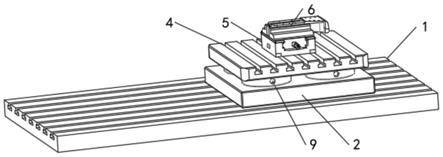
1.本发明属于机床技术领域,具体为一种机加自动换生产线及快速换产的方法。
背景技术:
2.机械加工自动化产线常用于大批量零件的生产,产线柔性较差,航天航空结构件产品具有种类多、批量小的特点,机加自动化生产线在此类产品的生产过程中存在换产频繁的问题,换产过程中主要工作集中在重新设定零件加工坐标系上,按照传统的方法,在换产时操作者需要在每个机床上对照工艺要求分别设定工件的加工坐标系,设定工件坐标系一方面增加了无效占机时间,影响机床利用率,另一方面过程容易出现人为坐标系设定错误,造成工件报废。
技术实现要素:
3.本发明的目的在于:本发明中很好的解决了机加自动化生产线在换产过程中坐标系的重新设定问题,该发明专利主要通过调整零件与机床坐标系原点的位置关系,从而保证同一批零件相对于机床坐标系原点的一致性,通过数控编程和雷尼绍测头实现零件坐标系的设定,该方法特别适用于种类多、批量小零件的生产,可以实现零件的快速换线,减少无效占机时间,降低人为对坐标错误。
4.本发明采用的技术方案如下:一种机加自动换生产线,包括,
5.工作台,用于对机床安装工件;
6.所述夹持组件包括零点定位基座、夹持孔、托盘、虎钳、工件、托盘定位孔、定位销、卡舌与虎钳定位孔,所述工作台的外壁顶部开设有滑槽,所述零点定位基座通过滑槽和滑块滑动嵌设于工作台的外壁顶部处,所述零点定位基座的外壁顶部边角处均向上凸起设置,所述夹持孔开设于零点定位基座的外壁顶部边角突出处,所述卡舌滑动嵌设于零点定位基座的外壁顶部边角突出处,所述定位销固定设置于托盘的外壁底部处,所述定位销与夹持孔相互匹配,所述定位销与卡舌相互卡接设置,所述托盘定位孔开设于托盘的外壁顶部处,所述虎钳定位孔开设于虎钳的外壁底部处,所述虎钳通过螺栓、托盘定位孔虎钳定位孔安装设置于托盘的外壁顶部处,所述工件通过滑槽滑动嵌设于虎钳的内壁处。
7.进一步的,所述托盘的外壁顶部开设有滑槽,所述工作板与托盘的滑槽呈九十度夹角设置。
8.一种机加自动换生产线的快速换产的方法,应用所述的一种机加自动换生产线中,包括以下步骤:
9.步骤一、首先对上述部件进行检查和维护。
10.步骤二、随后整机械坐标系原点位置,确保不同机床坐标系原点与机床工作台的偏差。
11.步骤三、零点定位基座通过螺栓与工作台连接,零点定位基座一次安装在工作台后一般不再移动,零点定位基座通过螺栓与工作台连接。
12.步骤四、托盘底面有四个定位销,定位销与夹持孔配合,实现连接和定位。
13.步骤五、虎钳与托盘通过托盘定位孔和虎钳定位孔实现连接定位。
14.步骤六、虎钳为自定心式,工件与虎钳之间其他方向自由度被限制,只存在左右方向的移动。
15.步骤七、工件6与机床机械坐标系的位置公差进行控制,工件加工前需测定其加工坐标系在机械坐标系下的数值,若测得坐标系值为(a,b,c),则通过数控程序即可实现坐标系的初步设定。
16.进一步的,根据步骤一中的操作步骤,所述不同机床坐标系原点与机床工作台的偏差,在x、y、z三个方向的距离偏差均小于0.5mm。
17.进一步的,根据步骤二中的操作步骤,所述零点定位基座一次安装在工作台后一般不再移动,与前端面距离,确保不同机床上基座与工作台端面两个方向安装距离的偏差均差小于1mm。
18.进一步的,根据步骤四中的操作步骤,所述定位销与夹持孔配合,其重复定位精度小于0.1mm,通过卡舌的伸缩实现夹紧和放松。
19.进一步的,根据步骤六中的操作步骤,所述需要限制工件与虎钳口之间的距离,保证工件每次的装夹误差小于1mm。
20.进一步的,根据步骤五中的操作步骤,所述虎钳与托盘通过托盘定位孔和虎钳定位孔实现连接定位,其重复定位精度小于0.1mm。
21.进一步的,根据步骤七中的操作步骤,所述工件6与机床机械坐标系的位置公差进行控制,可以控制在
±
2.45mm的空间范围内。
22.进一步的,根据步骤七中的操作步骤,所述零件与机床机械坐标系的位置公差小于雷尼绍测头测量标准容差值
±
10mm。
23.综上所述,由于采用了上述技术方案,本发明的有益效果是:
24.本发明中,很好的解决了机加自动化生产线在换产过程中坐标系的重新设定问题,该发明专利主要通过调整零件与机床坐标系原点的位置关系,从而保证同一批零件相对于机床坐标系原点的一致性,通过数控编程和雷尼绍测头实现零件坐标系的设定,该方法特别适用于种类多、批量小零件的生产,可以实现零件的快速换线,减少无效占机时间,降低人为对坐标错误。
附图说明
25.图1为本发明的立体图;
26.图2为本发明的主视图;
27.图3为本发明零点定位基座的立体图;
28.图4为本发明托盘的立体图;
29.图5为本发明定位销的立体图。
30.图中标记:1、工作台;2、零点定位基座;3、夹持孔;4、托盘;5、虎钳;6、工件;7、托盘定位孔;8、定位销;9、卡舌;10、虎钳定位孔。
具体实施方式
31.为了使本发明的目的、技术方案及优点更加清楚明白,以下结合附图及实施例,对本发明进行进一步详细说明。应当理解,此处所描述的具体实施例仅用以解释本发明,并不用于限定本发明。
32.请参阅图1-5,一种机加自动换生产线,包括,
33.工作台1,用于对机床安装工件6。
34.夹持组件包括零点定位基座2、夹持孔3、托盘4、虎钳5、工件6、托盘定位孔7、定位销8、卡舌9与虎钳定位孔10,工作台1的外壁顶部开设有滑槽,零点定位基座2通过滑槽和滑块滑动嵌设于工作台1的外壁顶部处,零点定位基座2的外壁顶部边角处均向上凸起设置,夹持孔3开设于零点定位基座2的外壁顶部边角突出处,卡舌9滑动嵌设于零点定位基座2的外壁顶部边角突出处,定位销8固定设置于托盘4的外壁底部处,定位销8与夹持孔3相互匹配,定位销8与卡舌9相互卡接设置,托盘定位孔7开设于托盘4的外壁顶部处,虎钳定位孔10开设于虎钳5的外壁底部处,虎钳5通过螺栓、托盘定位孔7虎钳定位孔10安装设置于托盘4的外壁顶部处,工件6通过滑槽滑动嵌设于虎钳5的内壁处。
35.本实施例:利用夹持组件,可以实现对工件6进行稳定的夹持作用,其中卡舌9方便对定位销8进行稳定的固定,避免产生托盘4的滑动,其中利用虎钳,可以实现稳定的工件夹持。
36.具体的,托盘4的外壁顶部开设有滑槽,工作台1与托盘4的滑槽呈九十度夹角设置。
37.本实施例:其中使用托盘4,可以实现稳定的虎钳5限制和安装。
38.一种机加自动换生产线的快速换产的方法,应用所述的一种机加自动换生产线中,包括以下步骤:
39.步骤一、首先对上述部件进行检查和维护,步骤二、随后整机械坐标系原点位置,确保不同机床坐标系原点与机床工作台1的偏差,步骤三、零点定位基座2通过螺栓与工作台1连接,零点定位基座2一次安装在工作台1后一般不再移动,零点定位基座2通过螺栓与工作台1连接,步骤四、托盘4底面有四个定位销8,定位销8与夹持孔3配合,实现连接和定位,步骤五、虎钳5与托盘4通过托盘定位孔7和虎钳定位孔10实现连接定位,步骤六、虎钳5为自定心式,工件6与虎钳5之间其他方向自由度被限制,只存在左右方向的移动,步骤七、工件6与机床机械坐标系的位置公差进行控制,工件6加工前需测定其加工坐标系在机械坐标系下的数值,若测得坐标系值为a,b,c,则通过数控程序即可实现坐标系的初步设定。
40.本实施例:机床工作台1和机床机械坐标系的位置关系,分别为坐标原点到工作台1右端距离、坐标原点到工作台1前端距离、坐标原点到工作台1上端距离,每台机床由于制造装配误差,机械坐标系原点的位置不一致,坐标系原点与机床工作台1在x、y、z三个方向的距离都有不同程度的偏差,为消除机床制造误差,需调整机械坐标系原点位置,确保不同机床坐标系原点与机床工作台1在x、y、z三个方向的距离偏差均小于0.5mm,零点定位基座2通过螺栓与工作台1连接,零点定位基座2一次安装在工作台1后一般不再移动,安装基座时需测量并控制其与工作台1右端面距离、与前端面距离6,确保不同机床上基座与工作台1端面两个方向安装距离的偏差均差小于1mm,托盘4底面有四个定位销8,定位销8与零点定位基座夹持孔3配合,实现连接和定位,其重复定位精度小于0.1mm,通过卡舌9的伸缩实现夹
紧和放松,虎钳5与托盘4通过托盘定位孔7和虎钳定位孔10实现连接定位,其重复定位精度小于0.1mm,自定心虎钳5,零件与虎钳5之间其他方向自由度被限制,只存在左右方向的移动,需要限制零件与虎钳5口之间的距离,保证零件每次的装夹误差小于1mm,零件与机床机械坐标系的位置公差可以控制在
±
2.45mm的空间范围内,其小于雷尼绍测头测量标准容差值
±
10mm,零件加工前需测定其加工坐标系在机械坐标系下的数值,若测得坐标系值为(a,b,c),则通过数控程序即可实现坐标系的初步设定为:
41.#5221=a
ꢀꢀꢀꢀꢀꢀꢀꢀꢀꢀꢀꢀꢀꢀꢀꢀꢀꢀꢀꢀꢀꢀꢀꢀ
(设定初始坐标系x值)
42.#5222=b
ꢀꢀꢀꢀꢀꢀꢀꢀꢀꢀꢀꢀꢀꢀꢀꢀꢀꢀꢀꢀꢀꢀꢀꢀ
(设定初始坐标系y值)
43.#5223=c
ꢀꢀꢀꢀꢀꢀꢀꢀꢀꢀꢀꢀꢀꢀꢀꢀꢀꢀꢀꢀꢀꢀꢀꢀ
(设定初始坐标系z值)
44.加工前开启雷尼绍测头,对初始加工坐标系进行修正,修正后的坐标系为最终加工坐标系。程序内容如下:
[0045][0046][0047]
以上仅为本发明的较佳实施例而已,并不用以限制本发明,凡在本发明的精神和原则之内所作的任何修改、等同替换和改进等,均应包含在本发明的保护范围之内。