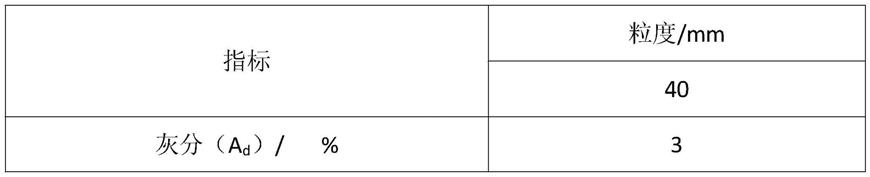
1.本发明属于煅烧石灰的环保可再生能源利用领域,特别涉及一种双高炭的制备方法。
背景技术:
2.生物炭又称为机制炭、再生炭、人造炭、无烟精洗炭。它是以木质或植物纤维碎料经挤压加工,经高温炭化,加工成炭质棒状物。根据形状来分又可分为三角形、四边形、五边形及六边形形状的空心生物炭;根据其炭化温度又可分为高温炭、中温炭和低温炭。其区别为:高温炭是采用高温炉(炭化温度800℃以上)快速烧制而成,其质地硬实,密度大,能沉于水。其含炭量大,挥发分和水分小,燃烧时无火焰,适合一切使用炭的场合;中温炭采用中温(550℃~800℃)烧制而成,机械强度较大,含碳量高于低温炭,密度较大;低温炭是在低温(350℃~550℃)烧制而成,其质地疏松、多孔,机械强度低,含碳量低,灰分大。
3.生物炭与其他普通木炭的区别在于:
4.①
环保:不砍伐树林,利用秸秆、竹木制品废料及菌渣等为原料,变废为宝,可持续再生,循环利用。
5.②
热值高:固定炭含量大于80%,热值7000~8000kcal/kg。
6.③
清洁卫生:无烟,无灰头,燃烧无火苗,燃烧时残炭自然落下,灰分在2%~6%左右,残灰少,易燃。
7.④
不含有害化学物质:无异味,无毒、无污染,燃烧时间长,挥发分小于15%
8.⑤
水分低:水分小于5%,形状规则,结构合理,使用方便,有较统一的尺寸和规格。
9.生产生物炭的主要原料很多,主要为秸秆、树皮、蔗渣等农作废弃物。秸秆是成熟农作物茎叶(穗)部分的总称。通常指小麦、水稻、玉米、薯类、油菜、棉花、甘蔗髓和其它农作物(通常为粗粮)在收获籽实后的剩余部分。秸秆除少量用于垫圈、喂养牲畜,部分用于堆沤肥外,大部分都作燃料烧掉了。焚烧秸秆形成的烟雾,会造成空气能见度下降,可见范围降低,直接影响民航、铁路、高速公路的正常运营,容易引发交通事故,影响人身安全和引起严重的污染问题。秸秆等农作废弃物的焚烧,极易引燃周围的易燃物,导致“火烧连营”,一旦引发麦田大火,往往很难控制,造成经济损失。尤其是在山林附近,后果更是不堪设想;秸秆等农作废弃物的焚烧也入地三分,地表中的微生物被烧死,腐殖质、有机质被矿化,田间焚烧秸秆破坏了这套生物系统的平衡,改变了土壤的物理性状,加重了土壤板结,破坏了地力,加剧了干旱,农作物的生长因而受到影响;焚烧秸秆等农作废弃物产生大量有毒有害物质,威胁人的身心健康。因此,加强秸秆等农作物的资源化利用显得尤为重要。
10.石灰(也称为氧化钙)是在高温下煅烧石灰石、白垩或其他碳酸盐原料所到的产物。目前煅烧石灰的主要燃料有:焦炭、无烟煤、烟煤、褐煤、泥煤、柴草、重油、各种煤气等,其中,固体燃料中最好的是焦炭。焦炭不仅是发热量高达6000~7000大卡/公斤,固定碳高达90%以上,机械强度高,不易被石灰石块压碎,而且焦炭在结焦时,挥发物质几乎全部溢出(小于2%),减少窑内结瘤现象和提高产品质量。但是由于焦炭价格昂贵,通常较少在煅
烧石灰中使用。
11.无烟煤是目前使用较为普遍的煅烧石灰的燃料。无烟煤具有固定碳含量高达80%以上、发热量高达5700~6500大卡/公斤、挥发分含量比其他煤种低10%以上、结焦相对较少等特点,在煅烧石灰中得到广泛使用。应当注意的是,由于产地不同,上述的质量指标是有波动的。在煅烧石灰工艺中,由于加入不同粒径的煤块,容易导致煤块不能很好的完全燃烧。煤块不能完全燃烧,不仅会生成未烧透的炭粒,最终影响石灰质量;而且燃烧不完全,也会容易使石灰石未烧透,出现轻烧的现象,会影响石灰的质量且增大能耗。若是以煤粉方式喷入立窑中燃烧,又容易堵塞喷嘴以及影响底部螺锥正常转动。
12.采用其他常用的燃料如重油、天然气和人造煤气等燃料受制于运输距离和成本等原因,使用较少,且对于石灰窑的结构有着特殊要求。
13.如果将生物炭直接替代煤炭在石灰窑中燃烧,从发热量来说不存在技术上的难题。因为生物炭的热值在6200~8000大卡/公斤以上,含碳量大于90%,而无烟煤或标煤的热值在6000~6500大卡/公斤,含碳量约为90%。生物炭和各项性能指标均与无烟煤相当。但由于生物炭易碎,机械强度不高,在与石灰石混合加入立窑煅烧的过程中,极易出现被挤压破碎成粉,极易造成堵塞出料口通风系统或底部螺锥等问题,生物炭在煅烧石灰中的应用也存在一定的技术困难。
14.如何将可再生能源用于煅烧石灰窑工艺中,成为摆在石灰行业面前的挑战之一。如何将煅烧石灰工艺使用可再生能源(生物炭)替代化石能源,是石灰行业今后健康发展的过程中,必须面临的紧迫挑战之一。
技术实现要素:
15.本发明要解决的技术问题是提供一种双高炭的制备方法,使制备出的双高炭适用于煅烧石灰石上。
16.本发明解决上述技术问题的技术方案是:一种双高炭的制备方法,包括以下步骤:
17.(1)粉碎:将秸秆、木渣、蔗髓的一种或多种混合物进行切割,得到原料颗粒;
18.(2)加入添加剂:称取添加剂,并加入到原料颗粒中得到混合料;
19.(3)搅拌:混合料放入超重力搅拌机,搅拌均匀;
20.(4)定型:将步骤(3)的材料送入到双级螺杆制型机中进行压制;
21.(5)炭化成型:将步骤(4)的材料送入到炭化炉中炭化成型,炭化成型完成后即得本发明的双高炭。
22.所述的粉碎是将秸秆用粉碎机粉碎为长度1mm以下的渣状物。
23.所述的秸秆占混合料的比例为80~90%。
24.所述的氧化钙是150~200目,含量为85%~98%的氧化钙,加入的氧化钙的量占混合料的比例的5~10%。
25.所述的硫酸钙占混合料的比例的3~5%。
26.所述的蓬松剂是尿素、碳酸氢氨或尿素与碳酸氢氨的组合物,所述的结构改造剂是由石灰、糊精、水玻璃、膨润土的一种或多种组合物。所述的蓬松剂与结构改造剂占混合料的比例的≤5%。
27.所述的搅拌是将粉碎后的秸秆与添加剂在重力搅拌机中搅拌成细碎粉末,搅拌速
度45r/min。
28.所述的炭化成型是在压力0.8mpa,烧制温度850℃的条件下快速炭化成型。
29.使用到的设备包括粉碎机、超重力搅拌机、双级螺杆制型机和炭化炉。粉碎机的出料口连接超重力搅拌机,超重力搅拌机连接双级螺杆挤压机的入料口,双级螺杆挤压机的出料口连接炭化炉的入口。所述连接通过传送带连接。
30.所述超重力搅拌机为双轴搅拌机。
31.本发明的有益效果是:
32.(1)改善煅烧石灰对于化石能源的依赖,有效解决窑炉燃料燃烧不充分等问题。
33.(2)实现农业废弃物与各类含碳有机物等高效可再生循环利用。
34.(3)提高能源利用率和石灰的质量,有利于二氧化碳后续工艺的回收利用。
35.(4)生产过程中,可大幅度减少各类污染物的排放,做到经济、安全、高效、节能、环保。
附图说明
36.图1是本发明装置的工艺流程图。
具体实施方式
37.下面结合附图和实施例对本发明作进一步地说明。此处所描述的具体实施案例仅仅用于解释本发明,并不用于限定本发明。
38.一种双高炭的制备方法,将秸秆粉碎后加入添加剂,经干燥、定型及炭化成型制得。使用到的设备包括粉碎机、超重力搅拌机、双级螺杆制型机和炭化炉。粉碎机的出料口连接超重力搅拌机,超重力搅拌机连接双级螺杆挤压机的入料口,双级螺杆挤压机的出料口连接炭化炉的入口。所述连接通过传送带连接。
39.秸秆包括蔗髓、各类农作物秸秆、木渣、树皮以及其他植物纤维原料。重力搅拌机为双轴搅拌机,电机功率为7.5kw,叶片直径为400mm,叶片转速为47.6r/min,最大处理量为1000kg/h。双级螺杆制型机为jzk系列双级真空挤出机,其基本结构包括机架、加料系统、挤出系统、传动系统、加热冷却系统及电气控制系统等部分。
40.炭化炉连续式双筒结构炭化炉。炭化炉所需热量由水煤气循环提供,冷却装置采用多级水冷,经管道将热水输送至炭化炉前端,利用余热使得原料初步预热干燥,实现了资源的循环利用,节约了能耗。
41.实施例1:
42.本发明所述的一种双高炭的制备方法的一个实例,包括如下步骤:
43.(1)粉碎:将木渣送入到粉碎机中进行搅拌切割10min,搅拌转速为50r/min,切割后得到1mm的碎木颗粒;
44.(2)加入添加剂:称取以下重量百分比例原料:将5%的200目质量比为85%的氧化钙、3%的硫酸钙、1.5%的尿素、0.5%的糊精,加入到90%碎木颗粒中得到混合料;
45.(3)搅拌:将步骤(2)混合料放入超重力搅拌机,搅拌反应50min,共混转速为600r/min,随后取出,表面含水率为1%,备用;
46.(4)定型:将步骤(3)的材料送入到双级螺杆制型机中进行压制。
47.(5)炭化成型:将步骤(4)的材料送入到炭化炉中炭化。炭化温度850℃,炭化时间3h。炭化完成后即得本发明双高炭。
48.本实施例的反应压力为0.8mpa。本实施例的连续式双筒结构炭化炉,筒体尺寸1000mm,转动电机功率55kw。
49.本实施例的成型机中双级螺杆制型机机功率为7.5kw,叶片直径为400mm,叶片转速为50r/min。
50.实施例1的技术指标如下所示
[0051][0052][0053]
实施例2:
[0054]
本实施例为本发明所述的双高炭的制备方法的另一个实例,包括如下步骤:
[0055]
(1)粉碎:将蔗髓送入到粉碎机中进行搅拌切割10min,搅拌转速为45r/min,切割后得到1mm蔗髓颗粒;
[0056]
(2)加入添加剂:称取以下重量百分比例原料:将7%的150目质量比为95%的氧化钙、4%的硫酸钙、2%的碳酸氢铵、1%的水玻璃加入到86%的蔗髓颗粒中得到混合料;
[0057]
(3)搅拌:将步骤(2)中混合料放入超重力搅拌机,搅拌反应45min,共混转速为550r/min,随后取出,表面含水率为1%,备用;
[0058]
(4)定型:将步骤(3)的材料送入到双级螺杆制型机中进行压制。
[0059]
(5)炭化成型:将步骤(4)的材料送入到炭化炉中炭化。炭化温度850℃,炭化时间3h。炭化完成后即得本发明双高炭。
[0060]
本实施例的反应压力为0.8mpa。本实施例的连续式双筒结构炭化炉。筒体尺寸1000mm,转动电机功率55kw。
[0061]
本实施例的成型机中双级螺杆制型机机功率为7.5kw,叶片直径为400mm,叶片转速为47.6r/min。
[0062]
实施例2的技术指标如下所示
[0063][0064]
实施例3:
[0065]
本实施例的一种用于生产双高炭制造方法,包括以下步骤:
[0066]
(1)粉碎:将蔗髓送入到粉碎机中进行搅拌切割10min,搅拌转速为40r/min,切割后得到1mm的蔗髓颗粒;
[0067]
(2)加入添加剂:称取以下重量百分比例原料:将10%的150目质量比为98%的氧化钙、5%的硫酸钙、3.5%的碳酸氢氨、1.5%的膨润土加入到80%的蔗髓颗粒中得到混合料;
[0068]
(3)搅拌:将步骤(2)中混合料放入超重力搅拌机,搅拌反应40min,共混转速为500r/min,随后取出,表面含水率为1%,备用;
[0069]
(4)定型:将步骤(3)的材料送入到双级螺杆制型机中进行压制。
[0070]
(5)炭化成型:将步骤(4)的材料送入到炭化炉中炭化。炭化温度850℃,炭化时间3h。炭化完成后即得本发明双高炭。
[0071]
本实施例的反应压力为0.8mpa。本实施例的连续式双筒结构炭化炉。筒体尺寸1000mm,转动电机功率55kw。
[0072]
本实施例的成型机中双级螺杆制型机机功率为7.5kw,叶片直径为400mm,叶片转速为45r/min。
[0073]
实施例3的技术指标如下所示
[0074][0075]