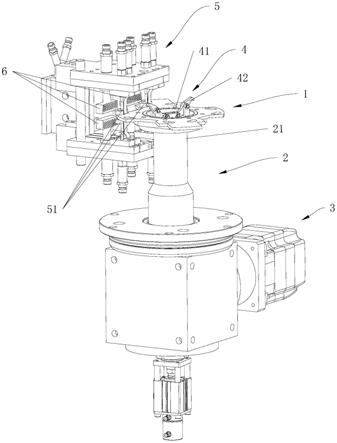
1.本发明涉及零件加工技术领域,具体涉及一种工件孔热处理装置。
背景技术:
2.高频淬火是使工件表面产生一定的感应电流,迅速加热零件表面,然后迅速淬火的一种金属热处理方法,多用于工业金属零件表面淬火。
3.对于具有孔结构的零件,目前的高频淬火工艺的热处理效果不佳,造成零件开孔位置的硬度通常达不到产品要求,影响零件的使用寿命,并且零件容易开裂,而且当零件表面积较大时,会造成大量能量损失。
技术实现要素:
4.为解决上述背景技术中阐述的技术问题,本技术的目的在于提出一种工件孔热处理装置,本技术对工件孔进行单独高频淬火,保证工件开孔位置的硬度达标,提高工件质量,并且提高淬火效率,减少能量损失。
5.为了达到上述目的,本技术采取了如下所述的技术方案:
6.一种工件孔热处理装置,所述工件孔围绕工件设置,所述热处理装置包括热处理机构,所述热处理机构包括底座、旋转结构、定位结构和电磁感应器;所述底座具有加热工位,所述旋转结构与所述底座相连,所述旋转结构能够带动所述底座旋转以使所述加热工位旋转;所述定位结构包括定位件,所述定位件将所述工件固定在所述加热工位;所述电磁感应器具有感应部,沿所述加热工位的旋转方向,所述感应部位于所述加热工位一侧,所述感应部绕有感应线圈;当所述工件固定于所述加热工位时,向所述感应线圈通入电流,并且通过所述旋转结构带动所述加热工位旋转,使得所述感应部依次对所有所述工件孔周围的表面进行电磁感应加热。
7.由上,在对工件进行热处理时,首先通过定位件将工件固定在热处理工位上,减小工件在热处理过程中由于定位不可靠造成热处理位置存在偏差的可能性,为工件孔的位置能够对准提供保障,保证工件质量;然后,通过旋转结构(例如:旋转电机)带动底座旋转,以使定位于加热工位的工件旋转,使得工件孔与感应部互相对应;最后,向感应线圈通入电流,并且通过旋转结构带动加热工位旋转,使得感应部依次对所有工件孔周围的表面进行电磁感应加热。
8.作为本发明的一种优选方案,示例性的,所述感应部的轮廓形状与所述工件孔的轮廓形状对应。由此,工件孔周围受热处理的表面的轮廓形状与工件孔的轮廓形状相对应,既保证热处理效果,又能够减少能量损失,且保证了热处理位置准确度。工件孔周围受热处理的表面的轮廓形状与工件孔的轮廓形状相对应,能够使工件孔受热平衡,减小工件孔开裂的可能性。
9.作为本发明的一种优选方案,示例性的,沿垂直于所述加热工位旋转方向的方向,所述感应部分布于所述加热工位的两侧。由此,能够通过同时对工件孔两侧的周围表面进
行热处理,提高工件孔的热处理均匀度,有效地避免工件孔中间层出现夹层,且降低工件孔发生开裂的可能性,且提高热处理效率。
10.作为本发明的一种优选方案,示例性的,所述工件具有多个突出部,每个所述突出部开有两个所述工件孔,将相邻两个所述突出部上距离最近的两个所述工件孔设为为一组;当所述工件固定于所述加热工位时,沿所述加热工位的旋转方向,所述感应部依次对每组所述工件孔周围的表面进行电磁感应加热。由此,每次都会对相邻突出部上相邻的工件孔进行热处理以补偿不同突出部上工件孔的平面度差异。
11.作为本发明的一种优选方案,示例性的,所述电磁感应器设有第一调节部,所述第一调节部与所述感应部远离所述加热工位的一侧连接,用于调节所述感应部与所述加热工位的距离以调节被加热表面的面积。由此,通过改变感应线圈与工件孔周围表面的间隙以改变工件孔周围被加热表面的面积,能够根据不同的工艺要求,将加热面积降到最小范围,减小额外的应力和应变,减小工件孔发生形变的可能性,且能够保证工件孔周围表面的硬度要求。
12.作为本发明的一种优选方案,示例性的,所述电磁感应器设有第二调节部,所述第二调节部与所述感应部连接,用于调节所述感应线圈的间隙以调节被加热表面的面积。由此,通过改变感应线圈的线圈间隙以改变工件孔周围被加热表面的面积,能够根据不同的工艺要求,将加热面积降到最小范围,减小额外的应力和应变,减小工件孔发生形变的可能性,且能够保证工件孔周围表面的硬度要求。
13.作为本发明的一种优选方案,示例性的,所述工件具有定位孔,所述底座具有所述加热工位的一侧具有销孔,所述定位件包括定位销,所述定位销依次进入所述定位孔与所述销孔以将所述工件定位于所述加热工位。由此,能够减小工件在热处理过程中由于定位不可靠造成热处理位置存在偏差的可能性,同时,为了对工件孔的位置能够对准提供保障,保证工件质量,结构简单,制造成本低。
14.作为本发明的一种优选方案,示例性的,所述定位结构还包括定位头,所述定位头沿垂直于所述加热工位旋转方向的方向移动以使所述工件与所述底座抵靠从而夹持所述工件。由此,能够减小工件在热处理过程中由于定位不可靠造成热处理位置存在偏差的可能性,同时,为了对工件孔的位置能够对准提供保障,保证工件质量,结构简单,制造成本低。
15.作为本发明的一种优选方案,示例性的,还包括冷却机构,沿所述加热工位的旋转方向,所述冷却机构位于所述加热工位一侧,所述冷却机构设有冷却喷头,所述冷却喷头的喷孔朝向所述加热工位设置;所述冷却机构工作时,所述旋转结构带动所述加热工位旋转以冷却所有所述工件孔。
16.作为本发明的一种优选方案,示例性的,所述冷却喷头至少设有两个,沿垂直于所述加热工位旋转方向的方向,所述冷却喷头分布于所述加热工位的两侧。
附图说明
17.此处所说明的附图用来提供对本发明的进一步理解,构成本发明的一部分,本发明的示意性实施例及其说明用于解释本发明,并不构成对本发明的不当限定。在附图中:
18.图1为本技术一种实施例中热处理装置的结构示意图;
19.图2为本技术一种实施例中工件的结构示意图。
20.1.工件;11.工件孔;12.突出部;13.定位孔;
21.2.底座;21.加热工位;
22.3.旋转结构;
23.4.定位结构;41.定位件;42.定位头;
24.5.电磁感应器;51.感应部;
25.6.冷却喷头。
具体实施方式
26.为了对本发明的技术特征、目的和效果有更加清楚的理解,现对照附图说明本发明的具体实施方式,在各图中相同的标号表示结构相同或结构相似但功能相同的部件。
27.在下面的描述中阐述了很多具体细节以便于充分理解本发明,但是,本发明还可以采用其他不同于在此描述的其他方式来实施,因此,本发明的保护范围并不受下面公开的具体实施例的限制。
28.针对本技术所提出的技术问题,为保证工件开孔位置的硬度达标,提高工件质量,并且提高淬火效率,减少能量损失,本技术提出一种工件孔热处理装置,图1为本技术一种实施例中热处理装置的结构示意图;图2为本技术一种实施例中工件的结构示意图。
29.参照图1和图2,一种工件孔热处理装置,工件孔11围绕工件1设置,热处理装置包括热处理机构,热处理机构包括底座2、旋转结构3、定位结构4和电磁感应器5;底座2具有加热工位21,旋转结构3与底座2相连,旋转结构3能够带动底座2旋转以使加热工位21旋转;定位结构4包括定位件41,定位件41将工件1固定在加热工位21;电磁感应器5具有感应部51,沿加热工位21的旋转方向,感应部51位于加热工位21一侧,感应部51绕有感应线圈;当工件1固定于加热工位21时,向感应线圈通入电流,并且通过旋转结构3带动加热工位21旋转,使得感应部51依次对所有工件孔11周围的表面进行电磁感应加热。
30.由上,在对工件1进行热处理时,首先通过定位件41将工件1固定在热处理工位上,减小工件1在热处理过程中由于定位不可靠造成热处理位置存在偏差的可能性,为工件孔11的位置能够对准提供保障,保证工件1质量;然后,通过旋转结构3(例如:旋转电机)带动底座2旋转,以使定位于加热工位21的工件1旋转,使得工件孔11与感应部51互相对应;最后,向感应线圈通入电流,并且通过旋转结构3带动加热工位21旋转,使得感应部51依次对所有工件孔11周围的表面进行电磁感应加热。
31.本领域技术人员应当明白,本技术利用电磁感应原理,具体地,通过在感应线圈的线路中产生高速变化的交变磁场,当磁场磁力线通过金属时,会在金属体内产生交变的电流(即涡流),涡流使金属原子高速无规则运动,从而金属原子之间相互碰撞、摩擦而产生热能,使得含有金属的被加热体自行高速发热,由此可对工件1进行高频淬火热处理,迅速加热工件孔11周围的表面,提高热处理效率。
32.本领域的技术人员应当明白,向感应线圈中通入的电流频率不同,感应线圈产生的交变磁场的强度不同,因此,热处理效果不同,工件1进行热处理后的硬度不同,频率越大,磁场强度越大,加热温度越高,反之,频率越小,磁场强度越小,加热温度越低,因此,在本技术中,可以根据工件孔11的硬度要求选择相应的热处理温度,根据热处理温度选择相
应频率的电源,以向感应线圈通入相应频率的电流,得到满足要求的工件1,作为示例性的实施例,可以采用变压器改变电源的电压以改变频率,由此可以对电源的频率进行相应的选择,示例性的,在热处理装置中,可以通过按键、触摸、遥控等方式对电源的频率进行选择,示例性的,热处理装置可以具有电源频率预选值供用户选择,或者用户能够设定任意值的电源频率。
33.本领域的技术人员应当明白,由于不同工件1的制造精度、工件孔11的数量、工件孔11的排布等结构特征可能不同,并且一次性对工件1的全部工件孔11的周围表面同时进行加热对热处理装置的制造精度要求较高,由此,本技术可以对工件1的工件孔11进行分组,以组为单位对工件孔11进行高频淬火,降低热处理装置的制造精度,降低热处理装置的制造成本,并且可以避免对工件1的全部表面进行热处理,减少能量损失。
34.本领域技术人员应当明白,在热处理时,将热处理温度降低进行二次回火,能够再次提高硬度,且保证耐磨度和抗疲劳度,因此,作为本发明的一种优选方案,示例性的,在进行热处理时,感应部51每次都会对工件孔11周围的表面进行两次电磁感应加热,第一次感应加热的加热功率大于第二次感应加热的加热功率,第一次感应加热的加热时长大于第二次感应加热的加热时长。
35.本领域技术人员应当明白,在进行热处理后,需要对工件1的硬度进行检测,硬度检测方法可以包括维氏硬度法、显微组织法、显微硬度法、硬度法、金相法等方法,示例性的,硬度测量位置可以为每个工件孔11测量多个位置,每个位置测量多层,每层按照梯度法检测硬化层深度,例如,工件1厚度为4mm,每个工件孔11检测3个位置,参照图2,分别为mp1、mp2、mp3,每个检测位置测量3层,每层按照梯度法检测硬化层深度,每个工件孔11热处理后表面硬度大于720hv1,并且层深达到0.5mm~4mm时,工件1合格。示例性的,可以通过对工件孔11进行抽样检测以检测硬度,还可以对工件孔11进行逐个检测。
36.本领域技术人员应当明白,进行热处理后,对工件孔11的检测还可以包括对工件孔11平面度、垂直度、位置度等指标的检测,并且工件孔11不能开裂,例如,工件孔11整个平面度应小于0.25mm,垂直度应小于0.025mm,位置度基准为0.04mm位置度带,位置度应为0.12mm。
37.本领域技术人员应当明白,以上说明中的工件孔11平面度、垂直度、位置度等指标的具体数值均为便于理解而进行的示例性的举例,本实施例中保护范围包括但并不限于上述例举的数值和数值范围。
38.为了保证产品一致性,作为本发明的一种优选方案,示例性的,热处理装置还包括检测机构,检测机构包括依次电性连接的图像识别单元、图像处理单元和控制单元,在进行热处理之前,工件1处于加热工位21时,图像识别单元对工件1图像进行识别并将图像信息数据传输至图像处理单元,图像处理单元对图像信息数据通过算法处理后向控制单元发送图像正反信号,若未正面,热处理机构即开始对工件孔11进行热处理,若为反面即发出警报,由此完成工件1正反面位置的检测。由此,通过检测工件1的正反面以提高工件1热处理时处理工艺的一致性,以保证产品的一致性。作为示例性的实施例,图像识别单元可以包括ccd相机或者cmos相机等图像传感器。
39.为了减少能量损失,提高热处理效果,且保证对工件孔11周围表面进行热处理的位置准确度,避免热处理时出现额外的应力和应变,减少工件孔11开裂的可能性,作为本发
明的一种优选方案,示例性的,感应部51的轮廓形状与工件孔11的轮廓形状对应。由此,工件孔11周围受热处理的表面的轮廓形状与工件孔11的轮廓形状相对应,既保证热处理效果,又能够减少能量损失,且保证了热处理位置准确度。工件孔11周围受热处理的表面的轮廓形状与工件孔11的轮廓形状相对应,能够使工件孔11受热平衡,减小工件孔11开裂的可能性。
40.经过发明人多次实验研究,发明人发现在进行热处理后,工件孔11的硬度中间层可能会出现夹生层,并且工件1的两面受热不均时可能会造成工件孔11开裂,尤其是在仅进行单面热处理的温度过大时,也可能会造成工件孔11容易开裂,因此,为了提高工件1进行热处理时的受热均匀性,减少出现工件孔11中间层出现夹生层的可能性,作为本发明的一种优选方案,示例性的,沿垂直于加热工位21旋转方向的方向,感应部51分布于加热工位21的两侧。由此,能够通过同时对工件孔11两侧的周围表面进行热处理,提高工件孔11的热处理均匀度,有效地避免工件孔11中间层出现夹层,且降低工件孔11发生开裂的可能性,且提高热处理效率。
41.经过发明人多次实验研究,发明人发现工件1较薄时,在进行对工件孔11进行局部的热处理后,容易造成工件1平面度变形大,发明人发现原因之一在于工件1的整体结构设计,因工件1的整体结构设计,若工件孔11分组不当可能也会引起每组工件孔11的平面度之间存在差异,为了补偿平面度,作为本发明的一种优选方案,示例性的,工件1具有多个突出部12,每个突出部12开有两个工件孔11,将相邻两个突出部12上距离最近的两个工件孔11设为为一组;当工件1固定于加热工位21时,沿加热工位21的旋转方向,感应部51依次对每组工件孔11周围的表面进行电磁感应加热。由此,每次都会对相邻突出部12上相邻的工件孔11进行热处理以补偿不同突出部12上工件孔11的平面度差异,以图2为例,热处理顺序可以依次是工件孔a和工件孔b、工件孔c和工件孔d、工件孔e和工件孔f、工件孔g和工件孔h。
42.本领域的技术人员应当明白,图2中工件1的结构形式仅为本技术中工件1的结构形式之一,图2中工件1的结构形式仅为为方便理解而作出的举例,本技术的工件1及工件孔11包括但不局限于图2中工件1和工件孔11的结构设计以及工件孔11的数量和排布方式。
43.本领域技术人员应当明白,在其他因素和条件不变时,感应线圈与工件孔11周围表面的间隙越小,通过工件1的磁场磁力线越多,工件孔11周围表面产生的涡流越大,能够造成工件孔11周围表面的热处理面积越大,热处理面积越大,额外的应力和应变相应的增多,例如,参照图2,mp2对面的位置上可能会产生额外的应力和应变,会直接对工件孔11的周围表面的硬度和形变造成不利影响,为了能够适应不同的工艺要求且保证工件1的质量,作为本发明的一种优选方案,示例性的,电磁感应器5设有第一调节部,第一调节部与感应部51远离加热工位21的一侧连接,用于调节感应部51与加热工位21的距离以调节被加热表面的面积。由此,通过改变感应线圈与工件孔11周围表面的间隙以改变工件孔11周围被加热表面的面积,能够根据不同的工艺要求,将加热面积降到最小范围,减小额外的应力和应变,减小工件孔11发生形变的可能性,且能够保证工件孔11周围表面的硬度要求。示例性的,第一调节部可以为与感应部51连接的调节杆等结构。
44.参照上述说明,同理,在其他因素和条件不变时,感应线圈的线圈间隙越小,通过工件1的磁场磁力线越多,工件孔11周围表面产生的涡流越大,能够造成工件孔11周围表面的热处理面积越大,因此,作为本发明的一种优选方案,示例性的,电磁感应器5还可以设有
第二调节部,第二调节部与感应部51连接,用于调节感应线圈的间隙以调节被加热表面的面积。由此,通过改变感应线圈的线圈间隙以改变工件孔11周围被加热表面的面积,能够根据不同的工艺要求,将加热面积降到最小范围,减小额外的应力和应变,减小工件孔11发生形变的可能性,且能够保证工件孔11周围表面的硬度要求。示例性的,第二调节部可以是在感应部51内部的可以调节间隙的线槽。
45.为了减小工件1在热处理过程中由于定位不可靠造成热处理位置存在偏差的可能性,同时,为了对工件孔11的位置能够对准提供保障,保证工件1质量,作为本发明的一种优选方案,示例性的,工件1具有定位孔13,底座2具有加热工位21的一侧具有销孔,定位件41包括定位销,定位销依次进入定位孔13与销孔以将工件1定位于加热工位21。
46.为了减小工件1在热处理过程中由于定位不可靠造成热处理位置存在偏差的可能性,同时,为了对工件孔11的位置能够对准提供保障,保证工件1质量,作为本发明的一种优选方案,示例性的,定位结构4还包括定位头42,定位头42沿垂直于加热工位21旋转方向的方向移动以使工件1与底座2抵靠从而夹持工件1。参照图1,定位头42可以将工件1夹紧在底座2的加热工位21上。本领域技术人员应当明白,定位头42可以依靠人力驱动也可以为电力驱动、液压驱动或者气动驱动。
47.本领域技术人员应当明白,工件1进行加热后需要进行冷却退火处理以加强硬度,冷却处理方式可以包括空冷、炉冷、水淬、油淬等冷却处理方式,其中,通过冷却水冷却工件1时的冷却面积大,冷却水廉价且冷却能力强,成本低。并且,当工件1在进行冷却处理时,若冷却不均匀,可能会造成工件孔11轮廓和/或垂直度超差严重,可能会造成工件孔11硬度不均匀。因此,作为本发明的一种优选方案,示例性的,热处理装置还包括冷却机构,沿加热工位21的旋转方向,冷却机构位于加热工位21一侧,冷却机构设有冷却喷头6,冷却喷头6的喷孔朝向加热工位21设置;冷却机构工作时,旋转结构3带动加热工位21旋转以冷却所有工件孔11。作为示例性的实施例,在进行冷却处理时,与底座2相连的旋转电机能够带动底座2旋转,以使工件1旋转,使得冷却水能够均匀冷却工件孔11周围的被加热表面。具体的,在进行冷却处理时,工件1与冷却喷头6的相对旋转角度可以为90
°
~360
°
,以此,可以使得工件1表面的每个位置和每个位置的对面位置都能够接触冷却水,进一步使得工件1冷却均匀。
48.本领域技术人员应当明白,通过控制冷却水的温度、压力、流速均可改善冷却效果,减小变形和开裂,获得理想的淬火效果,例如在进行冷却处理时,冷却时间至少为6s,冷却水中淬火液浓度为10%,冷却水温度为30℃,冷却水流量为每分钟5升。以上说明中,冷却时间、淬火液浓度、冷却水流量均为方便理解而做出的举例说明,并不代表本技术的范围,不能以此限制本技术的保护范围。
49.为了使工件1表面能够全面接触冷却水,作为本发明的一种优选方案,示例性的,冷却喷头6至少设有两个,沿垂直于加热工位21旋转方向的方向,冷却喷头6分布于加热工位21的两侧。
50.本领域技术人员应当明白,上述所有示例中的数值和数值范围,只是为了便于理解而进行的示例性的举例,本实施例中保护范围并不限于上述例举的所有示例中的数值和数值范围。
51.本说明书中的各个实施例均采用递进的方式描述,各个实施例之间相同相似的部分互相参见即可,每个实施例重点说明的都是与其他实施例的不同之处。尤其,对于系统实
施例而言,由于其基本相似于方法实施例,所以描述的比较简单,相关之处参见方法实施例的部分说明即可。
52.以上仅为本发明的实施例而已,并不用于限制本发明。对于本领域技术人员来说,本发明可以有各种更改和变化。凡在本发明的精神和原理之内所作的任何修改、等同替换、改进等,均应包含在本发明的权利要求范围之内。