂加气混凝土砌块,符合生产使用要求且拥有较高的强度,实现了铜尾砂再利用的问题,避免铜尾砂堆置造成生态环境的破坏,同时,铜尾砂代替江砂的使用,降低了混凝土砌块的使用成本;
22.本发明中的高强度铜尾砂加气混凝土砌块的加工方法,通过铜尾砂砂浆与粉煤灰进行混合搅拌形成料浆,料浆与水泥、石灰、石膏形成初级原浆,初级原浆加入铝粉形成成品原浆,后进行浇筑、养护成型,工序简单,制备效率高;铜尾砂和粉煤灰为硅质材料,水泥和石灰为钙质材料配合提供有效氧化钙,铝粉为加气剂,使混凝土产生气孔,石膏为调节剂,对生石灰消解和料浆稠化速度的延缓,且铜尾砂砂浆的扩散度控制在35
±
1cm,料浆的扩散度在控制在27
±
1cm,成品原浆扩散度控制在19
±
1cm,保证了铜尾砂加气混凝土砌块的成品性能。
具体实施方式
23.为使本发明实施例的目的、技术方案和优点更加清楚,下面将结合本发明实施例,对本发明实施例中的技术方案进行清楚、完整地描述,显然,所描述的实施例是本发明一部分实施例,而不是全部的实施例。基于本发明中的实施例,本领域普通技术人员在没有作出创造性劳动前提下所获得的所有其他实施例,都属于本发明保护的范围。
24.需要说明的是,当元件被称为“固定于”另一个元件,它可以直接在另一个元件上或者也可以存在居中的元件。当一个元件被认为是“连接”另一个元件,它可以是直接连接到另一个元件或者可能同时存在居中元件。
25.高强度铜尾砂加气混凝土砌块的加工方法,包括以下步骤:
26.s1:料浆制作:粉煤灰:铜尾砂=35:65,将铜尾砂投入湿法球磨机中进行球磨形成铜尾砂砂浆,铜尾砂砂浆固体份为48%,扩散度35
±
1cm;将铜尾砂砂浆通过渣浆泵抽至第一搅拌罐中和粉煤灰混合形成料浆,料浆固体份为56%,扩散度在27
±
1cm;
27.s2:配料搅拌:按料浆:水泥:石灰:石膏=76.28:12.39:9.91:1.41 的比例第二搅拌罐中搅拌混合形成初级原浆;
28.s3、浇筑:将搅拌均匀后的初级原浆通蒸汽加热至47℃,加入铝粉悬浮液,形成成品原浆,成品原浆扩散度在19
±
1cm,0.5-1分钟后浇筑在模具中;
29.s4、养护成型。
30.步骤s1中,铜尾砂砂浆中铜尾砂的细度过0.08mm,筛余≤25%。
31.步骤s3中,铝粉悬浮液的原料为铝粉,铝粉采用外掺法计算,料浆:水泥:石灰:石
膏:铝粉=76.28:12.39:9.91:1.41:0.0888。
32.步骤s4中,包括,s4.1预养切割:浇注后的模具进入温度设置为40℃、湿度设置为65%的预养室中预养;
33.预养至105min后,将预养完成后的胚体脱模后进行胚体切割;
34.s4.2蒸汽养护:切割后的胚体由吊具吊至蒸养小车,由蒸养小车将胚体送至蒸养釜中进行高温蒸养;
35.3小时的进气时间后,进入6小时的恒压状态,压力为1.0mpa,温度 185℃;恒压状态结束后导气排气;
36.s4.3烘干:对养护完成的胚体进行烘干。
37.步骤s4.1预养切割中,切割后形成的胚体规格为 600mmx240mmx100mm、600mmx240mmx200mm两种中的任意一种。
38.实施例
39.高强度铜尾砂加气混凝土砌块的加工方法,包括以下步骤:其中,1份设置为1kg,浇筑原料用量参见表1,
40.s1:料浆制作:将铜尾砂投入湿法球磨机中进行球磨形成铜尾砂砂浆,铜尾砂砂浆固体份为48%,扩散度35
±
1cm,铜尾砂砂浆中铜尾砂的细度过 0.08mm,筛余≤25%,
41.4500份铜尾砂砂浆通过渣浆泵抽至第一搅拌罐中和1200份粉煤灰混合形成料浆,料浆固体份为56%,扩散度在27
±
1cm;
42.s2:配料搅拌:3850份料浆、350份水泥、280份石灰和40份石膏加入第二搅拌罐中搅拌混合形成初级原浆;
43.s3、浇筑:将搅拌均匀后的初级原浆通蒸汽加热至47℃,加入2.5份铝粉制成的铝粉悬浮液,形成成品原浆,成品原浆扩散度在19
±
1cm,0.5-1 分钟后浇筑在模具中;
44.s4、养护成型:s4.1预养切割:浇注后的模具进入温度设置为40℃、湿度设置为65%的预养室中预养;
45.预养至105min后,将预养完成后的胚体脱模后进行胚体切割;
46.s4.2蒸汽养护:切割后的胚体由吊具吊至蒸养小车,由蒸养小车将胚体送至蒸养釜中进行高温蒸养;
47.3小时的进气时间后,进入6小时的恒压状态,压力为1.0mpa,温度 185℃;恒压状态结束后导气排气;
48.s4.3烘干:对养护完成的胚体进行烘干。
49.表1:浇筑原料用量表
50.51.表2:检测参数(产品符合gb11968-2020 a3.5b06标准)
[0052] 出釜容重出釜强度烘干容重烘干强度1780kg/m33.5mpa605kg/m34.61mpa2785kg/m33.3mpa610kg/m34.39mpa
[0053]
由表2中可得知,经过本高强度铜尾砂加气混凝土砌块的加工方法加工的混凝土砌块,满足混凝土砌块的生产使用要求且拥有较高的强度。
[0054]
成本分析:
[0055]
2021年铜陵江砂价格110元/吨,铜尾矿价格约70元/吨,粉煤灰价格约110元/吨,利用控制变量方法比较改变砂材料和粉煤灰的比例,正常江砂和粉煤灰比例为8:2,通过利用铜尾砂和粉煤灰的比例调成3.5:6.5,砌块出釜产品性能基本没有变化,成本降低12.86元/立方。
[0056]
其中料浆中,4500份固体份为48%的铜尾砂砂浆,1200份粉煤灰, 4500*0.48=2160,1200/2160≈35/65,同比缩小10倍,得铜尾砂:粉煤灰≈ 6.5:3.5。
[0057]
需要说明的是,在本文中,如若存在第一和第二等之类的关系术语仅仅用来将一个实体或者操作与另一个实体或操作区分开来,而不一定要求或者暗示这些实体或操作之间存在任何这种实际的关系或者顺序。而且,术语“包括”、“包含”或者其任何其他变体意在涵盖非排他性的包含,从而使得包括一系列要素的过程、方法、物品或者设备不仅包括那些要素,而且还包括没有明确列出的其他要素,或者是还包括为这种过程、方法、物品或者设备所固有的要素。在没有更多限制的情况下,由语句“包括一个
……”
限定的要素,并不排除在包括所述要素的过程、方法、物品或者设备中还存在另外的相同要素。
[0058]
以上实施例仅用以说明本发明的技术方案,而非对其限制;尽管参照前述实施例对本发明进行了详细的说明,本领域的普通技术人员应当理解:其依然可以对前述各实施例所记载的技术方案进行修改,或者对其中部分技术特征进行等同替换;而这些修改或者替换,并不使相应技术方案的本质脱离本发明各实施例技术方案的精神和范围。