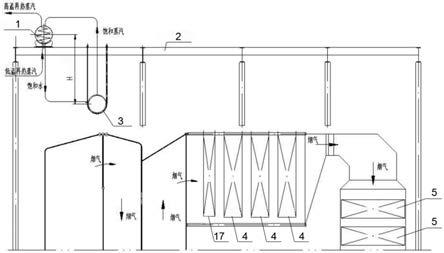
1.本实用新型属于垃圾焚烧的技术领域,具体而言,涉及一种高参数垃圾焚烧余热锅炉的再热蒸汽系统及汽汽换热器。
背景技术:
2.随着经济和社会生活的发展,城市数量和城市规模都在不断增加,伴生而来的是城市生活垃圾产量的迅速增加,垃圾的成分也发生了较大的变化,传统的堆肥和卫生填埋方式由于占地面积大、渗滤液处理等问题的存在,已经不能适应目前生活垃圾无害化处理的要求,而垃圾焚烧具有的处理效率高、占地面积小和减量化程度高的优点,加上焚烧产生的热能利用、灰渣后端资源化利用的优点和地价飞涨因素,使得垃圾焚烧发电越来越得到各级地方政府的青睐。
3.炉排焚烧炉作为垃圾焚烧发电的主要炉型之一,目前在国内外市场的应用较为普遍,但由于其焚烧产物中的腐蚀性气体的存在,使得其锅炉参数普遍较低,一般控制锅炉出口的蒸汽温度不超过450℃,以降低高温腐蚀的风险,但锅炉出口蒸汽的低参数也使得垃圾发电厂的效率降低,影响电厂的经济效益。
4.发电收益是国内外垃圾焚烧电厂盈利的主要组成部分,因此在不增加腐蚀风险的前提下,通过系统的优化改进提高发电效率,是目前垃圾焚烧电厂的主流发展方向。设置再热蒸汽系统,使汽轮机效率得到有效提升是其中的一个方面,次高压参数设置再热蒸汽系统,机组发电效率提高~2.6%。但如果按照常规的再热蒸汽系统设计,再热器受热面布置在尾部烟道内,一方面再热器受热面同样存在高温腐蚀的风险,另一方面,再热器、过热器高温级受热面同样需要控制入口烟温水平不超过600℃,受热面传热温压小,为达到要求的出口蒸汽温度需要更多的受热面积,这也意味着更大区域的高温腐蚀风险,高温级受热面可利用的烟温空间有限,锅炉运行的灵活性降低。
5.目前国内外已有的垃圾焚烧炉排炉余热锅炉,为增加电厂收益,在提升蒸汽压力的同时,倾向于设置再热器系统,以提高发电效率。但增设的再热器受热面布置在锅炉烟道中,一方面与锅炉原有的过热器争夺有限的高温级受热面换热所需烟温范围资源,使高温级受热面布置困难,影响锅炉运行的灵活性;另一方面,增加的再热器受热面同样存在高温腐蚀的风险。
技术实现要素:
6.鉴于此,为了解决现有技术存在的上述问题,本实用新型的目的在于提供一种高参数垃圾焚烧余热锅炉的再热蒸汽系统以达到通过合理设计再热蒸汽受热面布置位置,避免再热器受热面的高温腐蚀问题,实现系统运行自动调节,无需设置其他辅助系统,运行灵活性可靠性大大提高,进而最终提高机组效率的目的。
7.本实用新型所采用的技术方案为:一种高参数垃圾焚烧余热锅炉的再热蒸汽系统,该再热蒸汽系统包括:
8.锅炉,所述锅炉的顶部设有锅炉顶板且锅炉的内部设有烟气通道;
9.布置于锅炉外部的汽汽换热器,所述汽汽换热器不与烟气通道相接触;
10.布置于锅炉内部的锅筒,所述锅筒输出的饱和蒸汽经汽汽换热器换热后形成饱和水自动回流至锅筒,从汽汽换热器返回锅筒的饱和水,其流动的动力全部来自锅炉给水泵和自身重力,不需设置其他的动力设备,也不会增加给水泵的功率,且通过汽汽换热器的换热对低温再热蒸汽再加热后形成高温再热蒸汽。
11.进一步地,所述汽汽换热器和锅筒分别布置于锅炉顶板的上下两侧,汽汽换热器通过支撑组件装配连接于锅炉顶板上,且锅筒通过悬吊组件装配连接于锅炉顶板;将汽汽换热器布置在锅炉顶板上,整体采用支撑结构,不需增加锅炉的构架高度和锅炉房整体高度,同时,汽汽换热器位于锅炉顶部靠近炉前方向,以最大限度缩短再热蒸汽连接管长度,减少再热蒸汽的阻力损失和散热损失;将锅筒采用悬吊结构安装在锅炉顶板上,适用于大容量垃圾焚烧余热锅炉的内部设计。
12.进一步地,所述汽汽换热器布置在锅筒之上,汽汽换热器的中心线与锅筒的中心线在高度方向上的高度差为h,且h不小于4.0米;该高度h的选取使饱和水向下流入锅筒的势能足以克服饱和蒸汽向上流动的阻力和蒸汽在换热器内的流动阻力,使之形成自然循环,确保有足够的饱和蒸汽进入换热器中。
13.进一步地,所述烟气通道内沿烟气的流向依次布置有蒸发屏、多个过热器和多个省煤器;在锅炉的烟道内设置有蒸发屏、过热器和省煤器,过热器受热面布置在余热锅炉的水冷烟道内,锅炉出口主蒸汽温度达到400
‑
450℃,压力不低于6.0mpa。再热蒸汽受热面不与余热锅炉的烟气直接接触和换热。
14.在本实用新型的技术方案中还提供了一种汽汽换热器,该汽汽换热器应用于上述所述的高参数垃圾焚烧余热锅炉的再热蒸汽系统,其包括:
15.换热器壳体;
16.设于换热器壳体上的低温再热蒸汽输入端和高温再热蒸汽输出端;
17.设于换热器壳体内的多个蛇形管,各个所述蛇形管的两端分别伸出至换热器壳体的外部且分别作为饱和蒸汽输入端和饱和水输出端,在饱和水出口设置有消旋装置,避免水中夹带蒸汽,影响流动;
18.汽汽换热器中压力相对更高的饱和蒸汽在蛇形管内流动,压力低的再热蒸汽在蛇形管外流动,有利于减少换热器壳体壁厚,壳体壁温偏差影响小。
19.进一步地,所述换热器壳体内沿低温再热蒸汽至高温再热蒸汽的汽流方向上设有多层隔板,增加再热蒸汽流程,延长其停留时间,以进一步加强换热效果。
20.进一步地,所述换热器壳体为圆筒状结构,且换热器壳体的两端为半椭球型结构、半球型结构或者圆形平板结构,以便于再热蒸汽在其内部的有效流动,同时,汽汽换热器布置在锅炉顶部靠近炉前方向,以尽量缩短再热蒸汽连接管长度。
21.在本实用新型的技术方案中,还提供了另一种汽汽换热器,该汽汽换热器应用于上述所述的高参数垃圾焚烧余热锅炉的再热蒸汽系统,其包括:
22.换热器壳体,所述换热器壳体内部被分隔成第一隔离腔、第二隔离腔和第三隔离腔,且第一隔离腔设有与其连通的饱和蒸汽输入端,第二隔离腔设有与其连通的饱和水输出端;在饱和水出口设置有消旋装置,避免水中夹带蒸汽,影响流动;
23.低温再热蒸汽输入端和高温再热蒸汽输出端,所述低温再热蒸汽输入端和高温再热蒸汽输出端分别与第三隔离腔连通,且第三隔离腔内设有多个换热管,各个换热管的一端连通至第一隔离腔,另一端连通至第二隔离腔;
24.汽汽换热器中压力相对更高的饱和蒸汽在换热管内流动,压力低的再热蒸汽在换热管外流动,有利于减少换热器壳体壁厚,壳体壁温偏差影响小。
25.进一步地,所述第三隔离腔内沿低温再热蒸汽至高温再热蒸汽的汽流方向上设有多层隔板,增加再热蒸汽流程,延长其停留时间,以进一步加强换热效果。
26.进一步地,各所述换热管均设为u形状结构,有利于流动于各个换热管内的饱和蒸汽进行有效换热。
27.进一步地,所述换热器壳体为圆筒状结构,以便于再热蒸汽在其内部的有效流动,同时,汽汽换热器布置在锅炉顶部靠近炉前方向,以尽量缩短再热蒸汽连接管长度。
28.本实用新型的有益效果为:
29.1.采用本实用新型所提供的高参数垃圾焚烧余热锅炉的再热蒸汽系统,由于锅炉的再热器受热面不与烟气直接接触,没有再热器受热面的腐蚀问题,而加热用的饱和蒸汽也是来自锅炉的水冷系统中的锅筒,对水冷系统腐蚀的风险小,锅炉运行安全性高,通过合理设计再热蒸汽受热面布置位置,避免再热器受热面的高温腐蚀问题,系统运行自动调节,无需设置其他辅助系统,运行灵活性、可靠性大大提高。
附图说明
30.图1是本实用新型所提供的高参数垃圾焚烧余热锅炉的再热蒸汽系统的整体布置结构示意图;
31.图2是本实用新型所提供的高参数垃圾焚烧余热锅炉的再热蒸汽系统中汽汽换热器在实施例1中汽汽换热器的结构示意图;
32.图3是本实用新型所提供的高参数垃圾焚烧余热锅炉的再热蒸汽系统中汽汽换热器在实施例2中汽汽换热器的结构示意图;
33.附图中标注如下:
[0034]1‑
汽汽换热器,2
‑
锅炉顶板,3
‑
锅筒,4
‑
过热器,5
‑
省煤器,6
‑
换热器壳体,7
‑
分隔板,8
‑
饱和蒸汽输入端,9
‑
饱和水输出端,10
‑
低温再热蒸汽输入端,11
‑
高温再热蒸汽输出端,12
‑
半圆板,13
‑
第二隔板,14
‑
第一隔板,15
‑
第三隔板,16
‑
换热管,17
‑
蒸发屏。
具体实施方式
[0035]
为使本实用新型实施例的目的、技术方案和优点更加清楚,下面将结合本实用新型实施例中的附图,对本实用新型实施例中的技术方案进行清楚、完整地描述,显然,所描述的实施例是本实用新型一部分实施例,而不是全部的实施例。通常在此处附图中描述和示出的本实用新型实施例的组件可以以各种不同的配置来布置和设计。
[0036]
因此,以下对在附图中提供的本实用新型的实施例的详细描述并非旨在限制要求保护的本实用新型的范围,而是仅仅表示本实用新型的选定实施例。基于本实用新型中的实施例,本领域普通技术人员在没有作出创造性劳动前提下所获得的所有其他实施例,都属于本实用新型保护的范围。
[0037]
需要说明的是,在不冲突的情况下,本实用新型中的实施例及实施例中的特征可以相互组合。
[0038]
应注意到:相似的标号和字母在下面的附图中表示类似项,因此,一旦某一项在一个附图中被定义,则在随后的附图中不需要对其进行进一步定义和解释。
[0039]
在本实用新型实施例的描述中,需要说明的是,指示方位或位置关系为基于附图所示的方位或位置关系,或者是该实用新型产品使用时惯常摆放的方位或位置关系,或者是本领域技术人员惯常理解的方位或位置关系,或者是该实用新型产品使用时惯常摆放的方位或位置关系,仅是为了便于描述本实用新型和简化描述,而不是指示或暗示所指的装置或元件必须具有特定的方位、以特定的方位构造和操作,因此不能理解为对本实用新型的限制。此外,术语“第一”、“第二”仅用于区分描述,而不能理解为指示或暗示相对重要性。
[0040]
在本实用新型实施例的描述中,还需要说明的是,除非另有明确的规定和限定,术语“设置”、“连接”应做广义理解,例如,可以是固定连接,也可以是可拆卸连接,或一体地连接;可以是直接连接,也可以通过中间媒介间接连接。对于本领域的普通技术人员而言,可以具体情况理解上述术语在本实用新型中的具体含义;实施例中的附图用以对本实用新型实施例中的技术方案进行清楚、完整地描述,显然,所描述的实施例是本实用新型一部分实施例,而不是全部的实施例。通常在此处附图中描述和示出的本实用新型实施例的组件可以以各种不同的配置来布置和设计。
[0041]
实施例1
[0042]
目前国内外已有的垃圾焚烧炉排炉余热锅炉,为增加电厂收益,在提升蒸汽压力的同时,倾向于设置再热器系统,以提高发电效率。但增设的再热器受热面布置在锅炉烟道中,一方面与锅炉原有的过热器4争夺有限的高温级受热面换热所需烟温范围资源,使高温级受热面布置困难,影响锅炉运行的灵活性;另一方面,增加的再热器受热面同样存在高温腐蚀的风险。在本实施例中,具体提供一种高参数垃圾焚烧余热锅炉的再热蒸汽系统,再热器受热面不是布置在锅炉烟道内,而是采用汽汽换热器1型式。再热器系统蒸汽流程是将来自汽轮机的低温再热蒸汽进入汽汽换热器1中,被来自锅筒3的饱和蒸汽加热后,温度合格的再热蒸汽返回汽轮机做功。
[0043]
如图1所示,该再热蒸汽系统主要包括:锅炉、汽汽换热器1以及锅筒3,其具体设计如下:
[0044]
在所述锅炉的顶部设有锅炉顶板2且锅炉的内部设有烟气通道,烟气通道位于锅炉顶板2的下方,烟气通道内沿烟气的流向依次布置有蒸发屏17、多个过热器4和多个省煤器5;在锅炉内的烟气依次经过蒸发屏17、各个过热器4和各个省煤器5,锅炉的省煤器5系统、水冷系统和过热器4系统受热面布置与常规垃圾焚烧余热锅炉相同,即水冷系统受热面布置在高烟温区域,过热器4受热面布置在烟温在600
‑
620℃及以下的区域,省煤器5布置在低烟温区域。
[0045]
在锅炉顶板2的外侧布置汽汽换热器1,所述汽汽换热器1不与烟气通道相接触,汽汽换热器1可以布置一个或多个,进入余热锅炉的再热蒸汽全部被来自锅筒3的饱和蒸汽加热,再热蒸汽受热再加热在一个或多个汽汽换热器1中完成。将汽汽换热器1布置在锅炉顶板2仅是本实施例优选的应用方案,在实际应用时,汽汽换热器1可以布置在锅炉附近,也可以布置在汽轮机房。在本实施例中,将汽汽换热器1布置在锅炉顶部,且通过支撑组件安装
在锅炉顶板2上,距离锅筒3有一定高度;具体为:汽汽换热器1的中心线与锅筒3的中心线在高度方向上的高度差为h,且h不小于4.0米。进而确保在汽汽换热器1中冷凝下来的饱和水在重力作用下自动返回锅筒3中,既避免了热量的损失,也不需设置其他布置方案所需的再循环增压泵,由于汽汽换热器1出口的饱和水温度较高,如不返回锅筒3,则饱和水携带的热量无法高效利用。优选的,将汽汽换热器1通过支座固定的锅炉顶板2上,而锅筒3采用吊杆/板悬吊在顶板上,两者中心线的高度差为6.5米,通过合理设计饱和水与饱和蒸汽流速和管子走向,使饱和水向下流动的势能足以克服流动阻力,形成自然循环,并保证足够的饱和蒸汽进入换热器中。
[0046]
在锅炉顶板2的内侧布置锅筒3,以实现将汽汽换热器1和锅筒3分别布置于锅炉顶板2的两侧,且锅筒3通过悬吊组件装配连接于锅炉顶板2。在本实施例中,之所以将汽汽换热器1布置在锅筒3的上方,是因为如果将换热器布置在汽机房或其他高度低于锅筒3的位置,由于重力的存在,饱和水无法自动流回锅筒3,必须通过循环泵增压,克服换热器与锅筒3间的重位压差才能送回;不仅增加了运行的电耗,循环泵长期在高温介质情况下工作,且饱和水中不可避免有一定的含汽率会导致循环泵的汽蚀问题,也增加了运行的风险点。
[0047]
在本实施例中,如图2所示,对于汽汽换热器1的设计如下,主要包括:换热器壳体6和设于换热器壳体6内的多个蛇形管,各个蛇形管在换热器壳体6内呈相互平行的方式排列。由于在汽汽换热器1内部设置有多根并联的管路,管路在换热器壳体6内呈蛇形布置,以增加其在圆筒内的长度,增加换热面积。
[0048]
换热器壳体6设为圆筒状结构,该圆筒状结构的外部则为再热蒸汽受热面,在换热器壳体6上设有低温再热蒸汽输入端10和高温再热蒸汽输出端11,低温再热蒸汽输入端10接入来自汽轮机高压缸出口的低温再热蒸汽,且高温再热蒸汽输出端11返回至汽轮机做功。
[0049]
将各个所述蛇形管的两端分别伸出至换热器壳体6的外部且分别作为饱和蒸汽输入端8和饱和水输出端9,蛇形管由小口径管弯制而成。在饱和蒸汽输入端8接入来自锅筒3的饱和蒸汽,饱和水输出端9回流至锅筒3中。在实际应用时,在饱和水接口处设置有消旋装置,避免出口水中夹带蒸汽。
[0050]
为加强换热效果,在所述换热器壳体6内沿低温再热蒸汽至高温再热蒸汽的汽流方向上设有多层分隔板7,在各层分隔板7的作用下,增加了再热蒸汽在换热器壳体6内的流动路程,并进一步延长其停留时间,进而确保有效换热。
[0051]
本实施例中汽汽换热器1在工作时,来自锅筒3压力相对较高的饱和蒸汽在蛇形管内流动,来自汽轮机高压缸排汽的再热蒸汽在蛇形管外流动,换热器壳体6的承压相对较小;对于汽汽换热器1内部的工作原理具体如下:
[0052]
一方面,来自锅筒3的饱和蒸汽从换热器壳体6上部的饱和蒸汽输入端8进入,在各个蛇形管的管内流动并对管外流动在换热器壳体6内的再热蒸汽放热,饱和蒸汽被冷凝为饱和水并在管内向下流动,从换热器壳体6底部的饱和水输出端9排出;另一方面,来自汽轮机高压缸出口的低温再热蒸汽从换热器壳体6底部的低温再热蒸汽输入端10进入换热器壳体6的内部中,向上流动过程中被各个蛇形管内的饱和蒸汽加热,加热后为高温再热蒸汽,高温再热蒸汽流动至换热器壳体6的顶部时,蒸汽温度已经达到所需的温度,离开换热器壳体6并由连接管引回汽轮机做功。
[0053]
目前,锅炉主蒸汽压力采用国内成熟的次高压及以上(≥6.0mpa)参数,主蒸汽温度均为450℃,锅炉的高温级过热器4(工质温度在400℃以上)受热面布置在余热锅炉的水冷烟道内,利用水冷烟道内烟温相对较高的烟气使过热蒸汽升温,以获得所需要的工质温度。锅炉的再热蒸汽出口温度略低于锅筒3工作温度,采用本实施例中上述的再热蒸汽系统,其工作原理为:
[0054]
在锅炉烟道内不设置再热器受热面,再热器受热面设置在烟道外的汽汽换热器1中,来自汽轮机高压缸出口的低温再热蒸汽全部进入汽汽换热器1,来自锅筒3的一部分饱和蒸汽也进入汽汽换热器1,以将低温再热蒸汽加热至额定温度形成高温再热蒸汽,然后离开锅炉,高温再热蒸汽返回汽轮机继续做功,汽汽换热器1中的饱和蒸汽被冷凝下来的饱和水,能够在重力作用下自动返回锅筒3中。
[0055]
因此,上述方案中再热蒸汽系统布置与常规垃圾焚烧余热锅炉不同,锅炉主蒸汽参数为13.7mpa/450℃,再热蒸汽进口温度为215℃/320℃,将再热蒸汽受热面全部布置在位于锅炉炉顶的汽汽换热器1内,利用来自锅筒3的饱和蒸汽(~340℃)加热再热蒸汽,冷凝下来的饱和水在重力作用下自动返回锅筒3,不需另外的动力设备,也不会增加锅炉已有动力设备电耗,好处在于:
[0056]
①
不设置再循环泵,减少了给水泵及其附属设备的电耗;
[0057]
②
饱和水不可避免会带有蒸汽,不设置循环泵,也就没有循环泵的汽蚀风险,检修和维护工作量降低。
[0058]
实施例2
[0059]
在实施例1中所提供的再热蒸汽系统中,对其汽汽换热器1采用另一种方式设计,如图3所示,汽汽换热器1主要包括:换热器壳体6,且换热器壳体6设为圆筒状结构,该圆筒状结构的外部则为再热蒸汽受热面,同样,该再热蒸汽受热面不与烟气直接接触。
[0060]
将换热器壳体6内部被分隔成第一隔离腔、第二隔离腔和第三隔离腔,具体设计如下:在换热器壳体6内设有半圆板12、第一隔板14、第二隔板13和第三隔板15,由第一隔板14将换热器壳体6的内部分为两个部分,一部分由半圆板12、第一隔板14、第二隔板13分隔成第一隔离腔和第二隔离腔,其第一隔离腔设有与其连通的饱和蒸汽输入端8且第二隔离腔设有与其连通的饱和水输出端9,在实际应用时,在饱和水接口处设置有消旋装置,以避免出口水中夹带蒸汽;另一部分则为第三隔离腔,第三隔离腔设有与其连通的低温再热蒸汽输入端10和高温再热蒸汽输出端11。
[0061]
在第三隔离腔内设有多个换热管16,各个换热管16的一端连通至第一隔离腔,另一端连通至第二隔离腔。各所述换热管16均设为u形状结构且第一隔板14为多孔板,各个换热管16的两端端部均穿过第一隔板14且伸入至第一隔离腔和第二隔离腔内。在汽汽换热器1内部设置有多根并联的换热管16,换热管16在换热器壳体6内呈盘管布置,以增加其在圆筒内的长度,增加换热面积。
[0062]
为进一步加强换热效果,所述第三隔离腔内沿低温再热蒸汽至高温再热蒸汽的汽流方向上设有多层第三隔板15,在各层第三隔板的作用下,增加了再热蒸汽在换热器壳体6内的流动路程,并进一步延长其停留时间,进而确保有效换热,例如:将各层第三隔板密封装配在换热器壳体6内,并在各层第三隔板上开设有通气孔,在通气孔的作用下,将各层第三隔板间的汽流通道改变为蛇形状,以进一步延长再热蒸汽在第三隔离腔内部的停留时
间。
[0063]
在本实施例中,汽汽换热器1在工作时,来自锅筒3压力相对较高的饱和蒸汽在换热管16内流动,来自汽轮机高压缸排汽的再热蒸汽在换热管16外流动,换热器壳体6承压相对较小。汽汽换热器1的工作原理如下:
[0064]
来自锅筒3的饱和蒸汽进入该第一隔离腔,从位于第一隔板14上的开孔进入各个换热管16中,并对换热管16外的再热蒸汽放热,冷凝下来的饱和水从位于第一隔板14下部的开孔进入第二隔离腔内,通过第二隔离腔底部的开孔离开换热器壳体6,并在重力作用下回到锅筒3中;在换热器壳体6右侧的第三隔离腔内设置了多个第三隔板15,使该第三隔离腔内流动的再热蒸汽流动路程增加,进而强化了换热效果。
[0065]
本实用新型不局限于上述可选实施方式,任何人在本实用新型的启示下都可得出其他各种形式的产品,但不论在其形状或结构上作任何变化,凡是落入本实用新型权利要求界定范围内的技术方案,均落在本实用新型的保护范围之内。