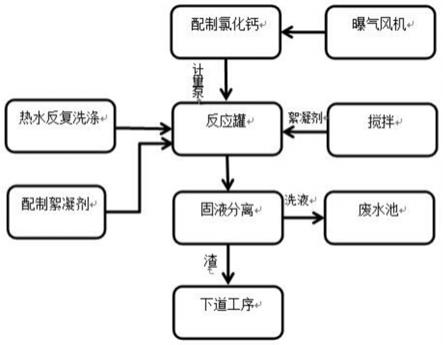
1.本发明涉及稀土湿法冶炼技术领域,特别涉及一种氟碳铈稀土矿冶炼分离中碱转渣固氟的方法。
背景技术:
2.氟碳铈矿是全球稀土产业的主要矿种,具有代表性的矿山主要有美国芒廷帕斯稀土矿山、四川牦牛坪矿山、以及包头白云鄂博混合稀土矿和山东微山湖稀土矿。四川氟碳铈矿氟含量在6%左右,采用“氧化焙烧-盐酸浸出-高温碱转化-水洗压滤-盐酸第二次浸出-浸出液净化除杂-萃取分离-沉淀-煅烧”工艺,其中,碱转渣水洗工序会产生高氟废碱水(即碱转洗液),氟含量在6g/l左右。
3.为了得到符合要求的碱转渣,传统工艺采用热水反复洗涤碱转渣,以去除碱转渣中的f
-
、oh
-
、na
+
等杂质,避免这些杂质影响后续处理工序,特别是f
-
,f
-
的去除效果直接影响后续高价值镨钕的收率,因此需要反复用热水洗涤碱转渣。该水洗工艺需要消耗大量热水,每洗合格一批碱渣需要加水13-15次,耗水量约为75m3/批,且f
-
只能洗到100mg/l左右,大量的时间用来洗涤碱渣限制了水洗岗位的处理能力,且直接影响污水处理成本。
技术实现要素:
4.本发明的发明目的在于:针对上述存在的问题,提供一种氟碳铈稀土矿冶炼分离中碱转渣固氟的方法,本发明通过在洗涤碱转渣至一定程度时,加入氯化钙和絮凝剂来去除洗液中游离的f
-
,将游离的f
-
转换成氟化钙沉淀而存在于碱转渣中,在后续酸溶处理时,作为不溶物被清除,洗液则不断洗涤碱转渣,进而间接提高了洗液的清洗效果,减少了洗涤次数和洗涤用水,在减少水洗成本的同时,加快了水洗工序的生产进度,提高了水洗工段的处理量,提升了稀土湿法冶炼的生产效率。
5.本发明采用的技术方案如下:一种氟碳铈稀土矿冶炼分离中碱转渣固氟的方法,包括如下步骤:
6.s1、对碱转得到的碱转渣进行多次水洗;
7.s2、待水洗至洗液的ph值在9-11时(此时有利于氟化钙的形成,且不易形成氢氧化钙,提高了钙的利用率),以一定的流量向洗液中投加浓度为30-150g/l的氯化钙溶液,并继续洗涤;
8.s3、投加氯化钙溶液后,向洗液中加入絮凝剂进行絮凝沉降处理,过滤后,得到的滤渣另做处理即可。
9.在本发明中,氯化钙溶液的浓度比较关键,发明人在试验中发现,投加的氯化钙溶液浓度如果过高,氯化钙溶液中的ca
2+
会优先与oh
-
结合生成ca(oh)2沉淀,不仅难以有效结合洗液中游离的f
-
,而且形成的ca(oh)2沉淀到下一个酸溶工序时,会被盐酸反溶导致溶液中ca
2+
超标,反而起到负面的效果;相应地,如果投加的氯化钙溶液浓度如果过低,其结合的f
-
较少,不仅不能有效去除洗液中的游离f
-
而导致效果不明显,而且此时产生的caf2沉淀
颗粒细小,易形成胶体体系而增加体系粘度,不易絮凝沉淀下来,分离效果差。通过多次试验尝试得到,当氟化钙溶液的浓度在80-120g/l时,恰好能够规避这些问题,使用效果良好。进一步,确定氯化钙溶液最适宜的浓度后,氯化钙溶液的加入时机也很重要,碱转渣水洗时,随着水洗次数的增加,其含氟量逐渐减少,每次洗后的洗液中含氟量也逐渐减少(每洗涤一次需要更换洗液),如果氯化钙溶液加入过早,由于此时洗液中的含氟量较高,过早投加会产生大量的caf2沉淀,caf2沉淀在盐酸体系下属微溶,大量的caf2沉淀的存在会导致溶于盐酸体系中的f
-
含量较多,进而导致镨钕等高价值稀土损失较高;相应地,如果氯化钙溶液加入过晚,则节省水洗次数以及水洗量的效果不明显,氯化钙的作用效果不能充分体现,达不到明显的节约处理成本的目的。通过多次试验尝试,在洗涤碱转渣时,洗液的ph值在9-11时(随着洗涤次数的增加洗液的ph值逐渐减小),氯化钙除氟效果最佳,该条件下形成的氟化钙颗粒较大,可直接絮凝沉淀,易将其从洗液中分离出,洗液中f
-
的含量可降至100mg/l以下,而且此时产生的caf2沉淀相对碱转渣来说属微量,溶于盐酸体系中的f
-
含量极少,几乎不会对镨钕等高价值稀土造成损失。
10.在本发明中,本发明通过在洗涤碱转渣至一定程度时,加入氯化钙和絮凝剂来去除洗液中游离的f
-
,将游离的f
-
转换成氟化钙沉淀而存在于碱转渣中,在后续酸溶处理时,作为不溶物被清除,洗液则不断洗涤碱转渣,进而间接提高了洗液的清洗效果,减少了洗涤次数和洗涤用水,在减少水洗成本的同时,加快了水洗工序的生产进度,提高了水洗工段的处理量,提升了稀土湿法冶炼的生产效率。
11.在本发明中,作为优选,氯化钙的配制浓度优选为80-120g/l。
12.在本发明中,洗涤碱转渣时,洗涤终点为洗液的ph值为9-11,在该条件下,固氟效果最好,碱转渣无需再进行下一步的洗涤操作,而是直接洗涤后进入下一步酸溶工序中进行处理。
13.进一步,在本发明中,通过试验总结得到,当氯化钙的投加量为ca
2+
与f
-
的质量比为3.28-4.5:1时,洗液中的游离ca
2+
与f
-
反应最充分,f
-
去除效果最好,f
-
可降低至50mg/l,洗液中剩余的ca
2+
含量低于1000mg/l,不会导致后续酸溶时ca
2+
含量超标的问题,镨钕等高价值稀土的损失量被降低至极低水平。
14.进一步,为了更精确的确定氯化钙溶液的加入量,以保证达到上述效果,在步骤s2中,对洗液中的氟含量进行检查,得到氟含量的检测浓度为c1,氯化钙的加入体积v2为:v2=(v1×
c1×n×
(1.1-1.3))/c2,该公式为生产总结得到,其中,v1为碱转洗液体积,c2为氯化钙中钙离子浓度,n为试验比例系数,(1.1-1.3)为过量系数。通过该总结得到的公式能够提前精确确定所加氯化钙溶液的量,进而保证氯化钙溶液的加入量不会过多或过少,保证固氟固氟效果。
15.进一步,在步骤s2中,氯化钙溶液的加入速度为5-15m3/h。
16.在本发明中,所述絮凝剂优选为聚丙烯酰胺。当然,其还可以选择其他絮凝剂,例如非离子絮凝剂等。
17.进一步,所述絮凝剂为阴离子聚丙烯酰胺溶液(根据ph环境要求选择),在该溶液中,阴离子聚丙烯酰胺的质量分数为2-3
‰
,在该ph值及浓度体系条件下,固液分离效果较好。
18.进一步,在s3中,洗液与阴离子聚丙烯酰胺溶液的体积比为45-55:1。
19.在本发明中,待反应体系中形成肉眼可见的矾花时,立即停止搅拌,然后等待沉淀完全再过滤。矾花实质为氟化钙沉淀,在絮凝过程中,通常絮凝成雪花状态,在本技术领域中被称为矾花,矾花形成后应立即停止搅拌,以避免打碎矾花而影响沉淀效果。
20.综上所述,由于采用了上述技术方案,本发明的有益效果是:
21.1、本发明通过在洗涤碱转渣至一定程度时,加入氯化钙和絮凝剂来去除洗液中游离的f
-
,将游离的f
-
转换成氟化钙沉淀而存在于碱转渣中,在后续酸溶处理时,作为不溶物被清除,洗液则不断洗涤碱转渣,进而间接提高了洗液的清洗效果,减少了洗涤次数和洗涤用水,在减少水洗成本的同时,加快了水洗工序的生产进度,提高了水洗工段的处理量,提升了稀土湿法冶炼的生产效率;
22.2、经计算,每5200吨(折reo)稀土精矿处理量将节约6.6万吨水,污水处理成本降低显著,后续酸溶固氟效果好,值得推广应用。
附图说明
23.图1是本发明的一种氟碳铈稀土矿冶炼分离中碱转渣固氟的方法工艺流程示意图。
具体实施方式
24.下面结合附图,对本发明作详细的说明。
25.为了使本发明的目的、技术方案及优点更加清楚明白,以下结合附图及实施例,对本发明进行进一步详细说明。应当理解,此处所描述的具体实施例仅仅用以解释本发明,并不用于限定本发明。
26.如图1所示,一种氟碳铈稀土矿冶炼分离中碱转渣固氟的方法,包括如下步骤:
27.s1、配制浓度为30-150g/l的氯化钙溶液,并用风机曝气均匀,待用;
28.s2、对碱转得到的碱转渣用热水进行多次水洗;
29.s3、待水洗至洗液的ph值在9-11时,以一定的流量向洗液中投加氯化钙溶液,并继续洗涤;
30.s4、配制絮凝剂,待用;
31.s5、投加氯化钙溶液后,向洗液中加入絮凝剂进行絮凝沉降处理,过滤后,得到的滤渣进入下道工序进行处理,滤液(上清液)进入废水池中进行处理。
32.为了更好地说明本发明的创新点,以下列举部分实施例:
33.实施例1
34.一种氟碳铈稀土矿冶炼分离中碱转渣除氟的方法,该方法为:碱转渣在洗涤到一定次数后,往洗涤罐内投加一定浓度的氯化钙溶液,具体步骤如下:
35.步骤一:配制氯化钙溶液,将其体积记为v1,经风机曝气均匀;
36.步骤二:热水洗涤碱转渣,将洗液ph值控制至9;
37.步骤三:检测最后一次洗液中氟的浓度,记为c1,然后加入氯化钙溶液以沉淀氟,加入氯化钙体积v2=(v1×
c1×n×
1.1)/c2,其中,v1为洗液体积,c2为氯化钙中钙离子浓度,n为试验比例系数,1.1为过量系数,氯化钙溶液的加入速度控制在5m3/h;
38.步骤四:向渣浆中加入阴离子型聚丙烯酰胺溶液,将形成的氟化钙细颗粒絮凝成
大颗粒,阴离子型聚丙烯酰胺溶液中阴离子型聚丙烯酰胺的质量浓度为2
‰
,洗液与阴离子型聚丙烯酰胺溶液的体积之比为45:1;
39.步骤五:氟化钙细颗粒絮凝成肉眼可见的矾花时,立即停止搅拌,完全沉淀后过滤,碱转渣进入下道工序。
40.实施例2
41.一种氟碳铈稀土矿冶炼分离中碱转渣除氟的方法,该方法为:碱转渣在洗涤到一定次数后,往洗涤罐内投加一定浓度的氯化钙溶液,具体步骤如下:
42.步骤一:配制氯化钙溶液,将其体积记为v1,经风机曝气均匀;
43.步骤二:热水洗涤碱转渣,将洗液ph值控制至10;
44.步骤三:检测最后一次洗液中氟的浓度,记为c1,然后加入氯化钙溶液以沉淀氟,加入氯化钙体积v2=(v1×
c1×n×
1.2)/c2,其中,v1为洗液体积,c2为氯化钙中钙离子浓度,n为试验比例系数,1.2为过量系数,氯化钙溶液的加入速度控制在12m3/h;
45.步骤四:向渣浆中加入阴离子型聚丙烯酰胺溶液,将形成的氟化钙细颗粒絮凝成大颗粒,阴离子型聚丙烯酰胺溶液中阴离子型聚丙烯酰胺的质量浓度为2.5
‰
,洗液与阴离子型聚丙烯酰胺溶液的体积之比为50:1;
46.步骤五:氟化钙细颗粒絮凝成肉眼可见的矾花时,立即停止搅拌,完全沉淀后过滤,碱转渣进入下道工序。
47.实施例3
48.一种氟碳铈稀土矿冶炼分离中碱转渣除氟的方法,该方法为:碱转渣在洗涤到一定次数后,往洗涤罐内投加一定浓度的氯化钙溶液,具体步骤如下:
49.步骤一:配制氯化钙溶液,将其体积记为v1,经风机曝气均匀;
50.步骤二:热水洗涤碱转渣,将洗液ph值控制至11;
51.步骤三:检测最后一次洗液中氟的浓度,记为c1,然后加入氯化钙溶液以沉淀氟,加入氯化钙体积v2=(v1×
c1×n×
1.3)/c2,其中,v1为洗液体积,c2为氯化钙中钙离子浓度,n为试验比例系数,1.3为过量系数,氯化钙溶液的加入速度控制在15m3/h;
52.步骤四:向渣浆中加入阴离子型聚丙烯酰胺溶液,将形成的氟化钙细颗粒絮凝成大颗粒,阴离子型聚丙烯酰胺溶液中阴离子型聚丙烯酰胺的质量浓度为2
‰
,洗液与阴离子型聚丙烯酰胺溶液的体积之比为55:1;
53.步骤五:氟化钙细颗粒絮凝成肉眼可见的矾花时,立即停止搅拌,完全沉淀后过滤,碱转渣进入下道工序。
54.利用实施例2提供的方法进行了两次生产试验,分别标记为试验
①
和试验
②
,试验
①
和试验
②
的试验结果分别如表1和表2所示:
55.表1试验
①
的试验结果
56.[0057][0058]
表2试验
②
的试验结果
[0059]
名称体积(l)温度(℃)phf-(mg/l)ca
2+
(g/l)反应前洗液500041.5101205/氯化钙溶液20421.25.5/97.5反应后洗液525040.1711.20.54
[0060]
由表1和表2的数据可以得出:试验
①
为氯化钙不足量的除氟反应,其除氟效果一般,试验
②
的氯化钙的量恰好,达到了可观的除氟效果。因此,通过试验
②
计算出,ca
2+
与f
-
的质量消耗比为3.28:1,即每处理1g f
-
需消耗3.28gca
2+
,即小试试验系数n为3.28。
[0061]
实施试验
②
的方法对碱转渣进行处理,增加氯化钙成本58吨*830元=48140元,节约絮凝剂成本13000元/吨*7吨=91000元,节约用水成本1.1元/吨*66000吨=72600元,节约污水处理成本1.16元/吨*66000吨=76560元年,节约环保排污费1.28元/吨*66000吨=84480元,预计年节约成本27.65万元左右,增加精矿处理量1300吨(折reo),具有可观的使用前景。
[0062]
另外,为了说明本发明配制的氯化钙溶液浓度的重要性,按照试验
②
的方法,分别设置试验
③
的氯化钙浓度为150g/l,试验
④
的氯化钙浓度为10g/l,试验结果如表3和表4所示:
[0063]
表3试验
③
的试验结果(氯化钙浓度150g/l)
[0064][0065][0066]
表4试验
④
的试验结果
[0067]
名称体积(l)温度(℃)phf-(mg/l)ca
2+
(g/l)反应前洗液500041.5101205/氯化钙溶液20421.25.5/10反应后洗液525040.17823.40.01
[0068]
由表3和表4可以得到,当氯化钙浓度过高或过低时,其除氟效果均较差,无法达到本发明所声称的技术效果,由此说明,本发明氯化钙的浓度需要在一个适宜的范围内才能达到可观的除氟效果,进而才能解决现有水洗工序处理成本过高的问题。
[0069]
以上所述仅为本发明的较佳实施例而已,并不用以限制本发明,凡在本发明的精
神和原则之内所作的任何修改、等同替换和改进等,均应包含在本发明的保护范围之内。