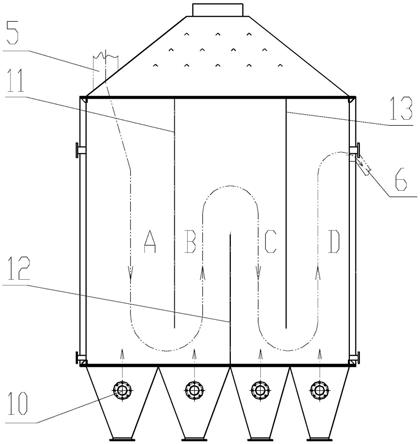
1.本实用新型涉及蒸汽沸腾炉煅烧设备技术,尤其是一种建筑石膏煅烧蒸汽沸腾炉炉内分隔装置。
背景技术:
2.现在建筑石膏行业广泛采用蒸汽沸腾炉作为煅烧设备,蒸汽沸腾炉一般由炉体、布风板、布风箱和换热管等几个部分组成,其基本工作原理是:干脱硫石膏从进料口进入炉内,而流化风由罗茨风机从风箱内吹入,经过布风板吹入炉体中,布风板上设有密集的小孔,以保证流化风速。物料从上至下进入炉内,流化风从炉底向上鼓入,物料在炉内形成流化。而蒸汽则由专用母管通入至换热管中,流化态物料在换热管外的炉体中受热后脱去结晶水,煅烧为建筑石膏后从出料口溢流出。现有技术中在一般的沸腾炉炉内设有一件分隔板,将炉体分为两个煅烧室,使得物料在炉内的流化路径呈u形。这些沸腾炉主要存在以下几个缺点:一是产量偏小,煅烧成品产量多小于30t/h;二是煅烧的建筑石膏容易产生欠烧的问题,三相组分中二水石膏成分容易偏高;三是煅烧温度高,煅烧温度多在160℃左右,要求蒸汽压力在1.0mpa以上;四是流化风缺少有效的控制手段。
技术实现要素:
3.本实用新型的目的是为了解决上述问题,提供一种建筑石膏煅烧蒸汽沸腾炉炉内分隔装置,它具有提升沸腾炉的产量,避免煅烧过程中出现欠烧现象,可以把低压蒸汽作为本设备的热源,流化风可调,物料流化效果佳等特点。
4.本实用新型的上述技术问题主要是通过下述技术方案得以解决的:一种建筑石膏煅烧蒸汽沸腾炉炉内分隔装置,包括炉体、布置在炉体内的换热管,以及位于炉体底部的进风箱、位于炉体顶部的集气罩,其特征是在所述炉体内由竖直布置的第一分隔板、第二分隔板、第三分隔板把炉体内腔分隔成四个煅烧室,四个煅烧室使物料在炉体内形成w形行走路径;其中第一煅烧室的顶部设有进料口,第四煅烧室设有出料口;所述进风箱设有与四个煅烧室单配的独立风箱,每个独立风箱的进风管上均设有调节阀。
5.前述的一种建筑石膏煅烧蒸汽沸腾炉炉内分隔装置中,作为优选,所述进风箱与炉体之间设有布风板。
6.前述的一种建筑石膏煅烧蒸汽沸腾炉炉内分隔装置中,作为优选,所述第一分隔板、第二分隔板、第三分隔板在炉体内按上、下、上的分隔结构布置,即第一分隔板和第三分隔板从炉体内的上部往下分隔,下部留出物料通道;第二分隔板从下部往上部分隔,上部留出物料通道。
7.前述的一种建筑石膏煅烧蒸汽沸腾炉炉内分隔装置中,作为优选,所述炉体底部设有冷凝出水口。
8.前述的一种建筑石膏煅烧蒸汽沸腾炉炉内分隔装置中,作为优选,第一煅烧室、以及在第一煅烧室中的换热管换热面积在四个煅烧室中所占比例最大,占整个炉体体积的
26-35%。
9.前述的一种建筑石膏煅烧蒸汽沸腾炉炉内分隔装置中,作为优选,所述进风箱设有的独立风箱内均设有压力传感器。
10.前述的一种建筑石膏煅烧蒸汽沸腾炉炉内分隔装置中,作为优选,在所述的四个煅烧室内均设有温度传感器。
11.前述的一种建筑石膏煅烧蒸汽沸腾炉炉内分隔装置中,作为优选,所述炉体横截面为长方形结构,进风箱、集气罩呈锥体结构。
12.前述的一种建筑石膏煅烧蒸汽沸腾炉炉内分隔装置中,作为优选,所述炉体上设有检修门。
13.前述的一种建筑石膏煅烧蒸汽沸腾炉炉内分隔装置中,作为优选,所述进风箱上设有观察窗。
14.本技术方案总体结构与传统沸腾炉类似,由炉体、布风板、布风箱以及换热管等几个主要部分构成,其基本工作原理为干脱硫石膏从进料口进入炉体内,而流化风由罗茨风机从进风箱内吹入,进风箱采用四个独立的风箱,每个独立的风箱均配一个进气口,进气口进风管上均设有一个手动调节阀,因此可根据煅烧需求调节炉内各个分区的风量。流化风经过布风板吹入炉体中,布风板上设有密集的小孔,以保证流化风速。物料从上至下进入炉内,流化风从炉底向上鼓吹,物料在炉内形成流化。蒸汽由母管进气口通入至换热管中,流化态物料在换热管外部的炉体中受热后脱去结晶水,煅烧为建筑石膏后从出料口溢流而出。
15.本方案沸腾炉炉体采用由三件分隔板分隔成四个煅烧室,分隔板采用上、下、上的分隔方式,从而使炉体形成4个独立的煅烧室,从而使物料在炉体内的行走路径呈w形,物料在炉体内停留时间比传统沸腾炉更长,煅烧更充分、效果更佳。根据建筑石膏的煅烧特点,刚进入炉内的物料温度低且容重大,故第一个煅烧室和换热面积均为最大,以充分保证第一煅烧室的煅烧效果。同时,4个煅烧室与底部4个风箱一一对应,在每个风箱内和炉体内设置压力传感器,在每个煅烧室设置温度传感器,可根据相关温度和压力数据反馈判断炉内的流化煅烧情况,并按此信息数据灵活调节每个煅烧室内的流化风量,使物料流化效果更佳,从而达到更好更稳定的煅烧效果。
16.与现有技术相比,本实用新型的有益效果是:生产量比传统沸腾炉大,产品质量稳定;在生产线运行平稳的情况下,三相组分中二水相可控制在3%以内;蒸汽压力及温度要求较低,适应性强,对气源要求低于传统沸腾炉;煅烧温度低,节能,煅烧效率高于传统沸腾炉;产品质量好;生产出现不稳定情况时,可通过调节流化风进口阀门,快速对煅烧工况实现调节。
附图说明
17.图1是本实用新型的一种结构示意图。
18.图2是图1的右视图。
19.图3是图1的俯视图。
20.图4是本实用新型的一种炉体分隔及物料走向图。
21.图5是图4的俯视图。
22.图中:1.集气罩,2.炉体,3.布风板,4.进风箱,5.进料口,6.出料口,7.进气口,8.冷凝出水口,9.换热管,10.进风口,11.第一分隔板,12.第二分隔板,13.第三分隔板。
23.a.第一煅烧室;b.第二煅烧室;c.第三煅烧室;d.第四煅烧室。
具体实施方式
24.下面通过实施例,并结合附图,对本实用新型的技术方案作进一步具体的说明。
25.本实施例一种建筑石膏煅烧蒸汽沸腾炉炉内分隔装置,设一横截面为长方形结构的炉体2,炉体2内竖直排列换热管9组,位于炉体2底部设有进风箱4,炉体2顶部设有集气罩1,如图1、图2所示,进风箱4呈倒锥体结构,集气罩1呈正锥体结构。
26.在炉体2内,通过竖直布置的第一分隔板11、第二分隔板12、第三分隔板13把炉体2内腔分隔成四个煅烧室,即第一煅烧室a、第二煅烧室b、第一煅烧室c、第一煅烧室d,分隔板为整块10mm厚的钢板,在炉体2与炉体2内壁焊接,第一分隔板11、第二分隔板12、第三分隔板13在炉体2内按上、下、上的分隔结构布置,即第一分隔板12和第三分隔板13从炉体内的上部往下分隔,下部留出物料通道,第二分隔板12从下部往上部分隔,上部留出物料通道,由此,四个煅烧室使物料在炉体2内形成w形行走路径。装配时在四个煅烧室内均装有温度传感器。
27.其中,第一煅烧室a的顶部设有进料口5,第一煅烧室a以及位于第一煅烧室a中的换热管9换热面积在四个煅烧室中所占比例最大,约占整个炉体体积的30%。第四煅烧室上部位置(位于集气罩1部位)设有出料口6。进风箱4设有与四个煅烧室单配的独立风箱,每个独立风箱的进风管上均设有调节阀,且进风箱4设有的独立风箱内都设有压力传感器。
28.进风箱4与炉体2之间设有布风板3,布风板3上设有密集的小孔,以保证流化风速。炉体2底部设有冷凝出水口8。
29.另外,炉体2上设有检修门,并在炉体2其中的一个对边设置安装脚,使整个装置可以在楼面上安装。进风箱4上设有观察窗或清理小门等。
30.工作时,干脱硫石膏从进料口5进入炉体2内,流化风由罗茨风机分别从四个独立进风箱4的进风口10吹入,进气口10的进风管上均设一个手动调节阀,可根据煅烧需求调节炉体2内各个分区的风量。流化风经过布风板3吹入炉体2中,由此,物料从上至下进入炉体2内,流化风从炉底向上鼓入,物料在炉体内形成流化。而蒸汽由母管进气口7通入至换热管9中,流化态物料在换热管9外的炉体2中受热后脱去结晶水,煅烧为建筑石膏后从出料口6溢流而出。由于物料在炉体2内的行走路径呈w形,停留时间比传统沸腾炉更长,并根据炉体2内相关温度、压力数据反馈判断炉内的流化煅烧情况,通过调节阀可以灵活调节每个煅烧室室内的流化风量,从而使物料流化更充分,煅烧效果更佳。
31.经检测,使用本装置建筑石膏产量可轻松达到40t/h以上,产品质量稳定。在生产线运行平稳的状态下,三相组分中二水相可控制在3%以内,基本不会出现超过5%的欠烧现象;对蒸汽压力及温度要求较低,可节省不少能源,采用0.8mpa过热蒸汽亦可稳定煅烧,实际生产中进炉蒸汽压力调到0.5mpa亦能煅烧出优质产品,对气源要求低于传统沸腾炉(一般要求1.0mpa以上);煅烧温度采用140~150℃煅烧即可,传统沸腾炉多在160℃,煅烧效率高于传统沸腾炉;建筑石膏成品质量方面2小时抗折强度最高可达4.0mpa,远高于国标中3.0等级的3.0mpa的最优标准。
32.上述实施例是对本实用新型的说明,不是对本实用新型的限定,在不脱离本技术方案原则,任何对本实用新型的简单变换后的结构等均属于本实用新型的保护范围。