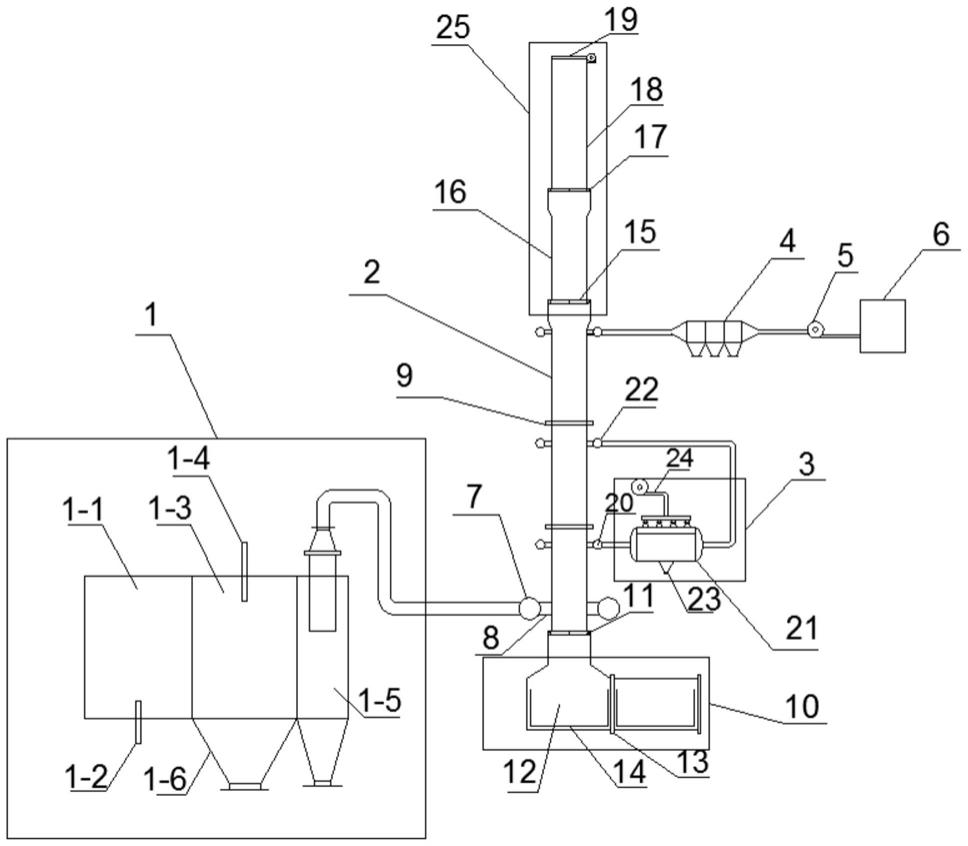
1.本发明属于冶金领域,特别涉及一种煤炭干馏与废钢预热复合设备及方法。
背景技术:
2.随着我国经济多年的高速发展,社会产生废钢量越来越大,废钢既是固废,也是资源。目前处理该固废的主要工艺有两个:一是电炉熔化冶炼;二是通过转炉过剩的热量熔化冶炼。电炉冶炼需要消耗电能,电能是二次能源,由于目前我国还是以火力发电为主,热电转换过程有60%左右的能源被浪费,发电过程综合排量放大。而利用转炉余热冶炼多消耗废钢是非常合理的。余热利用具有节能、成本低、排放少的优越性,还无需投资建设更多电炉。但是转炉的余热量有限,因而消耗废钢有限。钢铁企业为了让转炉多消化废钢,目前多采用废钢加热的办法,采用的工艺有铁水罐氧燃枪加热、钢水包氧燃枪加热等。这种加热方式存在一系列问题:热效率低(不到40%);烟气无法得到很好的处理,由于是间歇式加热,烟气温度变化极大,导致烟气无法脱硝,受环境限制,烟气的硫、二噁英、重金属也无法脱除。因此国家环保管理部门是不会允许此种工艺长期存在下去的。目前石家庄巨力科技股份有限公司发明的一种废钢预热装置也只是做了烟气除尘,其专利技术在出废钢环节也存在问题,废钢烧损比较大。
3.目前很多企业的烧结工艺仍然是以无烟煤做燃料的,而烧结工艺使用无烟煤会带来严重的环境污染问题。烧结生产过程中无烟煤的挥发分基本没有参与燃烧,这些挥发分全部排入大气中,既造成了大气污染,也浪费了能源。近年来有些地区的环保部门已经发现这个问题,要求企业必须以焦粉或者干馏煤做为烧结燃料,来降低烧结生产带来的环境污染。使用焦粉或干馏煤做为烧结燃料可以大大降低烧结生产造成的排放污染,无疑是烧结工艺的正确选择,但如果全国烧结企业都开始以焦粉或干馏煤做为烧结燃料,则目前焦粉产量远远无法满足需求,而目前生产干馏煤的工艺普遍存在能耗高、污染严重问题。
技术实现要素:
4.本发明的目的是克服上述现有技术存在的不足,提供一种煤炭干馏与废钢预热复合设备及方法,实现煤炭干馏与废钢预热相结合。
5.为实现上述目的,本发明采用以下技术方案:
6.一种煤炭干馏与废钢预热复合设备,包括煤炭干馏炉1和废钢预热竖炉2,所述的废钢预热段底部设有保温废钢槽14,炉顶设有等静压加料系统25,炉内设机械手9托扶废钢。
7.所述的煤炭干馏炉1由燃烧室1
‑
1、氧燃枪1
‑
2、干馏室1
‑
3、喷煤枪1
‑
4和除尘室1
‑
5组成。
8.所述的煤炭干馏炉1与废钢预热竖炉2用烟道连接,所述的废钢预热竖炉2侧壁设有支气管8与环形烟道7,所述的煤炭干馏炉1与支气管8通过环形烟道7与废钢预热竖炉2连接。
9.所述的支气管8设置的位置距离废钢预热竖炉2底要留有足够高度,避免废钢预热竖炉2底部出料系统承受高温。具体距离取决于高温烟气进入炉内处的温度和出料系统的材料选择,以不影响设备寿命为准。
10.所述的废钢预热竖炉2整个系统是负压运行,煤气不易泄露,但是要避免出料加料时空气进入,因此在炉底设等静压出料系统10,在炉顶设等静压加料系统25。
11.所述的等静压加料系统25由由下向上一次设置的下封闭翻板阀15、下加料储料仓16、上封闭翻板阀17、上加料仓18和上封闭板19组成。由于上部负压较大,因此设上下双层加料仓,上下加料仓间设上封闭翻板阀17,强化封闭效果。
12.所述的废钢预热段底部设有等静压出料系统10,所述的等静压出料系统10由炉底的翻板卸料阀11、储料仓12和侧封闭板13组成,所述的保温废钢槽14设于储料仓12内。
13.所述的机械手9设置个数结合整体需要进行设置,优选为2个,包括第一层机械手和第二层机械手,第一层机械手的材料选择要求耐热700℃以上;第二层机械手的材料选择要求耐热400℃以上,2个机械手设置使废钢预热竖炉2内形成三层废钢预热段。
14.所述的废钢预热竖炉2侧壁连接有锌回收系统3,锌回收系统入口连接于第一层机械手下部侧壁,锌回收系统排气口连接于第二层机械手下部侧壁,具体的,所述的锌回收系统3由引出烟气环形烟道20、锌回收装置21、烟气返回环形烟道22、出锌阀23和冷却系统24组成。引出烟气环形烟道20和烟气返回环形烟道22与竖炉内设在竖炉周围的支气管连接,引出烟气环形烟道20与竖炉内连接的支气管设在第一层废钢顶与第一层机械手之间,烟气返回环形烟道22与竖炉内连接的支气管设在第二层废钢顶与第二层机械手之间,引出烟气环形烟道20与锌回收装置21的进气口相连,烟气返回环形烟道22与锌回收装置21的出气口相连。
15.所述的废钢预热竖炉2炉顶设有排烟口,具体设置在第三层废钢上与炉顶之间,排烟口后设除尘器4,引风机5和,煤气柜6,完成预热后的烟气经除尘后进煤气柜6回收。
16.一种煤炭干馏与废钢预热复合方法,采用上述设备,包括以下步骤:
17.(1)煤炭干馏炉1内煤粉经干馏,生成高温干馏煤粉与高温煤气,高温煤气经环形烟道7,进入废钢预热竖炉2;
18.(2)由废钢预热竖炉2炉顶,向炉内分批加入废钢,第一层废钢落在炉底,之后的废钢层由机械手9托扶,高温煤气通过环形烟道7及连接支气管8送入废钢预热竖炉2内,在炉底上部的四周进入炉内,由下向上,与各层废钢进行换热,获得预热后废钢,排出至保温废钢槽14。
19.所述的步骤(1)中,煤炭干馏炉1燃料可以用自产煤气,也可以采用其它燃气。燃烧段在喷煤段前。如果燃气热值不够,可以采用高炉冶炼使用的热风炉方式梯度升温,如果煤气热值满足要求,可以采用直燃式。
20.所述的步骤(1)中,高温煤气具有还原性,在将废钢升温同时,还可将废钢中的部分氧化铁皮还原为金属铁。
21.所述的步骤(1)中,高温煤气为净化后高温煤气,该步骤发生的具体过程为:煤炭干馏炉1的燃烧室产生的高温烟气进入干馏室后首先将喷煤枪喷入的煤粉干馏,干馏出的挥发分气体又会与烟气中的过剩氧气和燃烧产生的二氧化碳反应,煤粉和干馏煤粉也会与氧气和二氧化碳反应,煤粉中的水分也会参与炉内的复杂反应,经过复杂反应产生的煤气
及干馏煤粉尘在除尘室被初步净化,净化后高温煤气引到竖炉预热废钢。通过控制进入炉内氧气量控制干馏炉内出烟气温度,保证干馏炉排出烟气温度在1000℃以上,保证干馏出的挥发分充分裂解,保证废钢加热温度。
22.所述的干馏室1
‑
3底部设干馏煤收集槽1
‑
6,通过控制喷煤枪1
‑
4中的煤粉喷吹流量速度和煤粉粒度,控制煤粉干馏状态,颗粒大的煤粉在漂浮态时会干馏没有结束,落入炉底干馏煤收集槽时,会继续干馏,干馏过程需要大量热,会降低干馏煤的降温难度,在干馏煤收集槽发生的干馏属于低温干馏,干馏出的挥发分进入上部高温区后仍然会被裂解,排出干馏室的烟气不会有苯萘芬类高气化点物质,不会影响后部烟气干法除尘;干馏煤收集槽收集的高温干馏煤粉通过分段水冷间接降温,可以回收部分蒸汽和热水。如果助燃气体采用富氧空气,可以预热空气给干馏煤粉降温。
23.所述的步骤(2)中,废钢预热竖炉2通过设机械手9进行废钢托扶,以实现废钢分层加热,分层出料,每层废钢废钢量与转炉每次加入量相等,这样便于操作。
24.所述的步骤(2)中,第二层废钢由第一层机械手托扶,高温烟气经过预热第一层废钢后,获得的一次预热后烟气温度不会超过700℃,因此第一层机械手的材料选择要耐热700℃以上即可,这是耐热钢可以承受的。经过第二层废钢预热后,获得的二次预热后烟气温度不会超过400℃,因此第二层机械手的材料选择能耐热400℃以上即可;经过三层废钢预热后,获得的三次预热后烟气温度一般在130
‑
180℃温度,可以做烟气处理和除尘;每一层的烟气温度也决定于每一层废钢量,这取决于转炉容量、铁水温度、冶炼钢种,这是在设计时要考虑的,以此作为确定竖炉直径的依据。如果排烟温度过高,再增加竖炉高度,增加机械手和预热料层。
25.所述的废钢预热竖炉2底部材料要求耐热700℃以上,由于热烟气沿竖炉向上走,竖炉底部出钢系统受热温度约等于第二层废钢底部的温度,此处废钢温度一般不会超过700℃,因此,竖炉底部材料耐热只要耐热700℃即可。这样设计的好处在于第一层机械手不承受高温,机械手材料更容易选择,降低了设备维护费用,设备运行更加稳定。炉底也不承受高温,炉底设备材料选择也更经济。
26.所述的步骤(2)中,废钢经过等静压加料系统11,分批加入废钢预热竖炉2,具体过程为:废钢先加到上加料仓18,然后关闭上封闭板19,打开上翻板阀17,废钢落入下加料仓16,关闭翻板阀17,在向竖炉内加料时,打开下翻板阀15,废钢落下后关闭翻板阀15。上部封闭一直在双封闭状态。为了安全可以向加料仓内充保护气体;
27.所述的步骤(2)中,预热后废钢经过等静压出料系统10,层层排出,具体过程为:为了确保安全,在出料时向储料仓12内喷吹保护性气体保护,出料时先打开翻板阀门11,将第一层废钢卸到储料仓内的保温废钢槽14内,关闭翻板阀,向储料仓内加大喷吹保护性气体,打开侧封闭门13,将保温废钢槽14取出,关闭侧封闭门,降低保护气体喷吹量,保证储料仓内微正压;
28.所述的步骤(2)中,废钢由废钢预热竖炉2内出料加料放料过程如下:打开翻板卸料阀11,将废钢预热竖炉2内的第一层废钢卸到储料仓12内的保温废钢槽14,关闭翻板下料阀门11,打开侧封闭门13,将废钢取出,关闭侧封闭门13,关闭翻板下料阀门11后撤出第一层机械手,将第二层废钢卸到炉底,恢复第一层机械手到托扶状态,撤出第二层机械手,将第三层废钢卸到第一层机械手上,恢复第二层机械手到托扶状态,打开下封闭翻板阀15,将
下加料仓内的废钢加入竖炉内的第二层机械手上。
29.本发明的功过原理如下:
30.煤炭在1100℃以上的高温环境下干馏,干馏出的煤炭挥发分在高温环境下可以实现裂解,煤气中不会有苯奈芬类物质存在,产生的煤气便于回收利用。但是干馏后的煤气温度高,目前热量只是用于生产蒸汽发电,能源利用率较低。如果采用低温干馏,就会带来一系列的环保问题,很难通过环保审批。如果把煤炭干馏与废钢预热结合在一起,在高温段进行煤炭干馏,干馏煤炭后的中温煤气正好用于预热废钢,干馏煤炭后的中温煤气预热废钢不但不氧化废钢,还会把废钢的氧化铁皮还原成金属铁。预热废钢过程也正好使中温煤气降温,这样也避免了传统工艺中煤气冷却水的消耗,避免了废水和焦油类污染物的产生。这种还原气氛预热废钢,还可以实现金属态回收废钢中的锌。干馏煤炭产生的煤气不但可以满足自身工艺使用,还会有剩余煤气供应其它工序使用。
31.竖炉是所有工业炉窑里传热最好的热工设备。因此本专利技术采用竖炉作为废钢预热设备,热源来自于煤炭干馏炉。
32.如果经常预热高锌的轻薄料废钢,会造成竖炉内锌蒸汽富集,为此本案选择在600℃
‑
750℃温度区域将烟气部分引出,用特制的锌回收装置对烟气进行锌回收处理,然后再将做完锌回收后的烟气送回竖炉内继续预热废钢,这样也能将烟气中未被回收的锌蒸汽送回炉内并被上部低温废钢捕捉,在废钢下行过程中再次生成锌蒸汽,进入下一次回收。
33.由于竖炉内是还原性气氛,氮氧化物会被烟气中的还原性气体还原,因此烟气中的氮氧化物会很低。烟气中会有部分干馏煤粉逃逸到后部,这些干馏煤粉都是很好的活性炭,可以脱除烟气中的硫、二噁英、苯并芘、重金属等有害物质。如果烟气不能达标,可以在竖炉后部设置二次喷吹干馏煤粉吸附装置,干馏煤粉可一并脱除烟气中的硫、二噁英、苯并芘、重金属等有害物质。喷入的干馏煤粉与炉内粉尘在后部除尘器一并被捕捉。除尘器回收的粉尘及干馏煤粉可送到高炉喷煤系统,随喷吹煤粉一并喷吹高炉,实现资源化利用和无害化处理。
34.所述的废钢预热竖炉2设有喷吹干馏煤粉吸附装置,以保证废钢预热竖炉2烟气达标排放。
35.本发明的技术效果:
36.采用本发明的煤炭干馏与废钢预热复合设备进行废钢预热,能够综合实现良好的节能环保减碳技术效果,并给钢铁工业行业带来可观的经济效益和社会效益。
附图说明
37.图1为本发明实施例1的煤炭干馏与废钢预热复合设备装置结构示意图,其中:
[0038]1‑
煤炭干馏炉,1
‑
2氧燃枪,1
‑
3干馏室,1
‑
4喷煤枪,1
‑
5除尘室,1
‑
6干馏煤收集槽,2
‑
废钢预热竖炉,3
‑
锌回收系统,4
‑
除尘器,5
‑
引风机,6
‑
煤气柜,7
‑
环形烟道,8
‑
支气管,9
‑
机械手,10
‑
等静压出料系统,11
‑
翻板卸料阀,12
‑
储料仓,13
‑
侧封闭板,14
‑
保温废钢槽,15
‑
下封闭翻板阀,16
‑
下加料储料仓,17
‑
上封闭翻板阀,18
‑
上加料仓,19
‑
上封闭板,20
‑
烟气环形烟道,21
‑
锌回收装置,22
‑
烟气返回环形烟道,23
‑
出锌阀,24
‑
冷却系统,25
‑
等静压加料系统。1
‑
1燃烧室。
具体实施方式
[0039]
实施例1
[0040]
某钢厂有两座100吨转炉,由于受高炉铁水产量限制,转炉产钢量无法满足连铸机需求,经常造成断浇。为提高转炉产量只好想办法多加废钢,由于受热平衡限制,无法加入足够废钢,为此曾采取铁水包氧燃枪预热废钢,由于烟气氮氧化物、硫、二噁英超标被关停。同时,烧结工艺由于采用无烟煤做烧结燃料,vocs排放严重超标,当地环保部门要求必须采用没有挥发分的焦粉、干馏煤粉或兰碳粉做烧结燃料,当地焦粉无法满足需要,采用兰碳粉运距远运费高,到冬季兰碳粉涨价,运输也无法保证,想自己生产干馏煤粉,传统方法环保审批困难,为此采用本专利技术。
[0041]
一种煤炭干馏与废钢预热复合设备装置,其结构示意图如图1所示,详细结构如前发明内容部分所记载,设煤炭干馏炉1,燃气采用本工艺产生的煤气,全氧助燃。煤炭选用当地挥发分18的低灰分低硫煤,发热值6000千卡/公斤。在煤炭干馏炉2后设废钢预热竖炉2,竖炉型设计成方形,炉内有效截面为2米正方形,废钢平均堆比重为2吨/立方米,设计每层废钢装入量40吨,第一层机械手设在距离炉底出料翻板阀5.5米处,第二层机械手设在距离炉底出料翻板阀11米处,炉顶等静压加料系统下封闭翻板阀15设在距离炉底翻板阀18米处;
[0042]
炉顶等静压加料系统25设下加料储料仓16和上加料储料仓18,上下储料室之间设上封闭卸料翻板阀17,上储料仓18顶部用上封闭板19封闭,上下储料仓都用氮气做微正压保护;
[0043]
炉底出料系统负压较低,设单等静压封闭,竖炉底部设翻板卸料阀11、储料仓12和侧封闭板13,在储料仓12内设保温废钢槽14,储料仓设氮气微正压保护;
[0044]
竖炉底部设环形烟道7,连接支气管8距离炉底高度0.4米,干馏炉的高温煤气经过环形烟道7分配到支气管8进入竖炉余热废钢,干馏炉排放煤气温度控制在1100℃左右,废钢预热平均温度控制在700
‑
800℃;
[0045]
锌回收系统引气支气管设在第一层机械手下部,引出的烟气经过环形烟道20送进锌回收装置21,烟气经过除锌后从排气口进入环形烟道22,通过支气管送回炉内继续预热废钢。返回烟气的支气管设在第二层机械手下部,烟气靠上下压力差自循环,无需外力;回收的金属锌定期通过排锌阀23排出;
[0046]
设备经过半年运行,以废钢预热运行为主,废钢入转炉平均温度为740
‑
760℃;每炉废钢加入量超过35吨,比原来废钢预热每炉废钢加入量增加15吨,满足了连铸工艺要求,而且还可以提高拉坯速度;废钢无烧损;每天出废钢40
‑
45次,预热废钢1500吨左右,可以满足一座转炉生产。平均每天回收锌15吨左右;每天消耗量550吨左右,每天生产干馏煤粉420吨左右,本系统产生的煤气约50%自用,其余煤气用于自备电厂发电;
[0047]
本项目优点:
[0048]
由于用煤炭干馏余热预热废钢,节省了废钢预热能耗;
[0049]
由于用高温煤气预热废钢,废钢没有烧损,每年该项目可减少废钢烧损2万吨左右;
[0050]
每年该项目回收金属锌2000吨左右;
[0051]
每年生产绿色烧结燃料近14万吨,每年烧结工艺因此可以减排vocs一万吨以上;
[0052]
由于可以就地采购燃料生产保障更安全,燃料成本也低于外采购;
[0053]
由于煤炭采用高温干馏工艺,没有化工废水产生,也没有废气排放,投资也远少于传统工艺投资;
[0054]
由于采用废钢预热,单炉每年多消耗废钢20万吨左右,多产钢20万吨左右。与电弧炉断流程相比减排二氧化碳10万吨左右,与长流程冶炼相比减排二氧化碳40万吨;
[0055]
通过上述分析可以看出,本发明的技术方案能够实现良好的节能环保减碳技术效果,能够给钢铁工业行业带来可观的经济效益和社会效益。