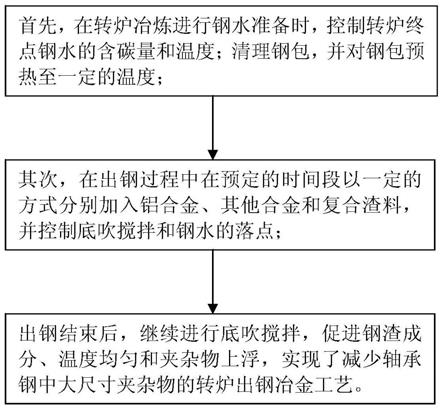
1.本发明涉及钢铁冶金生产领域,具体涉及到减少轴承钢中大尺寸夹杂物的转炉出钢冶金工艺。本发明特别适用于对大尺寸夹杂物有严格要求的高纯净度轴承钢冶炼工艺。
背景技术:
2.作为一种重要的冶金产品,轴承钢专门用于制造轴承套圈和滚动体,被广泛应用于机械制造、铁路运输、国防工业等领域,随着现代工业的发展,轴承的使用环境日趋恶劣,对轴承的疲劳寿命提出了更高更严的要求。夹杂物是影响轴承钢疲劳寿命的关键因素。近年来,随着冶金工艺技术的不断改进,国内轴承钢中的典型杂质元素氧、钛含量已能控制到极低水平,但大尺寸夹杂物的控制与国外先进水平相比仍有较大差距。这些大尺寸夹杂物数量少,出现的随机性强,但对轴承材料的使用寿命危害严重,已经成为制约轴承钢质量进一步提升的关键因素。
[0003]“转炉+lf精炼炉+rh/vd真空精炼炉+浇铸”是目前轴承钢主要生产工艺路线之一。其中,转炉出钢过程时间较短,通常只有2-6分钟,但是这个过程涉及到钢液脱氧、夹杂物生成、卷渣、降温、合金化等许多复杂环节,并且伴随着气体的搅拌和出钢钢液流对钢包钢液的冲击,各种现象混合在一起,容易导致大量大尺寸夹杂物的生成。部分大尺寸夹杂物即使经过lf和rh或者vd处理仍然会残留在钢中,从而影响钢材的质量。因此在转炉出钢过程,应尽量减少大尺寸夹杂物的生成,每一个工艺细节的精确控制非常重要,包括出钢前钢包和钢水的准备,出钢过程脱氧剂、合金和渣料的加入方式,底吹气体的控制等等,这不仅有效减少了大尺寸夹杂物的来源,同时减轻了后期精炼过程对夹杂物去除的负担,提高了精炼效率。
[0004]
为了提高轴承钢的纯净度,中国专利cn106591536a公开了《一种高纯净轴承钢的生产工艺》,该工艺电炉作为初炼炉,采用偏心炉底出钢可以有效控制下渣,电极加热可以准确控制温度,这是电炉相比转炉明显的两个优势,另外选择低钛预熔渣和石灰造渣,vd真空处理和保护浇铸等措施,有效地控制了合理的精炼渣系成分与夹杂物的上浮,但出钢合金化过程中将合金、铝饼和增碳剂混合,容易产生大尺寸夹杂物,给后期去除带来压力,最终导致容易在轴承钢中出现大尺寸夹杂物。中国专利cn110643786a《一种提高轴承钢纯净度的生产工艺》通过使用高铝精炼渣系、优化lf精炼过程吹气制度、vd后增加静置、球面水口保护浇铸等措施,有效地降低了轴承钢中氧含量,但缺少对初炼炉出钢的控制,而且缺少具体的造渣工艺,容易导致造渣的不稳定性,使得大尺寸夹杂物出现概率增加。
技术实现要素:
[0005]
针对目前轴承钢中大尺寸夹杂物控制不稳定的问题,本发明提出了一种减少轴承钢中大尺寸夹杂物的转炉出钢冶金工艺。转炉作为一种典型的初炼炉,其冶炼的主要任务为高效脱碳和脱磷,具有生产节奏快的特点,而且转炉冶炼的热量来源全部为化学热,温度控制难,转炉出钢采用出钢口出钢,容易下渣。因此,如何充分利用转炉出钢过程中的温度、
钢液流冲击产生的搅拌强度等来实现钢液脱氧、合金化、造渣等冶金效果,达到减少大尺寸夹杂物的目的是本发明的内容。通过严格控制出钢前钢水成分和温度、准备适合的钢包、出钢过程中合金和造渣剂的加入方式以及出钢后吹气制度和炉渣氧化性等关键的细节工艺参数,有效减少了大尺寸夹杂物的生成,探伤合格率和ds夹杂物评级的合格率都明显提高,为我国生产高洁净度轴承钢提供一种方法。
[0006]
为实现上述冶炼效果,本发明提出的一种减少轴承钢中大尺寸夹杂物的转炉出钢冶金工艺,采用如下技术方案:
[0007]
(1)出钢前钢液的准备。转炉作为轴承钢冶炼的初炼炉,其主要任务为脱磷、脱碳和升温。具体包括如下工序:将主要原料废钢和铁水装入转炉,通过加入渣料造渣、吹氧等方式对原料进行脱磷、脱碳和升温,在转炉冶炼结束时,控制终点c含量满足ω[c]0.1~0.4%,出钢温度满足1590~1650℃。准备出钢时,首先关闭位于出钢口的滑动挡板,倾斜转炉至一定的角度,使得炉渣层和出钢口之间充满足够的钢液,确保钢渣良好分离,避免转炉下渣,然后开启滑动挡板,开始出钢。
[0008]
(2)出钢前钢包的准备。生产高质量轴承钢时,要保证每次使用的钢包至少在其前两炉采用高碱度渣冶炼工艺,其中炉渣二元碱度(cao/sio2)不低于4.5。将钢包内衬清理干净,无明显的炉渣残留,可以清晰区分钢包砖轮廓;保证钢包温度达到1050℃以上。
[0009]
(3)出钢过程合金和渣料的加入方式。出钢量达到总出钢量的1/5时,加入铝合金进行脱氧,进一步达到1/3-1/2时加入其他合金,保证铝合金和其他合金要分开加入。合金加入完成后,在出钢量为总出钢量的1/2-3/4过程中,其他时间段不再加入其他辅料,首先加入合成渣料,然后加入石灰,在出钢量达到4/5之前完成全部渣料的加入,出钢时间范围为3-8分钟。其中铝合金选用纯铝锭或者铝铁合金,金属铝的加入量为0.8-1.7kg/吨钢。对铬铁、锰铁、硅铁等合金进行烘烤,保证加入钢包前的温度大于300℃,其他合金加入钢包前进行预加热升温,减少了大量合金加入钢水带来的温度损失,保证了后续炉渣较快熔化所需要的温度。
[0010]
采用添加合成渣料和石灰的复合造渣工艺,该工艺是指在转炉出钢过程中,选择合成渣料和石灰作为造渣剂进行造渣的工艺,需保证合成渣料中ω(cao)/ω(al2o3)的范围在0.9~2.0、ω(sio2)≤6%、ω(mgo)2~8%,保证石灰与合成渣料的质量比的范围在0.1~0.5,渣料加入顺序为先加入合成渣料再加入石灰,合成渣料和石灰的总的加入量为7.6-10kg/吨钢。出钢过程中,保证出钢的钢液流冲击位置位于钢包液面圆心附近,允许波动范围
±
2倍钢液流股直径,合金和渣料加入位置要保证落点位于转炉出钢钢液冲击钢包液面的活跃区,同时避免转炉出钢钢液直接冲击到合金或者渣料。
[0011]
(4)出钢过程底吹气体的控制。采用双透气砖进行底吹,吹气量根据出钢量进行调节,全程控制软吹状态,避免吹气量过大导致的钢液液面剧烈波动。其中两个透气砖位于距离钢包中心1/2-2/3钢包半径的范围,透气砖圆心与钢包底部圆心连线夹角范围为80
°‑
120
°
。利用双透气砖吹氩气进行钢液搅拌,每个透气砖的吹气流量保持一致,吹气流量范围控制在1.2-3.5nl/min/吨钢。出钢量达到总出钢量的1/5之前,即铝加入之前,控制较小的吹气流量采用新的双透气砖位置分布,配合底吹气体流量控制和出钢的钢液流冲击,得到更为合理的流场,减少了由于钢液面剧烈波动导致的卷渣类夹杂物生成。保证吹气流量1.2-2.0nl/min/吨钢;出钢量在总出钢量的1/5-1/2之间,即铝和其他合金加入过程,控制
适中的吹气流量,保证吹气流量2.0-2.7nl/min/吨钢;出钢量达到总出钢量的1/2以后,即渣料加入过程,控制较高的吹气流量,保证吹气流量2.7-3.5nl/min/吨钢,一直保持到出钢结束。
[0012]
(5)出钢结束后底吹气体和炉渣成分的控制。出钢结束前进行留钢操作,避免下渣,留钢量范围为7-11吨,总的下渣量控制在100kg以内;出钢结束后增大气体流量,促进炉渣熔化,吹气量范围控制在3.2-6nl/min/吨钢;出钢结束后,在钢包到达lf处理位之前,炉渣成分质量分数满足cao:52%-58%,al2o3:28%-35%,sio2:5%-8%,mgo:4%-8%,feo《1%。
[0013]
相比目前普遍采用的轴承钢冶炼工艺,本发明工艺的先进性体现为:
[0014]
(1)严格控制转炉出钢的碳含量和出钢温度以及钢包温度,保证了合理的钢液氧化程度、脱氧剂添加量、合金熔化时间、炉渣熔化温度,工艺稳定性强。
[0015]
(2)出钢前挡渣和出钢结束的留钢操作避免了下渣,钢包提前进行高碱度炉渣冶炼和钢包清理,最大化减少了残渣的影响。
[0016]
(3)精准控制出钢过程合金和渣料的加入时机、加入位置和加入量,对合金的成分和温度进行约束,减少出钢过程温降,促进炉渣熔化,降低了出钢过程中卷渣的可能性,并减少了后续精炼过程的操作,进一步减少大尺寸夹杂物的生成,水浸合格率较原来提高了13%。
[0017]
(4)出钢过程双透气砖软吹制度,对吹气位置和吹气流量进行精确控制,氩气使用量减少了15%以上,既保证了对钢液的有效搅拌,同时又避免了钢液表面剧烈波动导致的卷渣。
[0018]
(5)出钢结束继续吹气促进化渣和夹杂物上浮,严格控制lf进站前炉渣成分,有效控制了后续lf精炼过程中铝的过度烧损和补铝操作,减少了夹杂物的生成数量,尤其是氧化铝类高熔点夹杂物的数量,有效减少了水口结瘤,正常生产的连浇炉数可以稳定在8炉以上,稳定了后续精炼过程,提高了精炼效率。
[0019]
(6)本工艺很好地控制了大尺寸夹杂物的尺寸和数量,过程大尺寸夹杂物数量减少到原来的50%以下,总面积减少到原来的20%以内。
附图说明
[0020]
图1为本发明一种减少轴承钢中大尺寸夹杂物的转炉出钢冶金工艺流程图。
[0021]
图2为本发明实施例到站前炉渣熔化情况示意图。
[0022]
图3为对比例lf到站前炉渣熔化情况示意图。
[0023]
图4为本发明实施例和对比例lf到站前夹杂物主要类型对比图。
具体实施方式
[0024]
为使本发明工艺要解决的技术问题、技术方案和优点更加清楚,下面将结合具体实施例和对比例对本发明工艺特点与优势进行详细描述。实施例与对比例均采用“转炉+吹氩站+lf精炼炉+rh真空精炼炉+软搅拌”生产流程冶炼gcr15高洁净度轴承钢,主要对实施例和对比例的转炉出钢冶金工艺进行对比。
[0025]
如图1所示,本发明一种减少轴承钢中大尺寸夹杂物的转炉出钢冶金工艺,所述转
炉出钢冶金工艺具体为:
[0026]
首先,在转炉冶炼进行钢水准备时,控制转炉终点钢水的含碳量和温度,并调整出钢的倾角,
[0027]
清理钢包,并对钢包预热至一定的温度,
[0028]
其次,在出钢过程中在预定的时间段以一定的方式分别加入铝合金、其他合金和复合渣料,并控制底吹搅拌和钢水的落点;
[0029]
出钢结束后,继续进行底吹搅拌,促进钢渣成分、温度均匀和夹杂物上浮,实现了减少轴承钢中大尺寸夹杂物的转炉出钢冶金工艺。
[0030]
所述钢水中c含量满足ω[c]0.1~0.4%;出钢温度满足1590~1650℃,所述倾角的角度为≥75
°
,所述钢包预热至1050℃以上。
[0031]
加入方式为:当出钢量达到总出钢量的1/5时,加入铝合金进行脱氧;
[0032]
出钢量达到1/3-1/2时加入其他合金,其他合金加入完成后,出钢量达到1/2-3/4时加入复合渣料;
[0033]
同时采用双透气砖方式进行底吹氩气进行搅拌。
[0034]
所述双透气砖包括两个透气砖,且2个所述透气砖位于距离钢包中心1/2-2/3钢包半径范围内,透气砖圆心与钢包底部圆心连线夹角范围为80
°‑
120
°
;
[0035]
且每个透气砖的吹气流量控制在1.2-3.5nl/min/。
[0036]
所述双透气砖方式为:在出钢量达到总出钢量的1/5之前,即铝合金加入之前,控制吹气流量1.2-2.0nl/min/吨钢;
[0037]
当出钢量在总出钢量的1/5-1/2之间,即铝合金和其他合金加入过程,控制吹气流量为2.0-2.7nl/min/吨钢;
[0038]
当出钢量达到总出钢量的1/2以后,即复合渣料加入过程,控制吹气流量位2.7-3.5nl/min/吨钢,一直保持到出钢结束。
[0039]
所述铝合金包括纯铝锭或铝铁合金,加入量为0.8-1.7kg/吨钢;
[0040]
其他合金包括铬铁、锰铁和硅铁合金,加入前预热至一定温度;
[0041]
预热温度为加入钢包前的温度大于300℃。
[0042]
所述复合渣料的加入量为7.6-10kg/吨钢,所述复合渣料包括合成渣料和石灰,石灰与合成渣料的质量比为0.1~0.5;加入顺序为先加入合成渣料再加入石灰。
[0043]
所述合成渣料中ω(cao)/ω(al2o3)的范围在0.9~2.0、ω(sio2)≤6%、ω(mgo)2~8%;
[0044]
所述出钢过程结束采取留钢操作,留钢量范围为7-11吨;
[0045]
整个出钢过程时间范围为3-8分钟;
[0046]
总的转炉渣下渣量控制在100kg以内;
[0047]
吹气量范围控制在3.2-6nl/min/吨钢。
[0048]
所述炉渣成分质量分数满足cao:52%-58%,al2o3:28%-35%,sio2:5%-8%,mgo:4%-8%,feo《1%。
[0049]
一种gcr15轴承钢,所述gcr15轴承钢采用上述的转炉出钢冶金工艺制备得到。
[0050]
实施例1:
[0051]
(1)转炉冶炼进行钢水准备:将118t预处理铁水及32t废钢冷料装入转炉进行吹
炼,加石灰、白云石等造渣剂,完成脱磷、脱碳、升温任务,转炉吹炼结束时钢液成分为:ω[c]0.14%,ω[si]0.001%,ω[mn]0.092%,ω[p]0.012%,ω[s]0.017%,ω[cr]0.032%,出钢温度1600℃。,出钢前进行挡渣操作。
[0052]
(2)钢包准备:使用的钢包前两炉冶炼的二元炉渣碱度为5-9,钢包清理后无明显残渣,钢包温度为1100℃。
[0053]
(3)出钢过程合金和渣料加入方式:出钢量达到总出钢量的1/5时,加入铝铁合金360kg进行脱氧,出钢量达到1/3时加入硅铁300kg、低碳锰铁70kg、低碳铬铁2225kg、增碳剂1260kg,其中合金入炉温度为315℃,合金加入完成后,出钢量达到3/4时加入渣料,首先加入合成渣料800kg,然后加入石灰350kg。合金和渣料加入钢包落点处于出钢的钢液流冲击钢包液面的活跃区,但不接触出钢的钢液流。出钢过程中移动钢包来保证出钢的钢液流冲击位置处于钢包液面圆心。出钢时间为230s。
[0054]
(4)出钢过程底吹气体的控制:采用双透气砖进行底吹,透气砖位于钢包半径的1/2处,两个透气砖圆心与钢包底部圆心连线夹角为90
°
,两个透气砖底吹气体流量保持一致,出钢前期为1.3nl/min/吨钢,中期为2.1nl/min/吨钢,后期为2.8nl/min/吨钢。
[0055]
(5)出钢结束后底吹气体和炉渣成分的控制:出钢结束前进行留钢操作,避免下渣,留钢量为10吨;出钢结束后增大气体流量到3.8nl/min/吨钢,促进炉渣熔化;lf通电前控制炉渣成分的质量分数为cao:54.3%,al2o3:29.2%,sio2:6.4%,mgo:4.5%,feo:0.8%。
[0056]
实施例2:
[0057]
(1)转炉冶炼进行钢水准备:将130t预处理铁水及15t废钢冷料装入转炉进行吹炼,加石灰、白云石等造渣剂,完成脱磷、脱碳、升温任务,转炉吹炼结束时钢液成分为:ω[c]0.15%,ω[si]0.001%,ω[mn]0.089%,ω[p]0.010%,ω[s]0.015%,ω[cr]0.033%,出钢温度1645℃。,出钢前进行挡渣操作。
[0058]
(2)钢包准备:使用的钢包前两炉冶炼的二元炉渣碱度为4.6-8.5,钢包清理后无明显残渣,钢包温度为1090℃。
[0059]
(3)出钢过程合金和渣料加入方式:出钢量达到总出钢量的1/5时,加入铝铁合金400kg进行脱氧,出钢量达到1/3时加入硅铁296kg、低碳锰铁69kg、低碳铬铁2213kg、增碳剂1245kg,其中合金入炉温度为310℃,合金加入完成后,出钢量达到3/4时加入渣料,首先加入合成渣料800kg,然后加入石灰350kg。合金和渣料加入钢包落点处于出钢的钢液流冲击钢包液面的活跃区,但不接触出钢的钢液流。出钢过程中移动钢包来保证出钢的钢液流冲击位置处于钢包液面圆心。出钢时间为241s。
[0060]
(4)出钢过程底吹气体的控制:采用双透气砖进行底吹,透气砖位于钢包半径的1/2处,两个透气砖圆心与钢包底部圆心连线夹角为90
°
,两个透气砖底吹气体流量保持一致,出钢前期为1.2nl/min/吨钢,中期为2.3nl/min/吨钢,后期为3.0nl/min/吨钢。
[0061]
(5)出钢结束后底吹气体和炉渣成分的控制:出钢结束前进行留钢操作,避免下渣,留钢量为11吨;出钢结束后增大气体流量到4nl/min/吨钢,促进炉渣熔化;lf通电前控制炉渣成分的质量分数为cao:56.1%,al2o3:30%,sio2:6%,mgo:4.0%,feo:0.5%。
[0062]
实施例3:
[0063]
(1)转炉冶炼进行钢水准备:将125t预处理铁水及18t废钢冷料装入转炉进行吹
炼,加石灰、白云石等造渣剂,完成脱磷、脱碳、升温任务,转炉吹炼结束时钢液成分为:ω[c]0.20%,ω[si]0.003%,ω[mn]0.098%,ω[p]0.013%,ω[s]0.021%,ω[cr]0.051%,出钢温度1615℃。,出钢前进行挡渣操作。
[0064]
(2)钢包准备:使用的钢包前两炉冶炼的二元炉渣碱度为5-8.7,钢包清理后无明显残渣,钢包温度为1100℃。
[0065]
(3)出钢过程合金和渣料加入方式:出钢量达到总出钢量的1/5时,加入铝铁合金380kg进行脱氧,出钢量达到1/3时加入硅铁322kg、低碳锰铁102kg、低碳铬铁2184kg、增碳剂1173kg,其中合金入炉温度为315℃,合金加入完成后,出钢量达到3/4时加入渣料,首先加入合成渣料800kg,然后加入石灰400kg。合金和渣料加入钢包落点处于出钢的钢液流冲击钢包液面的活跃区,但不接触出钢的钢液流。出钢过程中移动钢包来保证出钢的钢液流冲击位置处于钢包液面圆心。出钢时间为248s。
[0066]
(4)出钢过程底吹气体的控制:采用双透气砖进行底吹,透气砖位于钢包半径的1/2处,两个透气砖圆心与钢包底部圆心连线夹角为90
°
,两个透气砖底吹气体流量保持一致,出钢前期为1.8nl/min/吨钢,中期为2.1nl/min/吨钢,后期为3.3nl/min/吨钢。
[0067]
(5)出钢结束后底吹气体和炉渣成分的控制:出钢结束前进行留钢操作,避免下渣,留钢量为8吨;出钢结束后增大气体流量到5.4nl/min/吨钢,促进炉渣熔化;lf通电前控制炉渣成分的质量分数为cao:57%,al2o3:32.2%,sio2:5.9%,mgo:4.2%,feo:0.7%。
[0068]
实施例4:
[0069]
(1)转炉冶炼进行钢水准备:将132t预处理铁水及19t废钢冷料装入转炉进行吹炼,加石灰、白云石等造渣剂,完成脱磷、脱碳、升温任务,转炉吹炼结束时钢液成分为:ω[c]0.30%,ω[si]0.002%,ω[mn]0.105%,ω[p]0.008%,ω[s]0.019%,ω[cr]0.049%,出钢温度1630℃。,出钢前进行挡渣操作。
[0070]
(2)钢包准备:使用的钢包前两炉冶炼的二元炉渣碱度为4.9-8.7,钢包清理后无明显残渣,钢包温度为1120℃。
[0071]
(3)出钢过程合金和渣料加入方式:出钢量达到总出钢量的1/5时,加入铝铁合金420kg进行脱氧,出钢量达到1/3时加入硅铁316kg、低碳锰铁150kg、低碳铬铁2098kg、增碳剂1186kg,其中合金入炉温度为303℃,合金加入完成后,出钢量达到3/4时加入渣料,首先加入合成渣料850kg,然后加入石灰400kg。合金和渣料加入钢包落点处于出钢的钢液流冲击钢包液面的活跃区,但不接触出钢的钢液流。出钢过程中移动钢包来保证出钢的钢液流冲击位置处于钢包液面圆心。出钢时间为229s。
[0072]
(4)出钢过程底吹气体的控制:采用双透气砖进行底吹,透气砖位于钢包半径的1/2处,两个透气砖圆心与钢包底部圆心连线夹角为90
°
,两个透气砖底吹气体流量保持一致,出钢前期为1.6nl/min/吨钢,中期为2.6nl/min/吨钢,后期为2.8nl/min/吨钢。
[0073]
(5)出钢结束后底吹气体和炉渣成分的控制:出钢结束前进行留钢操作,避免下渣,留钢量为10吨;出钢结束后增大气体流量到5.0nl/min/吨钢,促进炉渣熔化;lf通电前控制炉渣成分的质量分数为cao:58%,al2o3:28.3%,sio2:7.0%,mgo:5.0%,feo:0.84%。
[0074]
对比例:
[0075]
(1)转炉冶炼工序:将119t预处理铁水及34t废钢冷料装入转炉进行吹炼,加石灰、白云石等造渣剂,完成脱磷、脱碳、升温任务,转炉吹炼结束时钢液成分为:ω[c]0.01%,ω
[si]0.001%,ω[mn]0.143%,ω[p]0.017%,ω[s]0.019%,ω[cr]0.053%,出钢温度1587℃。出钢前无挡渣操作。
[0076]
(2)钢包准备:使用的钢包前两炉冶炼的二元炉渣碱度小于3,钢包清理后底部边缘部分有微量残渣,钢包温度为980℃。
[0077]
(3)出钢过程合金和渣料加入方式:开始出钢时即加入铝铁合金323kg,铝铁加入完成后,加入硅铁250kg、低碳铬铁1808kg、增碳剂923kg,其中低碳铬铁入炉温度为常温,合金加入末期,开始加入渣料,低碱度渣料100kg,石灰400kg,出现合金和渣料混合现象,未控制渣料和合金的加入落点,出现出钢钢液直接冲击合金和渣料的现象。出钢过程中,在出钢钢液流冲击钢包液面的位置接近钢包壁时移动一次钢包,调整出钢钢液流冲击钢包液面的位置,出钢时间为208s。
[0078]
(4)出钢过程底吹气体的控制:采用双透气砖进行底吹,透气砖位于钢包半径的1/2处,两个透气砖圆心与钢包底部圆心连线夹角为180
°
,两个透气砖底吹气体流量保持一致,出钢前期和中期为5nl/min/吨钢,后期为8nl/min/吨钢,对钢液进行强搅拌。
[0079]
(5)出钢结束后底吹气体和炉渣成分的控制:出钢结束前进行留钢操作,避免下渣,留钢量为5吨;出钢结束后气体流量为8nl/min/吨钢,促进炉渣熔化;lf通电前控制炉渣成分的质量分数为cao:56.5%,al2o3:22.2%,sio2:12.3%,mgo:4.7%,feo:0.8%。
[0080]
实施例与对比例主要区别在于转炉终点控制、下渣量控制、钢包管理、合金和渣料加入方式、底吹气体控制和炉渣成分控制。实施例对整个转炉出钢过程的各个工艺细节进行了严格控制,当部分条件无法满足时,则无法达到更为理想的冶炼效果。实施例出钢前有挡渣操作,避免了出钢前下渣;按照出钢量不同来控制合金和渣料的加入时机,铝合金和其他合金分开加入,对其他进行烘烤,合金和渣料分开加入,避免了合金和渣料的混冲导致合金收得率低;钢包烘烤温度保证和残渣清理干净,控制出钢过程温降,稳定合金和渣料熔化速度;没有低碱度渣的加入,而且将合成渣的加入提前到出钢过程,避免了低碱度渣加入使得炉渣粘度增大而导致炉渣结壳;出钢过程采用新的双透气砖位置和较少的底吹流量,促进了合金和渣料熔化,避免了炉渣的卷入;严格控制出钢结束后气体搅拌强度减少了炉渣卷入,控制炉渣成分减少后续精炼过程al的烧损。
[0081]
出钢结束后进行吹气搅拌,实际炉渣的熔化效果如图2和图3所示。从图2中可以看出,采用实施例冶炼工艺,由于严格控制了出钢过程造渣剂的成分和加入时机,本发明实施例的化渣均匀,无炉渣结壳现象,化渣效果良好;对比例有明显的炉渣结壳现象,出现了钢液的裸露,化渣效果较差。
[0082]
与图2阶段对应的主要夹杂物类型对比如图4所示。从图4可以看出,实施例炉渣熔化效果良好,且夹杂物主要类型为小尺寸的al2o3类夹杂物,是转炉出钢过程的脱氧产物,这类夹杂物熔点高,容易团聚成大尺寸夹杂物,在精炼过程可以很快上浮去除;对比例中夹杂物主要类型为cao-al2o
3-mgo-sio
2-mno类复合夹杂物,尺寸较大,这类夹杂物是典型的卷渣类夹杂物,并且在浅色的区域发现了合金元素cr,说明是合金和炉渣相互作用的产物,这类夹杂物熔点低,与钢液润湿性良好,在后续精炼过程中很难彻底上浮去除,容易残留在钢中导致大尺寸夹杂物超标。
[0083]
表2所示为本发明实施例与对比例进行轴承钢冶炼的生产效果对比(实施例和对比例的平均数据)。冶炼过程中在lf进站前、lf前期、lf中期和lf出站前、rh破空后、软吹中
期和吊包前取钢样,对每个钢样10mm*10mm范围内夹杂物进行统计分析,每炉的轧材随机抽检10支试样棒进行水浸探伤检测,每炉轧材随机取6个金相样进行夹杂物评级。从表2可以看出,本发明实施例工艺在冶炼过程中大尺寸夹杂物产生的数量和尺寸都明显降低,并且最终产品的ds评级和探伤检测合格率都明显高于对比例。以上对比说明本发明工艺可以有效减少轴承钢中的大尺寸夹杂物。
[0084]
表2本发明实施例与对比例进行轴承钢冶炼的生产效果对比
[0085][0086]
以上对本技术实施例所提供的一种减少轴承钢中大尺寸夹杂物的转炉出钢冶金工艺,进行了详细介绍。以上实施例的说明只是用于帮助理解本技术的方法及其核心思想;同时,对于本领域的一般技术人员,依据本技术的思想,在具体实施方式及应用范围上均会有改变之处,综上所述,本说明书内容不应理解为对本技术的限制。
[0087]
如在说明书及权利要求书当中使用了某些词汇来指称特定组件。本领域技术人员应可理解,硬件制造商可能会用不同名词来称呼同一个组件。本说明书及权利要求书并不以名称的差异来作为区分组件的方式,而是以组件在功能上的差异来作为区分的准则。如在通篇说明书及权利要求书当中所提及的“包含”、“包括”为一开放式用语,故应解释成“包含/包括但不限定于”。“大致”是指在可接收的误差范围内,本领域技术人员能够在一定误差范围内解决所述技术问题,基本达到所述技术效果。说明书后续描述为实施本技术的较佳实施方式,然所述描述乃以说明本技术的一般原则为目的,并非用以限定本技术的范围。本技术的保护范围当视所附权利要求书所界定者为准。
[0088]
还需要说明的是,术语“包括”、“包含”或者其任何其他变体意在涵盖非排他性的包含,从而使得包括一系列要素的商品或者系统不仅包括那些要素,而且还包括没有明确列出的其他要素,或者是还包括为这种商品或者系统所固有的要素。在没有更多限制的情况下,由语句“包括一个
……”
限定的要素,并不排除在包括所述要素的商品或者系统中还存在另外的相同要素。
[0089]
应当理解,本文中使用的术语“和/或”仅仅是一种描述关联对象的关联关系,表示可以存在三种关系,例如,a和/或b,可以表示:单独存在a,同时存在a和b,单独存在b这三种情况。另外,本文中字符“/”,一般表示前后关联对象是一种“或”的关系。
[0090]
上述说明示出并描述了本技术的若干优选实施例,但如前所述,应当理解本技术并非局限于本文所披露的形式,不应看作是对其他实施例的排除,而可用于各种其他组合、修改和环境,并能够在本文所述申请构想范围内,通过上述教导或相关领域的技术或知识进行改动。而本领域人员所进行的改动和变化不脱离本技术的精神和范围,则都应在本申
请所附权利要求书的保护范围内。