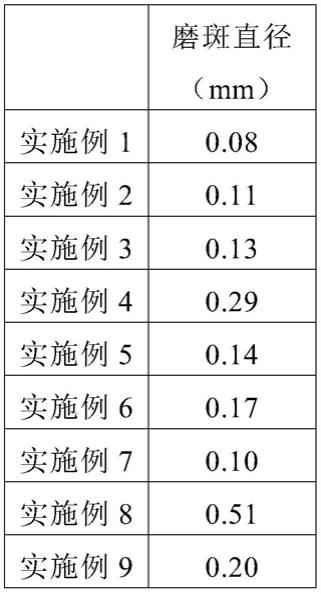
1.本发明涉及生物降解润滑油技术领域,具体涉及环保生物降解润滑油及其制备工艺。
背景技术:
2.现如今,人们的环保意识和危机意识已经有了极大的提高,面对生产、使用及后续无害处理润滑油所可能产生的渗透、泄漏、溢出和处理不当而造成的环境污染破坏问题,相关行业从业者们不得不通过技术创新和改造来解决这一难题。因此,具有生物降解能力的环境友好型润滑油势必将取代现有技术所采用的传统润滑油。现在,市面上绝大多数的润滑油虽然具有高品质和较长的服役寿命,但这些由传统技术所制得的润滑油往往对生态环境不够友好,常常造成巨大的环境灾害,后患无穷。不仅如此,虽然现在市面上出现了少量环境友好型、可生物降解的润滑油,但它们的性能水平还仍然未能满足市场和消费者们的需求。现在亟待解决的一个难题是如何高效、安全地生产出可以自然降解并且其力学、物化性能不会明显下降甚至能够超越传统技术的新型环境友好型的可降解润滑油。
3.棉籽油、棕榈油、蓖麻油是廉价易得、安全环保无污染的常用工业用油,但是,在现有技术中尚未有能够充分利用棉籽油、棕榈油、蓖麻油并将其应用在可以生物降解的润滑油的技术与相关研究报道。
4.专利cn107629847a公开了一种生态环保型润滑油及其制备工艺,以植物油、聚甲基丙烯酸酯、高分子无灰分散剂、石墨纳米粉为原料,但其所得润滑油的生物降解率未能满足现今市场需求,而且也未解决耐磨性和高温服役环境下氧化安定性和蒸发损失的问题。
技术实现要素:
5.针对上述现有技术中存在的不足,本发明提供了环保生物降解润滑油及其制备工艺。
6.棉籽油、棕榈油、蓖麻油是廉价易得、安全环保无污染的常用工业用油,但是,在现有技术中尚未有能够充分利用棉籽油、棕榈油、蓖麻油并将其应用在可以生物降解的润滑油的技术与相关研究报道。
7.为解决上述技术问题,本发明采用的技术方案是:
8.环保生物降解润滑油,由以下原料组成:变性基底油、分散剂、抗氧化剂、抗磨剂、消泡剂、粘度调节剂。
9.作为一种优选的方案,环保生物降解润滑油,由以下重量份的原料组成:90
‑
120重量份变性基底油、0.01
‑
0.05重量份分散剂、0.1
‑
2重量份抗氧化剂、0.5
‑
4重量份抗磨剂、0.01
‑
0.03重量份消泡剂、1
‑
3.5重量份粘度调节剂。
10.所述分散剂为丁二酰亚胺和/或丁二酸乙二醇聚酯。
11.作为一种优选的方案,所述分散剂为丁二酰亚胺、丁二酸乙二醇聚酯以质量比(1
‑
3):(1
‑
3)组成的混合物。
12.所述抗氧化剂为n
‑
乙基
‑1‑
萘胺和/或2,5
‑
二苯基对苯二酚。
13.作为一种优选的方案,所述抗氧化剂为n
‑
乙基
‑1‑
萘胺、2,5
‑
二苯基对苯二酚以质量比(1
‑
3):(1
‑
3)组成的混合物。
14.所述抗磨剂为三(壬基酚)亚磷酸酯和/或硫基双(十二烷基酚)钙盐。
15.作为一种优选的方案,所述抗磨剂为三(壬基酚)亚磷酸酯、硫基双(十二烷基酚)钙盐以质量比5:2.2组成的混合物。
16.所述消泡剂为乙二醇二甲基丙烯酸酯和/或新戊二醇二丙烯酸酯。
17.作为一种优选的方案,所述消泡剂为乙二醇二甲基丙烯酸酯、新戊二醇二丙烯酸酯以质量比(1
‑
6):(1
‑
6)组成的混合物。
18.作为一种优选的方案,所述粘度调节剂为盐酸羟胺。
19.由本发明特定方法制得的变性基底油与所采用的特定分散剂、抗氧化剂、抗磨剂、消泡剂、粘度调节剂所组成的混合体系之间彼此协调,具有良好的适配性和相容度,在彼此皆能充分发挥各自应有功效的同时不会存在彼此削弱的问题,各原料之间相辅相成。
20.所述环保生物降解润滑油的制备工艺为:按原料配方将变性基底油、分散剂、抗氧化剂、抗磨剂、消泡剂、粘度调节剂混合并均质后,得到所述环保生物降解润滑油。
21.作为一种优选的方案,所述环保生物降解润滑油的制备工艺为:按原料配方将变性基底油、分散剂、抗氧化剂、抗磨剂、消泡剂、粘度调节剂混合并均质后,得到所述环保生物降解润滑油;所述均质的条件为,压力大小为160
‑
180mpa,温度为145
‑
170℃、时长为20
‑
40min。
22.所述变性基底油的制备工艺为:
23.f1将基底油、醋酸钠水溶液混合,均质,得到中间产物a;
24.f2将所述中间产物a、吸水剂混合并搅拌,然后离心,过滤取液相,得到中间产物b;
25.f3将所述中间产物b、变性剂、羧酸酯混合,得到变性基底油。
26.本发明采用醋酸钠的水溶液,通过高压均质手段,充分去除了棉籽油、蓖麻油、棕榈油的混合物中游离的氢离子,这有利于后续处理中采用特定变性剂对所述混合物进行改性,因为氢离子会与六羟基铂酸钠中的羟基发生反应;并且,通过醋酸根与高压均质还可以增大该混合油相的均一度,这可以增强所述润滑油在服役时的可靠性。
27.作为一种优选的方案,所述变性基底油的制备工艺为:
28.f1将基底油、浓度为8
‑
13wt.%的醋酸钠水溶液以质量比1:(0.5
‑
2)混合,在70
‑
85℃以大小为45
‑
55mpa的压力均质15
‑
25min,得到中间产物a;
29.f2将所述中间产物a、吸水剂以质量比(6
‑
9):1混合并在45
‑
60℃以100
‑
300rpm的转速搅拌30
‑
50min,然后以8000
‑
12000rpm的转速离心3
‑
6min,过滤取液相,得到中间产物b;
30.f3将所述中间产物b、变性剂、羧酸酯以质量比(11
‑
13):(0.5
‑
0.9):(2.2
‑
2.8)混合,然后在135
‑
155℃、压力为190
‑
225mpa、转速为30
‑
80rpm的条件下处理70
‑
90min,得到变性基底油。
31.所述基底油为棉籽油、蓖麻油、棕榈油中的至少两种。
32.作为一种优选的方案,所述基底油为棉籽油、蓖麻油、棕榈油以质量比(1
‑
7):(1
‑
6):(1
‑
5)组成的混合物。
33.作为一种优选的方案,所述吸水剂为硅胶。
34.本发明采用硅胶去除前述步骤所引入的水分,同时也不会引入如常规吸水剂,即无水氯化钙,所会引入的氯离子,氯离子的存在将削弱后续加入的辛基苯氧基聚乙氧基乙基磷酸酯的反应活性。
35.所述变性剂为辛基苯氧基聚乙氧基乙基磷酸酯和/或六羟基铂酸钠。
36.作为一种优选的方案,所述变性剂为辛基苯氧基聚乙氧基乙基磷酸酯、六羟基铂酸钠以质量比(1
‑
3):(1
‑
3)组成的混合物。
37.辛基苯氧基聚乙氧基乙基磷酸酯的拓扑分子极性表面积和可旋转化学键数、六羟基铂酸钠的氢键受体数量和核心铂离子的电负性,使得它们复配作为所述基底油的变性剂时可以在所述羧酸酯的引发下改变所述基底油的分子空间构型,此微观层面的变动可以导致润滑油宏观力学、生化性能的提高:在提高所述润滑油常温耐磨性的同时提高其在高温环境下的抗氧化能力和耐蒸发性能,并且仍有非常好的生物降解率。
38.作为一种最优选的方案,所述变性剂为辛基苯氧基聚乙氧基乙基磷酸酯、六羟基铂酸钠以质量比2:1组成的混合物。
39.所述羧酸酯为双(2
‑
乙氧基乙基)癸二酸酯、壬二酸二辛酯、癸二酸二异辛酯中的至少一种。
40.本发明所采用的双(2
‑
乙氧基乙基)癸二酸酯、壬二酸二辛酯、癸二酸二异辛酯所具有的有机相浸润力和碳氧键的键能可以降低所述变性剂与所述基底油之间的反应难度,由此可以获得改性程度更充分的变性基底油。
41.作为一种优选的方案,所述羧酸酯为双(2
‑
乙氧基乙基)癸二酸酯、壬二酸二辛酯、癸二酸二异辛酯以质量比7:2:1.3组成的混合物。
42.本发明的有益效果:
43.1、本发明提供了一种环保生物降解润滑油及其制备工艺,得到了耐磨、耐蒸发、易降解,并且具有良好氧化安定性的环保生物降解润滑油。
44.2、本发明提供了一种可以变性基底油及其制备工艺,可用于制备可生物降解的润滑油,采用辛基苯氧基聚乙氧基乙基磷酸酯、六羟基铂酸钠作为变性剂,在双(2
‑
乙氧基乙基)癸二酸酯、壬二酸二辛酯、癸二酸二异辛酯的环境下可以改变由棉籽油、棕榈油、蓖麻油的分子空间排列情况,从而获得更好的宏观力学、生化性能。
具体实施方式
45.下面结合具体实施方式对本发明上述发明内容作进一步详细描述,但不应将其理解为本发明上述主题的范围仅限于下述实施例。
46.本技术中的部分原料介绍:
47.实施例中的丁二酰亚胺,cas:123
‑
56
‑
8,来源:湖北鑫润德化工有限公司。
48.实施例中的丁二酸乙二醇聚酯,cas:25569
‑
53
‑
3,来源:上海迈瑞尔化学技术有限公司,分子量:8300。
49.实施例中的n
‑
乙基
‑1‑
萘胺,cas:118
‑
44
‑
5,来源:百灵威科技有限公司。
50.实施例中的2,5
‑
二苯基对苯二酚,cas:5422
‑
91
‑
3,来源:湖北鑫润德化工有限公司。
51.实施例中的三(壬基酚)亚磷酸酯,cas:26523
‑
78
‑
4,来源:百灵威科技有限公司。
52.实施例中的硫基双(十二烷基酚)钙盐,cas:26998
‑
97
‑
0,来源:湖北鑫润德化工有限公司。
53.实施例中的乙二醇二甲基丙烯酸酯,cas:97
‑
90
‑
5,来源:天门恒昌化工有限公司。
54.实施例中的新戊二醇二丙烯酸酯,cas:2223
‑
82
‑
7,来源:上海迈瑞尔化学技术有限公司。
55.实施例中的盐酸羟胺,cas:5470
‑
11
‑
1,来源:湖北万得化工有限公司。
56.实施例中的棉籽油,cas:8001
‑
29
‑
4,来源:湖北云镁科技有限公司,凝固点:5℃,相对密度(5/15℃):0.925,碘值:109,皂化值:192,符合gb/t1537
‑
2019规定。
57.实施例中的蓖麻油,cas:8001
‑
79
‑
4,来源:邯郸丛台区资旺化工贸易有限公司,符合gb/t 8234
‑
2009规定。
58.实施例中的棕榈油,cas:8002
‑
75
‑
3,来源:济南富鸿化工有限公司,折射率:1.455,符合gb 15680
‑
2009规定。
59.实施例中的硅胶,cas:112926
‑
00
‑
8,来源:武汉华翔科洁生物技术有限公司,堆积密度:740g/l,比表面积(mm2/g)≥600,作用:吸水。
60.实施例中的辛基苯氧基聚乙氧基乙基磷酸酯,cas:52623
‑
95
‑
7,来源:湖北实顺生物科技有限公司,分子量:3700。
61.实施例中的六羟基铂酸钠,cas:12325
‑
31
‑
4,来源:湖北实顺生物科技有限公司。
62.实施例中的双(2
‑
乙氧基乙基)癸二酸酯,cas:624
‑
10
‑
2,来源:百灵威科技有限公司。
63.实施例中的壬二酸二辛酯,cas:103
‑
24
‑
2,来源:上海迈瑞尔化学技术有限公司。
64.实施例中的癸二酸二异辛酯,cas:122
‑
62
‑
3,来源:上海迈瑞尔化学技术有限公司。
65.实施例1
66.环保生物降解润滑油,由以下重量份的原料组成:100重量份变性基底油、0.02重量份分散剂、1重量份抗氧化剂、3重量份抗磨剂、0.01重量份消泡剂、2.5重量份粘度调节剂。
67.所述分散剂为丁二酰亚胺、丁二酸乙二醇聚酯以质量比1:1组成的混合物。
68.所述抗氧化剂为n
‑
乙基
‑1‑
萘胺、2,5
‑
二苯基对苯二酚以质量比3:2组成的混合物。
69.所述抗磨剂为三(壬基酚)亚磷酸酯、硫基双(十二烷基酚)钙盐以质量比5:2.2组成的混合物。
70.所述消泡剂为乙二醇二甲基丙烯酸酯、新戊二醇二丙烯酸酯以质量比5:1组成的混合物。
71.所述粘度调节剂为盐酸羟胺。
72.所述环保生物降解润滑油的制备工艺为:按原料配方将变性基底油、分散剂、抗氧化剂、抗磨剂、消泡剂、粘度调节剂混合并均质后,得到所述环保生物降解润滑油;所述均质的条件为,压力大小为175mpa,温度为150℃、时长为25min。
73.所述变性基底油的制备工艺为:
74.f1将基底油、浓度为12wt.%的醋酸钠水溶液以质量比1:1混合,在80℃以大小为50mpa的压力均质20min,得到中间产物a;
75.f2将所述中间产物a、吸水剂以质量比7:1混合并在50℃以200rpm的转速搅拌40min,然后以10000rpm的转速离心3min,过滤取液相,得到中间产物b;
76.f3将所述中间产物b、变性剂、羧酸酯以质量比12:0.7:2.7混合,然后在150℃、压力为200mpa、转速为50rpm的条件下处理80min,得到变性基底油。
77.所述基底油为棉籽油、蓖麻油、棕榈油以质量比4:1:1组成的混合物。
78.所述吸水剂为硅胶。
79.所述变性剂为辛基苯氧基聚乙氧基乙基磷酸酯、六羟基铂酸钠以质量比2:1组成的混合物。
80.所述羧酸酯为双(2
‑
乙氧基乙基)癸二酸酯、壬二酸二辛酯、癸二酸二异辛酯以质量比7:2:1.3组成的混合物。
81.实施例2
82.与实施例1基本相同,区别在于:
83.所述变性基底油的制备工艺为:
84.f1将基底油、浓度为12wt.%的醋酸钠水溶液以质量比1:1混合,在80℃以大小为50mpa的压力均质20min,得到中间产物a;
85.f2将所述中间产物a、吸水剂以质量比7:1混合并在50℃以200rpm的转速搅拌40min,然后以10000rpm的转速离心3min,过滤取液相,得到中间产物b;
86.f3将所述中间产物b、变性剂、羧酸酯以质量比12:0.7:2.7混合,然后在150℃、压力为200mpa、转速为50rpm的条件下处理80min,得到变性基底油。
87.所述基底油为棉籽油、蓖麻油、棕榈油以质量比4:1:1组成的混合物。
88.所述吸水剂为硅胶。
89.所述变性剂为辛基苯氧基聚乙氧基乙基磷酸酯。
90.所述羧酸酯为双(2
‑
乙氧基乙基)癸二酸酯、壬二酸二辛酯、癸二酸二异辛酯以质量比7:2:1.3组成的混合物。
91.实施例3
92.与实施例1基本相同,区别在于:
93.所述变性基底油的制备工艺为:
94.f1将基底油、浓度为12wt.%的醋酸钠水溶液以质量比1:1混合,在80℃以大小为50mpa的压力均质20min,得到中间产物a;
95.f2将所述中间产物a、吸水剂以质量比7:1混合并在50℃以200rpm的转速搅拌40min,然后以10000rpm的转速离心3min,过滤取液相,得到中间产物b;
96.f3将所述中间产物b、变性剂、羧酸酯以质量比12:0.7:2.7混合,然后在150℃、压力为200mpa、转速为50rpm的条件下处理80min,得到变性基底油。
97.所述基底油为棉籽油、蓖麻油、棕榈油以质量比4:1:1组成的混合物。
98.所述吸水剂为硅胶。
99.所述变性剂为六羟基铂酸钠。
100.所述羧酸酯为双(2
‑
乙氧基乙基)癸二酸酯、壬二酸二辛酯、癸二酸二异辛酯以质
量比7:2:1.3组成的混合物。
101.实施例4
102.与实施例1基本相同,区别在于:
103.所述变性基底油的制备工艺为:
104.f1将基底油、浓度为12wt.%的醋酸钠水溶液以质量比1:1混合,在80℃以大小为50mpa的压力均质20min,得到中间产物a;
105.f2将所述中间产物a、吸水剂以质量比7:1混合并在50℃以200rpm的转速搅拌40min,然后以10000rpm的转速离心3min,过滤取液相,得到中间产物b;
106.f3将所述中间产物b、羧酸酯以质量比12:2.7混合,然后在150℃、压力为200mpa、转速为50rpm的条件下处理80min,得到变性基底油。
107.所述基底油为棉籽油、蓖麻油、棕榈油以质量比4:1:1组成的混合物。
108.所述吸水剂为硅胶。
109.所述羧酸酯为双(2
‑
乙氧基乙基)癸二酸酯、壬二酸二辛酯、癸二酸二异辛酯以质量比7:2:1.3组成的混合物。
110.实施例5
111.与实施例1基本相同,区别在于:
112.所述变性基底油的制备工艺为:
113.f1将基底油、浓度为12wt.%的醋酸钠水溶液以质量比1:1混合,在80℃以大小为50mpa的压力均质20min,得到中间产物a;
114.f2将所述中间产物a、吸水剂以质量比7:1混合并在50℃以200rpm的转速搅拌40min,然后以10000rpm的转速离心3min,过滤取液相,得到中间产物b;
115.f3将所述中间产物b、变性剂以质量比12:0.7混合,然后在150℃、压力为200mpa、转速为50rpm的条件下处理80min,得到变性基底油。
116.所述基底油为棉籽油、蓖麻油、棕榈油以质量比4:1:1组成的混合物。
117.所述吸水剂为硅胶。
118.所述变性剂为辛基苯氧基聚乙氧基乙基磷酸酯、六羟基铂酸钠以质量比2:1组成的混合物。
119.实施例6
120.与实施例1基本相同,区别在于:
121.所述变性基底油的制备工艺为:
122.f1将基底油、浓度为12wt.%的醋酸钠水溶液以质量比1:1混合,在80℃以大小为50mpa的压力均质20min,得到中间产物a;
123.f2将所述中间产物a、吸水剂以质量比7:1混合并在50℃以200rpm的转速搅拌40min,然后以10000rpm的转速离心3min,过滤取液相,得到中间产物b;
124.f3将所述中间产物b、变性剂、羧酸酯以质量比12:0.7:2.7混合,然后在150℃、压力为200mpa、转速为50rpm的条件下处理80min,得到变性基底油。
125.所述基底油为棉籽油、蓖麻油、棕榈油以质量比4:1:1组成的混合物。
126.所述吸水剂为无水氯化钙。
127.所述变性剂为辛基苯氧基聚乙氧基乙基磷酸酯、六羟基铂酸钠以质量比2:1组成
的混合物。
128.所述羧酸酯为双(2
‑
乙氧基乙基)癸二酸酯、壬二酸二辛酯、癸二酸二异辛酯以质量比7:2:1.3组成的混合物。
129.实施例7
130.与实施例1基本相同,区别在于:
131.所述变性基底油的制备工艺为:
132.f1将基底油、水以质量比1:1混合,在80℃以大小为50mpa的压力均质20min,得到中间产物a;
133.f2将所述中间产物a、吸水剂以质量比7:1混合并在50℃以200rpm的转速搅拌40min,然后以10000rpm的转速离心3min,过滤取液相,得到中间产物b;
134.f3将所述中间产物b、变性剂、羧酸酯以质量比12:0.7:2.7混合,然后在150℃、压力为200mpa、转速为50rpm的条件下处理80min,得到变性基底油。
135.所述基底油为棉籽油、蓖麻油、棕榈油以质量比4:1:1组成的混合物。
136.所述吸水剂为硅胶。
137.所述变性剂为辛基苯氧基聚乙氧基乙基磷酸酯、六羟基铂酸钠以质量比2:1组成的混合物。
138.所述羧酸酯为双(2
‑
乙氧基乙基)癸二酸酯、壬二酸二辛酯、癸二酸二异辛酯以质量比7:2:1.3组成的混合物。
139.实施例8
140.环保生物降解润滑油,由以下重量份的原料组成:100重量份基底油、0.02重量份分散剂、1重量份抗氧化剂、3重量份抗磨剂、0.01重量份消泡剂、2.5重量份粘度调节剂。
141.所述基底油为棉籽油、蓖麻油、棕榈油以质量比4:1:1组成的混合物。
142.所述分散剂为丁二酰亚胺、丁二酸乙二醇聚酯以质量比1:1组成的混合物。
143.所述抗氧化剂为n
‑
乙基
‑1‑
萘胺、2,5
‑
二苯基对苯二酚以质量比3:2组成的混合物。
144.所述抗磨剂为三(壬基酚)亚磷酸酯、硫基双(十二烷基酚)钙盐以质量比5:2.2组成的混合物。
145.所述消泡剂为乙二醇二甲基丙烯酸酯、新戊二醇二丙烯酸酯以质量比5:1组成的混合物。
146.所述粘度调节剂为盐酸羟胺。
147.所述环保生物降解润滑油的制备工艺为:按原料配方将基底油、分散剂、抗氧化剂、抗磨剂、消泡剂、粘度调节剂混合并均质后,得到所述环保生物降解润滑油;所述均质的条件为,压力大小为175mpa,温度为150℃、时长为25min。
148.实施例9
149.与实施例1基本相同,区别在于:
150.所述变性基底油的制备工艺为:
151.f1将基底油、浓度为12wt.%的醋酸钠水溶液以质量比1:1混合,在80℃以功率为380w、频率为45khz的超声波处理20min,得到中间产物a;
152.f2将所述中间产物a、吸水剂以质量比7:1混合并在50℃以200rpm的转速搅拌
40min,然后以10000rpm的转速离心3min,过滤取液相,得到中间产物b;
153.f3将所述中间产物b、变性剂、羧酸酯以质量比12:0.7:2.7混合,然后在150℃、压力为200mpa、转速为50rpm的条件下处理80min,得到变性基底油。
154.所述基底油为棉籽油、蓖麻油、棕榈油以质量比4:1:1组成的混合物。
155.所述吸水剂为硅胶。
156.所述变性剂为辛基苯氧基聚乙氧基乙基磷酸酯、六羟基铂酸钠以质量比2:1组成的混合物。
157.所述羧酸酯为双(2
‑
乙氧基乙基)癸二酸酯、壬二酸二辛酯、癸二酸二异辛酯以质量比7:2:1.3组成的混合物。
158.测试例1
159.抗磨损性能测试:根据nb/sh/t 0189
‑
2017《润滑油抗磨损性能的测定四球法》测定由本发明各例所得环保生物降解润滑油的抗磨损性能并采用方法一测量实验数据。上紧力矩为50n
·
m;试验油倒入油盒后超过钢球顶部5mm。以条件b为试验条件:温度为75℃,速度为1200r/min,时间为60min,负荷为392n。
160.测试结果如表1所示。
161.表1环保生物降解润滑油的抗磨损性能
[0162][0163]
测试例2
[0164]
氧化安定性测试:根据sh/t 0193
‑
2008《润滑油氧化安定性的测定旋转氧弹法》测定由本发明各例所得环保生物降解润滑油的氧化安定性。实验所用铜丝线圈的外径为45mm,质量为55.6g,延伸高度为40mm。
[0165]
测试结果如表2所示。
[0166]
表2环保生物降解润滑油的氧化安定性
[0167][0168]
测试例3
[0169]
蒸发损失测试:根据nb/sh/t 0059
‑
2010《润滑油蒸发损失的测定诺亚克法》中的a法测定由本发明各例所得环保生物降解润滑油的蒸发损失值。实验温度为250℃,实验时长为1h。
[0170]
测试结果如表3所示。
[0171]
表3环保生物降解润滑油的蒸发损失值
[0172][0173]
[0174]
测试例4
[0175]
生物降解性测试:根据gb/t 21856
‑
2008《化学品快速生物降解性二氧化碳产生试验》测定由本发明各例所得环保生物降解润滑油的生物降解性。试验前10d每天测一次二氧化碳,其后每5d测一次,试验周期共计为28d。
[0176]
测试结果如表4所示。
[0177]
表4环保生物降解润滑油的生物降解性
[0178][0179]
本发明采用醋酸钠的水溶液,通过高压均质手段,充分去除了棉籽油、蓖麻油、棕榈油的混合物中游离的氢离子,这有利于后续处理中采用特定变性剂对所述混合物进行改性,因为氢离子会与六羟基铂酸钠中的羟基发生反应;并且,通过醋酸根与高压均质还可以增大该混合油相的均一度,这可以增强所述润滑油在服役时的可靠性。本发明采用硅胶去除前述步骤所引入的水分,同时也不会引入如常规吸水剂,即无水氯化钙,所会引入的氯离子,氯离子的存在将削弱后续加入的辛基苯氧基聚乙氧基乙基磷酸酯的反应活性。辛基苯氧基聚乙氧基乙基磷酸酯的拓扑分子极性表面积和可旋转化学键数、六羟基铂酸钠的氢键受体数量和核心铂离子的电负性,使得它们复配作为所述基底油的变性剂时可以在所述羧酸酯的引发下改变所述基底油的分子空间构型,此微观层面的变动可以导致润滑油宏观力学、生化性能的提高:在提高所述润滑油常温耐磨性的同时提高其在高温环境下的抗氧化能力和耐蒸发性能,并且仍有非常好的生物降解率。本发明所采用的双(2
‑
乙氧基乙基)癸二酸酯、壬二酸二辛酯、癸二酸二异辛酯所具有的有机相浸润力和碳氧键的键能可以降低所述变性剂与所述基底油之间的反应难度,由此可以获得改性程度更充分的变性基底油。
[0180]
由本发明特定方法制得的变性基底油与所采用的特定分散剂、抗氧化剂、抗磨剂、消泡剂、粘度调节剂所组成的混合体系之间彼此协调,具有良好的适配性和相容度,在彼此皆能充分发挥各自应有功效的同时不会存在彼此削弱的问题,各原料之间相辅相成。