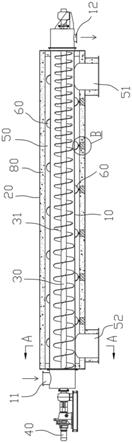
1.本实用新型涉及炭化炉技术领域,尤其是一种生物质卧式旋芯炭化炉。
背景技术:
2.目前市场上成熟应用的生物质炭化炉,主要为立式固定床炭化炉和卧式回转窑炭化炉,二者都是利用欠氧燃烧释放热能对生物质原料进行热解,存在固定碳烧损量大,产炭率降低,炭品质量不能保证等问题;同时,伴生燃气为欠氧燃烧的产物,其中含有空气带入的大量氮气,因此产气量大,温度和热值较低,且析出焦油,利用价值和工艺可靠性都有所降低,该类焦油属于危废,处理成本较高,威胁生态环境和人身健康安全;另外,这两种炭化炉还存在不同程度的单机产能低、生物质原料综合利用效率低、电耗高等缺陷。这些问题的存在严重制约了生物质原料炭化产业的进一步发展。
技术实现要素:
3.本技术人针对上述现有生产技术中的缺点,提供一种生物质卧式旋芯炭化炉,原料成炭率高、提高生产效率、保证炭品质量且使用寿命较长。
4.本实用新型所采用的技术方案如下:一种生物质卧式旋芯炭化炉,包括内筒以及套设在内筒外部的外筒,内筒内部设有旋芯推绞轴,旋芯推绞轴的外周壁上带有螺旋叶片,旋芯推绞轴的前端悬伸在内筒的外部并通过电机带动实现旋芯推绞轴的转动,内筒的前端和后端分别悬伸在外筒的外部,内筒的前端设置原料入口,内筒的后端设置第一出口,内筒的外筒壁和外筒的前端端口固定密封连接,内筒的外筒壁和外筒的后端端口通过密封圈实现动密封,内筒和外筒之间围合形成加热腔室,外筒的后端开设接口作为加热腔室的加热介质入口,外筒的前端开设接口作为加热腔室的加热介质出口,螺旋叶片上垂直布置多个搅拌柱,内筒的外周壁上设有螺旋导流片,螺旋导流片的底端设有多个滚动支撑单元,螺旋导流片的底端通过滚动支撑单元和外筒的内壁构成筒长方向的可滚动式支撑配合。
5.作为上述技术方案的进一步改进:
6.所述滚动支撑单元包括限位块和滚轴,限位块的下表面开设限位槽,滚轴可滚动式限位在限位槽中,滚轴可贴着外筒的内壁实现筒长方向的滚动。
7.所述外筒的内壁贴附绝热层,和每个滚动支撑单元相对的外筒的内壁上固定高强绝热块,高强绝热块的内表面贴附高温耐磨层,高强绝热块和高温耐磨层镶嵌在绝热层中,滚轴滚动时沿着高温耐磨层滚动。
8.所述内筒自前端向后端的横截面面积逐渐减小。
9.所述搅拌柱为条柱状,搅拌柱沿着螺旋叶片的螺旋边缘均匀间隔布置。
10.所述内筒、外筒的横截面均为腰型孔型且腰型孔的两条相平行的直边在上下方向上相互平行。
11.所述旋芯推绞轴为两个,两个旋芯推绞轴的螺旋叶片的旋向相同,螺旋叶片的螺距自前端向后端逐渐减小,旋芯推绞轴与内筒偏心设置,旋芯推绞轴的中心线位于内筒的
中心线的下方。
12.所述外筒由上半壳体和下半壳体通过法兰连接方式围合而成,上半壳体和下半壳体之间通过密封垫实现密封连接,外筒固定在支撑框架中,支撑框架的横截面为方形,支撑框架由上半框架和下半框架通过螺栓连接方式连接成一体,上半壳体焊接在上半框架中,下半壳体焊接在下半框架中,上半壳体、下半壳体之间的法兰连接和上半框架、下半框架之间的螺栓连接共用同一个螺栓。
13.本实用新型的有益效果如下:本技术加热介质不与生物质原料直接接触,通过间接的方式对生物质原料进行加热,即加热介质不会对生物质原料的反应提供氧气,不发生氧化反应,生物质原料中固定碳不会发生烧损,生成炭品中c元素含量高,原料成炭率高;内筒的外周壁上设有螺旋导流片,螺旋导流片对加热介质进行导流,使得加热均匀,使得生物质原料的反应时间充分,可实现生物质原料深度均匀炭化,炭品孔隙率高及c元素含量高,质量有可靠保证;螺旋叶片上垂直布置多个搅拌柱,在推进过程中对生物质原料进行搅拌,可以提高内筒的导热性和内筒内温度场的均匀性,促进生物质原料炭化反应过程的均衡性和快速性;外筒采用内侧绝热层绝热,运行时外筒外壁接近常温,轴向膨胀位移较小,内筒受加热介质包覆,温度较高,内筒的轴向膨胀位移较大,内筒膨胀时发生轴向移动,内筒移动时依靠滚轴在外筒内侧的高温耐磨层上滚动支撑,有效适应内筒的膨胀,不会因膨胀被限制而造成内筒的损坏,使得整个炭化炉使用寿命较长。
附图说明
14.图1是本实用新型的剖面结构示意图(支撑框架未示出)。
15.图2是图1的a
‑
a方向剖视图。
16.图3是本实用新型旋芯推绞轴的部分结构图。
17.图4是图1中b部分的放大图。
18.其中:10、内筒;11、原料入口;12、第一出口;20、外筒;21、上半壳体;22、下半壳体;30、旋芯推绞轴;31、螺旋叶片;32、搅拌柱;40、电机;50、加热腔室;51、加热介质入口;52、加热介质出口;60、螺旋导流片;71、限位块;72、滚轴;80、绝热层;91、高强绝热块;92、高温耐磨层;100、支撑框架;101、上半框架;102、下半框架;110、螺栓。
具体实施方式
19.下面结合附图,说明本实用新型的具体实施方式。
20.如图1
‑
4所示,本实施例的生物质卧式旋芯炭化炉,包括内筒10以及套设在内筒10外部的外筒20,内筒10内部设有旋芯推绞轴30,旋芯推绞轴30的外周壁上带有螺旋叶片31,旋芯推绞轴30的前端悬伸在内筒10的外部并通过电机40带动实现旋芯推绞轴30的转动,内筒10的前端和后端分别悬伸在外筒20的外部,内筒10的前端设置原料入口11,内筒10的后端设置第一出口12,内筒10的外筒壁和外筒20的前端端口固定密封连接,内筒10的外筒壁和外筒20的后端端口通过密封圈实现动密封,内筒10和外筒20之间围合形成加热腔室50,外筒20的后端开设接口作为加热腔室50的加热介质入口51,外筒20的前端开设接口作为加热腔室50的加热介质出口52,螺旋叶片31上垂直布置多个搅拌柱32,内筒10的外周壁上设有螺旋导流片60,螺旋导流片60的底端设有多个滚动支撑单元,螺旋导流片60的底端通过
滚动支撑单元和外筒20的内壁构成筒长方向的可滚动式支撑配合。其中密封圈采用柔性石墨密封圈。
21.滚动支撑单元包括限位块71和滚轴72,限位块71的下表面开设限位槽,滚轴72可滚动式限位在限位槽中,滚轴72可贴着外筒20的内壁实现筒长方向的滚动。
22.外筒20的内壁贴附绝热层80,和每个滚动支撑单元相对的外筒20的内壁上固定高强绝热块91,高强绝热块91的内表面贴附高温耐磨层92,高强绝热块91和高温耐磨层92镶嵌在绝热层80中,滚轴72滚动时沿着高温耐磨层92滚动。绝热层80、高强绝热块91、高温耐磨层92采用现有的一些材料即可。比如绝热层80采用硅酸铝纤维毡加耐火泥抹面等即可,高强绝热块91采用具有一定强度的绝热材料,高强绝热块91既要起到绝热效果,又要具有一定强度来支撑滚轴72。高温耐磨层92采用耐高温、耐磨的材料制成即可。高温耐磨层92可以减小滚动摩擦阻力系数。
23.内筒10自前端向后端的横截面面积逐渐减小。
24.搅拌柱32为条柱状,搅拌柱32沿着螺旋叶片31的螺旋边缘均匀间隔布置。为了加强生物质原料在内筒10内的扰动,提高干馏热解反应速度,防止原料沉积于内筒10下部,在旋芯推绞轴30的螺旋叶片31上沿周向均匀焊接搅拌柱32,在旋芯推绞轴30对原料的旋转推进过程中,可以勾起下部浓相区原料,在炭化过程中对原料不停搅拌,实现均化温度场、物料场的目的。
25.所述内筒10、外筒20的横截面均为腰型孔型且腰型孔的两条相平行的直边在上下方向上相互平行。这样内筒10和外筒20的下筒壁均为平板状,方便滚动支撑单元的安装,方便滚轴72的滚动。
26.所述旋芯推绞轴30为两个,两个旋芯推绞轴30的螺旋叶片31的旋向相同,螺旋叶片31的螺距自前端向后端逐渐减小,旋芯推绞轴30与内筒10偏心设置,旋芯推绞轴30的中心线位于内筒10的中心线的下方。为了提高产能,本技术旋芯推绞轴30可以设置两个或以上,具体个数根据实际需要而定。本技术优选采用两个旋芯推绞轴30,可以使单机处理能力翻倍。旋芯推绞轴30与内筒10偏心设置,利于推动和搅动下部浓相区原料,为上部气相区留出空间,并提高内筒10的筒壁辐射传热能力。螺旋叶片31的螺距随着生物质原料体积的变化从前到后逐渐由大变小,可以提高炉内后部生物质原料充满度和炉内炭化时间,保证炭化效果。
27.所述外筒20由上半壳体21和下半壳体22通过法兰连接方式围合而成,上半壳体21和下半壳体22之间通过密封垫实现密封连接,外筒20固定在支撑框架100中,支撑框架100的横截面为方形,支撑框架100由上半框架101和下半框架102通过螺栓连接方式连接成一体,上半壳体21焊接在上半框架101中,下半壳体22焊接在下半框架102中,上半壳体21、下半壳体22之间的法兰连接和上半框架101、下半框架102之间的螺栓连接共用同一个螺栓110。外筒20采用可分解式筒体,支撑框架100采用可分解框架,方便炭化炉的安装以及内部的检修。需要说明的是,为了整个结构的清楚表达,图1中未画出支撑框架100的结构,支撑框架100的结构在图2中展示。
28.本技术的工作过程为:
29.(1)炭化生物质原料从原料入口11进入内筒10内部,在电机40驱动下带动旋芯推绞轴30旋转,推动生物质原料在内筒10内从前往后运动;
30.(2)加热介质(采用燃气燃烧释放的高温烟气)从加热介质入口51进入内筒10和外筒20之间的加热腔室50,在内筒10外壁螺旋导流片60的导流作用下,与内筒10内生物质原料呈逆流方式,从后向前旋转绕流内筒10,加热介质对内筒10内生物质原料加热,降温后的加热介质从前部的加热介质出口52排出;
31.(3)内筒10内生物质原料在高温加热介质的加热作用下,在从前往后移动过程中逐步完成干馏热解、减容析气、深度炭化过程,最后在旋芯推绞轴30推动下,生成的炭和燃气从第一出口12排出。
32.与现有技术相比,本实用新型具有以下优点:
33.1、本技术中炭化炉为卧置固定式,加热介质布置在内筒10外部,加热介质不与生物质原料直接接触,通过间接的方式对生物质原料进行加热,即加热介质不会对生物质原料的反应提供氧气,不发生氧化反应,生物质原料中固定碳不会发生烧损,生成炭品中c元素含量高,原料成炭率高;
34.2、内筒10的外周壁上设有螺旋导流片60,螺旋导流片60对加热介质进行导流,使得加热均匀,使得生物质原料的反应时间充分,可实现生物质原料深度均匀炭化,炭品孔隙率高及c元素含量高,质量有可靠保证;
35.3、可以通过调节旋芯推绞轴30的旋转速度和加热介质的温度,对炭化过程进行有效控制和调节,对生物质原料适应性大大提高;
36.4、螺旋叶片31上垂直布置多个搅拌柱32,在推进过程中对生物质原料进行搅拌,可以提高内筒10的导热性和内筒10内温度场的均匀性,促进生物质原料炭化反应过程的均衡性和快速性;
37.5、内筒10自前端向后端的横截面面积逐渐减小,即内筒采用前端(生物质原料入口端)大、后端(炭、燃气出口端)小的锥体变截面结构,外筒20采用常规的等截面结构,使得内筒10和外筒20之间形成的加热腔室50按照加热介质流动方向形成先大后小的流通截面,适应加热介质随温度逐步降低体积逐步减小的变化,利于实现介质匀速流动,保证传热效果,合理控制流动阻力;
38.6、炭化过程中,生物质原料行进方向与加热介质呈逆向流动状态,增加了传热温压,提高了加热介质利用效率和炭化室内温度水平,利于提高炭化反应速度和炭品质量;
39.7、伴生燃气为生物质原料干馏热解气,没有空气混入和燃烧发生,燃气热值高,量少质优,用途广,处理成本低,利用效率高;
40.8、热解过程没有空气参与,完全避免爆燃、爆炸可能性,另外,燃气温度高,其输送过程没有焦油析出,不会发生管道堵塞,系统安全性有可靠保证;
41.9、炭化过程只产生生物炭和燃气,燃气中也不会发生危废焦油析出,系统没有固废、液废和气废排放,生产工艺清洁、环保。
42.10、外筒20采用内侧绝热层80绝热,运行时外筒20外壁接近常温,轴向膨胀位移较小,内筒10受加热介质包覆,温度较高,内筒10的轴向膨胀位移较大,内筒10膨胀时发生轴向移动,内筒10移动时依靠滚轴72在外筒20内侧的高温耐磨层92上滚动支撑,有效适应内筒10的膨胀,不会因膨胀被限制而造成内筒10的损坏,使得整个炭化炉使用寿命较长。
43.本实用新型的重载支承结构工作过程为:
44.内筒10内原料和变截面内筒10重量通过固定在内筒10外壁的滚动支撑单元传递
到等截面外筒20上,再传递到与外筒20焊接一体的支撑框架100上。旋芯推绞轴30及其驱动电机40可以采用安装支架也传到支撑框架100上,使卧式旋芯炭化炉固定为一整体。
45.以上描述是对本实用新型的解释,不是对实用新型的限定,本实用新型所限定的范围参见权利要求,在本实用新型的保护范围之内,可以作任何形式的修改。