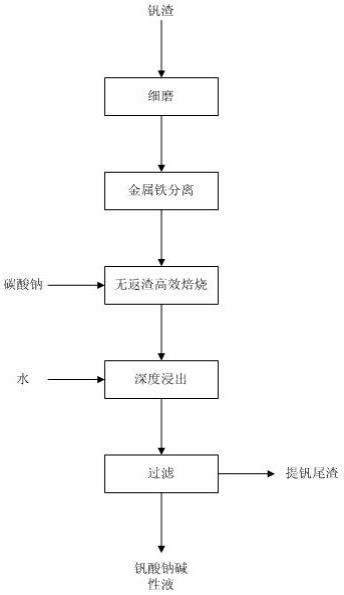
1.本发明涉及钒渣钠化焙烧提钒技术领域,尤其涉及一种钒渣钠化焙烧提钒的方法。
背景技术:
2.钒渣为含钒生铁氧化吹炼所得,为国内外主要的提钒原料,约占提钒原料总量的90%左右。而钠化焙烧提钒工艺因技术成熟,被广泛的应用于钒渣提钒,约占目前钒渣提钒行业的80%,故钠化焙烧提钒为当前钒行业的主流提钒技术。
3.钒渣钠化焙烧是将钒渣和碳酸钠混合后,于800℃左右氧化焙烧。氧化焙烧过程中发生多种反应,包括钒铁尖晶石的氧化、金属铁的氧化、低价钒的钠化和低价钒的氧化等过程,其中铁的氧化会产生大量的热,导致物料局部过热而产生熔体导致焙烧过程熔结。低价钒被氧化成五价钒,进而五价钒与碳酸钠反应形成偏钒酸钠,而偏钒酸钠融点较低,故易形成液相熔体,导致焙烧物料熔结。物料的熔结一方面导致大量的钒被包裹,影响钒的收率,另一方面容易导致回转窑结圈或多膛炉内部粘结,恶化焙烧工况,导致停炉停产。为了解决以上问题,现有技术是将部分提钒尾渣返回与钒渣进行混合以降低钒渣焙烧过程中的液相含量,避免物料烧结,但返回的尾渣量约为钒渣量的0.8~1.2倍,大大降低了焙烧工序的单次物料处理能力,降低了系统的生产效率。
4.专利cn102477491a公布了一种钒渣钠化焙烧的方法,该种方法是将钒渣与氧化剂进行预反应将钒渣中的低价钒氧化成五价钒,进而将氧化后的钒渣降温并与碳酸钠混合并升温焙烧,该种方法有效解决了钒渣焙烧过程中的熔结问题,但因需要两次焙烧,且一次焙烧后,需降温后混料升温进行二次焙烧,热能被无效消耗,能耗高。
5.专利cn102851507b公布了一种解决钒渣焙烧熔结问题的方法,该种方法是首先是将钒渣与纯碱混合物料于弱氧化气氛下进行焙烧,而后将焙烧熟料于强氧化气氛下进行二次焙烧,该种方法能够有效控制物料中的液相含量,进而避免了钒渣熔结的现象,但该种方法仍旧采用两段焙烧的方法,工艺流程长,能耗高。
6.综上所述,当前钒渣钠化焙烧提钒技术是通过返回尾渣或多段焙烧的方式解决钒渣钠化焙烧过程中物料烧结问题,普遍存在流程长,能耗高,钒收率低的问题,因此亟需开发新一种新的钒渣钠化焙烧方法,以解决当前钒渣钠化焙烧过程中所存在的问题。
技术实现要素:
7.为了解决上述技术问题,本发明提供了一种钒渣钠化焙烧提钒的方法,在解决物料烧结问题的前提下,无需返料,一次焙烧,流程短,能耗低。
8.为实现此技术目的,本发明采用如下方案:钒渣钠化焙烧提钒的方法,按如下步骤进行:s1、将钒渣倒入多级立式磨机中进行充分研磨,得到钒渣粉末;s2、将钒渣粉末经过多次磁选(先弱磁干选后强磁干选)去除其中的单质铁得到单
质铁质量含量小于等于3%的钒渣;s3、将除铁后的钒渣粉末与碳酸钠按照比例混合,并放入回转窑中焙烧;s4、焙烧反应结束后,将焙烧熟料与水混合制浆,并将浆液倒入高效自吸式搅拌反应器中进行浸出反应,该自吸式搅拌反应器的结构在公开号cn207822903u实用新型专利中公开;s5、浸出反应结束后,对浆料进行固液分离得到钒酸钠溶液和提钒尾渣。
9.与现有技术相比,本发明的有益效果在于:本方法解决了物料烧结问题的同时,无需返料,仅一次焙烧,降低工艺能耗,缩短流程时间,单次处理量相比于现有方法提升了80%以上;并且提高了钒收率,钒的浸出率达到95%以上。
10.本发明的优选方案为:s1研磨得到的钒渣粉末粒度小于100μm,优选钒渣粉末d
90
在50~80μm。
11.s2中磁选级数为2~6级,优选为3~5级。经过磁选后的钒渣粉末中铁含量<3%,优选为<0.5%。
12.s3中除铁后钒渣粉末与碳酸钠的混合比例按钒渣中全钒与碳酸钠的摩尔比计,具体为1:0.6~0.75,优选为1:0.6~0.65。
13.s3中回转窑焙烧温度为700℃~900℃,优选为800℃~850℃;焙烧时间为2~5h,优选为3~4h。
14.s4中焙烧熟料与水的固液质量比为3~5:1,优选为4~5:1。
15.s4中浸出温度为70~90℃,优选为80~85℃;浸出时间为2~4h,优选为2~3h。
附图说明
16.图1为本发明实施例提供的钒渣钠化焙烧提钒的方法的工艺流程图。
具体实施方式
17.为充分了解本发明之目的、特征及功效,借由下述具体的实施方式,对本发明做详细说明,但本发明并不仅仅限于此。
18.本发明提供的一种钒渣钠化焙烧提钒的方法的工艺流程图如图1所示,钒渣中单质铁和钒均以质量百分比计。
19.实施例1本实施例提供了一种钒渣无返渣高转化率钠化焙烧提钒的方法,步骤如下:s1、将含单质铁10%、含钒6.8%的钒渣在多级立式磨机中进行充分研磨至钒渣粒径<100微米。
20.s2、将得到的钒渣经磁选分离金属铁得到含单质铁1%、含钒7%钒渣,磁选级数为3,先进行一次弱磁选,再进行两次强磁选。
21.s3、碳酸钠与分离金属铁后的钒渣按照钒渣中全钒与碳酸钠的摩尔比为1:0.6混合,并在750℃回转窑内焙烧1.5h。
22.s4、焙烧后的钒渣采用自吸桨加水,且钒渣与水固液比为3:1,在65℃下浸出2.5h。
23.s5、得到的浆料过滤,获得钒酸钠溶液和提钒尾渣,其中钒酸钠溶液中钒含量为35 g/l,提钒尾渣中的钒质量百分比为0.3%,钒的浸出率为95.7%。
24.实施例2本实施例提供了一种钒渣无返渣高转化率钠化焙烧提钒的方法,步骤如下:s1、将含单质铁13%、含钒7%的钒渣在多级立式磨中进行充分研磨,破碎至钒渣粒径小于80微米。
25.s2、将得到的钒渣经磁选分离金属铁,得到含单质铁0.8%、含钒7.5%钒渣,磁选级数为3,先进行一次弱磁选,再进行两次强磁选。
26.s3、碳酸钠与分离金属铁后的钒渣按照钒渣中全钒与碳酸钠的摩尔比为1:0.65,在回转窑内在800℃下进行焙烧2h。
27.s4、焙烧后的钒渣采用自吸桨加水,且钒渣与水液固比为4:1,在70℃下浸出3h。
28.s5、得到的浆料过滤,获得钒酸钠溶液和提钒尾渣,其中钒酸钠溶液中钒含量为38 g/l,提钒尾渣中的钒质量百分比为0.35%,钒的浸出率为95.3%。
29.实施例3本实施例提供了一种钒渣无返渣高转化率钠化焙烧提钒的方法,步骤如下:s1、将含单质铁15%、含钒6.7%的钒渣在多级立式磨中进行充分研磨,至钒渣粒径小于90微米。
30.s2、将得到的钒渣经磁选分离金属铁,得到含单质铁0.9%、含钒7.2%钒渣,磁选级数为4,先进行两次弱磁选,再进行两次强磁选。
31.s3、碳酸钠与分离金属铁后的钒渣按照钒渣中全钒与碳酸钠的摩尔比为1:0.65,在回转窑内在800℃下进行焙烧2.5h。
32.s4、焙烧后的钒渣采用自吸桨加水,且钒渣与水液固比为4:1,在70℃下浸出3h。
33.s5、得到的浆料过滤,获得钒酸钠溶液和提钒尾渣,其中钒酸钠溶液中钒含量为30 g/l,提钒尾渣中的钒为0.29%,钒的浸出率为95.97%。
34.实施例4本实施例提供了一种钒渣无返渣高转化率钠化焙烧提钒的方法,步骤如下:s1、将含单质铁8%、含钒7.9%的钒渣在多级立式磨中进行充分研磨,至钒渣粒径小于50微米。
35.s2、将得到的钒渣经磁选分离金属铁,得到含单质铁1.2%、含钒8%的钒渣,磁选级数为4,先进行两次弱磁选,再进行两次强磁选。
36.s3、碳酸钠与分离金属铁后的钒渣按照钒渣中全钒与碳酸钠的摩尔比为1:0.6,在850℃下进行焙烧3h。
37.s4、焙烧后的钒渣采用自吸桨加水,且钒渣与水液固比为5:1,在80℃下浸出3.5h。
38.s5、得到的浆料过滤,获得钒酸钠溶液和提钒尾渣,其中钒酸钠溶液中钒含量为37 g/l,提钒尾渣中的钒为0.3%,钒渣的浸出率为96.25%。
39.最后,需要注意的是:以上列举的仅是本发明的优选实施例,当然本领域的技术人员可以对本发明进行改动和变型,倘若这些修改和变型属于本发明权利要求及其等同技术的范围之内,均应认为是本发明的保护范围。