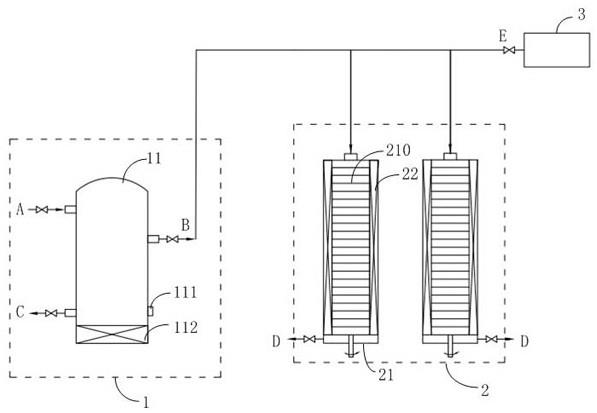
1.本发明涉及石油化工技术领域,特别涉及一种催化裂化油浆中固体颗粒的分离装置及方法。
背景技术:
2.我国催化裂化装置每年副产出大量油浆,当前利用方式经济性差。油浆密度大,相对分子质量大,其中短侧链芳烃含量高,是生产改性沥青、针状焦、炭黑、橡胶软化剂、碳素纤维材料等高附加值化工产品的理想原料。但油浆中固体颗粒含量高,若直接进行二次加工利用,产品性质较差,因此油浆进行高附加值利用的关键是分离出其中的固体颗粒。油浆中固体颗粒粒径较小,多为细粉物质,呈现不规则的块状分布,主要成分包括沸点较高的烃类化合物(焦粉)、无机盐、重金属以及硅铝催化剂细粉(粒径0~80 μm)等。
3.目前,国内外对于催化裂化油浆固体颗粒的分离方法主要包括自然沉降法、过滤分离法、静电分离法以及离心分离法等,其中自然沉降法操作简单,但分离效果差;静电分离法操作费用高,当油浆中胶质、沥青质含量高时分离效率较低,小于20μm的颗粒很难去除;离心分离法利用离心力进行分离,可分离大于10μm的颗粒,但设备投资大、维护难。与之相比过滤法设备简单、投资少、适应性强,因此目前国内外多采用过滤法分离催化裂化油浆中的固体颗粒。油浆过滤技术即通过烧结丝网滤芯和烧结粉末滤芯去除油浆中的固体颗粒,而油浆具有低温高粘度的特点,用于过滤的滤芯容易发生堵塞,必须进行频繁地清洗。
4.cn107617239a公开了一种脱除重质催化裂化油浆中催化剂粉末的方法,在预热的油浆中加入沉降剂,混合均匀后进行超声处理,实现催化剂粉末的脱除。要实现较好的脱除效果,沉降时间需在12 h以上,在实际生产中难以应用。
5.cn109868156a 公开了一种催化裂化油浆过滤装置及方法,催化裂化油浆在油浆原料罐与在两层膜过滤器之间反复循环过滤从而得到净化油浆。所采用的两层膜过滤器滤芯为金属材料膜滤芯,随着过滤的不断进行,固体颗粒在材料膜表面不断沉积形成滤饼,极易造成过滤芯堵塞。
6.磁分离技术是指利用物质间磁势的差异,借助外磁场对物质进行处理,从而达到强化分离过程的一种分离技术。根据外磁场场源的差异可分为永磁分离、电磁分离、超导磁分离。因其快速高效的分离效果,已在尾矿分选、生物技术、水处理、水生态修复等领域得到了广泛的研究和应用。磁分离技术目前还未广泛应用于石油化工领域,更未应用于催化裂化油浆中固体颗粒的分离。考虑到这种固体颗粒的现有技术仍不能高效的进行分离,亟需将磁分离技术应用到该领域,从而既能有效解决现有技术中油浆固体颗粒分离装置设备投资大,流程复杂的问题,又能有效解决现有技术中油浆固体颗粒脱除装置运行过程中过滤设施容易堵塞的问题。
7.公开于该背景技术部分的信息仅仅旨在增加对本发明的总体背景的理解,而不应当被视为承认或以任何形式暗示该信息构成已为本领域一般技术人员所公知的现有技术。
技术实现要素:
8.本发明的目的在于提供一种磁分离催化裂化油浆中固体颗粒的分离装置及方法,利用磁分离器实现对油浆中磁性颗粒的分离,设备投资小,工艺流程简单,同时可有效延长装置的运行周期。
9.为实现上述目的,根据本发明的第一方面,本发明提供一种催化裂化油浆中固体颗粒的分离装置,包括:沉降单元,其主体为沉降罐,沉降罐接收催化裂化油浆和沉降剂的混合进料,在加热的条件下、经磁力作用,使得大粒径的固体颗粒沉降分离;磁分离单元,其主体为分离筒,该分离筒接收来自沉降罐的油浆,该分离筒内设多层聚磁介质,分离筒外设有磁场发生装置,该磁场发生装置相对于分离筒可旋转,通过旋转改变各层所述聚磁介质与磁场方向间的角度,将小粒径的磁性固体颗粒均匀吸附在各层聚磁介质上。
10.进一步,上述技术方案中,分离筒可以为铝制圆筒,聚磁介质可以为不锈钢格栅。格栅的不锈钢丝直径为0.45至0.55mm;不锈钢丝间距为1.5至2.5mm;相邻层所述格栅的间距为10至15mm。
11.进一步,上述技术方案中,相邻层格栅的不锈钢丝延伸方向交错设置。相邻层格栅的不锈钢丝延伸方向的夹角可以为0~90
°
,优选为45
°
。
12.进一步,上述技术方案中,磁场发生装置为永磁体或电磁体。永磁体可以为环形,形成磁场强度为0.6t的水平磁场;环形永磁体与分离筒的相对旋转方向为逆时针旋转,相对转速为2~8 r/min。电磁体可以为磁体外筒,该磁体外筒由铜丝缠绕环状铁芯制成,磁体外筒形成磁场强度为0.6t的水平磁场;磁体外筒与分离筒的相对旋转方向为逆时针旋转,相对转速为2~8 r/min。
13.进一步,上述技术方案中,还可包括冲洗单元,其与分离筒的进料口相连,用于将失去磁吸附力后的小粒径的磁性固体颗粒冲洗至收集罐中。
14.进一步,上述技术方案中,沉降剂可包括絮凝剂、降粘剂和电解质。絮凝剂可为聚乙烯醇、聚乙二醇、聚丙烯酰胺、聚氧丙烯、聚合硅酸盐中的一种或两种以上的组合;降粘剂可为聚丙烯酸高碳酯类;电解质可为脂肪族季铵盐类。絮凝剂的添加量可为油浆质量的500-800 ppm;降粘剂的添加量可为油浆质量的50-100 ppm,电解质的添加量可为油浆质量的200-300 ppm。
15.进一步,上述技术方案中,沉降罐可由不锈钢制成,该沉降罐罐体外部缠绕加热电阻丝;罐体底部设有永磁体,罐体底部两侧设有振动器。沉降罐中的工作温度为90~100
ꢀ°
c;沉降时间为3小时。
16.为实现上述目的,根据本发明的第二方面,本发明还提供了一种催化裂化油浆中固体颗粒的分离方法,该方法通过沉降单元的沉降罐接收催化裂化油浆和沉降剂的混合进料,在加热的条件下、经磁力作用,使得大粒径的固体颗粒沉降分离;通过磁分离单元的分离筒接收来自沉降罐的油浆,使分离筒外部的磁场发生装置相对于分离筒旋转,通过旋转改变各层所述聚磁介质与磁场方向间的角度,将小粒径的磁性固体颗粒均匀吸附在各层聚磁介质上。
17.进一步,上述技术方案中,还可包括冲洗步骤,该冲洗步骤通过冲洗单元将失去磁吸附力后的所述小粒径的磁性固体颗粒冲洗至收集罐中。
18.与现有技术相比,本发明具有如下有益效果:
1)在磁分离之前,对催化裂化油浆进行沉降处理,可有效脱除油浆中的大粒径的固体颗粒,解决了后续磁分离过程中,分离效率低、容易堵塞格栅等问题;2)催化裂化油浆进料之前与沉降剂混合均匀,沉降剂的加入显著缩短了固体颗粒依靠重力自然沉降的时间;沉降罐底部的外加磁体,加速磁性固体颗粒的沉降;3)催化裂化油浆粘度较高,磁分离圆筒中内置分层格栅,且每层格栅不锈钢丝的延伸方向成一角度交错排列,使得油浆通过时不易堵塞;格栅放置在磁场中被磁化,使得磁性颗粒在流动过程中吸附到格栅上,实现了催化裂化油浆中磁性颗粒的分离;4)磁体外筒可以在底部转轴的驱动下旋转,通过磁体的旋转,改变各层格栅不锈钢丝与磁场方向间的角度,使各层格栅交替达到最好的磁场分离状态。在保持不锈钢丝两侧强磁区域存在,防止颗粒直接穿过分离圆筒的同时,又避免了固体颗粒直接停留在上层格栅间而无法再向下流动,避免分离圆筒在没有达到整体吸附饱和的情况下就提前堵塞。
19.上述说明仅为本发明技术方案的概述,为了能够更清楚地了解本发明的技术手段并可依据说明书的内容予以实施,同时为了使本发明的上述和其他目的、技术特征以及优点更加易懂,以下列举一个或多个优选实施例,并配合附图详细说明如下。
附图说明
20.图1是本发明催化裂化油浆中固体颗粒的分离装置连接示意图。
21.图2是本发明磁分离单元中分离筒各层格栅的俯视图(其中2-a至2-d为磁体外筒旋转过程中对应的四层格栅的俯视图)。
22.图3是最佳磁场分离状态下的格栅不锈钢丝延伸方向与磁场方向的夹角示意图。
23.图4是本发明磁分离单元的分离筒中的不锈钢格栅布置示意图。
24.主要附图标记说明:1-沉降单元,11-沉降罐,111-振动器,112-永磁体;2-磁分离单元,21-分离圆筒,210-不锈钢格栅,22-磁体外筒;3-冲洗单元。
25.a-油浆与沉降剂混合进料,b-沉降后上层油浆出料,c-沉降后固体颗粒出料,d-分离筒底部出料,e-冲洗液体进料。
具体实施方式
26.下面结合附图,对本发明的具体实施方式进行详细描述,但应当理解本发明的保护范围并不受具体实施方式的限制。
27.除非另有其他明确表示,否则在整个说明书和权利要求书中,术语“包括”或其变换如“包含”或“包括有”等等将被理解为包括所陈述的元件或组成部分,而并未排除其他元件或其他组成部分。
28.在本文中,为了描述的方便,可以使用空间相对术语,诸如“下面”、“下方”、“下”、“上面”、“上方”、“上”等,来描述一个元件或特征与另一元件或特征在附图中的关系。应理解的是,空间相对术语旨在包含除了在图中所绘的方向之外物件在使用或操作中的不同方向。例如,如果在图中的物件被翻转,则被描述为在其他元件或特征“下方”或“下”的元件将取向在所述元件或特征的“上方”。因此,示范性术语“下方”可以包含下方和上方两个方向。物件也可以有其他取向(旋转90度或其他取向)且应对本文使用的空间相对术语作出相应
的解释。
29.在本文中,术语“第一”、“第二”等是用以区别两个不同的元件或部位,并不是用以限定特定的位置或相对关系。换言之,在一些实施例中,术语“第一”、“第二”等也可以彼此互换。
30.实施例1如图1所示,本发明的催化裂化油浆中固体颗粒的分离装置包括沉降单元1和磁分离单元2。催化裂化油浆经初步沉降将主要为大粒径的固体颗粒分离出来后,油浆继续进入磁分离单元2对小粒径的固体颗粒进行磁性吸附,完成磁分离后的油浆由出口管流入油浆罐中。
31.进一步如图1所示,沉降单元1的主体为一沉降罐11,沉降罐11接收催化裂化油浆和沉降剂的混合进料a,混合进料a经加热和磁力作用,使得大粒径的固体颗粒沉降分离。除沉降罐11外,沉降单元1还包含永磁体112、振动器111及相应的管线。永磁体112位于罐体的底部,振动器111位于罐体底部两侧。优选而非限制性地,沉降罐11由sus304不锈钢制成,该沉降罐11的罐体外部缠绕加热电阻丝,以便为罐体进行加热。永磁体112的最大磁场强度为0.6t,油浆与沉降剂的混合进料a通过进料口进入沉降罐11,大粒径的固体颗粒在重力和沉降剂的作用下发生沉降分离,在沉降剂和底部永磁体112的磁力作用下,沉降过程加速进行,此时大粒径的焦粉、催化剂颗粒和部分磁性微小粒径颗粒沉降到罐体底部。沉降罐11外部缠绕加热电阻丝进行加热升温和保温,维持整个沉降单元温度为在90~100
°
c ,沉降3小时后上层油浆出料b由出料口进入磁分离单元2中,沉降后的固体颗粒出料c由底部出料口排入固体颗粒收集罐中。振动器111可防止固体颗粒沉积在罐体底部,不利于排出,振动器111的振动频率不宜过高,避免影响上层固体颗粒的沉降进程。
32.油浆沉降剂包括絮凝剂、降粘剂和电解质等。絮凝剂为有机或无机聚合物,包括但不限于聚乙烯醇、聚乙二醇、聚丙烯酰胺、聚氧丙烯、聚合硅酸盐中的一种或两种以上的组合,絮凝剂的添加量为油浆质量的500-800ppm。降粘剂为聚丙烯酸高碳酯类,油浆粘度较大,阻碍催化剂颗粒的沉降过程,采用聚丙烯酸高碳酯类可降低油浆粘度,促进催化剂颗粒沉降,降粘剂的添加量为油浆质量的50-100ppm。电解质为脂肪族季铵盐类,加入电解质能够降低颗粒之间的静电斥力,改变表面电荷量和分布,使颗粒易于碰撞结合,电解质的添加量为油浆质量的200-300ppm。
33.进一步如图1所示,磁分离单元2的主体为分离圆筒21,分离圆筒21可以是一个或多个,图1中示意两个。该分离圆筒21接收来自沉降罐11的油浆,即沉降后上层油浆出料b。优选而非限制性地,分离圆筒为铝制材料制成。分离圆筒21内设多层聚磁介质,聚磁介质可采用不锈钢格栅210。本发明的实施例分离圆筒21长为800 mm,壁厚为3 mm,不锈钢格栅210采用sus430不锈钢材质。沉降后上层油浆出料b经降液管流入分离圆筒21中,油浆通过内置的横向分层设置的格栅210,每层格栅具有平行设置的不锈钢丝。优选而非限制性地,相邻层格栅的不锈钢丝延伸方向交错设置。如图4所示,相邻层格栅的不锈钢丝延伸方向的夹角α为0~90
°
,优选为45
°
,即第一层210a的不锈钢丝横向设置,第二层210b倾斜45
°
设置,第三层210c继续倾斜45
°
,不锈钢丝呈竖直设置,第四层210d以此类推。格栅直径为100mm,不锈钢丝直径为0~1mm,优选0.45~0.55 mm;进一步如图4所示,钢丝间距d为 0~6 mm,优选1.5~2.5 mm;格栅相邻层的间距l为0~30mm,优选 10~15mm。采用相邻层格栅的不锈钢丝延伸方向交错设置可更加有效的去除油浆中的磁性颗粒。格栅在分离圆筒21内以一定排列
角度由上至下规整排列,当格栅尺寸、排列角度、排列间隔在上述优选范围区间时不锈钢丝间的相互作用最强,较强的相互作用尽可能地弯曲了空间内的磁力线,导致磁场强度在立面上更广地分布。
34.分离圆筒21外设有磁场发生装置,该磁场发生装置相对于分离圆筒21可旋转,通过旋转改变各层所述聚磁介质与磁场方向间的角度,使各层格栅交替达到最好的磁场分离状态(最佳磁场分离状态参见图3,即当格栅的不锈钢丝的延伸方向与磁场方向的夹角为90
°
时,磁分离效果最好),从而最终将小粒径的磁性固体颗粒更加均匀地吸附在各层聚磁介质上。
35.进一步地,磁场发生装置为一磁体外筒,可采用永磁体或电磁体,如果采用永磁体,永磁体为环形,可形成磁场强度为0.6t的水平磁场;环形永磁体与分离圆筒21的相对旋转方向为逆时针旋转,相对转速为2~8 r/min,优选5~8 r/min。此处环形永磁体与分离圆筒的相对旋转可以采用分离圆筒21静止,环形永磁体旋转的方式;也可以采用环形永磁体静止,分离圆筒21旋转的方式;当然也可两者以一定的速度差旋转。如果采用电磁体,电磁体可以为磁体外筒22(参见图1),该磁体外筒22由铜丝缠绕环状铁芯制成,磁体外筒形成磁场强度为0.6t的水平磁场;磁体外筒与分离筒的相对旋转方向也为逆时针旋转,相对转速也为2~8 r/min,优选5~8 r/min。结合图2、图3,在磁体外筒22旋转过程中,某一层的格栅不锈钢丝的延伸方向与磁场方向的夹角为90度(图2-a的状态),由于各层格栅的交错设置,当磁体外筒22旋转45度时,磁场方向恰好与下一层的不锈钢丝延伸方向的夹角为90度,以此类推,图2-b、图2-c和2-d都是最佳的磁场分离状态。当不锈钢格栅按图4的方式由上至下按一定排列角度进行排列,每层格栅不锈钢丝间存在着强磁区域与弱磁区域。磁体外筒在底部转轴的驱动下旋转,通过磁体的旋转,改变各层格栅不锈钢丝与磁场方向间的角度,使各层格栅交替达到最好的分离状态。在磁体外筒旋转的过程中强磁区域与弱磁区域的相对位置随之改变。当固体颗粒随油浆进入磁分离单元内,由于第一层格栅间弱磁区域的存在,导致部分磁性颗粒通过该区域达到下层格栅的对应位置,若第二层格栅相应的位置此时为强磁区域,磁性颗粒则被吸附,若仍为弱磁区域,穿过第二层格栅的磁性颗粒会被第三层格栅上的强磁区域吸附,以此类推,防止固体颗粒直接穿过分离圆筒的同时,又避免了固体颗粒直接停留在上层格栅间而无法再向下流动。
36.进一步如图1所示,经磁分离单元2对小粒径的磁性固体颗粒进行吸附后,油浆形成分离圆筒底部出料d,流出本发明的装置。进行磁分离处理一段时间后,分离圆筒21内格栅表面随磁分离过程进行,吸附的磁性固体颗粒不断增多,圆筒内外压差不断增大,当增大到一定程度要进行冲洗。冲洗单元3与分离圆筒21的进料口相连,在冲洗阶段,首先关闭油浆进料阀和分离圆筒21底部出口阀。切断磁场发生装置,吸附在格栅表面上的固体颗粒(例如催化剂颗粒),因磁吸附力消失会从表面脱落,打开冲洗液进料阀,冲洗液体进料e进入分离圆筒,冲洗格栅表面固体颗粒,同时打开底部出料阀门,将冲洗下来的磁性固体颗粒引入磁性颗粒收集罐中。
37.实施例2本发明的催化裂化油浆中固体颗粒的分离方法,包括如下步骤:步骤101,通过沉降单元1的沉降罐11接收催化裂化油浆和沉降剂的混合进料,经加热和磁力作用,使得大粒径的固体颗粒沉降分离。维持整个沉降单元温度为在90~100
ꢀ°
c ,
沉降时间3 小时,磁场强度为0.6t。经过沉降步骤,大粒径的焦粉、催化剂颗粒和部分磁性微小粒径颗粒沉降到罐体底部;步骤102,通过磁分离单元2的分离圆筒21接收来自沉降罐11的油浆,驱动分离圆筒外磁场发生装置,使其相对于分离圆筒可旋转,可以在顶部驱动,也可以在底部驱动,通过旋转改变各层聚磁介质与磁场方向间的角度,使各层格栅交替达到最好的磁场分离状态,从而最终将小粒径的磁性固体颗粒更加均匀地吸附在各层聚磁介质上。
38.步骤103,即冲洗步骤。在冲洗阶段,首先关闭油浆进料阀和分离圆筒21底部出口阀。切断电磁发生装置的电源,使得高梯度电磁场消失,吸附在格栅表面上的固体颗粒(例如催化剂颗粒)因磁吸附力消失会从表面脱落,此时冲洗格栅表面固体颗粒,同时打开底部出料阀门,将冲洗下来的磁性固体颗粒引入磁性颗粒收集罐中。
39.前述对本发明的具体示例性实施方案的描述是为了说明和例证的目的。这些描述并非想将本发明限定为所公开的精确形式,并且很显然,根据上述教导,可以进行很多改变和变化。对示例性实施例进行选择和描述的目的在于解释本发明的特定原理及其实际应用,从而使得本领域的技术人员能够实现并利用本发明的各种不同的示例性实施方案以及各种不同的选择和改变。针对上述示例性实施方案所做的任何简单修改、等同变化与修饰,都应落入本发明的保护范围。