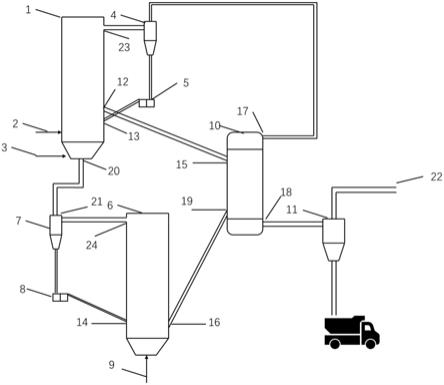
1.本发明涉及生物质气化领域,特别涉及一种能够实现生物质焦油裂解的生物质气化装置及方法。
技术背景
2.生物质气化技术能够将固态生物质能转化为气体燃料,不仅能够实现二氧化碳的零排放,还能缓解我国气体燃料不足的劣势。生物质气化技术具有转化效率高、设备简单、投资少、不受地区、燃料类型和气候限制等特点,环保性能和经济性能俱佳,对促进我国能源利用朝着绿色可持续方向迈进具有重要意义。然而,生物质焦油是生物质气化过程中不可避免的产物,不仅会造成管道、设备的堵塞,而且严重影响生物质气化过程的效率。因此,如何降低生物质气化过程中焦油量是亟需解决的一个问题。
技术实现要素:
3.本发明要解决的问题是,克服现有的技术不足,提供一种能够实现生物质焦油裂解的生物质气化装置及方法。
4.为解决现有技术的不足,本发明的解决方案是:本发明提供一种能够实现生物质焦油裂解的生物质气化装置及方法,包括设有排渣口的循环流化床生物质气化炉,设有排渣口的循环流化床生物质半焦燃烧炉以及高温半焦过滤器。
5.所述的循环流化床生物质气化炉的底部分别设有高温烟气入口和反应气入口,炉膛中下部分别设有生物质物料入口、返料入口以及半焦溢流口,顶部设有合成气出口;其中,顶部的合成气出口与旋风分离器相连,旋风分离器下部与返料器相连,返料器出口与循环流化床生物质气化炉的返料口相连;旋风分离器合成气出口与高温过滤器相连。
6.所述的循环流化床半焦燃烧炉的底部设有空气进口,炉膛的中下部设有返料口和半焦入口,炉膛顶部设有高温烟气出口;其中高温烟气出口与旋风分离器相连,旋风分离器下部与返料器相连,返料器出口与循环流化床半焦燃烧炉中下部的返料入口相连;循环流化床半焦燃烧炉中下部的半焦入口与高温过滤器相连。
7.在本发明中,所述的循环流化床生物质气化炉和燃烧炉的内部由下至上分为风室、密相区和稀相区;其中气化炉的高温烟气与反应气进口与风室相连;生物质给料口、气化炉和燃烧炉返料入口、气化炉半焦溢流口、燃烧炉半焦返料入口位于密相区下部;合成气出口、高温烟气出口位于气化炉和燃烧炉稀相区上部。
8.本发明中,高温过滤器的上部和下部分别设置有滤网,滤网孔径为0.1mm左右。
9.本发明中,循环流化床气化炉和循环流化床燃烧炉底部设带排渣口的锁斗。
10.本发明进一步提供了一种能够实现生物质焦油催化裂解的生物质气化装置及方法,包括下列步骤:(1)将成型后的生物质原料通过给料口添加至循环流化床气化炉密相区上部,控
制空气与生物质的质量比例为1.0
‑
1.2;循环流化床气化炉在常压运行,运行温度为700
‑
800℃;颗粒状生物质在密相区与来自底部的高温烟气和空气混合,使生物质发生气化反应产生合成气,该过程以空气和高温烟气作为气化剂。
11.(2)生物质气化过程产生的生物质半焦经半焦溢流口离开气化炉,并经高温过滤器半焦入口进入高温过滤器。循环流化床气化炉排放的合成气经过气化炉顶部的合成气出口送入旋风分离器,分离下来的固体颗粒经返料器重新送回气化炉中,离开旋风分离器后送入高温过滤器,合成气进入高温过滤器并从高温过滤器上部进入,从高温过滤器下部离开,并与高温过滤器中的生物质半焦充分接触,其中合成气中的焦油成分在生物质半焦的作用下发生裂解,达到焦油脱除的目的。
12.(3)实现焦油脱除后的生物质合成气进入旋风分离器,分离下来的固体物料进行收集用于其他用途,合成气则从旋风分离器出口离开系统进行后续利用。
13.(4)经过焦油脱除后的生物质半焦从高温过滤器的出口离开并进入循环流化床半焦燃烧炉,与来自炉膛底部的空气进行混合后燃烧,其中燃烧温度控制在900℃左右,控制底部空气与半焦物料的质量比例为1
‑
1.2,产生的烟气从炉膛上部进入旋风分离器,分离下来的物料重新送入循环流化床燃烧炉,高温烟气则送入循环流化床气化炉。
14.本发明中,所述粒状生物质的粒度控制在1
‑
10mm。
15.发明原理描述:本发明基于生物质气化过程焦油难以脱除的技术难题,结合生物质半焦对焦油有催化裂解的效果,通过设置生物质合成气与生物质半焦接触环节以达到焦油催化裂解的目的。
16.将生物质气化与生物质半焦
‑
焦油原位催化裂解有机结合实现生物质焦油的催化裂解,不仅可以提高生物质转化过程的热效率,同时能够防止焦油冷却带来的设备污染和管道堵塞等严重影响生物质气化系统正常运行的问题发生,实现生物质气化系统整体效益的最优化。
17.与现有技术相比,本发明具有的有益效果:1、将合成气进行冷却后完成焦油脱除,实现高温状态下的焦油催化裂解,提高生物质气化系统的整体效率。
18.2、生物质气化剩余半焦完成焦油的催化裂解,同时将生物质气化与生物质半焦燃烧有机结合,提高生物质原料的利用效率。
附图说明
19.图1为本发明所述装置的一种实现方案的示意图。
20.图中:循环流化床生物质气化炉1,生物质原料进口2,反应气进口3,旋风分离器4,返料器5,循环流化床燃烧炉6,旋风分离器7,返料器8,空气进口9,高温过滤器10,旋风分离器11,半焦溢流口12,气化炉返料入口13,燃烧炉返料入口14,高温过滤器半焦进口15,燃烧炉半焦进口16,高温过滤器合成气入口17,高温过滤器合成气出口18,高温过滤器半焦出口19,气化炉高温烟气进口20,旋风分离器高温烟气出口21,合成气出口22,气化炉合成气出口23,燃烧炉合成气出口24。
具体实施方式
21.下面结合附图,对本发明的实现方式进行描述。
22.在本发明中,所述的循环流化床生物质气化炉1的底部分别设有高温烟气入口20和反应气入口3,炉膛中下部分别设有生物质物料入口2、返料入口13以及半焦溢流口12,顶部设有合成气出口23;其中,顶部的合成气出口23与旋风分离器4相连,旋风分离器4下部与返料器5相连,返料器出口与循环流化床生物质气化炉的返料口13相连;旋风分离器合成气出口与高温过滤器10相连。
23.所述的循环流化床半焦燃烧炉6的底部设有空气进口9,炉膛的中下部设有返料口14和半焦入口16,炉膛顶部设有高温烟气出口24;其中高温烟气出口24与旋风分离器7相连,旋风分离器下部与返料器8相连,返料器出口与循环流化床半焦燃烧炉中下部的返料入口14相连;循环流化床半焦燃烧炉中下部的半焦入口16与高温过滤器10相连。
24.在本发明中,所述的循环流化床生物质气化炉1和燃烧炉6的内部由下至上分为风室、密相区和稀相区;其中气化炉的高温烟气进口20与反应气进口3与风室相连;生物质给料口2、气化炉返料入口13和燃烧炉返料入口16、气化炉半焦溢流口12、燃烧炉半焦返料入口14位于密相区下部;合成气出口23、高温烟气出口24位于气化炉和燃烧炉稀相区上部。
25.本发明中,高温过滤器的上部和下部分别设置有滤网,滤网孔径为0.1mm左右。
26.本发明中,循环流化床气化炉和循环流化床燃烧炉底部设带排渣口的锁斗。
27.基于本发明所述装置的煤炭部分气化分级转化方法,包括下述步骤:(1)将成型后的生物质原料通过给料口2添加至循环流化床气化炉1密相区上部,颗粒状生物质在密相区与来自底部的高温烟气入口20和空气入口3的高温烟气与空气混合,控制空气与生物质的质量比例为1.0
‑
1.2;循环流化床气化炉在常压运行,运行温度为700
‑
800℃;使生物质发生气化反应产生合成气,该过程中空气和高温烟气作为气化剂。
28.(2)生物质气化过程产生的生物质半焦经半焦溢流口12离开气化炉,并经高温过滤器半焦入口15进入高温过滤器。循环流化床气化炉排放的合成气经过气化炉顶部的合成气出口23送入旋风分离器4,分离下来的固体颗粒经返料器5经过气化炉返料入口13重新送回气化炉中,离开旋风分离器后的合成气经过高温过滤器的合成气进口17进入高温过滤器,从高温过滤器的合成气出口18离开,并与高温过滤器中的生物质半焦充分接触,其中合成气中的焦油成分在生物质半焦的作用下发生裂解,达到焦油脱除的目的。
29.(3)实现焦油脱除后的生物质合成气进入旋风分离器11,分离下来的固体物料进行收集用于其他用途,合成气则从旋风分离器出口22离开系统进行后续利用。
30.(4)经过焦油脱除后的生物质半焦从高温过滤器的半焦出口19离开并经燃烧炉返料入口16进入循环流床半焦燃烧炉6,与来自炉膛底部9的空气进行混合后燃烧,其中燃烧温度控制在900℃左右,控制底部空气与半焦物料的质量比例为1
‑
1.2,产生的烟气从炉膛上部进入旋风分离器7,分离下来的物料重新送入循环流化床燃烧炉6,高温烟气则送入循环流化床气化炉1中。
31.其中,粒状生物质的粒度控制在1
‑
10mm。