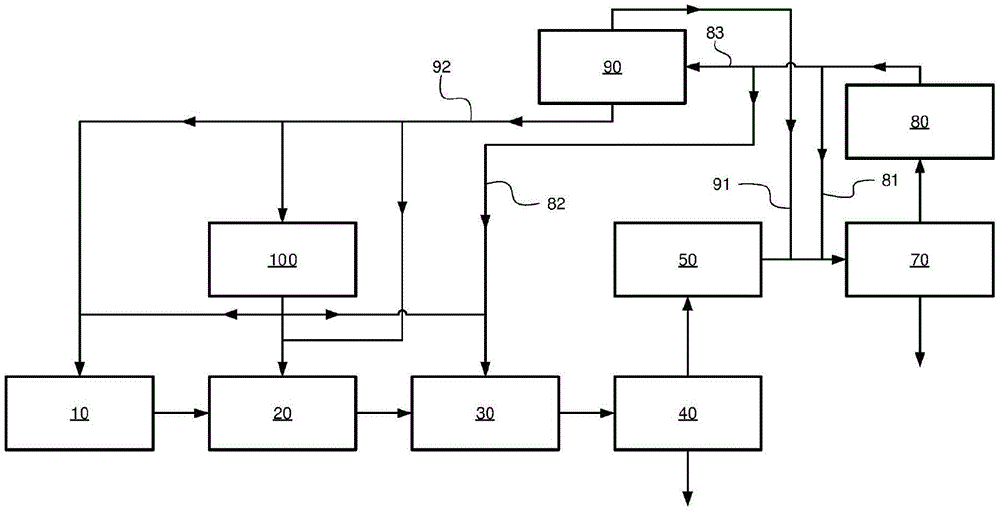
本发明涉及丙烯聚合方法。特别地,本发明涉及一种在多阶段方法中生产丙烯共聚物的方法,该方法具有提高的未反应丙烯单体的回收率并且以最低的操作成本在操作中稳定。进一步地,本发明还涉及用于生产丙烯共聚物的聚合装置。
背景技术
例如从EP0887380和WO2004/111095已知,在多阶段方法中聚合丙烯以调整最终聚丙烯的性能。
在EP2796472中,丙烯在两个反应阶段中聚合,特别是在环管反应器中,然后是串联连接的气相反应器,以生产聚丙烯,其特别适用于制造管道。另一方面,EP2853562描述了在类似的环管反应器-气相反应器配置中的丙烯聚合,其中生产的聚丙烯特别适用于制造薄膜。进一步地,EP2796473涉及在至少三个反应阶段中生产具有宽分子量分布的丙烯共聚物的方法,其中,例如,第一聚合阶段在环管反应器中进行,而第二和第三聚合阶段在串联连接的气相反应器中进行。
在这样的聚合过程中,通常在聚合过程中所应用的单体丙烯没有被完全消耗,使得需要从最终聚合物中除去未反应的单体。出于工艺经济原因,未反应的丙烯不送去处理,而是至少部分回收并再循环至工艺的反应阶段以进行进一步聚合。例如,EP0887380公开了离开环管反应器-气相反应器配置的气相反应器的反应产物被转移到固/气分离单元,在固/气分离单元中固体聚丙烯聚合物作为塔底产物回收,而包含未反应丙烯的气态塔顶馏出物通过单体回收系统再循环至气相反应器和/或环管反应器。在该单体回收系统(其可以包括膜单元或汽提塔)中,待再循环的丙烯单体不含氢气和/或轻质惰性烃。
在生产丙烯共聚物的情况下,未反应的丙烯通常与未反应的共聚单体混合。例如,当生产丙烯-乙烯共聚物,比如丙烯-乙烯无规共聚物时,再循环物流通常包含未反应的丙烯单体以及未反应的乙烯共聚单体。从而,乙烯可能会在反应阶段的丙烯进料容器中积累,未反应的丙烯被再循环至该反应阶段中。然而,来自所述丙烯进料容器的丙烯进料中的过高乙烯浓度可能导致操作问题,特别是当丙烯进料被引入淤浆反应器或前面的预聚合器时,要么是由于所提供的新鲜催化剂首先与丙烯进料接触的地方反应活性过高,要么是在预聚合器及其出口管线中由于形成粘性副产物,这些副产物可能会结块。
因此,当生产乙烯含量高的丙烯-乙烯共聚物,比如丙烯-乙烯无规共聚物时,要么需要限制不可避免地与乙烯共聚单体混合的未反应丙烯单体的再循环,要么必须将大部分夹带的乙烯共聚单体从再循环物流中除去,然后将再循环物流送入丙烯进料容器或作为进料直接送入预聚合阶段。然而,当未反应的丙烯单体的再循环被限制时,至少一部分未反应的丙烯单体被送去处理,从而降低了聚合过程的回收效率。另一方面,未反应的乙烯共聚单体的去除需要额外的工艺步骤。例如,可以通过蒸馏降低再循环物流中未反应的乙烯共聚单体的浓度。然而,在回收系统中长期运行乙烯蒸馏塔会消耗大量能源,因此成本非常高。同样,乙烯去除可在汽提塔中进行,在汽提塔中轻组分如氢气和乙烯至少部分地从丙烯再循环物流中去除。同样,从大量未反应的丙烯中汽提未反应的乙烯是一个能源密集型的过程,因此可能是不经济的。作为另一种选择,可以对再循环物流进行热处理,这也显著增加了能量消耗和操作成本。然而,在工业聚合过程中,一般目标是将必要的安装和操作成本降至最低。
因此,仍然需要一种在多阶段方法中生产丙烯共聚物,特别是丙烯和乙烯的共聚物,比如丙烯-乙烯无规共聚物的方法,该方法表现出以降低的操作成本提高了未反应丙烯单体的回收效率,并且不影响生产过程的稳定性。
技术实现要素:
本发明基于以下发现:在包括至少三个反应阶段的生产丙烯共聚物的方法中,可以通过将来自所述方法的回收系统的特定物流分成三股不同的物流,从而以最小的操作成本提高未反应的丙烯单体的回收效率,并且不影响该方法的稳定性。具体地,在现有技术中,来自回收系统的蒸馏塔的包含未反应丙烯、未反应乙烯和任选氢气的塔顶物流通常被冷凝并传送至汽提塔,在汽提塔中轻组分,比如氢气和乙烯,至少部分被除去。然后将包含未反应的丙烯的剩余部分再循环至丙烯进料容器或反应阶段。然而,在本发明中,来自回收系统的蒸馏塔的所述冷凝的塔顶物流被分成三股不同的物流,其中一股物流仍然被送至汽提塔,而一股物流被送至最后反应阶段和一股物流被循环回蒸馏塔。此外,已经发现由于一股分流的再循环,不再需要用于最后反应阶段的另一个丙烯进料容器。因此,甚至可以降低该方法的操作成本和各个聚合单元的安装成本。
因此,一方面,本发明涉及一种在至少三个串联连接的反应阶段中生产丙烯共聚物的方法,其包括以下步骤:
a)通过将丙烯、任选的乙烯、任选的氢气、聚合催化剂和任选的助催化剂引入预聚合阶段来预聚合聚合催化剂,以产生预聚合的聚合催化剂;
b)从预聚合阶段取出预聚合的聚合催化剂并将其送入第一反应阶段;
c)通过将丙烯、乙烯和任选的氢气引入第一反应阶段来聚合丙烯,以产生包含第一丙烯共聚物、未反应的丙烯、未反应的乙烯和氢气的第一反应混合物,如果未反应的丙烯、未反应的乙烯和氢气存在的话;
d)从第一反应阶段取出包含第一反应混合物的第一产物流并将其至少一部分送入第二反应阶段;
e)在第一丙烯共聚物的存在下在第二反应阶段继续聚合,任选地将额外的丙烯、额外的乙烯和/或额外的氢气引入第二反应阶段,以产生包含第一丙烯共聚物和第二丙烯共聚物的丙烯聚合物混合物、未反应的丙烯、未反应的乙烯和氢的第二反应混合物,如果未反应的丙烯、未反应的乙烯和氢存在的话;
f)从第二反应阶段取出包含第二反应混合物的第二产物流并将其至少一部分送至分离单元,并将第二产物流分离成第一塔顶物流和第一塔底产物流,第一塔顶物流包含未反应的丙烯、未反应的乙烯、低聚物以及氢气和助催化剂,如果未反应的丙烯、未反应的乙烯、低聚物以及氢气和助催化剂存在的话,第一塔底产物包含丙烯聚合物混合物的固体颗粒;
g)从第一塔底产物流中回收丙烯聚合物混合物;
h)将至少一部分第一塔顶物流冷凝;
i)将至少一部分第一塔顶物流送入蒸馏塔,并将所述至少一部分第一塔顶物流分离成第二塔顶物流和第二塔底产物流,第二塔顶物流包含未反应的丙烯、未反应的乙烯和氢气,如果未反应的丙烯、未反应的乙烯和氢气存在的话;
j)从蒸馏塔中取出第二塔顶物流和第二塔底产物流;以及
k)将至少一部分第二塔顶物流冷凝,从而产生冷凝的第二塔顶物流和任选的汽相第二塔顶物流;
其中,所述方法进一步包括以下步骤:
l)将冷凝的第二塔顶物流分为蒸馏回流物流、第一再循环物流和第二再循环物流,并将蒸馏回流物流返回到蒸馏塔的顶部,将第一再循环物流送至第二反应阶段并将第二再循环物流送至汽提塔;以及
m)从汽提塔中取出包含未反应的乙烯和氢气的第三塔顶物流,如果未反应的乙烯和氢气存在的话,和包含未反应的丙烯的第三塔底产物流,并将第三塔顶物流送至蒸馏塔,并将至少一部分第三塔底物流送至丙烯进料容器、预聚合阶段、第一反应阶段或到其组合。
另一方面,本发明涉及一种用于生产丙烯共聚物的聚合单元,其包括丙烯进料容器和串联连接的预聚合阶段、第一反应阶段和第二反应阶段,以及回收系统,所述回收系统包括:
i)与第二反应阶段连接的分离单元;
ii)与分离单元(的顶部)连接的第一冷凝器;
iii)与第一冷凝器(的底部)连接的蒸馏塔;
iv)与蒸馏塔(的顶部)连接的第二冷凝器;和
v)汽提塔;
其中所述回收系统进一步包括
vi)连接第二冷凝器(的底部)与蒸馏塔(的顶部)的蒸馏回流管线;
vii)连接第二冷凝器(的底部)与第二反应阶段的第一再循环管线;
viii)连接第二冷凝器(的底部)与汽提塔的第二再循环管线;
ix)连接汽提塔(的顶部)与蒸馏塔的第三再循环管线;和
x)连接汽提塔(的底部)与丙烯进料容器、预聚合阶段和/或与第一反应阶段的第四再循环管线。
附图说明
图1:根据本发明的聚合单元的示意图。
图2:根据本发明的聚合单元的一个优选实施方案的示意图。
具体实施方式
定义
根据本发明的“聚合单元”是一种其中可以通过聚合产生烯烃聚合物(这里是丙烯共聚物)的单元。该单元至少包括预聚合阶段、第一反应阶段和第二反应阶段。
术语“预聚合阶段”和“反应阶段”代表一个或多个相同类型的串联连接的聚合反应器,包括用于操作和互连各个聚合反应器的手段,比如进料容器、入口和出口管线等。
优选地,第一反应阶段包括至少一个淤浆反应器并且第二反应阶段包括至少一个气相反应器。预聚合阶段优选包括淤浆反应器。
“淤浆反应器”是指以散装或淤浆形式运行并且其中聚合物以颗粒形式形成的任何反应器。“淤浆”是分散在液相中的固体颗粒的异质混合物。固体颗粒通常是通过聚合过程获得的固体烯烃聚合物颗粒,这里是聚丙烯颗粒。流体相通常包含液态烯烃单体(这里是丙烯),和任选的未反应的共聚单体(这里是乙烯)。
优选地,淤浆反应器是“环管反应器”,其是指通常完全充满浆料的封闭管道,其中通过使用循环泵使浆料沿管道高速循环。环管反应器在本领域中是众所周知的,并且在例如US-A-4582816、US-A-3405109、US-A-3324093、EP-A-479186和US-A-5391654中给出了实例。环管反应器通常包括垂直段和水平段,两者分别通过弯管或弯头相互连接。取决于水平段是通过弯管或弯头与垂直段的上端或下端相互连接,水平段表示下水平段或上水平段。
“气相反应器”是指任何机械混合反应器或流化床反应器,其中聚合反应是使用气态烯烃单体(这里是丙烯)进行的,聚合物颗粒在其中生长。
“回收系统”代表适用于从聚合过程中回收未反应的单体(这里是丙烯)的所有技术手段的整体,例如气/固分离单元、蒸馏塔、汽提塔、排气冷凝器或膜单元。
术语“回收效率”是指实际重新引入聚合过程并最终被聚合消耗的未反应的丙烯单体的量与未反应的丙烯单体的总量之间的关系。因此,再循环到聚合过程中的未反应的丙烯单体的量相对于未反应的丙烯单体的总量越高,回收效率越好。
具体说明
方法
一方面,本发明涉及在至少三个串联连接的反应阶段中以提高的回收效率生产丙烯共聚物的方法。
预聚合阶段
在本发明方法的第一步(步骤a))中,通过将丙烯、任选的乙烯、任选的氢气、聚合催化剂和任选的助催化剂引入预聚合阶段来预聚合聚合催化剂。
引入预聚合阶段的聚合催化剂可以是能够生产所期望的丙烯聚合物的任何催化剂。合适的催化剂尤其是基于过渡金属的齐格勒-纳塔催化剂,比如钛、锆和/或钒催化剂。尤其是齐格勒-纳塔催化剂是有用的,因为它们可以以高生产率生产分子量范围宽的丙烯聚合物。
合适的齐格勒-纳塔催化剂优选包含负载在颗粒载体上的镁化合物、铝化合物和钛化合物。
颗粒载体可以是无机氧化物载体,比如二氧化硅、氧化铝、二氧化钛、二氧化硅-氧化铝和二氧化硅-二氧化钛。优选地,载体是二氧化硅。
二氧化硅载体的平均粒径通常可以为2μm至100μm。然而,已经证明,如果载体的中值粒径为6μm至90μm,优选6μm至70μm,则可以获得特别的优势。
镁化合物是二烷基镁和醇的反应产物。所述醇是直链或支链的脂肪族一元醇。优选地,所述醇具有6至16个碳原子。支链醇是特别优选的,并且2-乙基-1-己醇是优选醇的一个实例。二烷基镁可以是镁键合两个烷基的任何化合物,两个烷基可以相同也可以不同。丁基-辛基镁是优选的二烷基镁的一个实例。
铝化合物是含氯的烷基铝。特别优选的化合物是烷基二氯化铝和烷基倍半氯化铝。
钛化合物是含卤素的钛化合物,优选含氯的钛化合物。特别优选的钛化合物是四氯化钛。
催化剂可以通过将载体与上述化合物依次接触来制备,如EP-A-688794或WO-A-99/51646中所述。或者,如WO-A-01/55230中所述,可以通过首先由组分制备溶液然后将该溶液与载体接触来制备。
另一组合适的齐格勒-纳塔催化剂包含钛化合物和作为载体的卤化镁化合物。因此,催化剂含有在二卤化镁(如二氯化镁)上的钛化合物。此类催化剂公开于例如WO-A-2005/118655和EP-A-810235。
还有一种类型的齐格勒-纳塔催化剂是通过一种其中形成乳液的方法制备的催化剂,其中活性组分在至少两种液相的乳液中形成分散相,即不连续相。从乳液中固化液滴形式的分散相,其中形成固体颗粒形式的催化剂。这类催化剂的制备原理见Borealis的WO-A-2003/106510。
齐格勒-纳塔催化剂与助催化剂一起使用。合适的助催化剂是烷基金属化合物,尤其是烷基铝化合物。这些化合物包括烷基卤化铝,比如二氯化乙基铝、二乙基氯化铝、倍半氯化乙基铝、二甲基氯化铝等。它们还包括三烷基铝化合物,比如三甲基铝、三乙基铝、三异丁基铝、三己基铝和三正辛基铝。此外,它们包括烷基铝氧化合物,比如甲基铝氧烷(MAO)、六异丁基铝氧烷(HIBAO)和四异丁基铝氧烷(TIBAO)。也可以使用其他烷基铝化合物,比如异丁基异戊基铝。特别优选的助催化剂是三烷基铝,其中特别使用三乙基铝、三甲基铝和三异丁基铝。
如果需要,助催化剂还可以包括外部电子供体。合适的电子供体化合物公开于WO-A-95/32994、US-A-4107414、US-A-4186107、US-A-4226963、US-A-4347160、US-A-4382019、US-A-4435550、US-A-4465782、US-A-4472524、US-A-4473660、US-A-4522930、US-A-4530912、US-A-4532313、US-A-4560671和US-A-4657882。本领域还已知由以硅为中心原子的有机硅烷化合物组成的电子供体,该有机硅烷化合物含有Si-OCOR、Si-OR和/或Si-NR2键,R是具有1-20个碳原子的烷基、烯基、芳基、芳烷基或环烷基。此类化合物描述于US-A-4472524、US-A-4522930、US-A-4560671、US-A-4581342、US-A-4657882、EP-A-45976、EP-A-45977和EP-A-1538167。
助催化剂的用量取决于具体的催化剂和助催化剂。通常三乙基铝的用量使得铝与过渡金属的摩尔比,如Al/Ti,为1mol/mol至1000mol/mol,优选3mol/mol至100mol/mol,尤其是约5mol/mol至约30mol/mol。
还可以使用茂金属催化剂。茂金属催化剂包含过渡金属化合物,其含有环戊二烯基、茚基或芴基配体。优选地,催化剂含有两个环戊二烯基、茚基或芴基配体,它们可以被优选含有一个或多个硅和/或碳原子的基团桥连。进一步地,配体可以具有取代基,比如烷基、芳基、芳烷基、烷芳基、甲硅烷基、硅烷氧基、烷氧基或其他杂原子基团等。合适的茂金属催化剂在本领域中是已知的并且公开于尤其是WO-A-95/12622、WO-A-96/32423、WO-A-97/28170、WO-A-98/32776、WO-A-99/61489、WO-A-03/010208、WO-A-03/051934、WO-A-03/051514、WO-A-2004/085499、EP-A-1752462和EP-A-1739103。
茂金属催化剂与助催化剂一起使用。合适的助催化剂是金属烷基化合物,尤其是本领域已知的烷基铝化合物。与茂金属催化剂一起使用的特别合适的助催化剂是烷基铝氧化合物,比如甲基铝氧烷(MAO)、四异丁基铝氧烷(TIBAO)或六异丁基铝氧烷(HIBAO)。
预聚合的目的是在低温和/或低丙烯单体浓度下将少量丙烯(共)聚合物聚合到催化剂上,以产生预聚合的聚合催化剂。通过预聚合,可以提高催化剂在浆料中的性能和/或改变最终丙烯聚合物的性质。预聚合步骤优选在淤浆反应器中进行。更优选地,预聚合在环管反应器中进行。
然后预聚合优选在液体单体中进行,其中单体浓度为至少50重量%,通常至少60重量%。因此,环管反应器中的单体浓度可以为50重量%至90重量%,优选60重量%至90重量%,更优选70重量%至90重量%。
此外,预聚合优选连续地进行。
预聚合步骤中的温度通常为0℃至90℃,优选0℃至40℃,更优选0℃至30℃。
压力并不重要,通常为1巴至150巴,优选10巴至100巴。
通常,在预聚合步骤中每1克固体催化剂组分约0.1至1000克丙烯单体聚合到固体催化剂组分上。如本领域技术人员已知的,从连续预聚合反应器中回收的催化剂颗粒并不都包含相同量的预聚物。相反,每个颗粒都有其自身的特征量,这取决于该颗粒在预聚合反应器中的停留时间。由于一些颗粒在反应器中停留的时间较长,而一些颗粒的停留时间较短,因此不同颗粒上的预聚物的量也不同,一些单个颗粒可能含有超出上述范围限制的一定量的预聚物。然而,催化剂上预聚物的平均量通常在上述规定的范围内。
如本领域中已知的,可以通过氢气来控制预聚物的分子量。此外,如WO-A-96/19503和WO-A-96/32420中所公开的,抗静电添加剂可以用于防止颗粒彼此粘附或与反应器的壁粘附。
聚合催化剂组分优选全部引入预聚合步骤。然而,在固体催化剂组分和助催化剂可以分开进料的情况下,可以仅将一部分助催化剂引入预聚合阶段,而将其余部分提供给随后的聚合阶段。同样在这种情况下,有必要在预聚合阶段引入如此多的助催化剂,以便在预聚合阶段中获得充分的聚合反应。
在随后的步骤b)中,将预聚合的聚合催化剂从预聚合阶段取出并送至串联连接的第一反应阶段。
第一反应阶段
在本发明方法的步骤c)中,通过将丙烯、乙烯和任选的氢气引入第一反应阶段来聚合丙烯。
可以将氢气引入第一反应阶段以控制第一丙烯共聚物的分子量。
由于丙烯单体和乙烯共聚单体在聚合过程中通常不会被完全消耗,因此在第一反应阶段中产生包含第一丙烯共聚物、未反应的丙烯、未反应的乙烯和氢气(如果存在)的第一反应混合物。
优选地,第一反应阶段包括至少一个淤浆反应器,更优选至少一个环管反应器。因此,第一反应阶段可以包括两个或更多个串联连接的淤浆反应器,优选环管反应器。
此外,在第一反应阶段包括至少一个淤浆反应器,或优选至少一个环管反应器的情况下,丙烯的聚合通常在液体单体中以颗粒形式过程进行。在这种方法中,聚合催化剂经由如上所述的预聚合步骤以颗粒形式送入至少一个淤浆反应器,优选送入至少一个环管反应器。然后丙烯聚合物在催化剂颗粒上生长,从而形成在液体单体中包含固体丙烯聚合物颗粒的浆料。
液相中的单体浓度为至少50重量%,通常至少60重量%。因此,环管反应器中的单体浓度可以为50重量%至90重量%,优选60重量%至90重量%,更优选70重量%至90重量%。
至少一个淤浆反应器中,优选至少一个环管反应器中的温度通常为60℃至100℃,优选70℃至90℃。应避免过高的温度以防止聚丙烯部分溶解到稀释剂中和反应器结垢。压力为1巴至150巴,优选为40巴至80巴。
优选将氢气引入至少一个淤浆反应器,优选引入至少一个环管反应器,以控制丙烯聚合物的熔体流动速率(MFR)。达到所期望的MFR所需的氢气量取决于所用的催化剂和聚合条件。
在至少一个淤浆反应器中,优选在至少一个环管反应器中的平均停留时间通常为20至120分钟,优选30至80分钟。正如本领域众所周知的,平均停留时间τ可以从下式计算:
其中VR是反应空间的体积(即反应器的体积),QO是产物流(包括聚合物产物和流体反应混合物)的体积流率。
在至少一个淤浆反应器中,优选在至少一个环管反应器中的生产速率用催化剂进料速率适当地控制。
在随后的步骤d)中,从第一反应阶段取出包含第一反应混合物的第一产物流并且将其至少一部分送到第二反应阶段。
因此,取出的第一产物流可以被直接或间接地送到第二反应阶段。当直接送入时,第一产物流在没有任何纯化步骤的情况下被导入第二反应阶段。当间接送入时,第一产物流在被导入第二反应阶段之前经历纯化步骤。该纯化步骤可以包括将第一产物流导入气/固分离单元,例如闪蒸罐,在那里固体第一丙烯共聚物作为塔底产物被回收并送到第二反应阶段。包含未反应的丙烯和未反应的乙烯的排气在以气态形式被导入第二反应阶段之前通过使用膜单元或汽提塔完全或部分不含氢和/或轻质惰性烃杂质。或者,在未反应的丙烯单体作为液体进料到第二反应区之前,可以将排气冷凝,并且可以任选地除去氢气或其他轻组分。
第二反应阶段
在本发明方法的步骤e)中,在第一丙烯共聚物的存在下在第二反应阶段继续丙烯的聚合以产生第二反应混合物。
任选地,可将新鲜丙烯单体引入第二反应区。在本文中,新鲜丙烯单体是指未再循环的丙烯单体,而不是指已经由第一产物流从第一反应阶段转移的或经由第一再循环物流再循环到第二反应阶段的未反应的丙烯单体。
然而,优选不将新鲜丙烯单体引入第二反应阶段。相反,优选地,经由第一产物流来自第一反应阶段和/或经由第一再循环物流被再循环到第二反应阶段的未反应的丙烯单体的量足以在第二反应阶段中聚合丙烯。
进一步地,可将新鲜乙烯引入第二反应区。同样,新鲜乙烯是指未再循环的乙烯并且不指已经经由第一产物流从第一反应阶段转移的或经由第一再循环物流再循环到第二反应阶段的未反应的乙烯。
此外,可将新鲜氢气引入第二反应阶段以控制第二丙烯共聚物的分子量。因此,新鲜氢气涉及未再循环的氢气并且不指已经经由第一产物流中从第一反应阶段转移的或可以经由第一再循环物流再循环到第二反应阶段中的氢气。
尽管将氢气引入第一和第二反应阶段分别是任选的,但优选将氢气引入所述反应阶段中的至少一个。
由于含有分散在其中的活性聚合催化剂的第一丙烯共聚物的颗粒从第一反应阶段被送至第二反应阶段,因此不需要将额外的催化剂引入第二反应阶段。
在第二反应阶段,产生包含第一丙烯共聚物和第二丙烯共聚物的丙烯聚合物混合物的第二反应混合物。丙烯聚合物混合物可以包含10重量%至90重量%的第一丙烯共聚物和90重量%至10重量%的第二丙烯共聚物,优选30重量%至70重量%的第一丙烯共聚物和70重量%至30重量%的第二丙烯共聚物,更优选地35重量%至65重量%的第一丙烯共聚物和65重量%至35重量%的第二丙烯共聚物,甚至更优选地35重量%至50重量%的第一丙烯共聚物,和65重量%至50重量%的第二丙烯共聚物。由于丙烯单体和乙烯共聚单体在第二反应阶段的聚合过程中通常也不会完全消耗,因此第二反应混合物包含未反应的丙烯、未反应的乙烯和氢气(如果存在)。
优选地,第二反应阶段包括至少一个气相反应器。因此,第二反应阶段可以包括两个或更多个串联连接的气相反应器。
至少一个气相反应器可以适当地为流化床反应器。这种反应器在本领域中是众所周知的。
在流化床气相反应器中,烯烃(这里是丙烯和乙烯)在聚合催化剂的存在下在向上移动的气流中聚合。反应器通常包含流化床,该流化床包含含有活性催化剂的生长的聚合物颗粒,所述流化床的基底位于流化格栅上方,上层在气相反应器内。
聚合物床在包含烯烃单体(这里为丙烯)、一种或多种任选的共聚单体、任选的链增长控制剂或链转移剂(如氢气)和任选的惰性气体的流化气体的帮助下流化。流化气体被引入在反应器底部的入口室。为了确保气流均匀地分布在入口室的横截面区域上,入口管可以配备本领域已知的分流元件,例如US-A-4933149和EP-A-684871。通常将一种或多种上述组分连续添加到流化气体中以补偿尤其是由反应或产物取出引起的损失。
气流从入口室向上通过流化格栅进入流化床。流化格栅的目的是将气流均匀地分流通过床的横截面积。有时可以设置流化格栅以建立沿反应器壁吹扫的气流,如WO-A-2005/087361中所公开。尤其是在US-A-4578879、EP600414和EP-A-721798中公开了其他类型的流化格栅。在Geldart和Bayens:The Design of Distributors for Gas-fluidized Beds,Powder Technology,第42卷,1985年中进行了概述。
流化气体通过流化床。流化气体的表观速度必须高于流化床中所含颗粒的最小流化速度,否则将不会发生流化。另一方面,气体的速度应低于输送速度,否则整个床将被流化气体夹带。然后床层空隙率通常小于0.8,优选小于0.75,更优选小于0.7。通常,床层空隙率至少为0.6。尤其是在Geldart:Gas Fluidization Technology,J.Wiley&Sons,1986年中的第2.4和2.5章(第17-18页)以及第7.3到7.5章(第169-186页,尤其是第183页的图7.21)中给出了概述。
当流化气体与含有活性催化剂的床接触时,气体的反应组分(比如单体和链转移剂)在催化剂存在下反应以产生聚合物产物。同时气体被反应热加热。
未反应的流化气体从反应器顶部除去并在热交换器中冷却以除去反应热。将气体冷却至低于床温度的温度,以防止床因反应而发热。可以将气体冷却到其中一部分冷凝的温度。当液滴进入反应区时,它们被蒸发。然后蒸发热有助于除去反应热。这种操作称为冷凝模式,其变体在尤其是WO-A-2007/025640、US-A-4543399、EP-A-699213和WO-A-94/25495中公开。如EP-A-696293中所公开的,还可以将冷凝剂添加到再循环气流中。冷凝剂是不可聚合的组分,比如正戊烷、异戊烷、正丁烷或异丁烷,它们在冷却器中至少部分冷凝。
然后将气体压缩并再循环到反应器的入口室中。在进入反应器之前,可以将新鲜反应物引入流化气流中以补偿由反应和产物取出引起的损失。通常已知分析流化气体的组成并引入气体组分以保持组成恒定。实际组成由所期望的产物性质和聚合中使用的催化剂决定。
气相反应器的顶部可以包括所谓的分离区。在这样的区域中,反应器的直径增加以降低气体速度并允许随流化气体从床中携带的颗粒沉降回到床中。
可以通过本领域已知的不同技术来观察床水平,即上层。例如,可以在反应器的整个长度上记录反应器底部和床的特定高度之间的压差,并且可以基于压差值计算床水平。这样的计算产生了时间平均水平。也可以使用超声波传感器或放射性传感器。使用这些方法可以获得瞬时水平,然后当然可以随时间进行平均以获得时间平均的床水平。
如果需要,也可以将一种或多种抗静电剂引入气相反应器。合适的抗静电剂和使用它们的方法尤其在US-A-5026795、US-A-4803251、US-A-4532311、US-A-4855370和EP-A-560035中公开。它们通常是极性化合物,尤其包括水、酮、醛和醇。
反应器还可以包括机械搅拌器以进一步促进流化床内的混合。EP-A-707513中给出了合适的搅拌器设计的实例。
流化床气相反应器在65℃至100℃,优选65℃至85℃范围内的温度下操作。压力合适地为10巴至100巴,优选15巴至30巴。
回收
在本发明方法的步骤f)中,从第二反应阶段取出包含第二反应混合物的第二产物流并且将其至少一部分送至分离单元。
第二产物流可以连续或间歇地从第二反应区取出。也可以使用这些方法的组合。尤其是在WO-A-00/29452中公开了连续取出。尤其是在US-A-4621952、EP-A-188125、EP-A-250169和EP-A-579426中公开了间歇性取出。
在分离单元中,包含第二反应混合物的第二产物流被分离成第一塔顶物流和第一塔底产物流。第一塔顶物流包含未反应的丙烯、未反应的乙烯、低聚物以及氢气和助催化剂,如果分别存在的话。第一塔底产物流包含丙烯聚合物混合物的固体颗粒,即第一丙烯共聚物和第二丙烯共聚物的固体颗粒。
优选地,通过降低第二产物流的压力来进行分离。因此,分离单元优选为罐,在该罐中聚合物粉末从底部取出而气体从顶部排出。
在本发明方法的步骤g)中,从前面的分离步骤的第一塔底产物流中回收所期望的丙烯聚合物混合物。
丙烯聚合物混合物的回收可以包括清洗步骤、汽提步骤、萃取步骤等。也可以是不同步骤的组合。例如,丙烯聚合物混合物可以在90℃至110℃的温度下与蒸汽接触10分钟至3小时。此后,粉末可以用惰性气体比如氮气在20℃至80℃的温度下吹扫1至60分钟。或者,丙烯聚合物混合物可以用惰性气体比如氮气在50℃至90℃的温度下吹扫20分钟至5小时。
吹扫步骤优选在沉降的移动床中连续进行。聚合物以活塞流的形式向下移动,而被引入床底部的吹扫气体向上流动。
从聚合物中除去烃的合适方法在WO-A-02/088194、EP-A-683176、EP-A-372239、EP-A-47077和GB-A-1272778中公开。
在回收丙烯聚合物混合物之后,优选将其与如本领域公知的添加剂混合。此类添加剂包括抗氧化剂、加工稳定剂、中和剂、润滑剂、成核剂、颜料等。此后,可以如本领域已知的,将其挤出成粒料。优选地,同向旋转双螺杆挤出机用于挤出步骤。此类挤出机例如由Coperion(Werner&Pfleiderer)和Japan Steel Works制造。
在本发明方法的步骤h)中,来自分离单元的气态第一塔顶物流的至少一部分在送至蒸馏塔之前被冷凝。换言之,优选将至少一部分第一塔顶物流以液体形式引入蒸馏塔。冷凝可以通过本领域已知的方法进行,例如通过冷却和/或压缩。
在冷凝至少一部分第一塔顶物流之后,在随后的步骤i)中,将其至少一部分送入蒸馏塔。在那里,至少一部分冷凝的第一塔顶物流被分离成第二塔顶物流和第二塔底产物流。第二塔顶物流包含未反应的丙烯(其应当被回收),和未反应的乙烯以及氢气,如果存在的话。第二塔底产物流包含低聚物和助催化剂,它们可以表示为“重质物质”。由于“重质物质”从第一塔顶物流中除去,因此蒸馏塔也可称为“重物塔(heavies column)”。或者,它也可以表示为“丙烯蒸馏塔”。
通常,蒸馏塔具有6至15块塔板,例如10块塔板。操作压力通常为17至21巴(g),然后塔顶温度通常为48℃至50℃(在一定程度上取决于压力),塔底温度为50℃至55℃。正如本领域众所周知的,可以分析进料到蒸馏塔的物流(这里是冷凝的第一塔顶物流)、第二塔顶物流和第二塔底产物流的组成,以相应控制蒸馏塔。因此,可以调节第二塔顶物流经受的冷却速率和经由再沸器提供的加热速率以达到所期望的第二塔顶物流组成。
在蒸馏塔中,重组分与未反应的丙烯单体分离。因此,在本发明方法的步骤j)中,未反应的丙烯与其他轻组分比如未反应的乙烯和氢气(如果存在)一起作为第二塔顶物流从蒸馏塔的顶部取出,而重杂质,比如低聚物、助催化剂和丙烷,连同一些伴随的丙烯作为第二塔底产物流从蒸馏塔底部取出。
在方法步骤k)中,第二塔顶物流在其从蒸馏塔中取出后至少部分冷凝,从而产生冷凝的第二塔顶物流和任选的汽相第二塔顶物流。
通常,取出的第二塔顶物流的冷凝是通过将其以汽相送入热交换器并将其冷却以使至少一部分第二塔顶物流冷凝来进行的。然后将至少部分冷凝的第二塔顶物流适当地送入容器。从所述容器中取出液体流,即冷凝的第二塔顶物流和任选的汽相第二塔顶物流。汽相第二塔顶物流可以送至精炼厂或燃烧。
在本发明方法的步骤l)中,液体流,即冷凝的第二塔顶物流,被分成三股单独的物流。所述分流中的一股,蒸馏回流物流,作为回流物流返回到蒸馏塔中,优选返回到蒸馏塔的顶部。另一股分流,第一再循环物流,被送到第二反应阶段,而另一股分流,第二再循环流,被送到汽提塔以去除轻杂质。
已经发现,经由第一再循环物流再循环到第二反应阶段的未反应的丙烯单体的量以及从第一反应阶段转移的未反应的丙烯单体的量可能足以在第二反应阶段继续进行聚合,即用于生产第二丙烯共聚物。结果,不需要将新鲜丙烯引入第二反应阶段,从而不需要用于第二反应阶段的额外的丙烯进料容器。因此,降低了该方法的操作成本。
因此,在本发明方法中优选将丙烯从单个丙烯进料容器进料至预聚合阶段和/或第一反应阶段。如果需要将额外的丙烯引入第二反应阶段,也可以从所述单个丙烯进料容器进料。
第二再循环物流被送至汽提塔。汽提塔是具有大约6至12块塔板,比如8块塔板的蒸馏塔。操作汽提塔,使得其塔顶物流(第三塔顶物流)包含大部分未反应的乙烯和氢气(如果存在),与第二再循环流一起供应,而塔底产物流(第三塔底产物流)包含未反应的丙烯以及含量降低的乙烯和氢。
在本发明方法的最后步骤m)中,第三塔顶物流从汽提塔取出并送至蒸馏塔。合适地,第三塔顶物流在第一塔顶物流进入塔的同一塔板上或附近返回蒸馏塔。适当地控制第三塔顶物流的质量流率以在第三塔底产物流中获得所期望的未反应的丙烯含量。
进一步地,第三塔底产物流也从汽提塔中取出并且其至少一部分被适当地送至丙烯进料容器,从那里取出送至预聚合阶段和第一反应阶段(和任选地第二反应阶段)的丙烯进料物流。此外,或者,至少一部分第三塔底物流可以分别作为进料直接送至预聚合阶段和/或第一反应阶段。
优选地,在本发明的方法中,第一再循环物流与蒸馏回流物流的比率(质量/质量)为1:5至2:1。同样,第一再循环物流与第二再循环物流的比率(质量/质量)优选为1:5至3:2。
本发明的方法可以优选地包括进一步的步骤h’),其在步骤h)之后且在步骤i)之前进行。在步骤h’)中,第一塔顶物流不直接送入蒸馏塔(“丙烯蒸馏塔”),而是送入乙烯蒸馏塔,在那里它被分离成乙烯塔塔顶物流和乙烯塔塔底产物流。乙烯塔塔顶物流主要包含轻组分,比如未反应的乙烯和氢气,如果存在的话。因此,乙烯塔塔底产物流包含未反应的丙烯、含量降低的未反应的乙烯和氢气(如果存在)以及低聚物和助催化剂。
在该实施方案中,然后将乙烯塔塔底产物流作为第一塔顶物流的一部分送至蒸馏塔,在蒸馏塔中乙烯塔塔底产物流在随后的步骤i)中被分离为第二塔顶物流和第二塔底产物流。
第二反应阶段可以包括两个串联连接的气相反应器。在该实施方案中,第一产物流从第一反应阶段取出并被送入第一气相反应器,在第一气相反应器中如上所述继续进行聚合。包含来自第一气相反应器的反应混合物的产物流可以被直接或间接地送入第二气相反应器。当直接送入时,所述产物流在没有任何纯化步骤的情况下被导入第二气相反应器。当间接送入时,所述产物流在被导入第二气相反应器之前进行纯化步骤。该纯化步骤可以包括将所述产物流导入气/固分离单元,比如闪蒸罐,在那里固体丙烯聚合物混合物作为塔底产物被回收并送入第二气相反应器。在被再循环至第一气相反应器或第二气相反应器之前,包含未反应的丙烯和未反应的乙烯的排气可以通过使用膜单元或汽提塔完全或部分不含氢气和/或轻质惰性烃杂质。特别地,如EP2330135A1中所公开的,可以将来自第一气相反应器的产物流取出并送入第二气相反应器。如上所述聚合在第二气相反应器中继续进行,然后可以使在第二气相反应器中获得的反应混合物经历与上文详细描述的相同的回收过程。然后可以将第一再循环物流送入第一气相反应器或第二气相反应器或两个气相反应器。
聚合单元
在另一方面,本发明涉及聚合单元,其特别适合于进行本发明的方法。
在图1中,显示了根据本发明的用于生产丙烯共聚物的聚合单元。根据本发明的聚合单元包括丙烯进料容器(100)和串联连接的预聚合阶段(10)、第一反应阶段(20)和第二反应阶段(30),以及回收系统。
回收系统包括:
i)与第二反应阶段(30)连接的分离单元(40);
ii)与分离单元(40)连接的第一冷凝器(50);
iii)与第一冷凝器(50)连接的蒸馏塔(70);
iv)与蒸馏塔(70)连接的第二冷凝器(80);和
v)汽提塔(90);
vi)连接第二冷凝器(80)与蒸馏塔(70)的蒸馏回流管线(81);
vii)连接第二冷凝器(80)与第二反应阶段(30)的第一再循环管线(82);
viii)连接第二冷凝器(80)和汽提塔(90)的第二再循环管线(83);
ix)连接汽提塔(90)和蒸馏塔(70)的第三再循环管线(91);和
x)连接汽提塔(90)与丙烯进料容器(100)、预聚合阶段(10)和/或第一反应阶段(20)的第四再循环管线(92)。
由于本发明的聚合单元特别适合于进行本发明的方法,因此上文针对本发明方法概述的考虑和限制在经过必要修改之后适用于本发明的聚合单元。
第一反应阶段(20)优选包括至少一个淤浆反应器,进一步优选至少一个环管反应器。此外,优选第二反应阶段(30)包括至少一个气相反应器。
此外,优选预聚合阶段(10)包括淤浆反应器,进一步优选环管反应器。
此外,优选回收系统的分离单元(40)是用于固/气分离的罐。分离单元(40)连接至第二反应阶段(30)。在一个实施方案中,其中第二反应阶段(30)包括一个气相反应器,分离单元(40)连接至一个气相反应器。在另一个实施方案中,第二反应阶段(30)包括两个串联连接的气相反应器。在这种情况下,分离单元(40)然后可以连接至最后的气相反应器。或者,它可以连接至两个气相反应器。
进一步地,回收系统包括与分离单元(40)连接的第一冷凝器(50)。优选地,第一冷凝器(50)与分离单元(40)的顶部连接。第一冷凝器(50)可以包括冷却容器、热交换器、压缩机和/或用于冷凝的另外的常规装置。
回收系统的蒸馏塔(70)与第一冷凝器(50)连接并代表如上定义的“重质塔”或“丙烯蒸馏塔”。优选地,蒸馏塔(70)与第一冷凝器(50)的底部连接。
回收系统的第二冷凝器(80)与蒸馏塔(70)连接并且还可以包括冷却容器、热交换器、压缩机和/或用于冷凝的另外的常规装置。优选地,第二冷凝器(80)与蒸馏塔(70)的顶部连接。
回收系统进一步包括汽提塔(90),连接第二冷凝器(80)和蒸馏塔(70)的蒸馏回流管线(81);连接第二冷凝器(80)和第二反应阶段(30)的第一再循环管线(82);以及连接第二冷凝器(80)和汽提塔(90)的第二再循环管线(83)。
优选地,回收系统进一步包括用于控制通过蒸馏回流管线(81)、第一再循环管线(82)和/或第二再循环管线(83)的质量流量的控制装置。这种控制装置通常包括用于测量质量流量的流量计,比如质量流量计;控制器,其接收来自流量计的信号并将该信号与设定点值进行比较,如果存在偏差,则向控制阀发送信号;以及控制阀,其接收来自控制器的信号并根据该信号打开或关闭。控制器可以独立地接收它们的设定点,但它们也可以从更高级别的控制器接收设定点。然后可以将设定点例如相对于彼此设置为特定比率。正如本领域众所周知的,这种更高级别的控制器可以优化该方法,例如,用于实现所期望的物流纯度。
蒸馏回流管线(81)将第二冷凝器(80)与蒸馏塔(70)连接。优选地,蒸馏回流管线(81)将第二冷凝器(80)的底部与蒸馏塔(70)的顶部连接。
第一再循环管线(82)将第二冷凝器(80)与第二反应阶段(30)连接。在第二反应阶段(30)包括两个串联连接的气相反应器的情况下,第一再循环管线(82)将第二冷凝器(80)与第一气相反应器或与第二气相反应器或两个气相反应器连接。优选地,第一再循环管线(82)将第二冷凝器(80)的底部与第二反应阶段(30)连接。
在本发明的聚合单元中,第一再循环管线(82)满足用于第二反应阶段的丙烯进料容器的功能。换言之,聚合单元不需要用于第二反应阶段的任何丙烯进料容器。因此,聚合单元的安装成本以及操作成本显著降低。
优选地,第一再循环管线(82)包括流量控制回路和防回流系统。因此,可以控制通过第一再循环管线(82)到第二反应阶段(30)的流体并且可以避免从第二反应阶段(30)到回收系统的回流。
第二再循环管线(83)将第二冷凝器(80)与汽提塔(90)连接。优选地,第二再循环管线(83)将第二冷凝器(80)的底部与汽提塔(90)连接。
聚合单元进一步包括连接汽提塔(90)(的顶部)与蒸馏塔(70)的第三再循环管线(91);以及连接汽提塔(92)(的底部)与丙烯进料容器(100)、预聚合阶段(10)和/或第一反应阶段(20)的第四再循环管线(92)。优选地,第三再循环管线(91)将汽提塔(90)的顶部与蒸馏塔(70)连接,并且第四再循环管线(92)将汽提塔(90)的底部与丙烯进料容器(100)、预聚合阶段(10)和/或第一反应阶段(20)连接。
优选地,如图2所示,回收系统进一步包括介于第一冷凝器(50)和蒸馏塔(70)之间的乙烯蒸馏塔(60)。在该实施方案中,乙烯蒸馏塔(60)与第一冷凝器(50)连接,优选与第一冷凝器(50)的底部连接,而不是与蒸馏塔连接。因此,蒸馏塔(70)然后与乙烯蒸馏塔(60)连接,优选与乙烯蒸馏塔(60)的底部连接。
发明益处
本发明特别适用于以多阶段方法生产具有高乙烯含量的丙烯-乙烯无规共聚物。在用于生产此类丙烯共聚物的常规方法中,由于存在过高浓度的与丙烯混合的未反应的乙烯共聚单体,未反应的丙烯单体的有效、经济的回收常常被阻碍。具体而言,来自常规回收系统的“重质塔”或“丙烯蒸馏塔”的塔顶物流(包含未反应的丙烯、未反应的乙烯和任选的氢气)通常被冷凝并作为一个整体送入汽提塔,在汽提塔中轻组分,比如氢和乙烯,应至少部分被去除。然后将剩余物,即包含未反应的丙烯的塔底产物流再循环至丙烯进料容器或反应阶段。然而,在高浓度乙烯共聚单体的情况下,汽提塔上的负载太高,导致在塔底产物流中未反应的乙烯共聚单体浓度太高。这可能会导致操作问题,使得需要将新鲜丙烯进料到预聚合反应器中,从而降低了工艺经济性,或者需要用于去除乙烯的额外的工艺步骤,从而增加了操作成本。
然而,在本发明中,通过将来自“重质塔”或“丙烯蒸馏塔”的塔顶物流分成三股单独的物流来减少汽提塔的进料,其中三股物流中仅有一股仍然送至汽提塔。因此,在汽提塔中乙烯从未反应的丙烯中的分离更有效,并且降低了塔底产物流中的乙烯含量。当来自汽提塔的塔底产物流或其至少一部分随后被送入丙烯进料罐并从那里送入预聚合进料时,与常规回收装置相比,聚合进料的乙烯含量降低。然后,不需要用于去除乙烯的额外的工艺步骤,这种额外的工艺步骤可能是能量密集型的,因此是不经济的,或者不需要将不必要的大量新鲜丙烯进料到反应器中。此外,由于三股物流中的一股被再循环到最后的反应阶段,而三股物流中的另一股被再循环回蒸馏塔,因此不需要将未反应的丙烯送去处理。因此,在不影响工艺稳定性的情况下,提高了未反应的丙烯单体的回收效率。此外,已经发现由于将三股分流中的一股再循环到最后的反应阶段,因此不需要向最后的反应阶段中引入新鲜丙烯以继续进行聚合。结果,不需要用于所述反应阶段的额外的丙烯进料容器。因此,甚至可以降低该方法的操作成本和各个聚合单元的安装成本。
参考符号表
10 预聚合阶段
20 第一反应阶段
30 第二反应阶段
40 分离单元
50 第一冷凝器
60 乙烯蒸馏塔
70 蒸馏塔
80 第二凝器
81 蒸馏回流管线
82 第一再循环管线
83 第二再循环管线
90 汽提塔
91 第三再循环管线
92 第四再循环管线
100 丙烯进料容器
[实施例]
在所有实施例和比较例中,丙烯和乙烯共聚。催化剂、助催化剂和外部电子供体首先与来自丙烯进料容器的丙烯一起进料到预聚合反应器中(预聚合阶段)。来自预聚合反应器的浆料与来自丙烯进料容器的额外的丙烯一起被送入环管反应器,在环管反应器中生产丙烯与乙烯的共聚物(第一反应阶段)。此外,乙烯和氢气被进料到环管反应器中。在没有将流体组分与聚合物分离的情况下,将来自环管反应器的浆料(第一产物流)送入气相反应器,并且丙烯和乙烯在气相反应器中进一步共聚(第二反应阶段)。额外的丙烯(即再循环的丙烯)、乙烯和氢气被进料到气相反应器中。
从气相反应器中取出聚合物-气体混合物(第二产物流)并将聚合物(第一塔底产物)与气体分离。将气体(第一塔顶物流)送入冷凝器,从那里将冷凝的气流送入具有11块塔板的蒸馏塔(“丙烯塔”)的顶部塔板,进行操作使得塔顶温度为48℃至50℃,塔底温度为50℃至55℃。压力为17巴g至21巴g。取出所得的塔底物流(第二塔底产物流)并将其送至低聚物处理处。所得塔顶物流(第二塔顶物流)在冷凝器中部分冷凝。未冷凝馏分的主要部分(汽相第二塔顶物流)返回气相反应器,而一小部分则送至燃烧。冷凝的馏分(冷凝的第二塔顶物流)被分成三股物流:一股物流返回到丙烯塔的顶部塔板(蒸馏回流物流),一股物流被直接送入气相反应器(第一再循环物流)(仅在实施例1-3中,但不在比较例中),并且一股物流(第二再循环物流)被送至汽提塔的底部塔板。汽提塔是一个具有10块塔板的蒸馏塔。操作使得顶部温度为57℃至60℃,底部温度为59℃至61℃。压力为17巴g至24巴g。
来自汽提塔的塔顶物流(第三塔顶物流)返回到丙烯塔的顶部,塔底物流(第三塔底产物流)被分成三股物流:第一部分被送至气相反应器的出口容器以增强聚合物的脱气;第二部分被送入丙烯进料容器;第三部分被送至裂化器。
除非另有说明,否则实施例中给出的气体组成的百分比数均为摩尔%。
比较例1
从聚合物脱气中回收的气流(第一塔顶物流)的组成包含6.6%的氢气、1.5%的乙烯、0.2%的乙烷、69.2%的丙烯、21.6%的丙烷、0.6%或更高的丁烷和0.2%的氮气。混合物向丙烯塔的进料速率为6800kg/h。馏出物流(第二塔顶物流)被部分冷凝。从冷凝器取出的蒸气流(汽相第二塔顶物流)为300kg/h。从冷凝的第二塔顶物流中,6900kg/h返回到丙烯塔(蒸馏回流物流),7500kg/h转移到汽提塔(再循环物流)。
从汽提塔中回收1100kg/h作为塔顶物流(第三塔顶物流)和6400kg/h作为塔底物流(第三塔底产物流)。塔底物流含有0.5%的乙烯、73%的丙烯和26%的丙烷。一部分塔底物流被送入丙烯进料容器,一部分用于气相反应器下游的聚合物脱气,一小部分返回裂解器。
操作回收系统的总相对小时成本为100。
实施例1
该过程如对比例1进行操作,不同之处在于从冷凝器底部回收的物流(总质量流率为7500kg/h的再循环物流)被分成两部分,其中3000kg/h被送入气相反应器(第一再循环物流)和4500kg/h被送入汽提塔(第二再循环物流)。操作该过程使得从汽提塔作为塔底物流回收的物流(第三塔底产物流)具有与比较例1相同的组成。气相反应器运行平稳,产品质量控制没有问题。
操作回收系统的总相对小时成本为83。
比较例2
从聚合物脱气中回收的气流(第一塔顶物流)的组成包含0.3%的氢气、2.3%的乙烯、0.1%的乙烷、89.2%的丙烯、7.7%的丙烷、0.1%或更高的丁烷和0.2%的氮气。混合物向丙烯塔的进料速率为7400kg/h。馏出物流(第二塔顶物流)被部分冷凝。从冷凝器取出的蒸气流(汽相第二塔顶物流)为470kg/h。从冷凝的第二塔顶物流中,3200kg/h返回丙烯塔(蒸馏回流物流),8500kg/h转移到汽提塔(再循环物流)。
从汽提塔中回收1100kg/h作为塔顶物流(第三塔顶物流)和7400kg/h作为塔底物流(第三塔底产物流)。塔底物流含有1%的乙烯、90%的丙烯和9%的丙烷。一部分塔底物流被送入丙烯进料罐,一部分用于气相反应器下游的聚合物脱气,一小部分返回裂解器。
操作回收系统的总相对小时成本为100。
实施例2
该过程如对比例2进行操作,不同之处在于从冷凝器底部回收的物流(总质量流率为8500kg/h的再循环物流)被分成两部分,其中3000kg/h被送入气相反应器(第一再循环物流)和5500kg/h被送入汽提塔(第二再循环物流)。操作该过程使得从汽提塔作为塔底物流回收的物流(第三塔底产物流)具有与比较例2相同的组成。气相反应器运行平稳,产品质量控制没有问题。
操作回收系统的总相对小时成本为80。
比较例3
从聚合物脱气中回收的气流(第一塔顶物流)的组成包含0.4%的氢气、2.3%的乙烯、0.1%的乙烷、86.8%的丙烯、10%的丙烷、0.1%或更高的丁烷和0.2%的氮气。混合物向丙烯塔的进料速率为7900kg/h。馏出物流(第二塔顶物流)被部分冷凝。从冷凝器取出的蒸气流(汽相第二塔顶物流)为340kg/h。从冷凝的第二塔顶物流中,3300kg/h返回丙烯塔(蒸馏回流物流),9000kg/h转移到汽提塔(再循环物流)。
从汽提塔中回收1100kg/h作为塔顶物流(第三塔顶物流)和7900kg/h作为塔底物流(第三塔底产物流)。塔底物流含有1%的乙烯、88%的丙烯和11%的丙烷。一部分塔底物流被送入丙烯进料罐,一部分用于气相反应器下游的聚合物脱气,一小部分返回裂解器。
操作回收系统的总相对小时成本为95。
实施例3
该过程如对比例3进行操作,不同之处在于从冷凝器底部回收的物流(总质量流率为9000kg/h的再循环物流)被分成两部分,其中3000kg/h被送入气相反应器(第一再循环物流)和6000kg/h被送入汽提塔(第二再循环物流)。操作该过程使得从汽提塔作为塔底物流回收的物流(第三塔底产物流)具有与比较例3相同的组成。在这种情况下,气相反应器的运行也很平稳,产品质量的控制也没有问题。
操作回收系统的总相对小时成本为78。