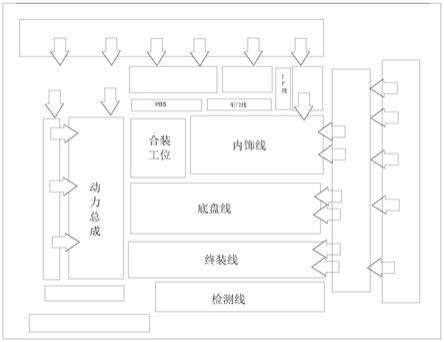
1.本发明涉及柔性化生产技术领域,具体涉及一种柔性化汽车生产线与生产方法。
背景技术:
2.现代化的生产对于质量和效率的追求近乎极致,尤其是现代大型设备制造领域,其效率与灵活性更是直接影响到工厂的生存前景。目前汽车整车厂中存在以下严重影响生产效率的问题:1)一次性投资,土建设备为固定投资;2)固定设备较多,空间利用不灵活,物料边缘存储,转运成本高;3)单间产品影响全线产品质量;4)建设周期长,停机改造周期长;5)单型号连续生产效率高,多型号生产饱和度低;6)需要定期维护,维护室需要整场停机,影响正常生产。针对上述问题,申请人提出了将柔性化生产技术应用于汽车整车生产领域,通过优化工艺流程,合理设定生产节拍,三流合一,对整个生产线进行柔性布局,从而实现空间合理化、路径最短化、库存最小化和错误最低化。
技术实现要素:
3.本发明的目的在于提供一种柔性化汽车生产线与生产方法,以解决上述背景技术中提出的目前在传统汽车总装生成线中存在固定投资高、转运成本高、改造周期长和多型号切换生产时效率较低的问题。
4.为实现上述目的,本发明提供如下技术方案:一种柔性化汽车生产线,包括:
5.pbs立库,其用作涂装车间与总装车间之间的缓冲、存储区域;
6.内饰线,包括12个标准工位、3个差异工位和至少20台带举升背负式agv运输小车,所述带举升背负式agv运输小车将工件从所述pbs立库运输至所述内饰线,并依照工艺流程在个工位之间运输;其用于完成车辆内饰件的安装;
7.动力总成线,其包括15个标准工位、4个差异工位和至少25台带举升背负式agv运输小车;其用于完成车辆动力组件的安装;
8.底盘线,其包括包括22个标准工位、4个差异工位和至少30台背负式agv运输小车,其用于完成车辆底盘组件的安装;
9.合装工位,其设置于所述内饰线、所述动力总成线、所述底盘线之间,将完成内饰、动力总成和底盘安装的车辆组件在合装标准工位上进行定点合装;
10.终装线,其设置于所述底盘线和所述动力总成线旁侧,包括15个标准工位、3个差异工位和至少23台背负式agv运输小车;对完成总装的车辆安装剩余全部配件,形成整车;
11.检测线,其设置于所述终装线的远离所述底盘线的另一侧,其用于对完成组装的整车进行检测;
12.优选的,还包括车门线,其设置于pbs立库旁,用于完成车门密封条、车门电器件、车门外饰板的安装,及对安装完成的车门进行检测。
13.优选的,还包括仪表分装线,其设置于所述车门线旁,其用于完成仪表管梁、hvac、仪表板、转向管柱和相关电器件的安装,并对安装完成的全部仪表功能进行检测。
14.优选的,还包括至少一座淋雨房,其用于对完成终装和全部测试工作的出厂整车进行淋雨测试,以便测试整车的密封性。
15.优选的,车门线中还设有天窗自动装配装置和风挡自动装配装置,分别设置于所述车门线的其中一个标准工位处,用于完成天窗和风挡的自动装配。
16.优选的,底盘线中的标准工位处还设有仪表盘自动化装配装置和座椅自动装配设备,用于完成仪表盘与座椅的自动化安装。
17.优选的,合装工位处设有合装自动拧紧装置与玻璃自动涂胶及装配装置,用于完成玻璃的安装,合装螺丝的拧紧。
18.一种柔性化汽车生产方法,使用如上述任意一种柔性化汽车生产线,其特征在于,包括以下步骤:
19.步骤一:将存储于pbs立库中的涂装件通过agv小车输送至所述内饰线,在内饰线依次设置的多个工位上完成拆车门、罩板及背门安装、vin打刻、堵盖隔热垫、天窗安装与装调、行李架安装、高低压线束安装、制动泵及踏板支架安装、仪表总成安装、玻璃涂胶、铭牌及vin黏贴、地毯铺设、顶棚安装、气帘及a内饰板安装、安全带安装、天窗开关、遮阳板及室内灯安装、后排风管安装、雨刮电机安装、前后风挡安装,完成上述安装后,通过agv小车输送至所述合装工位;
20.步骤二:在所述底盘线中设置的多个工位上完成装饰板安装、副仪表板安装、360全景影像ecu安装、手刹档把安装、车身底部管线安装、迎宾踏板安装、氛围灯安装、座椅安装、轮胎安装、行李舱附件安装、贴标识、方向盘安装、助力转向安装、前后车灯安装、前端模块杠安装、保险杠安装和车门安装工序;
21.步骤三:在所述动力总成线设置的多个工位上完成esc分装、动力总成分装、前悬架分装、后悬架分装以及散热器前端模块分装;
22.步骤四:在所述底盘线中进行底盘组件安装;
23.步骤五:在所述合装工位处进行定点合装;
24.步骤六:在所述终装线的多个工位处完成全部零部件的终装;
25.步骤七:对完成终装的整车进行完整的功能检测;
26.步骤八:将完成测试的整车运送至所述淋雨房进行密封性测试。
27.优选的,步骤七中的功能测试包括电检、线上外观检测、颠簸路测试、四轮定位测试、侧滑测试、adas测试转毂测试、制动力测试、低怠速测试和高怠速测试。
28.优选的,在汽车柔性组装之前,需要根据生成计划对所述标准工位与差异工位数量、agv小车数量以及他调度方法以及上述各分装配线的位置设置方案进行统一的柔性规划。
29.与现有技术相比,本发明的有益效果是:
30.该柔性化汽车生产线通过将汽车生产线合理的划分为内饰线、动力总成线、底盘线、合装工位和终装线,现在各分线完成内饰、动力总成、底盘的安装,最后在合装工位完成定点合装,最后由终装线完成终装,运送至检测线进行检测后出厂,全程物料的转运由设有agv小车的柔性运输先完成,辅以合理的工位设置,以及各分线之间“三面包围、向内推进”位置关系的柔性设计,加上多种agv设备及自动化设备的协同作业,实现了汽车生产线的整体的柔性化设计,实现空间合理化、路径最短化、库存最小化和错误最低化,从而便于后续
扩展与改造;与此同时,在保障装配可靠性与生产稳定性的同时兼具了高工位利用率,到机械逻辑限制的优点。
附图说明
31.图1为本发明的柔性化汽车生产线的整体布局示意图;
32.图2为本发明柔性化汽车生产线的总装工艺流程图;
33.图3为本发明柔性化汽车生产线的内饰线的运行流程图;
34.图4为本发明柔性化汽车生产线的底盘线的运行流程图。
具体实施方式
35.下面将结合本发明实施例中的附图,对本发明实施例中的技术方案进行清楚、完整地描述,显然,所描述的实施例仅仅是本发明一部分实施例,而不是全部的实施例。基于本发明中的实施例,本领域普通技术人员在没有做出创造性劳动前提下所获得的所有其他实施例,都属于本发明保护的范围。
36.请参阅图1,本发明提供一种技术方案:一种柔性化汽车生产线与生产方法,包括:pbs立库,其用作涂装车间与总装车间之间的缓冲、存储区域;
37.请参阅图3,1内饰线,包括12个标准工位、3个差异工位和至少20台带举升背负式agv运输小车,所述带举升背负式agv运输小车将工件从所述pbs立库运输至所述内饰线,并依照工艺流程在个工位之间运输;其用于完成车辆内饰件的安装;动力总成线,其包括15个标准工位、4个差异工位和至少25台带举升背负式agv运输小车;其用于完成车辆动力组件的安装;请参阅图4,底盘线,其包括包括22个标准工位、4个差异工位和至少30台背负式agv运输小车,其用于完成车辆底盘组件的安装;合装工位,其设置于所述内饰线、所述动力总成线、所述底盘线之间,将完成内饰、动力总成和底盘安装的车辆组件在合装标准工位上进行定点合装;终装线,其设置于所述底盘线和所述动力总成线旁侧,包括15个标准工位、3个差异工位和至少23台背负式agv运输小车;对完成总装的车辆安装剩余全部配件,形成整车。
38.优选的,还包括车门线,其设置于pbs立库旁,用于完成车门密封条、车门电器件、车门外饰板的安装,及对安装完成的车门进行检测。
39.优选的,还包括仪表分装线,其设置于所述车门线旁,其用于完成仪表管梁、hvac、仪表板、转向管柱和相关电器件的安装,并对安装完成的全部仪表功能进行检测。
40.优选的,还包括至少一座淋雨房,其用于对完成终装和全部测试工作的出厂整车进行淋雨测试,以便测试整车的密封性。车门线中还设有天窗自动装配装置和风挡自动装配装置,分别设置于所述车门线的其中一个标准工位处,用于完成天窗和风挡的自动装配。底盘线中的标准工位处还设有仪表盘自动化装配装置和座椅自动装配设备,用于完成仪表盘与座椅的自动化安装。合装工位处设有合装自动拧紧装置与玻璃自动涂胶及装配装置,用于完成玻璃的安装,合装螺丝的拧紧。
41.其工作原理:一种柔性化汽车生产方法,包括以下步骤:
42.步骤一:将存储于pbs立库中的涂装件通过agv小车输送至所述内饰线,在内饰线依次设置的多个工位上完成拆车门、罩板及背门安装、vin打刻、堵盖隔热垫、天窗安装与装
调、行李架安装、高低压线束安装、制动泵及踏板支架安装、仪表总成安装、玻璃涂胶、铭牌及vin黏贴、地毯铺设、顶棚安装、气帘及a内饰板安装、安全带安装、天窗开关、遮阳板及室内灯安装、后排风管安装、雨刮电机安装、前后风挡安装,完成上述安装后,通过agv小车输送至所述合装工位;
43.步骤二:在所述底盘线中设置的多个工位上完成装饰板安装、副仪表板安装、360全景影像ecu安装、手刹档把安装、车身底部管线安装、迎宾踏板安装、氛围灯安装、座椅安装、轮胎安装、行李舱附件安装、贴标识、方向盘安装、助力转向安装、前后车灯安装、前端模块杠安装、保险杠安装和车门安装工序;
44.步骤三:在所述动力总成线设置的多个工位上完成esc分装、动力总成分装、前悬架分装、后悬架分装以及散热器前端模块分装;
45.步骤四:在所述底盘线中进行底盘组件安装;
46.步骤五:在所述合装工位处进行定点合装;
47.步骤六:在所述终装线的多个工位处完成全部零部件的终装;
48.步骤七:对完成终装的整车进行完整的功能检测;
49.步骤八:将完成测试的整车运送至所述淋雨房进行密封性测试。
50.优选的,步骤七中的功能测试包括电检、线上外观检测、颠簸路测试、四轮定位测试、侧滑测试、adas测试转毂测试、制动力测试、低怠速测试和高怠速测试。
51.优选的,在汽车柔性组装之前,需要根据生成计划对所述标准工位与差异工位数量、agv小车数量以及他调度方法以及上述各分装配线的位置设置方案进行统一的柔性规划。
52.该柔性化汽车生产线通过将汽车生产线合理的划分为内饰线、动力总成线、底盘线、合装工位和终装线,现在各分线完成内饰、动力总成、底盘的安装,最后在合装工位完成定点合装,最后由终装线完成终装,运送至检测线进行检测后出厂,全程物料的转运由设有agv小车的柔性运输先完成,辅以合理的工位设置,以及各分线之间“三面包围、向内推进”位置关系的柔性设计,加上多种agv设备及自动化设备的协同作业,实现了汽车生产线的整体的柔性化设计,实现空间合理化、路径最短化、库存最小化和错误最低化,从而便于后续扩展与改造;与此同时,在保障装配可靠性与生产稳定性的同时兼具了高工位利用率,到机械逻辑限制的优点。
53.尽管已经示出和描述了本发明的实施例,对于本领域的普通技术人员而言,可以理解在不脱离本发明的原理和精神的情况下可以对这些实施例进行多种变化、修改、替换和变型,本发明的范围由所附权利要求及其等同物限定。