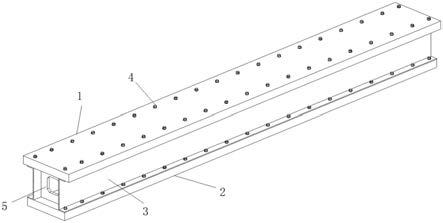
1.本实用新型涉及现代木结构与钢材组合桥梁,尤其涉及一种木-钢组合箱梁。
背景技术:
2.木结构具有集实用性与艺术性于一身的特点,是古代建筑结构与艺术的结晶。木材是一种各向异性材料,木材纹路对其力学性能具有较大的影响。木材顺纹方向的抗拉压强度远远大于其横纹方向的抗拉强度,同时木材顺纹及横纹方向的抗剪强度均较低,一般工程中的木梁多为受剪破坏,且多为脆性破坏。而现代胶合木结构很大程度上弥补了传统原木结构在承载能力和使用功能方面的缺陷,随着国家倡导社会经济发展与自然环境保护相协调,使得胶合木结构桥梁与建筑具有较大的研究与推广应用价值。
技术实现要素:
3.本实用新型要解决的技术问题是克服现有技术的不足,提供一种结构简单,抗弯、抗剪、抗扭性能好,稳定性高的木钢组合箱梁。
4.为解决上述技术问题,本实用新型采用以下技术方案:
5.一种木-钢组合箱梁,包括平行布置的胶合木顶板及胶合木底板,所述胶合木顶板与胶合木底板之间设有两块钢腹板,所述钢腹板上侧与所述胶合木顶板通过紧固件相连,所述钢腹板下侧与胶合木底板通过紧固件相连。
6.作为上述技术方案的进一步改进:
7.两块所述钢腹板之间设有多块钢隔板,多块所述钢隔板沿所述钢腹板的长度方向间隔布置。
8.所述钢隔板与所述钢腹板焊接连接。
9.所述钢隔板中部设有方形缺口部,所述方形缺口部相邻的两条边之间设有倒角。
10.所述钢腹板为槽形钢腹板,两所述钢腹板的槽口相背布置。
11.所述钢腹板包括立板以及两块水平板,其中一块所述水平板与所述立板的上侧采用单边v型坡口焊缝焊接,另一块所述水平板与所述立板的下侧采用单边v型坡口焊缝焊接,上侧的所述水平板与所述胶合木顶板连接,下侧的所述水平板与所述胶合木底板连接。
12.两块所述钢腹板对称布置于所述胶合木底板的左右两侧,所述胶合木顶板的左右两侧对称延伸至所述钢腹板外。
13.所述胶合木顶板及所述胶合木底板均为正交胶合木双向板。
14.与现有技术相比,本实用新型的优点在于:本实用新型公开的木-钢组合箱梁,包括平行布置的胶合木顶板及胶合木底板,胶合木顶板与胶合木底板之间设有两块钢腹板,钢腹板上侧与胶合木顶板通过紧固件相连,钢腹板下侧与胶合木底板通过紧固件相连,形成一个箱形闭口截面梁,抗扭能力大大提高,且钢材抗剪强度高,相比纯胶合木梁,木-钢组合梁抗弯、抗剪、抗扭能力显著提高,充分发挥了两种材料的性能,结构简单,在景区人行桥与景观建筑等实际工程中具有较大的应用价值。
附图说明
15.图1是本实用新型木-钢箱梁的立体结构示意图。
16.图2是本实用新型木-钢箱梁的主视图。
17.图3是本实用新型木-钢箱梁的主视图中a-a剖面图。
18.图4是本实用新型木-钢箱梁的主视图中b-b剖面图。
19.图5是本实用新型木-钢箱梁的主视图中c-c剖面图。
20.图6是本实用新型中钢腹板的结构示意图。
21.图7是本实用新型中钢隔板的结构示意图。
22.图中各标号表示:1、胶合木顶板;2、胶合木底板;3、钢腹板;31、立板;32、水平板;4、紧固件;5、钢隔板;51、方形缺口部;6、单边v型坡口焊缝。
具体实施方式
23.以下结合说明书附图和具体实施例对本实用新型作进一步详细说明。显然地,所描述的实施例仅仅是本实用新型一部分实施例,而不是全部的实施例。基于本实用新型中的实施例,本领域普通技术人员在没有做出创造性劳动前提下所获得的所有其他实施例,都属于本实用新型保护的范围。
24.如图1至图7所示,本实施例的木-钢组合箱梁,包括平行布置的胶合木顶板1及胶合木底板2,胶合木顶板1与胶合木底板2之间设有两块钢腹板3,钢腹板3上侧与胶合木顶板1通过紧固件4相连,钢腹板3下侧与胶合木底板2通过紧固件4相连。
25.该木-钢组合箱梁,包括平行布置的胶合木顶板1及胶合木底板2,胶合木顶板1与胶合木底板2之间设有两块钢腹板3,钢腹板3上侧与胶合木顶板1通过紧固件4相连,钢腹板3下侧与胶合木底板2通过紧固件4相连,形成一个箱形闭口截面梁,抗扭能力大大提高,且钢材抗剪强度高,相比纯胶合木梁,木-钢组合梁抗弯、抗剪、抗扭能力显著提高,充分发挥了两种材料的性能,结构简单,在景区人行桥与景观建筑等实际工程中具有较大的应用价值,适用于跨径10m-20m,高跨比为1/9-1/15的人行简支桥梁。优选的,紧固件4可以为螺栓等。
26.本实施例中,两块钢腹板3之间设有多块钢隔板5,多块钢隔板5沿钢腹板3的长度方向间隔布置。设置多块钢隔板5有利于进一步提高木-钢组合箱梁的抗弯、抗剪、抗扭能力。
27.本实施例中,钢隔板5与钢腹板3焊接连接,连接可靠,强度高。
28.本实施例中,钢隔板5中部设有方形缺口部51,方形缺口部51相邻的两条边之间设有倒角,可进一步提升木-钢组合梁的抗弯、抗剪、抗扭能力,同时减轻组合箱梁的自重。
29.本实施例中,钢腹板3为槽形钢腹板,两钢腹板3的槽口相背布置,便于通过紧固件4与胶合木顶板1及胶合木底板2相连。优选的,钢腹板3沿长度方向可适当设置横向加劲肋,稳定性更高。
30.本实施例中,钢腹板3包括立板31以及两块水平板32,其中一块水平板32与立板31的上侧采用单边v型坡口焊缝6焊接,另一块水平板32与立板31的下侧采用单边v型坡口焊缝6焊接,上侧的水平板32与胶合木顶板1连接,下侧的水平板32与胶合木底板2连接,结构简单,布置紧凑,采用单边v型坡口焊缝6能使连接部位焊透,提高焊缝强度。
31.本实施例中,两块钢腹板3对称布置于胶合木底板2的左右两侧,胶合木顶板1的左右两侧对称延伸至钢腹板3外,有利于进一步提升组合箱梁的力学性能,同时一定幅度上增加了箱梁的宽度,便于通行,实用性更强。
32.本实施例中,胶合木顶板1及胶合木底板2均为正交胶合木双向板,以承受纵、横双向弯曲及拉压。
33.该木-钢组合箱梁的构造如下:
34.如图2所示,简支木-钢组合箱梁桥跨长l一般为10m~20m,计算跨径l0,梁端距支座中心为l1(150mm~250mm),高跨比h/l取值1/9~1/15,胶合木顶板1(或称上翼缘板)宽度b=3m~4.5m,胶合木底板(或称下翼缘板)2宽度b=2.5m~4m,主梁上可铺设桥面铺装(图中未示出)。钢腹板3中心线间距b1为1.5m~3m,下翼缘悬臂宽b2一般取20cm,上翼缘悬臂宽b3取50cm~75cm。为增强钢腹板3的稳定性和梁的整体性,在两片钢腹板3之间设置钢隔板5(q345钢板),钢隔板5厚度取8mm~10mm,钢隔板5设有方形缺口部51(图7),方形缺口部51边长为钢隔板5边长的一半,并在拐角处设置45
°
倒角,倒角直角边长为d1(100mm~150mm),沿跨度方向等距离布置5道。按稳定计算要求,钢腹板3沿跨径方向可适当设置横向加劲肋。
35.胶合木顶板1及胶合木底板2(或称上、下翼缘板)采用正交胶合木双向板,厚度一般为200mm~250mm;钢腹板3厚度t为15mm~20mm。d为螺栓中心线与钢腹板3中心线的距离,需满足规范要求。纵向螺栓间距:一般采用等间距布置,跨中l3为450mm~500mm;梁端间距适当减小,l2取200mm~400mm;梁端第1个螺栓与梁端的距离l1一般取100mm~120mm。
36.该木-钢组合箱梁的制作工艺如下:
37.胶合木顶板1及胶合木底板2(或称上、下翼缘板)采用长度不小于1000mm、宽100mm~250mm、厚25mm~45mm的松木锯材,按正交方式形成正交胶合木(clt)双向板。具体做法为:胶合木顶板1与胶合木底板2均采用兴安落叶松为原材料,先将原木锯材通过刨光使表面光滑,采用新型水基聚氨酯结构胶,将主剂与交联剂按5:1进行充分混合,然后涂抹至木板胶合层表面,按正交方式将单层薄板沿宽度方向和厚度方向进行拼接胶合,使之成为clt整体板。胶合时,木板的接长沿宽度方向和厚度方向须将胶缝错开,然后进行固定加压使胶凝固,加压时间要求在24小时以上,以保证胶缝的强度。
38.钢腹板3采用焊接槽形钢(q345钢),角部连接采用单边v形坡口对接焊缝6,可使连接部位焊透以提高焊缝强度,如图6所示;钢腹板3与钢隔板5之间,采用焊接方式连接。
39.然后,按照图2中所示的螺栓布置位置进行开孔,先精确定位出螺孔位置,并在指定位置打孔,胶合木顶板1及胶合木底板2的孔径比螺栓直径大1mm以内,钢腹板3中的孔径比螺栓直径大1mm~2mm,在螺栓顶部和螺帽以下使用边长或直径最小等于3倍螺栓直径且厚度最小等于0.3倍螺栓直径的垫圈,然后将组合梁的钢腹板3与胶合木翼缘板接触的表面清洗擦拭干净与防腐处理,再将螺栓打入螺孔中进行安装(螺栓采用不小于8mm的普通六角头螺栓),螺栓安装完成后用重物压住一定时间,最终形成如图1所示的木-钢组合箱形梁。
40.虽然本实用新型已以较佳实施例揭露如上,然而并非用以限定本实用新型。任何熟悉本领域的技术人员,在不脱离本实用新型技术方案范围的情况下,都可利用上述揭示的技术内容对本实用新型技术方案做出许多可能的变动和修饰,或修改为等同变化的等效实施例。因此,凡是未脱离本实用新型技术方案的内容,依据本实用新型技术实质对以上实施例所做的任何简单修改、等同变化及修饰,均应落在本实用新型技术方案保护的范围内。