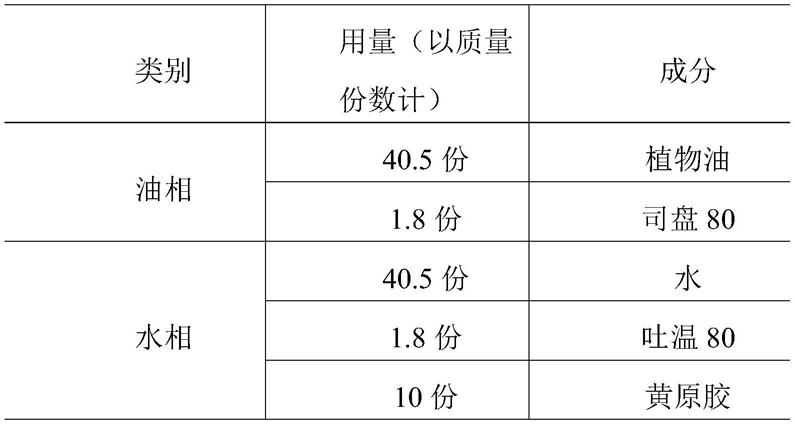
1.本发明属于脱模技术领域,具体涉及一种植物油混凝土脱模剂及其制备方法和应用。
背景技术:
2.混凝土脱模剂又称混凝土隔离剂或脱模润滑剂,是一种涂于模板内壁起润滑和隔离作用,使混凝土在在拆模时能顺利脱离模板,保持混凝土形状完整无损的物质。目前,混凝土行业使用的脱模剂大多数是矿物油基脱模剂,这些脱模剂性能优异,但是其由不可再生资源组成,不易生物降解,对周围的环境产生影响。随着矿物油的不断紧缺,人类环保意识的不断增强,寻找可再生资源的脱模剂替代目前的矿物油基脱模剂也变得极为迫切。
3.当今,人们对混凝土的表面要求越来越高,因此要求脱模剂的使用性能也要更全面,先存在混泥土脱模剂主要存在以下问题:大多数脱模剂由不可再生资源组成,不易生物降解,对周围的环境产生影响;制造成本高;稳定性差、脱模效果差,在低温环境耐冻性差等缺点;因此,开发脱模性能更全面的植物油基混凝土脱模剂意义重大,且具有巨大的市场应用前景。
技术实现要素:
4.为了克服上述现有技术的缺点,本发明的目的在于提供一种植物油混凝土脱模剂的制备方法,以解决目前混凝土脱模剂不易降解、制造成本高、稳定性差、脱模效果差,在低温环境耐冻性差的缺点。
5.为了达到上述目的,本发明采用以下技术方案予以实现:
6.本发明公开了一种植物油混凝土脱模剂,以质量份数计,其成分包括40~70份植物油、1~3份司盘80、40~70份水、1~3份吐温80和4~10份黄原胶。
7.优选地,该植物油混凝土脱模剂分子的平均粒径为1
‑
5微米。
8.本发明还公开了上述植物油油混凝土脱模剂的制备方法,包括以下步骤:
9.1)将植物油加热后,向其中加入司盘80,搅拌至混合均匀,得到油相溶液;
10.2)将水加热后,向其中加入吐温80和黄原胶,搅拌至混合均匀,得到水相溶液;
11.3)搅拌油相溶液,并向其中加入水相溶液并混合均匀,继续搅拌测定其溶液分子粒径,随后降低搅拌速率直至停止搅拌,将形成的入液冷却至室温,得到一种植物油混凝土脱模剂。
12.优选地,步骤1)中,植物油加热至70~80℃。
13.优选地,步骤1)中,搅拌是在800~1000rpm的转速下机械搅拌10~20min。
14.优选地,步骤2)中,水加热至65~75℃。
15.优选地,步骤2)中,搅拌是在800~1000rpm的转速下机械搅拌10~20min。
16.优选地,步骤3)中,水相溶液加入油相溶液时搅拌速度为10000~15000rpm,混合均匀后再搅拌5~10min后,测量其溶液分子粒径。
17.优选地,步骤3)中,测量当溶液分子粒径小于5微米时,降低搅拌转速再搅拌15~20min后停止搅拌。
18.本发明还公开了上述植物油混凝土脱模剂的应用,其在进行脱模时的具体步骤为:将植物油混凝土脱模剂和水以1:5的体积份数混合,搅拌均匀形成植物油混凝土脱模剂乳液,将植物油混凝土脱模剂乳液喷洒在模板上,进行脱模处理。
19.与现有技术相比,本发明具有以下有益效果:
20.本发明所提出的一种植物油混凝土脱模剂,以植物油为有效成分,辅以添加剂配置而成。本发明中选用的水相和油相表面活性剂应用广泛,性能优良,它们可以通过吸附在气液界面上,打破液体分子之间的强烈相互作用或分子间的作用力,从而降低液体的表面张力。本发明采用的原料配比为实验得出的最佳配比,在这样的配比条件下可以实现脱模剂的长时间稳定以及良好的脱模效果。本发明加入了黄原胶作为水相表面活性剂,它可以防止水相和油相分离,提升乳液的稳定性,同时黄原胶也起乳化剂的作用,有利于油和水发生乳化作用形成乳液。本发明使用的表面活性剂均具有可生物降解性,能够有效降低表面张力,提高脱模剂的稳定性,延长产品的使用寿命。
21.进一步地,本发明制备的植物油混凝土脱模剂,其乳液分子平均粒径为1
‑
5微米,此粒径相对较小,可以提高脱模剂乳液的稳定性,使其不发生破乳、分层等现象。
22.本发明所提出的上述植物油混凝土脱模剂的制备方法,该方法简单易操作,制备过程中使用的脱模剂的原料成本仅为4.5~10元,与市场上每公斤脱模剂20~25元的价格相比,成本大幅度降低。
23.根据相关实验结果表明:该植物油混凝土脱模剂用水稀释5倍后,倒置20次后,放置14天也不会出现分层、乳化、絮凝、沉淀的现象,具有十分优异的稳定性,可大幅度增强混凝土脱模剂的实际应用效果;在
‑
15~
‑
20℃的低温下也能保持流动性,具有优异的抗凝固性,符合实际使用需求,扩大了实际应用范围。
附图说明
24.图1为本发明实施例1合成的植物油混凝土脱模剂放置14天后实物图;
25.图2为本发明实施例1合成的植物油混凝土脱模剂与其他脱模剂在冰箱中放置2小时后对比图;
26.图3为本发明实施例1合成的植物油混凝土脱模剂与其他脱模剂脱模试样对比;
27.其中a
‑
其他脱模剂;b
‑
植物油混凝土脱模剂。
具体实施方式
28.为了使本技术领域的人员更好地理解本发明方案,下面将结合本发明实施例中的附图,对本发明实施例中的技术方案进行清楚、完整地描述,显然,所描述的实施例仅仅是本发明一部分的实施例,而不是全部的实施例。基于本发明中的实施例,本领域普通技术人员在没有做出创造性劳动前提下所获得的所有其他实施例,都应当属于本发明保护的范围。
29.需要说明的是,本发明的说明书和权利要求书及上述附图中的术语“第一”、“第二”等是用于区别类似的对象,而不必用于描述特定的顺序或先后次序。应该理解这样使用
的数据在适当情况下可以互换,以便这里描述的本发明的实施例能够以除了在这里图示或描述的那些以外的顺序实施。此外,术语“包括”和“具有”以及他们的任何变形,意图在于覆盖不排他的包含,例如,包含了一系列步骤或单元的过程、方法、系统、产品或设备不必限于清楚地列出的那些步骤或单元,而是可包括没有清楚地列出的或对于这些过程、方法、产品或设备固有的其它步骤或单元。
30.下面结合附图对本发明做进一步详细描述:
31.本发明提出的一种植物油混凝土脱模剂的制备方法,首先,将植物油与油相表面活性剂混合制备出油相溶液;再将水和水相表面活性剂混合制备出水相溶液;最后,将水相溶液缓慢加入到油相溶液中,在相应温度下充分搅拌,得到植物油混凝土脱模剂。所获得的产品稳定性好、不易分层、易喷涂、不易干燥和风化,容易从模板上剥离,环境友好且成本较低。
32.实施例1
33.一种植物油混凝土脱模剂的制备方法,包括以下步骤:
34.步骤一、以质量份数计,将40.5份植物油加入烧杯中并加热升温到80℃,向其中加入1.8份司盘80油相表面活性剂,以800rpm的转速机械搅拌10min,待表面活性剂完全溶解,得到油相溶液;
35.步骤二、将40.5份水加入新的烧杯中并加热升温到75℃,随后加入1.8份吐温80、10份黄原胶的水相表面活性剂,以800rpm的转速进行机械搅拌10min,待表面活性剂完全溶解,得到水相溶液;
36.步骤三、在15000rpm转速机械搅拌下将水相溶液缓慢加入油相溶液中,完全加入后继续搅拌15min,当溶液分子粒径小于5微米时,降低搅拌转速再搅拌15min后停止搅拌,将所形成的乳液冷却至室温,得到一种植物油混凝土脱模剂,其成分如表1所示。
37.表1植物油混凝土脱模剂的组成成分
[0038][0039]
制得的植物油混凝土脱模剂保持粘度后,用水稀释5倍,将样品放入瓶中,室温保存14天监测,可观察到样品稳定,无乳化、沉淀、絮凝等现象,如图1所示。所述样品在冰箱低温
‑
15℃放置两小时后,样品未出现凝固,样品状态图片见图2。经现场脱模实验测试,混凝土的粘模程度较低,易脱模,脱模过程中锤击次数可低至2次,脱模后模板表面浮灰量少,混
凝土表面光泽鲜亮程度较高,且本脱模剂耐受低温为
‑
15℃。如图3所示,将本发明植物油混凝土脱模剂(b)与其他脱模剂(a)脱模试样进行对比,可看到a有气泡的产生,甚至已经出现了质量缺陷,而本发明所制备的植物油混凝土脱模剂脱模效果良好,几乎看不到明显的气泡和缺陷。
[0040]
实施例2
[0041]
一种植物油混凝土脱模剂的制备方法,包括以下步骤:
[0042]
步骤一、以质量份数计,将40.5份植物油加入烧杯中并加热升温到80℃,向其中加入2.5份司盘80油相表面活性剂,以800rpm的转速机械搅拌10min,待表面活性剂完全溶解,得到油相溶液;
[0043]
步骤二、将40.5份水加入新的烧杯中并加热升温到75℃,随后加入2.5份吐温80、10份黄原胶的水相表面活性剂,以800rpm的转速进行机械搅拌10min,待表面活性剂完全溶解,得到水相溶液;
[0044]
步骤三、在15000rpm转速机械搅拌下将水相溶液缓慢加入油相溶液中,完全加入后继续搅拌15min,当溶液分子粒径小于5微米时,降低搅拌转速再搅拌15min后停止搅拌,将所形成的乳液冷却至室温,得到一种植物油混凝土脱模剂,其成分如表2所示。
[0045]
表2植物油混凝土脱模剂的组成成分
[0046][0047]
将所得脱模剂保持粘度后,用水稀释5倍,将样品放入瓶中,室温保存14天监测,可观察到未发生乳化、沉淀、分离、产生絮凝等现象,如图2所示。
[0048]
实施例3
[0049]
一种植物油混凝土脱模剂的制备方法,包括以下步骤:
[0050]
步骤一、以质量份数计,将60份植物油加入烧杯中并加热升温到80℃,向其中加入1.5份司盘80油相表面活性剂,以800rpm的转速机械搅拌10min,待表面活性剂完全溶解,得到油相溶液;
[0051]
步骤二、将60份水加入新的烧杯中并加热升温到75℃,随后加入1.5份吐温80、7份黄原胶的水相表面活性剂,以800rpm的转速进行机械搅拌10min,待表面活性剂完全溶解,得到水相溶液;
[0052]
步骤三、在15000rpm转速机械搅拌下将水相溶液缓慢加入油相溶液中,完全加入
后继续搅拌15min,当溶液分子粒径小于5微米时,降低搅拌转速再搅拌15min后停止搅拌,将所形成的乳液冷却至室温,得到一种植物油混凝土脱模剂,其成分如表3所示。
[0053][0054]
实施例4
[0055]
一种植物油混凝土脱模剂的制备方法,包括以下步骤:
[0056]
步骤一、以质量份数计,将40份植物油加入烧杯中并加热升温到80℃,向其中加入1份司盘80油相表面活性剂,以800rpm的转速机械搅拌10min,待表面活性剂完全溶解,得到油相溶液;
[0057]
步骤二、将40份水加入新的烧杯中并加热升温到75℃,随后加入1份吐温80、4份黄原胶的水相表面活性剂,以800rpm的转速进行机械搅拌10min,待表面活性剂完全溶解,得到水相溶液;
[0058]
步骤三、在15000rpm转速机械搅拌下将水相溶液缓慢加入油相溶液中,完全加入后继续搅拌15min,当溶液分子粒径小于5微米时,降低搅拌转速再搅拌15min后停止搅拌,将所形成的乳液冷却至室温,得到一种植物油混凝土脱模剂,其成分如表4所示。
[0059]
表4植物油混凝土脱模剂的组成成分
[0060]
[0061]
实施例5
[0062]
一种植物油混凝土脱模剂的制备方法,包括以下步骤:
[0063]
步骤一、以质量份数计,将70份植物油加入烧杯中并加热升温到80℃,向其中加入3份司盘80油相表面活性剂,以800rpm的转速机械搅拌10min,待表面活性剂完全溶解,得到油相溶液;
[0064]
步骤二、将70份水加入新的烧杯中并加热升温到75℃,随后加入3份吐温80、10份黄原胶的水相表面活性剂,以800rpm的转速进行机械搅拌10min,待表面活性剂完全溶解,得到水相溶液;
[0065]
步骤三、在15000rpm转速机械搅拌下将水相溶液缓慢加入油相溶液中,完全加入后继续搅拌15min,当溶液分子粒径小于5微米时,降低搅拌转速再搅拌15min后停止搅拌,将所形成的乳液冷却至室温,得到一种植物油混凝土脱模剂,其成分如表5所示。
[0066]
表5植物油混凝土脱模剂的组成成分
[0067][0068]
以上实施例得到的植物油混凝土脱模剂保持粘度后,用水稀释5倍,将样品放入瓶中,室温保存14天监测,可观察到未发生乳化、沉淀、分离、产生絮凝等现象。经现场脱模实验测试,混凝土的粘模程度较低,易脱模,脱模过程中锤击次数可低至2次,脱模后模板表面浮灰量少,混凝土表面光泽鲜亮程度较高,且本脱模剂耐受低温为
‑
15℃。
[0069]
以上内容仅为说明本发明的技术思想,不能以此限定本发明的保护范围,凡是按照本发明提出的技术思想,在技术方案基础上所做的任何改动,均落入本发明权利要求书的保护范围之内。