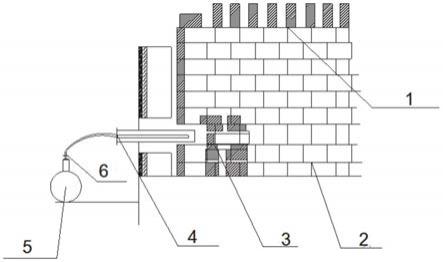
1.本实用新型属于烘炉设备技术领域,具体涉及一种采用正压烘炉技术的焦炉负压烘炉设备。
背景技术:
2.焦炉的烘炉是焦炉开工投产前的一项重要工作,烘炉质量的好坏直接影响到焦炉砌体的寿命。根据不同的情况制订科学合理的烘炉方案,并严格操作规程、加强管理,是保证烘炉质量和安全的重要环节。
3.烘炉就是把已经砌好并安装了护炉设备的冷态焦炉由常温逐步加热到能够装煤的温度。烘炉时需配置烘炉设施,所需热量由燃料供给。烘炉的初期是排出砌体内水分的阶段,称为干燥期,干燥期过后是升温期,达到正常加热(或装煤)的温度时烘炉才算结束。
4.在烘炉过程中砌体各部分应遵循一定的升温曲线升温,应使砌体在一定的水平负荷下升温,避免升温过程中损坏焦炉砌体,破坏砌体的严密性。
5.烘炉时加热气体的流向为:烘炉小灶(或炉门)——炭化室-—烘炉孔——立火道——斜道——蓄热室——小烟道——烟道——烟囱,最后排入大气。
6.目前国内外使用的烘炉技术有负压烘炉和正压烘炉两种工艺。
7.所谓负压烘炉,是指在烘炉前先在焦炉的烟囱里面点燃火炬进行烘烤,使烟囱产生一定的吸力,经过一段时间(一般为10~15天)后,再点燃炭化室内的烘炉烧嘴,燃烧室管理火道温度在250~300℃前,燃烧室看火孔压力为负压的烘炉工艺。
8.此工艺为多年成熟的烘炉工艺,目前主要存在的问题有:
9.1)烘炉至300℃前,炭化室为负压操作,从炉门预留的烘炉孔处吸入大量的冷空气参与燃烧,冷空气流经处对炉墙进行了降温,导致上下部膨胀不均匀,甚至出现局部烘炉温度激变造成的炉墙剥蚀;
10.2)烘炉初期炭化室负压,炉顶部分在高温及膨胀作用线产生开裂,冷空气自开裂处吸入炭化室,导致炉体严密性变差,升温不均匀,生产期间漏气严重;
11.3)负压烘炉,炉体燃烧室、斜道及蓄热室三部位膨胀不均匀,易在蓄热室和炉顶部位产生炉体拉裂情况,影响炉体寿命。
12.4)负压烘炉过程中,高温废气在流经斜道、小烟道及开闭器过程中,产生冷凝水,会冲刷焦炉砌体灰缝,腐蚀开闭器铁件;
13.所谓正压烘炉,是用采用炉外燃烧设备,煤气和空气在炉外燃烧设备内燃烧,废气经鼓风机吹入炭化室内的烘炉技术,该烘炉技术不用提前烘烟囱,且炭化室内不用砌筑烘炉火床。
14.该正压烘炉技术主要存在如下问题:
15.1)烘炉费用较高,单座焦炉烘炉,采用国外送风式烧嘴烘炉设备,租赁费很高,采用国内送风式烧嘴烘炉设备,技术服务费和设备租赁费约为国外设备的50%,造价相当高;
16.2)不砌筑烘炉火床,存在火焰控制不好烧坏炉墙的风险;
17.3)烘炉前不烘烟囱,依靠鼓风机将热气流强制吹入焦炉燃烧室立火道,再经蓄热室、烟道排出炉体,大量热气流留存在燃烧室顶部,导致上部膨胀量大,且出现纵向膨胀,造成抵抗墙受力外倾严重;
18.4)单侧安装烘炉设备,容易的导致焦炉横向温度分布不均匀,安装烘炉设备侧温度高,膨胀量大,机焦侧膨胀不均匀。
19.针对常规负压烘炉和正压烘炉,本实用新型重点解决如下问题:
20.1)采用常规负压烘炉设备,不需要安装国内外正压烘炉用的送风式烧嘴,工程造价低,节省投资费用;烘炉设备机焦侧双侧安装,杜绝了单侧燃烧对炉体造成的冷热不均问题;
21.2)烘炉时砌筑烘炉火床,对炉体进行保护;
22.3)焦炉烘炉前在烟囱安装烘炉用火炬,烘炉前不点燃,不需要对烟囱进行烘烤脱水;
23.4)焦炉烘炉炭化室点火后,控制燃烧室看火孔压力+1~2pa,此时炭化室为正压,不会吸入冷空气对炉体降温;
24.5)烘炉过程不会产生冷凝水,对炉体灰缝及铸造件冲刷、腐蚀小;
25.6)烘炉升温均匀,不会在蓄热室、炉顶部位产生拉裂问题,炉体严密无串漏。
技术实现要素:
26.鉴于现有技术中焦炉负压烘炉及正压烘炉中存在的问题,本实用新型的目的在于采用常规负压烘炉设备实现正压烘炉操作,以降低烘炉费用,提高炉体严密性,防止出现燃烧室、蓄热室、小烟道不均匀膨胀而产生的炉顶及蓄热室炉体拉裂问题,延长焦炉的寿命。
27.为实现上述目的,本实用新型采用下述技术方案:一种采用正压烘炉技术的焦炉负压烘炉设备,包括两侧炉门和炭化室,所述两侧炉门均设有烧嘴,烧嘴置于炭化室内,烧嘴通过软管与烘炉煤气主管连接,所述烘炉煤气主管设置在机、焦侧平台上,与焦侧平台左右对称设置机侧平台;所述炭化室内设有分火砖,靠近两侧炉门处设有u字形火床,所述烧嘴中心和分火砖重合,所述火床顶部设有不同间距的均布气流砖;
28.热气流在均布气流砖上进行分布,克服炉头火道烘炉孔大、吸力大造成的热气流多,中心火道热气流少的弊端;
29.为防止同一炭化室两侧燃烧室吸力偏差造成气流紊乱,炭化室内的热量不能均衡的分布在两个燃烧室内,在烘炉火床内设有分火砖,火焰在火床内燃烧时,火焰出口距离分火砖40mm,火焰在分火砖的作用下分成两路,进入不同的燃烧室内;
30.进一步,所述烧嘴通过炉门设置的预留孔固定于炉门上,更进一步,所述固定的方式为螺旋固定;
31.进一步,所述软管为橡胶软管,更进一步,所述橡胶软管长度为1.5m;
32.进一步,所述炭化室内设有烘炉孔;
33.进一步,焦侧平台和机侧平台上的烘炉煤气主管形成反转对称;
34.进一步,所述炭化室两侧设有燃烧室,所述燃烧室通过两个斜道分别连通煤气蓄热室和空气蓄热室,所述煤气蓄热室和空气蓄热室通过烟道与烟囱连接,所述烟囱内设有火炬;更进一步,所述煤气蓄热室和空气蓄热室与烟道之间还设有开闭器,开闭器上设有调
节翻板,所述烟道内设有烟道调节翻板,所述火炬与火炬燃气管道连接,所述火炬燃气管道上还设有调节阀。
35.进一步,所述烟囱的高度不低于2.5m。
36.本实用新型的一个或多个具体实施方式至少取得了以下技术效果:
37.本实用新型采用负压烘炉设备,烘炉费用可以减低约500万元,烘炉期间采用正压烘炉技术,炭化室点火前不烘烤烟囱,炭化室点火后再点燃烟囱内的火炬,让火炬产生吸力诱导作用,将炭化室内的热气流引入烟囱内进行排放;重点是调节调节翻板、烟道翻板调整烟囱内火焰的燃烧强度,炉门处砌筑有烘炉火床对炉体进行保护,控制焦炉炉顶看火孔+1~2pa的压力,在微正压的状态下进行烘炉作业,保证了炉体不会吸入大量冷空气,对炉体降温作用少,炉体不会产生不均匀膨胀。且正压烘炉过程中,焦炉炉体膨胀均匀,不会形成蓄热室和炉顶的阶梯裂缝,同时也不会经由炉顶、蓄热室封墙吸入冷空气,提高了炉体的严密性,延长了焦炉的寿命,规避了常规焦炉负压烘炉,炉顶看火孔
‑
50pa压力下,大量冷空气从焦炉炉门预留烘炉孔、炉顶裂缝处、蓄热室封墙裂缝处吸入冷空气而导致的炉墙拉裂、小烟道出现冷凝水等问题。
附图说明
38.构成本技术的一部分的说明书附图用来提供对本技术的进一步理解,本技术的示意性实施例及其说明用于解释本技术,并不构成对本技术的限定。
39.图1为本实用新型实施例中炭化室的结构示意图;
40.图2为本实用新型实施例中炭化室中烧嘴、分火砖和火床结构示意图;
41.图3为本实用新型实施例中火床和分火砖的结构图;
42.图4为本实用新型实施例中焦炉的结构示意图;
43.图5为本实用新型实施例中气流运动轨迹流程图;
44.图6为本实用新型实施例中整体结构示意图。
45.图中:1、均布气流砖,2、火床,3、分火砖,4、烧嘴,5、烘炉煤气主管,6、孔板,7、炭化室炉墙,8、橡胶软管,9、焦侧平台,10、机侧平台,11、炭化室,12、燃烧室,13、烘炉孔,14、开闭器,15、开闭器调节翻板,16、烟道,17、烟道调节翻板,18、火炬,19、烟囱,20、调节阀,21、火炬燃气管道,22、炉门,23、斜道,24、煤气蓄热室,25、空气蓄热室。
具体实施方式
46.应该指出,以下详细说明都是例示性的,旨在对本技术提供进一步的说明。除非另有指明,本文使用的所有技术和科学术语具有与本技术所属技术领域的普通技术人员通常理解的相同含义。
47.需要注意的是,这里所使用的术语仅是为了描述具体实施方式,而非意图限制根据本技术的示例性实施方式。如在这里所使用的,除非上下文另外明确指出,否则单数形式也意图包括复数形式,此外,还应当理解的是,当在本说明书中使用术语“包含”和/或“包括”时,其指明存在特征、步骤、操作、器件、组件和/或它们的组合。
48.本实用新型的一种典型实施方式中,如图1
‑
6所示,一种采用正压烘炉技术的焦炉负压烘炉设备,包括两侧炉门22和炭化室11,所述两侧炉门22均设有通过炉门设置的预留
孔螺旋固定于炉门上的烧嘴4,烧嘴4置于炭化室内11,通过1.5m的橡胶软管8与烘炉煤气主管5连接,所述烘炉煤气主管5设置在机、焦侧平台9和10上,机侧平台10与焦侧平台9左右对称,机、焦侧平台上的烘炉煤气主管5形成反转对称;所述炭化室11内设有烘炉孔13和分火砖3,火焰出口距离分火砖40mm,靠近两侧炉门22处设有u字形火床2,所述烧嘴4中心和分火砖3重合,所述火床2顶部设有不同间距的均布气流砖1;炭化室11两侧设有燃烧室12,燃烧室12通过两个斜道23分别连通煤气蓄热室24和空气蓄热室25,煤气蓄热室24和空气蓄热室25通过烟道16与设有火炬18的烟囱19连接,烟囱19的高度不低于2.5m,所述煤气蓄热室24和空气蓄热室25与烟道16之间还设有开闭器14,开闭器14上设有调节翻板15,烟道16内设有烟道调节翻板17,火炬18与设有调节阀20的火炬燃气管道21连接。
49.工作原理:焦炉砌筑完成,护炉铁件安装结束后,在焦炉炭化室11内砌筑烘炉专用火床2和分火砖3,并按照负压烘炉的工艺要求机、焦侧安装烘炉煤气主管、烧嘴4及孔板6,旋塞阀门,并在主管路上安装管道至焦炉烟囱19,在烟囱19内安装煤气火炬18,并在火炬进烟囱前安装调节阀门20及测压管、吹扫管放散管等附件。
50.炭化室烘炉点火前1天,1)首先将炉顶装煤孔盖(或导烟孔盖)打开50%开度,倾斜的放置在装煤孔座(或导烟孔座)上,形成由炭化室11直通炉顶的通道。
51.炭化室11点火前,烟道调节翻板17(或烟道闸板)处于关闭位置,废气开闭器上14的废气铊处于关闭位置,废气开闭器14上的调节翻板15根据距离烟囱的距离分3~4段调节好开度。
52.焦炉端墙砌筑不低于2.5米高的烟囱19,端墙烧嘴4燃烧产生的废气经由烟囱排放至大气中。
53.焦炉烘炉烧嘴4点火,机焦侧各点燃一半的烧嘴,且机焦侧不对称点燃(即机侧点单数,焦侧点燃双数烧嘴,或者机侧点燃双数焦侧点燃单数烧嘴)。燃烧产生的废气经由炉顶看火孔、装煤孔(或导烟孔),排放至大气中。
54.2)炭化室11烧嘴点火后,再点燃烟囱内的火炬18,以产生诱导作用。
55.然后将焦炉烟道调节翻板17(或闸板)打开20%开度,提起废气开闭器14上的废气铊至300
㎜
高度。
56.3)同时关闭炉顶上已经打开的装煤孔盖(火导烟孔盖),炭化室11内烧嘴4产生的废气在烟囱火炬18的诱导作用下,经烘炉孔13进入燃烧室12,再经斜23、蓄热室24和25、小烟道16、开闭器14、烟道16导入烟囱19。
57.通过调节4)废气开闭器14上的调节翻板15;
58.5)烟道翻板17或烟道闸板;
59.6)烟囱内火炬18的燃烧强度;
60.使炉顶燃烧室立火道产生+1~2pa的吸力,烘炉期间,在气温变化及外界风力变化时,需要及时测量看火孔压力并及时进行调节,以满足看火孔+1~2pa的压力。此时炭化室内正压烘炉操作,不会产生负压,以防抽入冷空气对炉体降温而损坏。
61.随着炉温的升高,看火孔压力逐步提高,当烟囱19内废气温度达到90℃后,关闭烟囱内的火炬18,依靠废气自身的热浮力,能满足烘炉吸力要求。
62.上述虽然结合附图对本实用新型的具体实施方式进行了描述,但并非对本实用新型保护范围的限制,所属领域技术人员应该明白,在本实用新型的技术方案的基础上,本领
域技术人员不需要付出创造性劳动即可做出的各种修改或变形仍在本实用新型的保护范围以内。