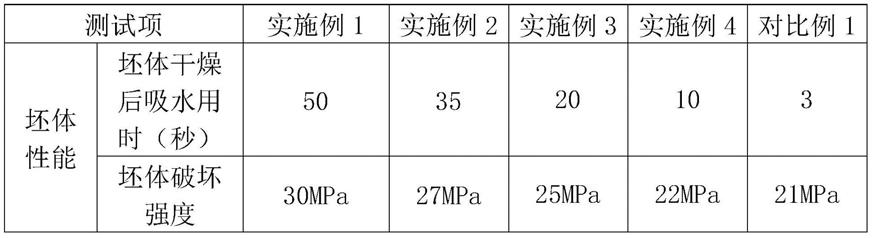
1.本发明涉及建筑材料技术领域,具体涉及一种大规格高强陶瓷薄板制备工艺及陶瓷薄板。
背景技术:
2.陶瓷环境下,有很多工艺并不能完全实施到现在市场附加值高的产品,陶瓷的大板薄板,尤其是薄板越薄工艺要求和生产要求越高,局限度高,工艺可用性随着厚度变化,砖坯越来越薄可运用的工艺越变越少,相对于产品越来越单一,薄板的生产难度与生产问题也很棘手,砖坯强度造成的烂砖,砖坯水分多时釉线走砖的砖形变化、水分过多容易出现边裂,烂砖等等,正是因为有难度,大板薄板有必要突破工艺无限制,提高市场活跃度,促进陶瓷行业发展。
3.为了解决上述技术问题,有必要提出一种新的技术方案,以解决大板薄板的砖坯强度差、生产线走砖烂砖、水分过多造成烂砖、解决大板薄板的工艺单一等问题,有助于提高生产的质与量,减少损失,重要的是可以使大板薄板的工艺更加多样性,提高新产品的开发效率和在陶瓷市场的产品竞争力。
技术实现要素:
4.为了克服现有技术的不足,本发明的目的在于提供一种大规格高强陶瓷薄板及其制备工艺,通过在薄型板件的制备过程中添加坯体防裂剂,可减缓水分吸收的速度,水分吸收时间比现有技术延长三倍,延长水分干燥时间,增加固化效果,可使坯体强度增强;坯体防裂剂干燥后形成有机膜,具有一定的防水功能,防止水分渗入坯体会快速降低坯体强度,可解决薄板水分过多对新工艺的限制问题;并且提高砖坯强度,减少干燥烂砖和裂纹,达到坯体防裂的目的,可降低出砖破损率,提高生产质量。
5.本发明的目的之一采用如下技术方案实现:一种大规格高强陶瓷薄板的制备工艺,包括以下步骤:
6.步骤1:陶瓷坯体的制备;
7.步骤2:在步骤1中制备好的坯体表面喷涂坯体防裂剂;
8.步骤3:在步骤2所得的坯体表面依次淋面釉、小干燥、表面图案装饰;
9.步骤4:将完成步骤3的坯体进行保护釉、效果釉喷涂处理;
10.步骤5:对步骤4经喷涂处理的坯体进行小干燥、烧成、磨边、抛光,制得大规格高强陶瓷薄板。
11.作为上述方案的进一步说明,所述步骤2中,所述坯体防裂剂选自丙烯酸酯类聚合物。
12.作为上述方案的进一步说明,所述步骤2中,所述坯体防裂剂加水配置成溶液,所述坯体防裂剂与水的比例为(1-2):(1-3)。
13.作为上述方案的进一步说明,所述步骤2中,所述坯体防裂剂与水的比例为1:1。
14.作为上述方案的进一步说明,所述坯体防裂剂的流速为12s。
15.作为上述方案的进一步说明,所述步骤1中,所述陶瓷坯体原料包括以下质量百分数计的组分:精选砂10-25%、超白石粒15-30%、高粘土3-10%、钾长石5-15%、高岭土10-30%、福白砂3-20%、高铝土2-10%、球土10-20%、钠砂5-10%、水玻璃0.5-1%、三聚磷酸钠0.2-0.5%、解胶剂0.1-0.3%;所述陶瓷坯体的制备过程为:将上述原料配料球磨至细度达标后进行喷雾造粒、压制成型、干燥,制得陶瓷坯体。
16.在上述制备工艺中,所述配料球磨后,料浆细度为30目筛上料≤10%;120目筛上料:≤5%,喷雾造粒粉料含水率为5-6%。
17.作为上述方案的进一步说明,所述坯体原料的化学组成为:sio2:50-70%、al2o3:16-28%、k2o:1-5%、na2o:1-5%、cao:0-0.3%、mgo:0-0.2%、fe2o3:0-0.6%;上述成分的烧失量为5.5-6%。
18.作为上述方案的进一步说明,所述坯体防裂剂的喷涂量为60*60盘15-20g。
19.作为上述方案的进一步说明,所述步骤3中,小干燥具体操作为:坯体进入干燥窑,温度为150-200℃,干燥时间为2-5分钟;所述步骤5中的小干燥具体操作为:坯体进入干燥窑,温度为150-200℃,干燥时间为2-5分钟;所述步骤5中的烧成温度为1210-1220℃,烧成时间为90-100分钟。本发明的目的之二采用如下技术方案实现:
20.一种大规格高强陶瓷薄板,所述大规格高强陶瓷薄板采用上述的制备工艺获得,所述大规格高强陶瓷薄板厚度小于3.5mm,面积大于1.62m2。
21.相比现有技术,本发明的有益效果在于:
22.1.本发明在坯体出干燥后增加一道工序,喷一层坯体保护剂,此保护剂具有一定的控水和排水功能,从而延长水分的干燥时间,在坯体表面形成一层有机膜,具有一定的防水功能和保湿效果,防止因水分渗入坯体而快速降低坯体强度,从而造成烂砖和变形;可解决薄板水分过多,减少干燥后裂砖现象;
23.2.同时,在施釉前喷一层坯体保护剂,釉面还可以起到一定的保湿效果,可以减少釉面针孔;
24.3.喷涂配体保护剂后,也为陶瓷薄板的可装饰性能提升,原来只能做数码模具装饰效果,增加坯体保护剂后可以做抛釉效果、干粒效果、金属釉效果或者数码磨具效果与干粒效果叠加装饰等,也为后期的图案、纹理装饰以及产品效果上进行多重工艺叠加应用奠定了基础;
25.4.本发明的制备工艺适应性强,减少工艺限制,适合各种大规格陶瓷薄板的制备,尤其厚度小于3.5mm,单件产品面积大于1.62m2的薄型大规格陶瓷板。
具体实施方式
26.以下以具体实施例来详细说明本发明的实施方式,借此对本发明如何应用技术手段来解决技术问题,并达成技术效果的实现过程能充分理解并据以实施。若未特别指明,实施例中所采用的技术手段为本领域技术人员所熟知的常规手段,所采用的试剂和产品也均为可商业获得的。未详细描述的各种过程和方法是本领域中公知的常规方法,所用试剂均为通过商业途径可以购买到的常用试剂。
27.本发明提供一种大规格高强陶瓷薄板的制备工艺,其包括以下步骤:
28.步骤1:陶瓷坯体的制备;
29.步骤2:在步骤1中制备好的坯体表面喷涂坯体防裂剂;
30.步骤3:在步骤2所得的坯体表面依次淋面釉、小干燥、表面图案装饰;
31.步骤4:将完成步骤3的坯体进行保护釉、效果釉喷涂处理;
32.步骤5:对步骤4经喷涂处理的坯体进行小干燥、烧成、磨边、抛光,制得大规格高强陶瓷薄板。
33.在本发明的制备工艺中,在坯体出干燥后增加一道工序,喷一层坯体保护剂,此保护剂具有一定的控水和排水功能,从而延长水分的干燥时间,在坯体表面形成一层有机膜,具有一定的防水功能和保湿效果,防止因水分渗入坯体而快速降低坯体强度,从而造成烂砖和变形;可解决薄板水分过多,减少干燥后裂砖现象;
34.同时,在施釉前喷一层坯体保护剂,釉面还可以起到一定的保湿效果,可以减少釉面针孔;
35.喷涂配体保护剂后,也为陶瓷薄板的可装饰性能提升,原来只能做数码模具装饰效果,增加坯体保护剂后可以做抛釉效果、干粒效果、金属釉效果或者数码磨具效果与干粒效果叠加装饰等,也为后期的图案、纹理装饰以及产品效果上进行多重工艺叠加应用奠定了基础。
36.作为进一步优选方案,所述步骤2中,所述坯体防裂剂选自丙烯酸酯类聚合物。
37.在本发明中,所述丙烯酸酯类聚合物选购自广东翁江化学试剂有限公司型号为pb95349的丙烯酸酯类聚合物。
38.丙烯酸酯类聚合物用于坯体干燥过程中,通过烘燥,可使其从水溶性好转变为防水性好;同时在坯体表面形成一层高透明度的有机膜,具有一定的防水功能和保湿效果,有效地阻止水分子渗透坯体,防止因水分渗入坯体而快速降低坯体强度,从而造成烂砖和变形;可解决薄板水分过多,减少干燥后裂砖现象;达到坯体防裂的目的,提高坯体强度,使制备的大规格陶瓷薄板性能优异。
39.作为进一步优选方案,所述步骤2中,所述坯体防裂剂加水配置成溶液,所述坯体防裂剂与水的比例为(1-2):(1-3)。
40.作为进一步优选方案,所述步骤2中,所述坯体防裂剂与水的比例为1:1。
41.在本发明的研究实践中发现当所述的所述坯体防裂剂与水的比例为1:1时,其防裂性能最优,延长水分渗入坯体的时间最长,为现有技术的水分渗透时间的三倍,从而更好地避免因水分渗入坯体而快速降低坯体强度,从而造成烂砖和变形;可解决薄板水分过多,减少干燥后裂砖现象。
42.作为进一步优选方案,所述坯体防裂剂的流速为12s。
43.作为进一步优选方案,所述步骤1中,所述陶瓷坯体原料包括以下质量百分数计的组分:精选砂10-25%、超白石粒15-30%、高粘土3-10%、钾长石5-15%、高岭土10-30%、福白砂3-20%、高铝土2-10%、球土10-20%、钠砂5-10%、水玻璃0.5-1%、三聚磷酸钠0.2-0.5%、解胶剂0.1-0.3%;所述陶瓷坯体的制备过程为:将上述原料配料球磨至细度达标后进行喷雾造粒、压制成型、干燥,制得陶瓷坯体。
44.在上述制备工艺中,所述配料球磨后,料浆细度为30目筛上料≤10%;120目筛上料:≤5%,喷雾造粒粉料含水率为5-6%。
45.作为进一步优选方案,所述坯体原料的化学组成为:sio2:50-70%、al2o3:16-28%、k2o:1-5%、na2o:1-5%、cao:0-0.3%、mgo:0-0.2%、fe2o3:0-0.6%;上述成分的烧失量为5.5-6%。
46.在本发明的实施例中,sio2主要来源于瓷石和高岭土,al2o3主要来源于高岭土和高铝土,k2o和na2o主要来源于长石,主要起助熔作用;
47.所述坯体原料的化学组成包括al2o3和sio2,是保证形成足够多的具有良好性能的莫来石晶体的化学组成来源,使得经过烧制后制得的所述快烧陶瓷砖的强度高,且避免了坯体在烧制过程中产生辊棒印等缺陷;
48.应当注意的是,在上述配方中,主要通过控制si和al的比例,在长石熔融作用下,继而高温熔液过程中析出更多针状的二次莫来石。二次莫来石越多、晶型越致密,坯体的机械性能越好。
49.严格控制cao、mgo的引入量,防止和减少高温烧成过程因坯体软化而产生的变形;
50.作为进一步优选方案,所述坯体防裂剂的喷涂量为60*60盘15-20g。
51.作为进一步优选方案,所述步骤3中,小干燥具体操作为:坯体进入干燥窑,温度为150-200℃,干燥时间为2-5分钟;所述步骤5中的小干燥具体操作为:坯体进入干燥窑,温度为150-200℃,干燥时间为2-5分钟;所述步骤5中的烧成温度为1210-1220℃,烧成时间为90-100分钟。在本发明中,所述坯体在辊道窑中进行烧成处理,但不局限于此。
52.本发明还提供一种大规格高强陶瓷薄板,所述大规格高强陶瓷薄板采用上述的制备工艺获得,所述大规格高强陶瓷薄板厚度小于3.5mm,面积大于1.62m2。在制备所述大规格高强陶瓷薄板的过程中,通过在坯体出干燥后增加一道工序,喷一层坯体保护剂,此保护剂具有一定的控水和排水功能,从而延长水分的干燥时间,在坯体表面形成一层有机膜,具有一定的防水功能和保湿效果,防止因水分渗入坯体而快速降低坯体强度,从而造成烂砖和变形;可解决薄板水分过多,减少干燥后裂砖现象,使得所述大规格高强陶瓷薄板的破砖率低,成品率高,大大提升产品的综合性能指标,经济效益好。
53.以下为本发明的优选实施例,以进一步阐述本发明:
54.实施例1-4及对比例1:
55.一种大规格高强陶瓷薄板的制备工艺,包括以下步骤:
56.步骤1:陶瓷坯体的制备;
57.步骤2:在步骤1中制备好的坯体表面喷涂坯体防裂剂;
58.步骤3:在步骤2所得的坯体表面依次淋面釉、小干燥、表面图案装饰;
59.步骤4:将完成步骤3的坯体进行保护釉、效果釉喷涂处理;
60.步骤5:对步骤4经喷涂处理的坯体进行小干燥、烧成、磨边、抛光,制得大规格高强陶瓷薄板。
61.其中,所述陶瓷坯体原料包括以下质量百分数计的组分:精选砂18%、超白石粒15.5%、高粘土5.5%、钾长石6%、高岭土28%、福白砂5%、高铝土5%、球土11%、钠砂6%、水玻璃0.9%、三聚磷酸钠0.3%、解胶剂0.125%,坯体增强剂1.25%;所述陶瓷坯体的制备过程为:将上述原料配料球磨至细度达标后进行喷雾造粒、压制成型、干燥,制得陶瓷坯体。
62.在上述制备工艺中,所述配料球磨后,料浆细度为30目筛上料≤10%;120目筛上料:≤5%,喷雾造粒粉料含水率为5-6%。
63.需要说明的是,本发明的陶瓷坯体采用常规配方及工艺制备而成,上述实施方式仅为示例,不限于此。
64.在上述制备工艺中,所述坯体防裂剂的使用参数如表1所示:
65.表1:实施例1-4及对比例1的坯体防裂剂加水量配比表
66.实施例实施例1实施例2实施例3实施例4对比例1防裂剂:水2:11:11:21:3不添加防裂剂
67.以上实施例1-4及对比例1均采用上述制备工艺进行制备,区别在于所述坯体防裂剂加水量配比,而对比例1为不添加所述坯体防裂剂;
68.具体为:
69.步骤1:将18%精选砂、15.5%超白石粒、5.5%高粘土、6%钾长石、28%高岭土、5%福白砂、5%高铝土、11%球土、6%钠砂、以及辅剂0.9%水玻璃、0.3%三聚磷酸钠、0.125%解胶剂,坯体增强剂1.25%进行配料球磨至细度达标后进行喷雾造粒、压制成型、干燥,制得陶瓷坯体;
70.步骤2:在步骤1中制备好的坯体表面喷涂坯体防裂剂;
71.步骤3:在步骤2所得的坯体表面依次淋面釉、小干燥、表面图案装饰;
72.步骤4:将完成步骤3的坯体进行保护釉、效果釉喷涂处理;
73.步骤5:对步骤4经喷涂处理的坯体进行小干燥、烧成、磨边、抛光,制得大规格高强陶瓷薄板。
74.其中,所述步骤3及步骤5中,小干燥具体操作为:坯体进入干燥窑,温度为180℃,干燥时间为5分钟;所述步骤5中的烧成温度为1220℃,烧成时间为100分钟。
75.效果评价及性能检测
76.测试标准及方法:
77.对实施例1-4及对比例1制备的大规格陶瓷薄板进行相关性能测试,其中:
78.1、坯体性能测试(根据企业制定的测试方法进行测试)
79.坯体干燥后吸水用时:用滴定管滴一滴水滴在坯体表面,测试被吸收的时间长;
80.釉面效果(剥釉、针孔、气泡等):具体测试过程为取600*600规格样品,施釉后观察此单位面积下釉面性能情况。
81.2、产品性能测试:根据《gbt 23266-2009》国家标准的规定进行断裂模数及破坏强度的测定;
82.抗釉裂性:具体的测试方法为:使整砖在蒸压釜中承受高压蒸汽的作用,再观察表面的釉裂情况,一般是在500kpa的压力,保持2小时试验后,釉面应无裂纹或剥落。
83.上述测试项目测试结果如表4所示:
84.表4:试验数据汇总表
[0085][0086][0087]
如上表测试数据所示,所述坯体原料的化学组成包括al2o3和sio2,是保证形成足够多的具有良好性能的莫来石晶体的化学组成来源,使得经过烧制后制得的所述快烧陶瓷砖的强度高,且避免了坯体在烧制过程中产生辊棒印等缺陷;
[0088]
应当注意的是,在上述配方中,主要通过控制si和al的比例,在长石熔融作用下,继而高温熔液过程中析出更多针状的二次莫来石。二次莫来石越多、晶型越致密,坯体的机械性能越好。
[0089]
严格控制cao、mgo的引入量,防止和减少高温烧成过程因坯体软化而产生的变形;
[0090]
更重要的是,本发明的制备工艺中,在坯体出干燥后增加一道工序,喷一层坯体保护剂,此保护剂具有一定的控水和排水功能,从而延长水分的干燥时间,在坯体表面形成一层有机膜,具有一定的防水功能和保湿效果,防止因水分渗入坯体而快速降低坯体强度,从而造成烂砖和变形;可解决薄板水分过多,减少干燥后裂砖现象;同时,在施釉前喷一层坯体保护剂,釉面还可以起到一定的保湿效果,可以减少釉面针孔;
[0091]
上述实施例2为本发明的最优实施例,实施例1中虽然在添加防裂剂后坯体干燥吸水用时最长,但淋完釉后干的慢,生产线落脏影响产品质量,釉面效果欠佳,而实施例2制备的大规格陶瓷薄板各方面性能指标较优,釉面效果好,这是由于在本发明的研究实践中发现当所述的所述坯体防裂剂与水的比例为1:1时,其防裂性能最优,延长水分渗入坯体的时间最长,为现有技术的水分渗透时间的三倍,从而更好地避免因水分渗入坯体而快速降低坯体强度,从而造成烂砖和变形;可解决薄板水分过多,减少干燥后裂砖现象。
[0092]
同样的,参考实施例4与对比例1中的数据,由于实施例4加入防裂剂对比加水量偏小,对比例中未加入防裂剂,因此实施例4与对比例1的水分渗透速率较高,釉面出现针孔,且坯体强度较低,制备的陶瓷薄板的断裂模数及破坏强度相比实施例1-3而言也偏低。
[0093]
以上所述,仅为本发明较佳实施例而已,故不能依此限定本发明实施的范围,即依
本发明专利范围及说明书内容所作的等效变化与修饰,皆应仍属本发明涵盖的范围内。