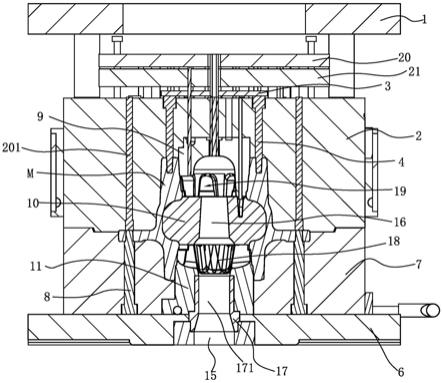
1.本发明属于轮毂技术领域,具体涉及一种铝合金轮毂的铸造模具及铸造铝合金轮毂的方法。
背景技术:
2.随着中国经济的快速增长,以电商、危化品、冷链等为代表的高端物流迅猛发展,其对车辆的轻量化要求更为突出;以1辆牵引车为例(每年运行约20万公里),每减重1kg,每年多赚运费近200元;所以商用车用户及整车厂对轻量化的需求迫在眉睫。
3.相较于商用车传统轮毂的材质球墨铸铁,铝的密度约为球墨铸铁的1/3,容易保证产品的动平衡,车辆防抖动效果好;而且产品质量轻,不容易锈蚀,对节能减排有着较好的促进效果;铝合金良好的性能也能够保正相应的轮毂疲劳强度硬度,所以用铝合金代替铸铁将成为轮毂轻量化的重要方法。
4.但同时还要保持相应的轮毂疲劳强度硬度,铝合金轮毂的固溶时效处理是能保证强度的良好手段。原来用于制造传统轮毂的模具不适用于铸造铝合金轮毂,因此,需要发明一种铝合金轮毂的铸造模具,以适应轮毂轻量化发展的进程。
5.现有的铝合金轮毂的法兰盘上的螺栓孔和铝合金轮毂端面的半轴螺栓孔均由机加工开设,加工成本高,且轮毂储油腔位置无法由铸造直接得到,铸造完成后,需要机加工毛坯储油腔位置才能得到轮毂油腔,但是在机加工轮毂油腔之前需要对轮毂毛坯进行固溶处理和时效处理,由于未加工时的毛坯储油腔处壁厚较厚,可能导致固溶处理和时效处理不充分致使晶粒粗大,致使产品性能较差,并且浪费材料、刀具。
技术实现要素:
6.为克服上述现有技术的不足,本发明所要解决的第一个技术问题是提供一种铝合金轮毂的铸造模具,能由铸造直接获得螺栓孔和轮毂储油腔,节约铸造成本和机加工成本,并且适应轮毂轻量化发展。
7.为解决第一个技术问题,本发明采用以下技术方案:
8.一种铝合金轮毂的铸造模具,其特征在于,包括:
9.上模组件,所述上模组件包括上模连接板和上模,所述上模固定连接在所述上模连接板下部,所述上模顶部固定连接有固定压板,所述固定压板上固定连接有伸入所述上模内部的多个上模预铸孔销,所述上模内部固定连接有上模镶块,
10.下模组件,所述下模组件包括下模底板和下模,所述下模固定在所述下模底板上,所述下模内固定连接有多个下模预铸孔销,
11.模芯组件,所述模芯组件包括上模芯、成型轮毂油腔的中间模芯和下模芯,所述上模芯固定连接在所述上模,所述下模芯位于所述下模内并与所述下模固定连接,所述中间模芯与所述下模芯固定连接,所述上模芯与所述中间模芯插接,
12.脱模辅助组件,所述脱模辅助组件包括推板、多个顶出杆和多个导向柱,所述推板
位于所述上模连接板和所述上模之间,所述顶出杆和所述导向柱分别与所述推板固定连接,多个所述顶出杆分别穿过所述上模、所述上模芯和所述上模镶块,所述顶出杆可相对所述上模和所述上模镶块上下移动,所述导向柱可相对所述上模上下移动,
13.所述上模、所述上模镶块、所述上模预铸孔销、所述下模、所述下模预铸孔销和所述模芯组件共同围成铝合金轮毂的型腔,
14.浇注系统,所述浇注系统设置有连通所述型腔的浇口、直流式竖向浇道和横向浇道,所述浇口设置于所述下模底板。
15.优选的,所述下模芯内部设置有浇口件,所述浇口件上开设有与所述浇口相通的浇口浇道,所述中间模芯上开设有所述直流式竖向浇道,所述浇口浇道与所述直流式竖向浇道之间设置有过滤网;
16.所述直流式竖向浇道与所述横向浇道相连通,所述横向浇道包括第一横向浇道和第二横向浇道,所述下模芯上设置有多个所述第一横向浇道,所述上模芯上设置有多个所述第二横向浇道。
17.优选的,所述下模芯设置有多个沿圆周方向间隔分布的上凸支撑腿,相邻的两个所述上凸支撑腿之间的空间形成所述第一横向浇道,所述上凸支撑腿顶部设置有第一定位凸起,
18.所述上模芯设置有多个沿圆周方向间隔分布的下凸支撑腿,相邻的两个所述下凸支撑腿之间的空间形成所述第二横向浇道,所述下凸支撑腿底部设置有第二定位凸起,
19.所述中间模芯的底部和顶部分别开设有多个底部凹槽和多个顶部凹槽,所述底部凹槽与所述第一定位凸起相适配,所述顶部凹槽与所述第二定位凸起相适配。
20.优选的,所述中间模芯的周面上设置有使轮毂毛坯达到动平衡的动平衡凹槽。
21.优选的,所述中间模芯的其中一个底部凹槽设为防错凹槽,所述下模芯上其中的一个所述第一定位凸起对应设为防错凸起。
22.优选的,轮毂毛坯上沿周向上设置有多个间隔设置的加强筋和多个间隔设置的止口台,对应的每个所述加强筋和每个所述止口台相连,称为加强止口结构,所述上模镶块设置有多块,沿周向间隔设置在所述上模内,加强止口成型腔成型所述加强止口结构,所述加强止口成型腔的其中一部分设置在所述上模镶块上,另一部分设置在所述上模上。
23.优选的,所述推板包括固定连接的固定拆卸板和导向拆卸板,多个所述顶出杆的上部连接端穿过所述导向拆卸板与所述固定拆卸板固定,其中一部分所述顶出杆的下部顶出端顶至所述轮毂毛坯的法兰盘端面上,另外一部分顶至所述轮毂毛坯开设半轴螺栓孔的端面上。
24.优选的,所述上模上设置有竖向的排气杆。
25.作为同一个发明构思,本发明所要解决的另一个技术问题是提供一种轮毂铸造方法,使得铝合金轮毂致密性好和强度高。
26.为解决第二个技术问题,本发明采用以下技术方案:
27.使用上述铝合金轮毂的铸造模具铸造铝合金轮毂的方法,包括如下步骤:
28.a)熔化原料:对铝合金原料进行化学成分检验,将检验合格的铝合金原料熔炼,熔炼时,当铝合金熔液温度在750℃~760℃时加入精炼剂进行精炼,所述铝合金原料和所述精炼剂的质量比是100:(0.2~0.25);
29.对熔化炉进行除气,向铝合金熔液内加入除渣剂进行除杂质除渣,所述铝合金原料和所述除渣剂的质量比是100:(0.1~0.15);
30.将检测合格后的熔液在715℃~735℃转移至保温炉内保温,对保温炉内保温的熔液取样浇注试棒,检测浇注试棒,检测合格后,保温炉内所述熔液作为浇铸液;
31.b)制作中间模芯:与a)步骤同时,向壳芯机内射砂制作所述中间模芯的砂芯,并将所述砂芯浸涂、烘烤,得到所述中间模芯;
32.c)模具预处理:对模具进行预热,当模具温度达到80
±
20℃时,用喷砂枪开始清理型腔;
33.继续预热模具,对所述浇注系统喷涂保温涂料,然后再喷涂润滑脱模涂料;
34.模具加热,烤模温度设定360
±
20℃,烤模保温时间为≥50分钟;
35.然后将所述中间模芯与所述下模芯和所述上模芯连接;
36.模具继续加热,保持模具的上模组件温度在340℃~360℃,保持模具的下模组件温度在360℃~400℃;
37.d)浇注:a)步骤的浇铸液在压力作用下从所述保温炉进入升液管,升液管连接浇口;
38.升液时间10s,使保温炉压力保持210mbar;
39.继续加压15s,进行充型并使保温炉压力保持270mbar;
40.继续加压6s,使保温炉压力保持360mbar;
41.继续加压6s,使保温炉压力保持520mbar;
42.继续加压,当保温炉压力达到800mbar后,保压时间240s,然后开始泄压;
43.e)冷却:对模具进行冷却,使铸件凝固,冷却时间150~200s;
44.f)取出铝合金轮毂毛坯,然后用x光探伤检测,然后对铝合金轮毂毛坯的分型面处飞边和毛刺进行打磨清理,然后进行固溶时效处理,最后进行抛丸处理。
45.采用了上述技术方案后,本发明的有益效果是:
46.本发明铝合金轮毂的铸造模具能由铸造得出铝合金轮毂的法兰盘上的螺栓孔和铝合金轮毂端面的半轴螺栓孔,由于预铸孔销已经将螺栓孔铸造成型,需要机加工的工作量大幅减小,成品工艺出品率高。且轮毂储油腔位置也由铸造直接得到,由于加工体积的减小,刀具磨损也大幅下降,提高了加工效率、降低了加工费用。
47.本发明采用低压铸造的方法铸造铝合金轮毂,采用内置式浇道制造模具和浇注轮毂时用料少,内置式浇道设为直流式竖向浇道和横向浇道,浇注时,浇铸液通过直流式竖向浇道和横向浇道向型腔内充型,铝液平稳缓流且可以补缩,使轮毂毛坯顺序凝固,轮毂毛坯工艺出品率高,可以达到82%。
附图说明
48.图1是本发明铝合金轮毂的铸造模具的结构示意图;
49.图2是图1中模芯组件的结构示意图;
50.图3是图2中中间模芯的仰视图的结构示意图;
51.图4是图3中a-a处的剖视示意图;
52.图5是图2中上模芯的仰视结构图;
53.图6是图5中b-b处的剖视示意图;
54.图7是图2中下模芯的俯视结构图;
55.图8是铝合金轮毂毛坯的结构示意图;
56.图9是上模镶块5的结构示意图;
57.图10是图1中上模的示意图;
58.图11是图10中c-c处的剖视示意图;
59.图12是铝合金轮毂的铸造模具合模状态下的结构示意图;
60.图13是铝合金轮毂的铸造模具开模状态下的结构示意图;
61.图中:1、上模连接板;2、上模;201、排气杆;202、上模镶块安装孔;203、预铸孔销安装孔;204、部分加强止口成型腔;3、固定压板;4、上模预铸孔销;5、上模镶块;501、成型止口台沟槽;6、下模底板;7、下模;8、下模预铸孔销;9、上模芯;91、下凸支撑腿;91a、第二定位凸起;901、排气孔;902、顶出杆孔;10、中间模芯;101、底部凹槽;101a、防错凹槽;102、顶部凹槽;103、动平衡凹槽;11、下模芯;111、上凸支撑腿;111a、第一定位凸起;111b、防错凸起;13、顶出杆;14、导向柱;15、浇口;16、直流式竖向浇道;17、浇口件;171、浇口浇道;18、过滤网;19、横向浇道;191、第一横向浇道;192、第二横向浇道;m、轮毂毛坯;m1、加强筋;m2、止口台;m3、法兰盘端面;m4、半轴螺栓孔的端面,20、固定拆卸板;21、导向拆卸板。
具体实施方式
62.下面结合附图和实施例对本发明进一步详细说明。
63.本发明的铝合金轮毂的铸造模具包括:上模组件、下模组件、模芯组件、脱模辅助组件和浇注系统。
64.如图1至图13所示,上模组件包括上模连接板1和上模2,上模2固定连接在所述上模连接板1下部,所述上模2顶部固定连接有固定压板3,所述固定压板3上固定连接有伸入所述上模2内部的多个上模预铸孔销4,所述上模2内部固定连接有上模镶块5,上模2上开设有上模镶块安装孔202,上模镶块5安装在上模镶块安装孔202内。上模2上开设有安装上模预铸孔销4的预铸孔销安装孔203。
65.下模组件包括下模底板6和下模7,所述下模7固定在所述下模底板6上,所述下模7内固定连接有多个下模预铸孔销8,
66.如图2所示,模芯组件包括上模芯9、成型轮毂油腔的中间模芯10和下模芯11,所述上模芯9固定连接在所述上模2,所述下模芯11位于所述下模7内并与下模7固定连接,中间模芯10与所述下模芯11固定连接,上模芯9与中间模芯10插接,
67.如图1、图12和图13所示,脱模辅助组件包括推板、多个顶出杆13和多个导向柱14,推板位于所述上模连接板1和所述上模2之间,顶出杆13和导向柱14分别与推板固定连接,多个所述顶出杆13分别穿过所述上模2、所述上模芯9和所述上模镶块5,所述顶出杆13可相对所述上模2和所述上模镶块5上下移动,导向柱14可相对上模2上下移动,
68.上模2、所述上模镶块5、所述上模预铸孔销4、所述下模7、所述下模预铸孔销8和所述模芯组件共同围成铝合金轮毂的型腔,上模2上设置有排气孔901,浇注系统设置有连通型腔的浇口15、直流式竖向浇道16和横向浇道19,所述浇口15设置于所述下模底板6。
69.下模芯11内部设置有浇口件17,所述浇口件17上开设有与所述浇口15相通的浇口
浇道171,所述中间模芯10上开设有所述直流式竖向浇道16,所述浇口浇道171与所述直流式竖向浇道16之间设置有过滤网18;
70.所述直流式竖向浇道16与所述横向浇道19相连通,所述横向浇道19包括第一横向浇道191和第二横向浇道192,所述下模芯11上设置有多个所述第一横向浇道191,所述上模芯9上设置有多个所述第二横向浇道192。
71.如图2和图7所示,下模芯11设置有多个沿圆周方向间隔分布的上凸支撑腿111,相邻的两个所述上凸支撑腿111之间的空间形成所述第一横向浇道191,所述上凸支撑腿111顶部设置有第一定位凸起111a,
72.上模芯9设置有多个沿圆周方向间隔分布的下凸支撑腿91,相邻的两个下凸支撑腿91之间的空间形成所述第二横向浇道192,下凸支撑腿91底部设置有第二定位凸起91a,上模和上模芯9上开设有顶出杆孔902。
73.铸造采用内置式浇道,用料少,轮毂毛坯工艺出品率高,成品率可以达到82%。轮毂从模具下方浇注,采用直流式竖向浇道16和横向浇道19浇注充型,直流式竖向浇道16可以补缩,使铝液平稳缓流,并且可以使轮毂毛坯顺序凝固。
74.中间模芯10的底部和顶部分别开设有多个底部凹槽101和多个顶部凹槽102,底部凹槽101与第一定位凸起111a相适配,顶部凹槽102与第二定位凸起91a相适配。
75.如图3所示,中间模芯10的周面上设置有使轮毂毛坯m达到动平衡的动平衡凹槽103。中间模芯10的其中一个底部凹槽设为防错凹槽101a,下模芯11上其中的一个第一定位凸起111a对应设为防错凸起111b。
76.如图8所示,轮毂毛坯m上沿周向上设置有多个间隔设置的加强筋m1和多个间隔设置的止口台m2,对应的每个所述加强筋m1和每个所述止口台m2相连,称为加强止口结构,所述上模镶块5设置有多块,沿周向间隔设置在上模2内,加强止口成型腔成型所述加强止口结构,所述加强止口成型腔的其中一部分设置在所述上模镶块5上,另一部分设置在上模2上,如图10所示,上模2上的部分加强止口成型腔204。
77.轮毂加强筋m1形状细长,如果仅将成型轮毂加强筋m1的型腔开设在上模镶块5上,则需要在上模镶块5上的开设有较深狭窄的沟槽,无法直接加工成型,并且成型后难以脱模。因此,如图9所示,上模镶块5上的成型止口台沟槽501是敞开式的,比较容易脱模和清理。通过进一步的优化,如图10所示,将所述加强止口成型腔的其中一部分设置在所述上模镶块5上,另一部分设置在上模2上,具体可以将所述加强止口成型腔对半均分设置在所述上模镶块5上和上模2上,铸造成型时避免了其易粘存、难清理的缺陷。并且,若上模镶块5磨损,则可以方便地拆卸修理更换。
78.在制作模具时,上模镶块5与上模之间存留细微狭缝,狭缝间隙约为0.15mm,利于充型及排气,且不会钻入铝水。上模镶块5与上模为同体材料,采用线切割的方法将其分割,并利用螺钉连接形式将上模镶块与上模固定在一起。
79.推板包括固定连接的固定拆卸板20和导向拆卸板21,多个顶出杆13的上部连接端穿过所述导向拆卸板21与所述固定拆卸板20固定,其中一部分顶出杆13的下部顶出端顶至所述轮毂毛坯的法兰盘端面m3上,另外一部分顶至所述轮毂毛坯开设半轴螺栓孔的端面m4上。上模2上设置有竖向的排气杆201。上模芯9上设置有排气孔901。
80.现有的铝合金轮毂法兰盘上的螺栓孔以及半轴螺栓孔通常是经机加工打孔得到,
本发明的铝合金轮毂铸造模具利用上模预铸孔销4和下模预铸孔销8铸造出法兰盘上的螺栓孔以及半轴螺栓孔,由于预铸孔销已经将螺栓孔铸造预成型,加工余量大幅减小,成品工艺出品率达87%。由于加工体积的减小,刀具磨损也大幅下降,提高了加工效率、降低了加工费用。
81.如图12所示,合模状态下,上模2压在下模7上,此时的导向柱14下部支撑在下模7上,导向柱14上部将导向拆卸板21和所述固定拆卸板20顶起,导向拆卸板21与固定压板3在上下方向有距离。如图13所示,开模时,上模连接板1被吊起,带动上模2以及与上模镶块5固定的组件升起,在上模2上升并与下模7分开的过程中,导向拆卸板21和所述固定拆卸板20相对下移,固定拆卸板20使顶出杆将轮毂毛坯m推留在下模7上,使得轮毂毛坯m与上模2易于脱模分开。
82.上模组件和下模组件均设置有加热棒,加热棒用于加热模具,上模组件和下模组件上均设置有冷却水管,用于冷却。
83.利用上述铝合金轮毂的铸造模具铸造铝合金轮毂的方法,包括如下步骤:
84.a)熔化原料:对铝合金原料进行化学成分检验,利用电子秤称重,并用光谱机对铝锭或铝棒等回炉料分析化验,与标准进行比对,将检验合格的铝合金原料熔炼,熔炼时,当铝合金熔液温度在750℃~760℃时加入精炼剂进行精炼,所述铝合金原料和所述精炼剂的质量比是100:(0.2~0.25);例如:使用1吨铝合金原料倾倒融化炉进行融化合金,当铝液温度在750~760℃时,用钟罩压入烘烤后的精炼剂,每100kg的合金原料需要加入精炼剂0.2~0.25kg,使用一体式除气机,对熔化炉进行除气,除气10~15分钟后静置10分钟;
85.向铝合金熔液内加入除渣剂进行除杂质除渣,铝合金原料和所述除渣剂的质量比是100:(0.1~0.15);即在100kg合金加除渣剂0.1~0.15kg进行覆盖翻压铝液表面杂物,扒渣后静置10分钟。
86.将检测合格后的熔液在715℃~735℃转移至保温炉内保温,炉内取样检查变质效果,即对保温炉内保温的熔液取样浇注试棒,检测浇注试棒,检测合格后,保温炉内所述熔液作为浇铸液,检查炉门密封状态后关闭炉门。
87.b)制作中间模芯:与a)步骤同时,向壳芯机内射砂制作所述中间模芯的砂芯,并将所述砂芯浸涂、烘烤,得到所述中间模芯;具体如下:
88.将制作中间模芯的定模模具加热至220~240℃,动模模具温度240~260℃;向定模模具和动模模具内射砂,射砂时间5s,射砂压力0.5mpa,砂芯固化时间130~160s,然后浸涂砂芯,浸涂物料为水基或醇基涂料,在砂芯表面沾涂浸涂物料厚度0.2~0.3mm,烘烤保温时间2小时,烘烤温度180~195℃,得到中间模芯。
89.c)模具预处理:对模具进行预热,用红外线测温仪确认模具温度达到80
±
20℃时,使用手持式喷砂枪开始清理浇注系统如型腔、直流式竖向浇道16和横向浇道19流道;
90.继续预热模具,用红外线测温仪确认模具温度达到240
±
20℃时,对所述浇注系统多次喷涂或刷涂保温涂料,当模具温度达到300
±
20℃时,在型腔表面喷涂保温涂料,然后再喷涂润滑脱模涂料;模具加热,烤模温度设定360
±
20℃,烤模保温时间为≥50分钟,使整体的模具在一定范围内温度均匀一致;
91.然后将中间模芯10放入模具中并与下模芯11和上模芯9连接;
92.模具继续加热,保持模具的上模组件温度在340℃~360℃,保持模具的下模组件
温度在360℃~400℃;并检查冷却水管是否通顺,观察回水状态。
93.d)浇注:a)步骤的浇铸液在压力作用下从所述保温炉进入升液管,升液管连接浇口;
94.升液时间10s,使保温炉压力保持210mbar;
95.继续加压15s,进行充型并使保温炉压力保持270mbar;
96.继续加压6s,使保温炉压力保持360mbar;
97.继续加压6s,使保温炉压力保持520mbar;
98.继续加压,当保温炉压力达到800mbar后,保压时间240s,然后开始泄压;
99.e)冷却:泄压后对模具进行冷却,使铸件凝固,冷却时间150~200s;
100.f)取出铝合金轮毂毛坯,然后用x光探伤检测,然后对铝合金轮毂毛坯m的分型面处飞边和毛刺进行打磨清理,然后进行固溶时效处理,最后进行抛丸处理。
101.以上所述仅为本发明的较佳实施例而已,并不用以限制本发明,凡在本发明的精神和原则之内所作的任何修改、等同替换和改进等,均应包含在本发明的保护范围之内。