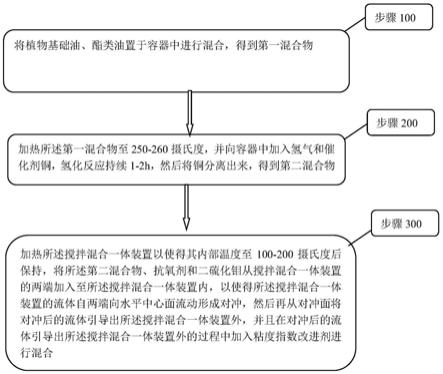
1.本发明涉及润滑油技术领域,具体涉及一种环保型复合润滑油及制备方法。
背景技术:
2.润滑油在设备运转中起着抗磨减摩、冷却和提高效率等不可或缺的关键作用,但是通常与环境的相容性较差。传统矿物润滑油的生物降解性差,若在生产、储运及使用过程中发生泄漏就会污染环境。由于矿物润滑油生物降解性差,加上人们环保意识的增强和国家环保法规的严格,可生物降解润滑油的研究和发展越来越受到人们的重视。
3.目前,可生物降解润滑油已成为绿色化学和绿色工程领域重要的组成部分。可生物降解润滑油是指既能满足机械设备的使用要求,又能在短时间内被活性微生物分解为二氧化碳和水的润滑油,它通常被纳入环境友好润滑剂之列。环境友好润滑剂的性能不仅包括生物降解能力,而且还包括润滑剂的生态毒性。生物降解性和生态毒性是两个不同的方面,有些有毒物质也可生物降解,降解后生成非毒性物质;有些物质降解后的产物比原物质有更强的毒性。环境友好润滑剂既要求生物降解性要好,又要求生态毒性及毒性累积性要小。
4.现有技术中环保型润滑油由于添加大量植物油,而植物油容易发生氧化,导致环保型润滑油寿命较差,可通过增加抗氧化剂解决,例如二硫化钼,二硫化钼即可具有抗氧化剂作用又具有抗磨剂作用,并且毒性极小,是环保型润滑油中一种较好的抗氧化添加剂,但是因此带来的问题是,二硫化钼作为抗氧化剂添加,导致添加的量较大,连同润滑油中的抗磨剂导致润滑油中固体颗粒较多,而固体颗粒容易发生沉降,导致润滑油在制备过程中固体颗粒混合不均匀。
技术实现要素:
5.本发明的目的在于提供一种环保型复合润滑油及制备方法,以解决现有技术中因选用二硫化钼作为抗氧化剂添加至环保型润滑油中,导致导致润滑油中固体颗粒较多,而固体颗粒容易发生沉降,从而使得润滑油中固体颗粒在制备过程中混合不均匀的技术问题。
6.为解决上述技术问题,本发明具体提供下述技术方案:
7.一种环保型复合润滑油,由以下重量份的原料制成:
8.植物基础油500
‑
700份、酯类油80
‑
130份、降凝剂0.1
‑
0.4份、抗氧剂70
‑
160、二硫化钼30
‑
70份、粘度指数改进剂25
‑
55份和石墨抗磨剂5
‑
25份。
9.作为本发明的一种优选方案,所述植物基础油包含菜籽油、玉米胚芽油、大豆油、花生油、葵花籽油、蓖麻油、棕榈油的一种或多种。
10.作为本发明的一种优选方案,所述抗氧剂包含2,4,6
‑
三叔丁基苯酚、2,6
‑
二叔丁基
‑4‑
壬基酚、2,6
‑
二叔丁基对甲酚、异辛基
‑3‑
(3,5二叔丁基
‑
羟基苯基)丙酸酯中的一种或多种的混合物;
11.所述酯类油为三羟甲基丙烷油酸酯,所述降凝剂为聚甲基丙烯酸酯,所述粘度指数改进剂为聚氢化苯乙烯异戊二烯型的粘度指数改进剂。
12.为解决上述技术问题,本发明还进一步提供下述技术方案:
13.一种复合润滑油的制备方法,包括如下步骤:
14.步骤100、将植物基础油、酯类油置于容器中进行混合,得到第一混合物;
15.步骤200、加热所述第一混合物至250
‑
260摄氏度,并向容器中加入氢气和催化剂铜,氢化反应持续1
‑
2h,然后将铜分离出来,得到第二混合物;
16.步骤300、加热所述搅拌混合一体装置以使得其内部温度至100
‑
200摄氏度后保持,将所述第二混合物、抗氧剂和二硫化钼从搅拌混合一体装置的两端加入至所述搅拌混合一体装置内,以使得所述搅拌混合一体装置的流体自两端向水平中心面流动形成对冲,然后再从对冲面将对冲后的流体引导出所述搅拌混合一体装置外,并且在对冲后的流体引导出所述搅拌混合一体装置外的过程中加入粘度指数改进剂进行混合。
17.作为本发明的一种优选方案,所述搅拌混合一体装置包括:
18.反应釜,用于容纳制备复合润滑油的原料,并作为混合反应的容器;
19.流体对冲机构,设置于所述反应釜的两端,所述流体对冲机构用于驱动所述反应釜的两端的流体相对流动,以在所述反应釜的中间水平面上形成对冲面;
20.出料机构,套设于所述反应釜上,所述出料机构用于承接所述对冲面处的流体,并将所述对冲面处的流体引出至所述搅拌混合一体装置外;
21.其中,所述流体对冲机构包括用于驱动相对运动的流体的搅拌组件,设置于所述搅拌组件的两端的第一进料组件,所述第一进料组件用于持续向所述反应釜两端提供相对运动流体的组成物;
22.所述搅拌组件包括驱动机构、第一驱动桨和第二驱动桨,所述第一驱动桨和第二驱动桨对称设置于所述反应釜的内部的两端,所述驱动机构能够向所述第一驱动桨和所述第二驱动桨提供旋转的动力,且所述第一驱动桨和第二驱动桨的旋转方向相反;
23.所述驱动机构包括主动轴和从动轴,所述主动轴和从动轴分别安装于所述第一驱动桨和第二驱动桨上,所述主动轴和从动轴之间通过反向联动组件进行传动连接。
24.作为本发明的一种优选方案,所述反向联动组件包括设置于所述主动轴和从动轴之间的密封中空体,所述密封中空体通过支架安装于所述反应釜内,所述主动轴和从动轴均以自身轴线为中心进行转动地延伸至所述密封中空体的内腔中,所述密封中空体的内腔中镜像设置有两个锥形齿轮,所述主动轴和从动轴分别与两个第一锥形齿轮连接,两个第一锥形齿轮之间设置有第二锥形齿轮,所述第二锥形齿轮的两侧分别与两个所述第一锥形齿轮相啮合,所述第二锥形齿轮以自身轴线为中心进行转动地安装于所述密封中空体的内腔上。
25.作为本发明的一种优选方案,所述出料机构包括:
26.环形管道,套设于所述反应釜上,且其内腔与所述反应釜的内腔相连通;
27.引流单元,横向设置于所述反应釜的内腔,用于引导被所述第一驱动桨和第二驱动桨驱动对冲后的固液混合流流入至所述环形管道内;
28.至少一个搅拌出料单元,设置于所述环形管道上,用于对所述环形管道的内容物进行搅拌并向所述搅拌混合一体装置外导出;
29.至少一个第二进料组件,一对一匹配地设置于所述搅拌出料单元上,用于向所述环形管道内添加所述粘度指数改进剂;
30.其中,所述引流单元包括活动设置于所述密封中空体的两个镂空板,两个所述镂空板分别可转动地套设于所述密封中空体,在所述镂空板上设置有至少一个锥面板。
31.作为本发明的一种优选方案,所述搅拌出料单元包括二次掺混竖管,所述二次掺混竖管轴向设置于所述环形管道上,所述二次掺混竖管的内腔与所述环形管道的内腔相连通,在所述二次掺混竖管内设置有第二驱动轴,在所述第二驱动轴上安装有搅拌桨,所述二次掺混竖管远离所述反应釜的一侧上连接有出料管,所述搅拌桨能够使所述二次掺混竖管内形成环形固液混合流。
32.作为本发明的一种优选方案,所述第一驱动轴的两端均延伸出所述反应釜外,并且两个所述进料组件分别设置于所述第一驱动轴的两端上;
33.所述第二驱动轴的顶端延伸出所述环形管道外,并且所述第二进料组件设置于所述第二驱动轴上。
34.作为本发明的一种优选方案,所述进料组件和所述第二进料组件的结构相同,两者均包括安装于所述第二驱动轴上或所述第一驱动轴上的负压管道,所述负压管道内套接有驱动活塞,所述驱动活塞能够在所述负压管道内直线往复运动或完全脱出所述负压管道;
35.所述负压管道靠近所述反应釜一端连接有挤料管和至少一根吸料管,所述负压管道上设置有至少一个储料罐,每个所述储料罐上连接有一个所述吸料管,所述吸料管的两端分别连通所述负压管道的内腔和对应所述储料罐;所述挤料管的一端连通所述负压管道的内腔,另一端连通所述二次掺混竖管的内腔或所述反应釜的内腔;所述挤料管和吸料管内均设置有控制阀门;
36.在所述吸料管内的控制阀门处于打开状态且所述挤料管内的控制阀门处于闭合状态时,所述驱动活塞能够于所述负压管道内滑动产生负压,以使所述负压管道通过所述吸料管吸取所述储料罐内的液体原料;位于所述吸料管内的控制阀门闭合且位于所述挤料管内的控制阀门打开时,所述驱动活塞的一端能够通过滑动将所述负压管道内的液体原料通过所述挤料管向外挤出。
37.本发明与现有技术相比较具有如下有益效果:
38.本润滑油通过将基础油设置为植物油,较大程度的提高了润滑油的降解能力,使润滑油更加环保,其中,二硫化钼即可具有抗氧化剂作用又具有抗磨剂作用,并且毒性极小,是环保型润滑油中一种较好的抗氧化添加剂,但该种润滑油因固体颗粒较多容易产生在制备过程中固体颗粒混合不均匀的情况;本制备方法,通过流体对冲机构形成纵向对冲的混合流体,以对抗固体颗粒沉降,得到相对均匀的润滑油原料的混合物(除粘度指数改进剂外),出料机构能够对固体颗粒已经搅拌均匀的混合物进行二次搅拌,并在二次搅拌的过程中加入粘度指数改进剂,以防止粘度指数改进剂对固体颗粒混匀的干扰,从而使得本制备方法能够解决本润滑油在生产中的缺陷。
附图说明
39.为了更清楚地说明本发明的实施方式或现有技术中的技术方案,下面将对实施方
式或现有技术描述中所需要使用的附图作简单地介绍。显而易见地,下面描述中的附图仅仅是示例性的,对于本领域普通技术人员来讲,在不付出创造性劳动的前提下,还可以根据提供的附图引伸获得其它的实施附图。
40.图1为本发明实施例中制备方法的流程示意图;
41.图2为本发明实施例中整体的结构示意图
42.图3为本发明实施例中环形管道的俯视图;
43.图4为本发明实施例中液体进料单元的截面图。
44.图中的标号分别表示如下:
[0045]1‑
反应釜;2
‑
搅拌组件;3
‑
进料组件;4
‑
环形管道;5
‑
引流单元;6
‑
二次掺混竖管;7
‑
第二驱动轴;8
‑
搅拌桨;9
‑
出料管;
[0046]
21
‑
驱动机构;22
‑
第一驱动桨;23
‑
第二驱动桨;
[0047]
211
‑
主动轴;212
‑
从动轴;213
‑
密封中空体;214
‑
第一锥形齿轮;215
‑
第二锥形齿轮;
[0048]
51
‑
镂空板;52
‑
锥面板;
[0049]
31
‑
负压管道;32
‑
驱动活塞;33
‑
挤料管;34
‑
吸料管;35
‑
储料罐;36
‑
控制阀门。
具体实施方式
[0050]
下面将结合本发明实施例中的附图,对本发明实施例中的技术方案进行清楚、完整地描述,显然,所描述的实施例仅仅是本发明一部分实施例,而不是全部的实施例。基于本发明中的实施例,本领域普通技术人员在没有做出创造性劳动前提下所获得的所有其他实施例,都属于本发明保护的范围。
[0051]
本发明提供了一种环保型复合润滑油,由以下重量份的原料制成:植物基础油500
‑
700份、酯类油80
‑
130份、降凝剂0.1
‑
0.4份、抗氧剂70
‑
160、二硫化钼30
‑
70份、粘度指数改进剂25
‑
55份和石墨抗磨剂5
‑
25份。
[0052]
通过使用植物油作为基础油,利用植物油的高降解性,提高润滑油的降解能力,但植物油的不饱和酸较多,导致植物油在使用过程中容易被氧化。
[0053]
二硫化钼是经过化学提纯综合反应而得,其ph值为7
‑
8,略显碱性。它覆盖在摩擦材料的表面,能保护其它材料,防止它们被氧化,尤其是使其他材料不易脱落,贴附力增强,同时,二硫化钼也是充当抗磨剂,并且,二硫化钼毒性极小,符合环保的目的。
[0054]
作为本发明的一种优选方案,所述植物基础油包含菜籽油、玉米胚芽油、大豆油、花生油、葵花籽油、蓖麻油、棕榈油的一种或多种。
[0055]
作为本发明的一种优选方案,所述抗氧剂包含2,4,6
‑
三叔丁基苯酚、2,6
‑
二叔丁基
‑4‑
壬基酚、2,6
‑
二叔丁基对甲酚、异辛基
‑3‑
(3,5二叔丁基
‑
羟基苯基)丙酸酯中的一种或多种的混合物;所述酯类油为三羟甲基丙烷油酸酯,所述降凝剂为聚甲基丙烯酸酯,所述粘度指数改进剂为聚氢化苯乙烯异戊二烯型的粘度指数改进剂。
[0056]
如图1、图2、图3和图4所示,本发明还提供了一种复合润滑油的制备方法,包括如下步骤:
[0057]
步骤100、将植物基础油、酯类油置于容器中进行混合,得到第一混合物;
[0058]
步骤200、加热所述第一混合物至250
‑
260摄氏度,并向容器中加入氢气和催化剂
铜,氢化反应持续1
‑
2h,然后将铜分离出来,得到第二混合物;
[0059]
步骤300、加热所述搅拌混合一体装置以使得其内部温度至100
‑
200摄氏度后保持,将所述第二混合物、抗氧剂和二硫化钼从搅拌混合一体装置的两端加入至所述搅拌混合一体装置内,以使得所述搅拌混合一体装置的流体自两端向水平中心面流动形成对冲,然后再从对冲面将对冲后的流体引导出所述搅拌混合一体装置外,并且在对冲后的流体引导出所述搅拌混合一体装置外的过程中加入粘度指数改进剂进行混合。
[0060]
通过步骤100和步骤200,对植物基础油、酯类油进行氢化,以增加植物基础油、酯类油的饱和度,进一步提高植物基础油、酯类油的抗氧化能力。
[0061]
作为本发明的一种优选方案,所述搅拌混合一体装置包括:反应釜1,用于容纳制备复合润滑油的原料,并作为混合反应的容器;流体对冲机构,设置于所述反应釜1的两端,所述流体对冲机构用于驱动所述反应釜1的两端的流体相对流动,以在所述反应釜1的中间水平面上形成对冲面;所述出料机构用于承接所述对冲面处的流体,并将所述对冲面处的流体引出至所述搅拌混合一体装置外;其中,所述流体对冲机构包括用于驱动相对运动的流体的搅拌组件2,设置于所述搅拌组件2的两端的第一进料组件3,所述第一进料组件3用于持续向所述反应釜1两端提供相对运动流体的组成物;所述搅拌组件2包括驱动机构21、第一驱动桨22和第二驱动桨23,所述第一驱动桨22和第二驱动桨23对称设置于所述反应釜1的内部的两端,所述驱动机构21能够向所述第一驱动桨22和所述第二驱动桨23提供旋转的动力,且所述第一驱动桨22和第二驱动桨23的旋转方向相反;所述驱动机构21包括主动轴211和从动轴212,所述主动轴211和从动轴212分别安装于所述第一驱动桨22和第二驱动桨23上,所述主动轴211和从动轴212之间通过反向联动组件进行传动连接。
[0062]
为了制备上述的润滑油,存在以下几个难点:第一,由于选用二硫化钼作用抗氧化剂和抗磨剂,导致本发明所述的润滑油固体颗粒高于现有技术的润滑油,而固体颗粒由于自身在搅拌过程中容易发生沉降等现象,导致润滑油内固液难以混合均匀;第二,由于粘度越大,各运动机件摩擦表面间的油膜愈厚,对机件摩擦表面的保护性越强,故在润滑油生产过程中,需要加入粘度指数改进剂,而粘度很大的混合物很难将其中的固体颗粒搅拌均匀。
[0063]
综上所述,本发明还需提供一种能够对抗固体颗粒沉降以均匀混合润滑油原料,并且,能在此混合过程中调整至少一种添加原料的加入顺序的装置。
[0064]
在本实施例中,流体对冲机构用于实现对抗固体颗粒沉降,以均匀混合润滑油的原料除粘度指数改进剂外,出料机构用于对固体颗粒已经搅拌均匀的混合物进行二次搅拌,并在二次搅拌的过程中加入粘度指数改进剂。
[0065]
作为本发明的一种优选方案,所述反向联动组件包括设置于所述主动轴211和从动轴212之间的密封中空体213,所述密封中空体213通过支架安装于所述反应釜1内,所述主动轴211和从动轴212均以自身轴线为中心进行转动地延伸至所述密封中空体213的内腔中,所述密封中空体213的内腔中镜像设置有两个锥形齿轮214,所述主动轴211和从动轴212分别与两个第一锥形齿轮214连接,两个第一锥形齿轮214之间设置有第二锥形齿轮215,所述第二锥形齿轮215的两侧分别与两个所述第一锥形齿轮215相啮合,所述第二锥形齿轮215以自身轴线为中心进行转动地安装于所述密封中空体213的内腔上。
[0066]
在反应釜1内,由于固体颗粒有一定程度的沉降的,故在反应釜1内固体颗粒的密度自上而下呈逐渐降低的态势,利用第一驱动桨22和第二驱动桨23的反向旋转,使得反应
釜1内形成两股对冲的纵向固液混合流,使得反应釜1内对冲面位置产生一个高密度区域和低密度区域的对冲和混合,从而使得对冲面位置的混合均匀度高于其余区域。
[0067]
通过将现有技术中电机输出轴于主动轴211相互连接,而主动轴211转动则会带动与自身相连的第一锥形齿轮214进行转动,而第一锥形齿轮214则会带动与其啮合第二锥形齿轮215的进行转动,所述第二锥形齿轮215则会带动另一个第一锥形齿轮215反向转动。该种转动的方式,同步对第一驱动桨22和第二驱动桨23进行驱动,使得形成的对冲更加均衡。
[0068]
作为本发明的一种优选方案,所述出料机构包括:环形管道4,套设于所述反应釜1上,且其内腔与所述反应釜1的内腔相连通;引流单元5,横向设置于所述反应釜1的内腔,用于引导被所述第一驱动桨22和第二驱动桨23驱动对冲后的固液混合流流入至所述环形管道4内;至少一个搅拌出料单元,设置于所述环形管道4上,用于对所述环形管道4的内容物进行搅拌并向所述搅拌混合一体装置外导出;至少一个第二进料组件,一对一匹配地设置于所述搅拌出料单元上,用于向所述环形管道4内添加所述粘度指数改进剂;其中,所述引流单元5包括活动设置于所述密封中空体213的两个镂空板51,两个所述镂空板51分别可转动地套设于所述密封中空体213,在所述镂空板51上设置有至少一个锥面板52。
[0069]
通过在对冲的固液混合流混合面上,设置引流单元5,利用引流单元5的特殊形状,将经过二次混合的固液混合流向环形管道4内进行引导。
[0070]
作为本发明的一种优选方案,所述搅拌出料单元包括二次掺混竖管6,所述二次掺混竖管6轴向设置于所述环形管道4上,所述二次掺混竖管6的内腔与所述环形管道4的内腔相连通,在所述二次掺混竖管6内设置有第二驱动轴7,在所述第二驱动轴7上安装有搅拌桨8,所述二次掺混竖管6远离所述反应釜1的一侧上连接有出料管9,所述搅拌桨8能够使所述二次掺混竖管6内形成环形固液混合流。
[0071]
环形管道4设置于固液混合流的对冲面上,由于带有横向外侧移动的初速度的对冲后液体会逐渐进入至环形管道4,通过环形管道4向外排出。
[0072]
需要特别解释的是,本装置是一种持续性的润滑油制备装置,故从环形管道4内抽出部分混合成品时,反应釜1内会持续进行原料添加,形成一个从反应釜1内连续加入,从而环形管道4内持续抽出,而不是一次制备设备。
[0073]
作为本发明的一种优选方案,所述第一驱动轴211的两端均延伸出所述反应釜1外,并且两个所述进料组件3分别设置于所述第一驱动轴211的两端上;所述第二驱动轴7的顶端延伸出所述环形管道4外,并且所述第二进料组件设置于所述第二驱动轴7上。
[0074]
作为本发明的一种优选方案,所述进料组件3和所述第二进料组件的结构相同,两者均包括安装于所述第二驱动轴7上或所述第一驱动轴211上的负压管道31,所述负压管道31内套接有驱动活塞32,所述驱动活塞32能够在所述负压管道31内直线往复运动或完全脱出所述负压管道31;所述负压管道31靠近所述反应釜1一端连接有挤料管33和至少一根吸料管34,所述负压管道31上设置有至少一个储料罐35,每个所述储料罐35上连接有一个所述吸料管34,所述吸料管34的两端分别连通所述负压管道31的内腔和对应所述储料罐35;所述挤料管33的一端连通所述负压管道31的内腔,另一端连通所述二次掺混竖管6的内腔或所述反应釜1的内腔;所述挤料管33和吸料管34内均设置有控制阀门36;在所述吸料管34内的控制阀门36处于打开状态且所述挤料管33内的控制阀门36处于闭合状态时,所述驱动活塞32能够于所述负压管道31内滑动产生负压,以使所述负压管道31通过所述吸料管34吸
取所述储料罐35内的液体原料;位于所述吸料管34内的控制阀门36闭合且位于所述挤料管33内的控制阀门36打开时,所述驱动活塞32的一端能够通过滑动将所述负压管道31内的液体原料通过所述挤料管33向外挤出。
[0075]
而在添加固体原料时,可以用人工将驱动活塞32脱出于负压管道31,将固体形颗粒加入至负压管道31内,通过套入驱动活塞3,打开吸料管34的控制阀门36,直线驱动驱动活塞32将负压管道31内的空气从吸料管3挤出,然后关闭吸料管34的控制阀门36,打开挤料管33内控制阀门36,进行出料。
[0076]
也可以,直接将固体原料加入液体原料进行混合,直接被吸料管34进行吸出也可实现。
[0077]
进料组件3的作用主要是实现一个不破坏反应釜1密封性的条件下对其进行加料,以防止氧气进入反应釜中,从而在高温混合过程中发生氧化。
[0078]
以下通过实例对本发明进一步进行说明,下述实例中步骤b
‑
e均在图2
‑
4中所述的所述添料搅拌一体装置中进行。
[0079]
实施例1
[0080]
步骤a、以重量份计,准备大豆油500份、酯类油130份、聚甲基丙烯酸酯0.1份、抗氧剂70、二硫化钼30份、粘度指数改进剂55份和石墨抗磨剂25份;
[0081]
步骤b、将大豆油、酯类油置于容器中进行混合,得到初级混合物;
[0082]
步骤c、使用微波等方式加热所述初级混合物至250
‑
260摄氏度,并通过管道向容器中加入氢气和催化剂铜,氢化反应持续1
‑
2h,然后将铜和所述初级混合物分离,再将分离后的所述初级混合物加入搅拌混合一体装置内;
[0083]
步骤d、再对搅拌混合一体装置内的反应釜抽真空,通过进料单元3向反应釜1内加入抗氧剂、二硫化钼和石墨抗磨剂,并将反应釜1加热至200摄氏度;
[0084]
步骤e、通过第一驱动桨22和第二驱动桨23搅拌,通过引流单元5将混合后液体引导至环形管道4,再通过液体进料单元32向环形管道4内的二次掺混竖管6内腔中加入粘度指数改进剂,最后通过搅拌桨22进行搅拌,该过程持续1个小时,最后成品由出料管9导出。
[0085]
实施例2
[0086]
按照实施例1的方法进行,唯一不同的是:以重量份计,步骤a、植物基础油700份、酯类油130份、聚甲基丙烯酸酯0.1份、抗氧剂160、二硫化钼70份、粘度指数改进剂55份和石墨抗磨剂25份。
[0087]
实施例3
[0088]
与实施例1不同的是:步骤a、以重量份计,植物基础油600份、酯类油130份、聚甲基丙烯酸酯0.1份、抗氧剂160、二硫化钼70份、粘度指数改进剂55份和石墨抗磨剂25份。
[0089]
对比例1
[0090]
步骤a、以重量份计,准备大豆油500份、酯类油130份、聚甲基丙烯酸酯0.1份、抗氧剂70、二硫化钼30份、粘度指数改进剂55份和石墨抗磨剂25份;
[0091]
步骤b、将大豆油、酯类油置于容器中进行混合,得到初级混合物;
[0092]
步骤c、使用微波等方式加热所述初级混合物至250
‑
260摄氏度,并通过管道向容器中加入氢气和催化剂铜,氢化反应持续1
‑
2h,然后将铜和所述初级混合物分离,再将分离后的所述初级混合物、抗氧剂、二硫化钼和石墨抗磨剂加另一个容器内,再对该容器使用微
波进行加热至200摄氏度,并进行搅拌1小时。
[0093]
对本发明实施例1
‑
3制备的环保型润滑油进行生物降解率、氧化诱导期和最大无卡咬负荷性能检测(测试方法采用bg/t3142记载的方法),检测结果见表1。
[0094]
表1
[0095][0096][0097]
最大无卡咬负荷反应了润滑油的承载能力和润滑极压性能,氧化诱导期则反应了氧化,最大无卡咬负荷反应了润滑油的承载能力和润滑极压性能,氧化诱导期则反应了氧化稳定性,由表1中结果可见,实施例1
‑
3所制得的环保型润滑油,不仅承载能力高,而且生物降解率高,氧化稳定性好。
[0098]
以上实施例仅为本技术的示例性实施例,不用于限制本技术,本技术的保护范围由权利要求书限定。本领域技术人员可以在本技术的实质和保护范围内,对本技术做出各种修改或等同替换,这种修改或等同替换也应视为落在本技术的保护范围内。