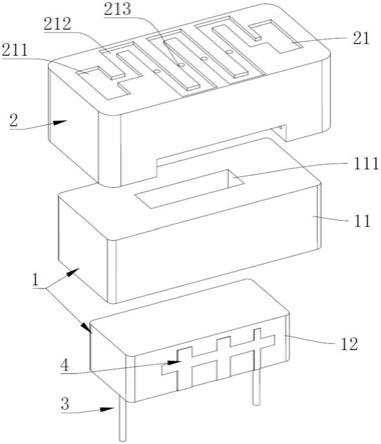
1.本实用新型涉及电子烟陶瓷雾化芯技术领域,特别是涉及一种基于烧制热片结构的雾化芯。
背景技术:
2.电子烟主要用于戒和替代香烟,它可以模拟香烟的味道,但抽电子烟时却不会释放对人体有害的焦油、尼古丁和二手烟雾,它能提高尼古丁替代疗法的戒烟成功率,因此,电子烟在推出不久便受到市场的追捧和国家的重视。电子雾化香烟,其原理为发烟剂在雾化系统的电加热元件上受热气化成高温蒸汽并向开口端喷出,喷出后的蒸汽在大气中膨胀冷凝成烟状的微小液滴,从而形成类似传统卷烟的烟雾。
3.其中,雾化芯是电子烟的关键部件之一,现有的雾化芯包括有棉芯雾化、陶瓷雾化和超声波雾化,作用都是将烟油加热雾化。现有的陶瓷电子烟雾化器存在不足,由于发热片结构单一,在发热雾化过程中稳定性差,同时发热雾化效率低,导致口感不佳等问题存在需要进一步改进的。
技术实现要素:
4.为解决上述问题,本实用新型提供一种能够实现快速传热和发热,对发热体内进行快速加热,加热雾化效率高,并采用一体烧制成型的发热和传热结构,结构可靠,传热效果好,雾化效率高的基于烧制热片结构的雾化芯。
5.本实用新型所采用的技术方案是:一种基于烧制热片结构的雾化芯,包括发热体、包覆于发热体的硅胶座、设于发热体底部的发热组件、及设于发热体两侧并与发热组件连接的传热组件;所述发热体包括上端部和下端部,所述上端部开设有第一微孔,所述下端部开设有第二微孔,所述第一微孔的孔径大于所述第二微孔的孔径;所述发热组件包括发热引线、连接于发热引线的接电片,所述传热组件包括若干组的传热引线,所述传热引线与所述发热引线连接,所述传热引线一体烧制成型于下端部两侧。
6.对上述方案的进一步改进为,所述发热体为陶瓷发热体,所述上端部与下端部为一体成型。
7.对上述方案的进一步改进为,所述上端部开设有导油腔,所述硅胶座对应导油腔设有导油槽,所述导油槽连通至导油腔。
8.对上述方案的进一步改进为,所述上端部朝两侧延伸有延伸台阶,所述硅胶套包覆于延伸台阶。
9.对上述方案的进一步改进为,所述上端部与下端部之间设有快速传热部,所述快速传热部为金属颗粒组成、并一体成型于上端部与下端部之间。
10.对上述方案的进一步改进为,所述导油槽包括进油口、连接于进油口的迷宫油路,所述迷宫油路开设有进油孔,所述进油孔连通至所述导油腔。
11.对上述方案的进一步改进为,所述下端部靠近上端部两侧开设有密封卡槽,所述
硅胶套设有密封卡扣,所述密封卡扣卡入至密封卡槽内。
12.对上述方案的进一步改进为,所述发热引线设有弯曲部,所述传热引线连接于所述弯曲部。
13.对上述方案的进一步改进为,所述传热引线设有若干组,若干组的传热引线设有贯通线连接。
14.一种基于烧制热片结构的雾化芯的制备工艺,包括如下步骤:
15.步骤s1,制备下端部,准备下端部成型的材料,包括将陶瓷骨料和助烧剂进行干燥处理;将干燥后的陶瓷骨料、助烧剂和造孔剂进行混料,得到预混料;将所述预混料与粘结剂、分散剂进行混炼得到混炼陶瓷料;对所述混炼陶瓷料进行造粒,得到颗粒状陶瓷喂料;将所述颗粒状陶瓷喂料通过注射入发热体治具内、并与热片连接形成下端部生坯;在形成下端部生坯的同时也成型发热槽和传热槽;
16.步骤s2,在下端部生坯表面分散放入金属颗粒;
17.步骤s3,制备下端部,准备上端部的成型材料,包括将陶瓷骨料和助烧剂进行干燥处理;将干燥后的陶瓷骨料、助烧剂和造孔剂进行混料,得到预混料;将所述预混料与粘结剂、分散剂进行混炼得到混炼陶瓷料;对所述混炼陶瓷料进行造粒,得到颗粒状陶瓷喂料,将所述颗粒状陶瓷喂料通过注射入发热体治具内将金属颗粒覆盖在下端部生坯表面,形成上端部生坯,此时上端部生坯与下端部生坯形成发热体生坯;
18.步骤s4,在发热槽和传热槽内注入钢溶液流体,并等待钢溶液流体冷却形成发热组件和传热组件;
19.步骤s5,将发热体生坯从发热体治具内取出,将取出的发热体生坯在煅烧氧化铝的埋粉条件下,以预设的脱脂条件进行脱脂处理;将脱脂得到的陶瓷坯于大气条件下,以预设的烧结条件进行烧结,得到烧制热片雾化芯。
20.对上述方案的进一步改进为,所述煅烧氧化铝的粒径为30~100μm,所述煅烧氧化铝的埋粉条件是埋粉深度为5~6cm。
21.对上述方案的进一步改进为,所述脱脂条件为:以0.3~1.1℃/min的升温速率从室温升温至120~200℃保温1.0~1.5h,接着以0.15~0.4℃/min的升温速率升温至220~280℃,再以0.4~0.6℃/min的升温速率升温至400~560℃保温1.0~3.5h,然后以1.4~3.6℃/min的升温速率升温至800~900℃保温0.3~1.8h,最后随炉冷却。
22.对上述方案的进一步改进为,所述烧结条件为:以3~8℃/min的升温速率从室温升温至800~960℃保温0.3~1.8h,接着以1.6~2.8℃/min的升温速率升温至1000~1300℃保温1.2~2.8h,最后随炉冷却。
23.对上述方案的进一步改进为,所述步骤s2中,干燥处理的条件为100~150℃干燥2
‑
4h;混炼的条件是在90℃
‑
160℃条件下混炼3
‑
5h;注射成型中注射温度为50℃
‑
70℃;
24.所述预混料的过程为,以预混料总量为100%,按质量百分比计,所述陶瓷骨料的质量百分比为55~70%,所述助烧剂的质量百分比为20~25%,所述造孔剂的质量百分比为10~20%。
25.对上述方案的进一步改进为,所述步骤s4中,干燥处理的条件为100~150℃干燥2
‑
3h;混炼的条件是在80℃
‑
150℃条件下混炼2
‑
3h;注射成型中注射温度为40℃
‑
80℃。
26.对上述方案的进一步改进为,所述预混料的过程为,以预混料总量为100%,按质
量百分比计,所述陶瓷骨料的质量百分比为45~60%,所述助烧剂的质量百分比为20~25%,所述造孔剂的质量百分比为20~30%。
27.对上述方案的进一步改进为,所述陶瓷骨料为硅藻土、长石、石英砂中的至少一种;所述助烧剂为低温无铅玻璃粉、高岭土和电气石中的至少一种;所述粘结剂为石蜡、蜂蜡、棕榈蜡、聚乙烯中的至少一种;所述造孔剂为聚甲基丙烯酸甲酯、聚乙烯醇、聚苯乙烯中的至少一种;所述分散剂为硬脂酸。
28.本实用新型的有益效果是:
29.相比传统的陶瓷雾化芯,本实用新型在发热体底部设置发热组件,两侧设置传热组件,在配合发热组件和传热组件,能够实现快速传热和发热,对发热体内进行快速加热,加热雾化效率高,并采用一体烧制成型的发热和传热结构,结构可靠,传热效果好,雾化效率高。具体是,设置了发热体、包覆于发热体的硅胶座、设于发热体底部的发热组件、及设于发热体两侧并与发热组件连接的传热组件;所述发热体包括上端部和下端部,所述上端部开设有第一微孔,所述下端部开设有第二微孔,所述第一微孔的孔径大于所述第二微孔的孔径;所述发热组件包括发热引线、连接于发热引线的接电片,所述传热组件包括若干组的传热引线,所述传热引线与所述发热引线连接,所述传热引线一体烧制成型于下端部两侧。采用不同孔径的微孔,可通过不同体积的烟油颗粒成分,当烟油成分种类足够多时,烟油雾化口感更佳丰富。
30.基于烧制热片结构的雾化芯的制备工艺,过程为:制备下端部,准备下端部成型的材料,包括将陶瓷骨料和助烧剂进行干燥处理;将干燥后的陶瓷骨料、助烧剂和造孔剂进行混料,得到预混料;将所述预混料与粘结剂、分散剂进行混炼得到混炼陶瓷料;对所述混炼陶瓷料进行造粒,得到颗粒状陶瓷喂料;将所述颗粒状陶瓷喂料通过注射入发热体治具内、并与热片连接形成下端部生坯;在形成下端部生坯的同时也成型发热槽和传热槽;在下端部生坯表面分散放入金属颗粒;制备下端部,准备上端部的成型材料,包括将陶瓷骨料和助烧剂进行干燥处理;将干燥后的陶瓷骨料、助烧剂和造孔剂进行混料,得到预混料;将所述预混料与粘结剂、分散剂进行混炼得到混炼陶瓷料;对所述混炼陶瓷料进行造粒,得到颗粒状陶瓷喂料,将所述颗粒状陶瓷喂料通过注射入发热体治具内将金属颗粒覆盖在下端部生坯表面,形成上端部生坯,此时上端部生坯与下端部生坯形成发热体生坯;在发热槽和传热槽内注入钢溶液流体,并等待钢溶液流体冷却形成发热组件和传热组件;将发热体生坯从发热体治具内取出,将取出的发热体生坯在煅烧氧化铝的埋粉条件下,以预设的脱脂条件进行脱脂处理;将脱脂得到的陶瓷坯于大气条件下,以预设的烧结条件进行烧结,得到烧制热片雾化芯;在完成发热体生坯制造后填充入钢溶液流体,一体性强,在经过后续进行烧结成型,形成一体,结构可靠,加热和传热效果好,雾化效率高。
附图说明
31.图1为本实用新型的爆炸结构示意图;
32.图2为本实用新型另一视角的爆炸结构示意图;
33.图3为本实用新型的俯视示意图;
34.图4为图3中a
‑
a的剖视图;
35.图5为本实用新型的制造工艺流程示意图。
36.附图标记说明:发热体1、上端部11、导油腔111、延伸台阶112、下端部12、密封卡扣121、快速传热部13、硅胶座2、导油槽21、进油口211、迷宫油路212、进油孔213、发热组件3、发热引线31、弯曲部311、接电片32、传热组件4、传热引线41、贯通线411。
具体实施方式
37.为了便于理解本实用新型,下面将参照相关附图对本实用新型进行更全面的描述。附图中给出了本实用新型的较佳实施例。但是,本实用新型可以以许多不同的形式来实现,并不限于本文所描述的实施例。相反地,提供这些实施例的目的是使对本实用新型的公开内容的理解更加透彻全面。
38.需要说明的是,当元件被称为“固定于”另一个元件,它可以直接在另一个元件上或者也可以存在居中的元件。当一个元件被认为是“连接”另一个元件,它可以是直接连接到另一个元件或者可能同时存在居中元件。
39.除非另有定义,本文所使用的所有的技术和科学术语与属于本实用新型的技术领域的技术人员通常理解的含义相同。本文中在本实用新型的说明书中所使用的术语只是为了描述具体的实施例的目的,不是旨在于限制本实用新型。
40.如图1~图5所示,一种基于烧制热片结构的雾化芯,包括发热体1、包覆于发热体1的硅胶座2、设于发热体1底部的发热组件3、及设于发热体1两侧并与发热组件3连接的传热组件4;所述发热体1包括上端部11和下端部12,所述上端部11开设有第一微孔,所述下端部12开设有第二微孔,所述第一微孔的孔径大于所述第二微孔的孔径;所述发热组件3包括发热引线31、连接于发热引线31的接电片32,所述传热组件4包括若干组的传热引线41,所述传热引线41与所述发热引线31连接,所述传热引线41一体烧制成型于下端部12两侧。
41.发热体1为陶瓷发热体1,所述上端部11与下端部12为一体成型,采用一体成型的结构,方便雾化液体的导入,结构可靠,一体性腔。
42.上端部11开设有导油腔111,所述硅胶座2对应导油腔111设有导油槽21,所述导油槽21连通至导油腔111,进一步改进为,所述导油槽21包括进油口211、连接于进油口211的迷宫油路212,所述迷宫油路212开设有进油孔213,所述进油孔213连通至所述导油腔111,通过导油腔111配合导油槽21用于导油传输,导油效果好,方便快速传热雾化。
43.上端部11朝两侧延伸有延伸台阶112,所述硅胶座包覆于延伸台阶112,通过延伸台阶112加强导油面积,同时也方便结构的固定安装。
44.上端部11与下端部12之间设有快速传热部13,所述快速传热部13为金属颗粒组成、并一体成型于上端部11与下端部12之间,通过快速传热部13实现快速传热,能够进一步提升传热效果和雾化效果。
45.下端部12靠近上端部11两侧开设有密封卡槽,所述硅胶座设有密封卡扣121,所述密封卡扣121卡入至密封卡槽内,通过密封卡槽配合密封卡扣121对结构进行密封,密封效果好。
46.发热引线31设有弯曲部311,所述传热引线41连接于所述弯曲部311,通过弯曲部311配合发热引线31连接,方便快速传热。
47.传热引线41设有若干组,若干组的传热引线41设有贯通线411连接,设置贯通线411保证传输的稳定性。
48.一种基于烧制热片结构的雾化芯的制备工艺,包括如下步骤:
49.步骤s1,制备下端部12,准备下端部12成型的材料,包括将陶瓷骨料和助烧剂进行干燥处理;将干燥后的陶瓷骨料、助烧剂和造孔剂进行混料,得到预混料;将所述预混料与粘结剂、分散剂进行混炼得到混炼陶瓷料;对所述混炼陶瓷料进行造粒,得到颗粒状陶瓷喂料;将所述颗粒状陶瓷喂料通过注射入发热体1治具内、并与热片连接形成下端部12生坯;在形成下端部12生坯的同时也成型发热槽和传热槽;
50.步骤s2,在下端部12生坯表面分散放入金属颗粒;
51.步骤s3,制备下端部12,准备上端部11的成型材料,包括将陶瓷骨料和助烧剂进行干燥处理;将干燥后的陶瓷骨料、助烧剂和造孔剂进行混料,得到预混料;将所述预混料与粘结剂、分散剂进行混炼得到混炼陶瓷料;对所述混炼陶瓷料进行造粒,得到颗粒状陶瓷喂料,将所述颗粒状陶瓷喂料通过注射入发热体1治具内将金属颗粒覆盖在下端部12生坯表面,形成上端部11生坯,此时上端部11生坯与下端部12生坯形成发热体1生坯;
52.步骤s4,在发热槽和传热槽内注入钢溶液流体,并等待钢溶液流体冷却形成发热组件3和传热组件4;
53.步骤s5,将发热体1生坯从发热体1治具内取出,将取出的发热体1生坯在煅烧氧化铝的埋粉条件下,以预设的脱脂条件进行脱脂处理;将脱脂得到的陶瓷坯于大气条件下,以预设的烧结条件进行烧结,得到烧制热片雾化芯;
54.本实施例中,煅烧氧化铝的粒径为30~100μm,所述煅烧氧化铝的埋粉条件是埋粉深度为5~6cm。
55.本实施例中,脱脂条件为:以0.3~1.1℃/min的升温速率从室温升温至120~200℃保温1.0~1.5h,接着以0.15~0.4℃/min的升温速率升温至220~280℃,再以0.4~0.6℃/min的升温速率升温至400~560℃保温1.0~3.5h,然后以1.4~3.6℃/min的升温速率升温至800~900℃保温0.3~1.8h,最后随炉冷却。
56.本实施例中,烧结条件为:以3~8℃/min的升温速率从室温升温至800~960℃保温0.3~1.8h,接着以1.6~2.8℃/min的升温速率升温至1000~1300℃保温1.2~2.8h,最后随炉冷却。
57.本实施例中,步骤s2中,干燥处理的条件为100~150℃干燥2
‑
4h;混炼的条件是在90℃
‑
160℃条件下混炼3
‑
5h;注射成型中注射温度为50℃
‑
70℃。
58.本实施例中,预混料的过程为,以预混料总量为100%,按质量百分比计,所述陶瓷骨料的质量百分比为55~70%,所述助烧剂的质量百分比为20~25%,所述造孔剂的质量百分比为10~20%。
59.本实施例中,步骤s4中,干燥处理的条件为100~150℃干燥2
‑
3h;混炼的条件是在80℃
‑
150℃条件下混炼2
‑
3h;注射成型中注射温度为40℃
‑
80℃。
60.本实施例中,预混料的过程为,以预混料总量为100%,按质量百分比计,所述陶瓷骨料的质量百分比为45~60%,所述助烧剂的质量百分比为20~25%,所述造孔剂的质量百分比为20~30%。
61.本实施例中,陶瓷骨料为硅藻土、长石、石英砂中的至少一种;所述助烧剂为低温无铅玻璃粉、高岭土和电气石中的至少一种;所述粘结剂为石蜡、蜂蜡、棕榈蜡、聚乙烯中的至少一种;所述造孔剂为聚甲基丙烯酸甲酯、聚乙烯醇、聚苯乙烯中的至少一种;所述分散
剂为硬脂酸。
62.本实用新型在发热体1底部设置发热组件3,两侧设置传热组件4,在配合发热组件3和传热组件4,能够实现快速传热和发热,对发热体1内进行快速加热,加热雾化效率高,并采用一体烧制成型的发热和传热结构,结构可靠,传热效果好,雾化效率高。具体是,设置了发热体1、包覆于发热体1的硅胶座2、设于发热体1底部的发热组件3、及设于发热体1两侧并与发热组件3连接的传热组件4;所述发热体1包括上端部11和下端部12,所述上端部11开设有第一微孔,所述下端部12开设有第二微孔,所述第一微孔的孔径大于所述第二微孔的孔径;所述发热组件3包括发热引线31、连接于发热引线31的接电片32,所述传热组件4包括若干组的传热引线41,所述传热引线41与所述发热引线31连接,所述传热引线41一体烧制成型于下端部12两侧。采用不同孔径的微孔,可通过不同体积的烟油颗粒成分,当烟油成分种类足够多时,烟油雾化口感更佳丰富。
63.基于烧制热片结构的雾化芯的制备工艺,过程为:制备下端部12,准备下端部12成型的材料,包括将陶瓷骨料和助烧剂进行干燥处理;将干燥后的陶瓷骨料、助烧剂和造孔剂进行混料,得到预混料;将所述预混料与粘结剂、分散剂进行混炼得到混炼陶瓷料;对所述混炼陶瓷料进行造粒,得到颗粒状陶瓷喂料;将所述颗粒状陶瓷喂料通过注射入发热体1治具内、并与热片连接形成下端部12生坯;在形成下端部12生坯的同时也成型发热槽和传热槽;在下端部12生坯表面分散放入金属颗粒;制备下端部12,准备上端部11的成型材料,包括将陶瓷骨料和助烧剂进行干燥处理;将干燥后的陶瓷骨料、助烧剂和造孔剂进行混料,得到预混料;将所述预混料与粘结剂、分散剂进行混炼得到混炼陶瓷料;对所述混炼陶瓷料进行造粒,得到颗粒状陶瓷喂料,将所述颗粒状陶瓷喂料通过注射入发热体1治具内将金属颗粒覆盖在下端部12生坯表面,形成上端部11生坯,此时上端部11生坯与下端部12生坯形成发热体1生坯;在发热槽和传热槽内注入钢溶液流体,并等待钢溶液流体冷却形成发热组件3和传热组件4;将发热体1生坯从发热体1治具内取出,将取出的发热体1生坯在煅烧氧化铝的埋粉条件下,以预设的脱脂条件进行脱脂处理;将脱脂得到的陶瓷坯于大气条件下,以预设的烧结条件进行烧结,得到烧制热片雾化芯;在完成发热体1生坯制造后填充入钢溶液流体,一体性强,在经过后续进行烧结成型,形成一体,结构可靠,加热和传热效果好,雾化效率高。
64.以上所述实施例仅表达了本实用新型的几种实施方式,其描述较为具体和详细,但并不能因此而理解为对本实用新型专利范围的限制。应当指出的是,对于本领域的普通技术人员来说,在不脱离本实用新型构思的前提下,还可以做出若干变形和改进,这些都属于本实用新型的保护范围。因此,本实用新型专利的保护范围应以所附权利要求为准。