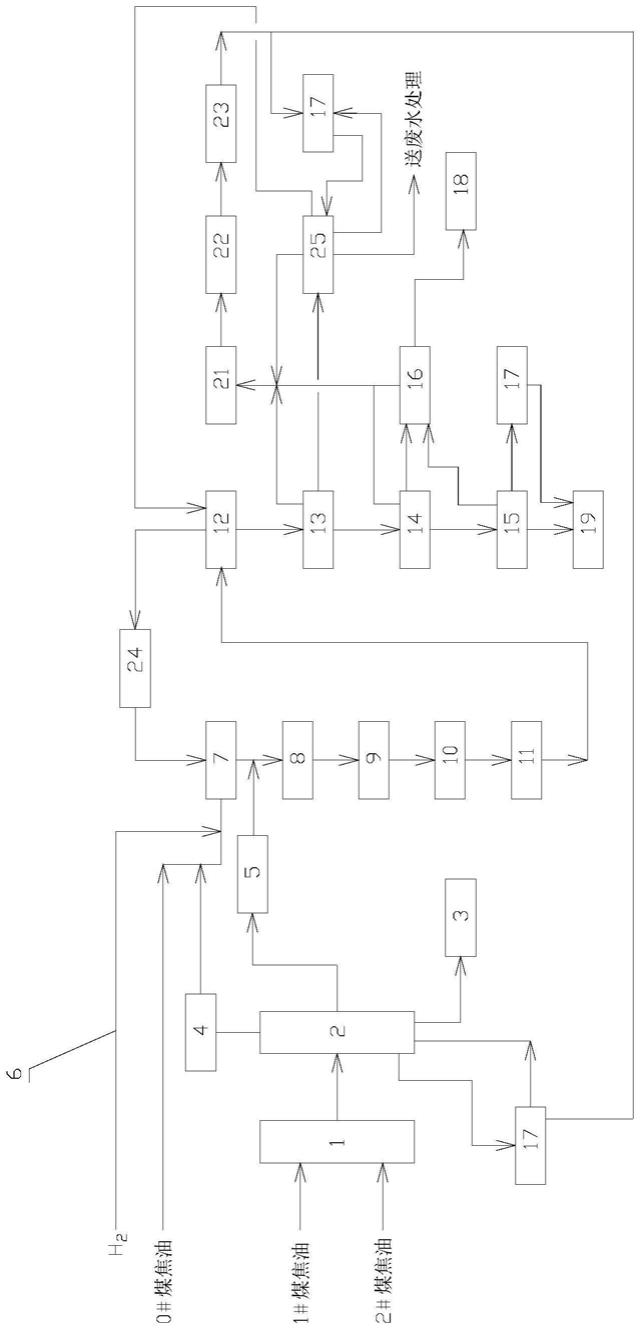
:
1.本实用新型涉及一种煤焦油加氢系统,尤其涉及一种节能高效利用酸性干气的煤焦油加氢系统。
背景技术:
2.我国煤炭储量丰富,以煤为主的多元化能源发展思路已成为我国调整和优化能源结构的重要手段。其中,采用煤热解、炼焦或气化副产的煤焦油通过加氢改质生产汽、柴油及其添加剂技术,可以充分提高煤焦油综合利用价值,解决因煤焦油低值利用而造成的环境污染等问题。
3.原料煤焦油中含有大量的水分、硫、氮、金属盐类等杂质,煤焦油加氢技术首先经过预处理去除水分和重质煤沥青,而后加氢反应脱除煤焦油中硫、氮等对环境产生污染的组分,同时去除金属,将煤焦油中的杂质去除的同时使部分重组分转化为轻组分,生产环境友好的 c1
‑
c4的轻烃、石脑油、煤油、柴油和尾油。
4.但是,传统的煤焦油加氢系统,产生的酸性干气经放空总管送至火炬燃烧排放,一方面由于酸性干气中含有少量甲烷、乙烷、氢气、一氧化碳等可燃气体,其含有一定热值直接放空燃烧造成资源浪费;另一方面酸性干气中含有少量硫化氢,直接外排容易污染环境。
5.此外,煤焦油与氢气在催化剂的作用下加氢反应后,经过多级分离后才能得到合格的产品油,其中在分离器内,不仅甲烷、乙烷、氢气、一氧化碳等气体从分离器顶部排除实现了气液分离,而且液体内也实现分层,底部排出酸性废水,其余产品进入后续系统继续分离以得到最终的合格产品油。其中酸性废水一般通过管道外排送入废水处理系统处理,但是酸性废水中仍然溶解有可燃气体,且低压分离器内主要实现的是气液分离,水和油的分离效果较差,故外排的酸性废水中仍然含有大量的油分,不仅浪费资源,而且后续处理困难。
技术实现要素:
6.为解决上述技术问题,本实用新型的目的在于提供一种节能高效利用酸性干气的煤焦油加氢系统。
7.本实用新型由如下技术方案实施:一种节能高效利用酸性干气的煤焦油加氢系统,包括脱水塔、煤焦油分馏塔、煤沥青罐、中间轻油罐、中间中油罐、新氢管线、第一反应器、第二反应器、第三反应器、第四反应器、第五反应器、高压分离器、低压分离器、预分馏塔、分馏塔、石脑油稳定塔、侧线塔和1#轻质煤焦油罐和2#轻质煤焦油罐,所述脱水塔的下部出口与所述煤焦油分馏塔进口连通,所述煤焦油分馏塔的底部出口与所述煤沥青罐连通,所述煤焦油分馏塔的顶部出口与所述中间轻油罐连通,所述煤焦油分馏塔的上部出口与所述中间中油罐进口连通,所述中间轻油罐的出口以及新氢管线与所述第一反应器的进口连通,所述第一反应器的出口以及所述中间中油罐的出口与所述第二反应器的进口连通,所述第二反应器、第三反应器、第四反应器和第五反应器依次连通,所述第五反应器的
出口与所述高压分离器的进口连通,所述高压分离器的出液口与所述低压分离器的进口连通,所述低压分离器的侧部出液口与所述预分馏塔进口连通,所述预分馏塔的底部出口与所述分馏塔进口连通,所述预分馏塔的顶部出口与所述石脑油稳定塔进口连通,所述分馏塔的塔顶出口与所述石脑油稳定塔连通,所述分馏塔的侧部出口与所述侧线塔的进口连通,所述石脑油稳定塔的出口均与所述1#轻质煤焦油罐连通,所述分馏塔的底部出口以及所述侧线塔的出口均与所述2#轻质煤焦油罐连通;
8.其还包括分液罐、加热炉和脱硫装置,所述分液罐设有进口、顶部出气口、侧部出口和底部出口,所述分液罐的进口与所述低压分离器的底部出口连通,所述分液罐的顶部出口与所述脱硫装置的进口连通,所述分液罐的侧部出口与所述高压分离器的进口连通,所述分液罐的底部出口与废水处理系统连通;
9.所述低压分离器的出气口、所述预分馏塔的顶部出口、所述分馏塔的顶部出口均与所述脱硫装置的进口连通,所述脱硫装置的出口与所述加热炉的炉腔通过管道连通,所述煤焦油分馏塔的塔底通过管线与所述加热炉连通。
10.进一步的,所述脱硫装置包括增压机、脱硫塔和干燥塔,所述低压分离器的出气口、所述预分馏塔的顶部出口、所述分馏塔的顶部出口以及所述分液罐的顶部出口均与所述增压机的进口连通,所述增压机的出口与所述脱硫塔的进气口连通,所述脱硫塔的出气口与所述干燥塔的进口连通,所述干燥塔的出口与所述加热炉的炉腔连通。
11.进一步的,所述高压分离器出气口与循环氢压缩机进口连通,所述循环氢压缩机的出口与所述新氢管线连通。
12.进一步的,在所述分液罐内腔设有盘管,所述盘管的进口与出口均与所述加热炉连通。
13.本实用新型的优点:
14.1、本方案通过将低压分离器、预分馏塔和石脑油稳定塔内得到的酸性干气进行脱硫处理和干燥处理后,送加热炉内燃烧,加热炉为煤焦油分馏塔供热,避免了传统的煤焦油加氢系统中酸性干气放空燃烧造成的资源浪费和环境污染。
15.2、本方案通过将低压分离器内分离出的废水降压加热处理,酸性气体进入脱硫系统脱硫和干燥后送加热炉内燃烧,静置分离后的油回送高压分离器内处理,其余废水再送后续废水处理系统处理,避免了传统酸性废水通过管道外排送入废水处理系统处理造成的造成了资源浪费,节约了生产成本。
附图说明:
16.为了更清楚地说明本实用新型实施例或现有技术中的技术方案,下面将对实施例或现有技术描述中所需要使用的附图作简单地介绍,显而易见地,下面描述中的附图仅仅是本实用新型的一些实施例,对于本领域普通技术人员来讲,在不付出创造性劳动的前提下,还可以根据这些附图获得其他的附图。
17.图1为本实用新型一种节能高效利用酸性干气的煤焦油加氢系统的示意图。
18.图中:脱水塔1、煤焦油分馏塔2、煤沥青罐3、中间轻油罐4、中间中油罐5、新氢管线6、第一反应器7、第二反应器8、第三反应器9、第四反应器10、第五反应器11、高压分离器12、低压分离器 13、预分馏塔14、分馏塔15、石脑油稳定塔16、侧线塔17、1#轻质煤焦油罐18、2#
轻质煤焦油罐19、加热炉20、增压机21、脱硫塔 22、干燥塔23、循环氢压缩机24、分液罐25。
具体实施方式:
19.下面将结合本实用新型实施例中的附图,对本实用新型实施例中的技术方案进行清楚、完整地描述,显然,所描述的实施例仅仅是本实用新型一部分实施例,而不是全部的实施例。基于本实用新型中的实施例,本领域普通技术人员在没有作出创造性劳动前提下所获得的所有其他实施例,都属于本实用新型保护的范围。
20.一种节能高效利用酸性干气的煤焦油加氢系统,包括脱水塔1、煤焦油分馏塔2、煤沥青罐3、中间轻油罐4、中间中油罐5、新氢管线6、第一反应器7、第二反应器8、第三反应器9、第四反应器10、第五反应器11、高压分离器12、低压分离器13、预分馏塔14、分馏塔15、石脑油稳定塔16、侧线塔17和1#轻质煤焦油罐18和2#轻质煤焦油罐19,脱水塔1的下部出口与煤焦油分馏塔2进口连通,煤焦油分馏塔2的底部出口与煤沥青罐3连通,煤焦油分馏塔2的顶部出口与中间轻油罐4连通,煤焦油分馏塔2的上部出口与中间中油罐5进口连通,中间轻油罐4的出口以及新氢管线6与第一反应器7的进口连通,第一反应器7的出口以及中间中油罐5的出口与第二反应器8的进口连通,第二反应器8、第三反应器9、第四反应器10和第五反应器11依次连通,第五反应器11的出口与高压分离器12的进口连通,高压分离器12出气口与循环氢压缩机24进口连通,循环氢压缩机24的出口与新氢管线6连通;高压分离器12的出液口与低压分离器13的进口连通,低压分离器13的侧部出液口与预分馏塔14 进口连通,预分馏塔14的底部出口与分馏塔15进口连通,预分馏塔 14的顶部出口以及分馏塔15的顶部出口均与石脑油稳定塔16进口连通,分馏塔15的侧部出口与侧线塔17的进口连通,石脑油稳定塔 16的出口与1#轻质煤焦油罐18连通,分馏塔15的底部出口以及所述侧线塔17的出口均与2#轻质煤焦油罐19连通;
21.其还包括加热炉20和脱硫装置,脱硫装置包括增压机21、脱硫塔22和干燥塔23,低压分离器13的出气口、预分馏塔14的顶部出口、分馏塔15的顶部出口均与增压机21的进口连通,增压机21的出口与脱硫塔22的进气口连通,脱硫塔22的出气口与干燥塔23的进口连通,干燥塔23的出口与加热炉20的炉腔连通,煤焦油分馏塔 2的塔底通过管线与加热炉20连通,煤焦油分馏塔2内底部的物料送入加热炉20内加热后再返回煤焦油分馏塔2内,实现加热循环。
22.本实施例还包括分液罐25,分液罐25的进口与低压分离器的底部出口连通,分液罐25的顶部出口与增压机21的进口连通,分液罐 25的侧部出口与高压分离器12的进口连通,分液罐25的底部出口与废水处理系统连通;在分液罐25内腔设有盘管,盘管的进口与出口均与加热炉20连通,通过加热炉20为分液罐25内液体加热。
23.工作原理:
24.密度为963.6kg/m3的1#煤焦油和密度为1041.4kg/m3的2#煤焦油经加热到160
‑
168℃送入脱水塔1内,控制脱水塔1底部温度为 130
‑
140℃,脱水塔1顶部排出含油污水,送外部进行处理,脱水塔 1下部的脱水煤焦油送入煤焦油分馏塔2内,由加热炉20加热到 305
‑
310℃,进入煤焦油分馏塔2,煤焦油分馏塔2顶部得到中间轻油,中部得到中间中油,底部得到重质燃料油
‑
煤沥青(1#和2#煤焦油中含有重质油,无法进行加氢反应,需要在前期脱除),中间轻油、0#煤焦油与新氢管线6来的氢气一并送入第一反应器7内,在加氢精制催化
剂轻油处理剂的催化作用下进行加氢反应,第一反应器 7内得到的加氢产物与中间中油罐5内得到的中间中油一并进入第二反应器8进行加氢反应,而后依次送入第三反应器9、第四反应器10 和第五反应器11内,其中第一反应器7中加氢精制催化剂主要型号为hprl
‑
φ1.4;第二反应器8中加氢精制催化剂主要型号为hpm
‑ꢀ
φ1.3;第三反应器9中加氢精制催化剂主要型号为hprh
‑
φ1.4/φ 1.6;第四反应器10加氢精制催化剂主要型号为hp
‑
1.2/φ1.4;第五反应器11中催化剂主要型号为hpt
‑
φ1.2,催化剂厂家全部为萍乡石化填料有限责任公司,煤焦油馏分油在不同加氢精制催化剂的催化作用下进行加氢反应,加氢产物主要成分是烷烃,还包括有环烷烃、单环芳烃、多环芳烃等,加氢产物送入高压分离器12内,控制高压分离器12内压力为16.5mpa,气体(主要成分包括氢气、少量甲烷)经循环氢压缩机24加压到18.0mpa后送第一反应器7内回用;高压分离器12分离后的液体(主要成分包括c5以上烷烃、环烷烃及单环芳烃、多环芳烃等)送入低压分离器13,控制压力为 1.30mpa,侧部排出液体进入预分馏塔14,控制预分馏塔14塔底温度为303℃,塔顶产出温度为176℃的物料进入石脑油稳定塔16,塔底液体进入分馏塔15内,控制分馏塔15底部温度为306℃,塔顶产出温度为176℃的物料进入石脑油稳定塔16,塔侧产出温度为197℃的气体进入侧线塔17,分馏塔15塔底和侧线塔17的塔底得到主要成分为c10以上烷烃、环烷烃及单环芳烃、多环芳烃的2#轻质煤焦油;石脑油稳定塔16得到主要成分为稳定石脑油和重石脑油的1#轻质煤焦油;
25.低压分离器13底部不连续排出酸性废水,酸性废水进入分液罐 25内,压力继续降低到常压,经加热炉20加热到70℃左右,气体从分液罐25顶部排出,油和水静置分离,油从侧部出口排出并送入高压分离器12内进一步分离,废水从底部出口排出,送后续水处理系统处理;分液罐25排出的气体与低压分离器13、预分馏塔14和石脑油稳定塔16的塔顶气体一并经增压机21增压后送入脱硫塔22 内,脱硫塔22内采用湿法脱硫,脱硫剂为碱液,经湿法脱硫后的气体送入干燥塔23内脱水干燥,而后送入加热炉20内燃烧,充分利用了其热值。
26.以上所述仅为本实用新型的较佳实施例而已,并不用以限制本实用新型,凡在本实用新型的精神和原则之内,所作的任何修改、等同替换、改进等,均应包含在本实用新型的保护范围之内。