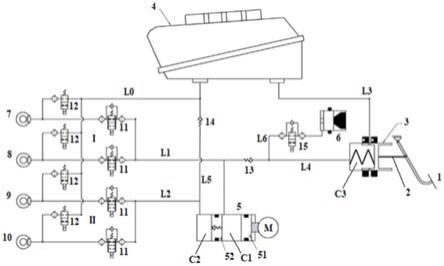
1.本实用新型涉及机动车制动领域,更具体地,涉及电子液压制动系统和包括该电子液压制动系统的机动车。
背景技术:
2.电子液压制动系统也称作是线控制动系统,其相对于传统的制动系统具有许多优点,因而在如今的机动车中得到广泛应用。在线控制动模式下,可电控制的压力提供装置根据踏板行程传感器等检测到的信号产生使车轮制动所需的制动压力。在发生电气故障的情况下,通过制动主缸来产生所需的制动压力。
3.在一种典型的用于双制动回路的电子液压制动系统中,制动主缸构造成串联主缸,在制动主缸与各制动回路之间设置有常开的隔离阀,在可电控制的压力提供装置与各制动回路之间设置有常闭的接通阀。这样的电子液压制动系统结构复杂且成本较高。另外,在一个制动回路发生泄漏的情况下,可能无法在另一制动回路中建立制动压力。
技术实现要素:
4.本实用新型是鉴于以上背景而做出的,旨在提供一种结构简单且成本低的电子液压制动系统。
5.本实用新型的第一方面提供了一种电子液压制动系统,该电子液压制动系统包括制动主缸和可电控制的压力提供装置,所述可电控制的压力提供装置包括电机和缸-活塞组件,所述缸-活塞组件包括设置在缸体中的第一活塞和第二活塞,所述第一活塞和所述第二活塞以及所述缸体限定第一液压腔和第二液压腔。
6.在一个优选实施方式中,所述第一液压腔与第一制动回路液压连通,并且通过朝所述第一液压腔和所述第一制动回路打开的单向阀与所述制动主缸的液压腔液压连通;所述第二液压腔与第二制动回路液压连通。
7.在一个优选实施方式中,所述第一活塞通过旋转-平移传动机构与所述电机连接。
8.在一个优选实施方式中,所述第二液压腔设置在所述第二活塞与端盖之间,所述端盖上固设有伸入所述第二液压腔中的导向杆,所述第二活塞上固设有伸入所述第二液压腔中的导向套筒。
9.在一个优选实施方式中,在所述第二液压腔中设置有第一弹簧,所述第一弹簧连接在所述第二活塞与所述端盖之间。
10.在一个优选实施方式中,所述第二活塞形成有能够连通所述第一液压腔和所述第二液压腔的中央通道,在所述中央通道中设置有阀销、第二弹簧和挡板,所述阀销能够在第一液压腔侧封闭所述中央通道,所述挡板连接到所述阀销的位于第二液压腔侧的端部,所述第二弹簧的一端连接到所述挡板。
11.在一个优选实施方式中,所述电子液压制动系统还包括模拟装置,所述模拟装置经由模拟器阀与所述制动主缸液压连通。
12.在一个优选实施方式中,所述模拟器阀是常闭的电磁阀,并且连接在所述单向阀、所述模拟装置以及所述制动主缸之间。
13.在一个优选实施方式中,所述电子液压制动系统还包括用于每个车轮制动器的常开的进入阀和常闭的排出阀。
14.本实用新型的第二方面提供了一种机动车,该机动车包括根据上述第一方面的电子液压制动系统。
15.本实用新型提供的电子液压制动系统省去了与制动主缸相关联的隔离阀和与可电控制的压力提供装置相关联的接通阀,并且不需要采用串联主缸,简化了系统结构且降低了成本。另外,该电子液压制动系统提高了在制动回路中发生泄漏情况下的冗余安全性能。
附图说明
16.图1是根据本实用新型一实施例的电子液压制动系统的示意图。
17.图2是可电控制的压力提供装置的缸-活塞组件的局部示意图。
具体实施方式
18.下面参照附图描述本实用新型的具体实施例。
19.图1示出了根据本实用新型一实施例的电子液压制动系统的示意图。如图1所示,该电子液压制动系统包括:可借助于制动踏板1经由推杆2操纵的制动主缸3;被分配给制动主缸3的、处于大气压力下的压力介质储备容器4;可电控制的压力提供装置5;与制动主缸3共同作用的模拟装置6;设置在每个车轮处的可液压操纵的车轮制动器7、8、9、10;可电控制的、用于调整各个车轮处的制动压力的压力调制装置,其包括用于每个车轮制动器的常开的进入阀11和常闭的排出阀12;以及未示出的电子控制单元。
20.在图1所示的实施例中,车轮制动器7、8被分配给第一制动回路i,车轮制动器9、10被分配给第二制动回路ii。第一制动回路i中的车轮制动器7、8分别是左前轮制动器和右后轮制动器,第二制动回路ii中的车轮制动器9、10分别是右前轮制动器和左后轮制动器。然而,本实用新型并不局限于此。例如,在另外的实施例中,第一制动回路i中的车轮制动器7、8可以分别是左前轮制动器和右前轮制动器,而第二制动回路ii中的车轮制动器9、10可以分别是左后轮制动器和右后轮制动器。
21.进入阀11和排出阀12成对地通过液压管路连接在一起,并且通过管接头液压地连接到相应的车轮制动器。排出阀12的输出接头通过回流管路l0与压力介质储备容器4相连接。第一制动回路i的两个进入阀11的输入接头通过制动回路供给管路l1相互连接。第二制动回路ii的两个进入阀11的输入接头通过制动回路供给管路l2相互连接。各进入阀11分别与朝制动回路供给管路l1、l2的方向打开的单向阀/止回阀并联。
22.不同于具有两个相继布置的活塞的常规串联主缸,在本实施例中,制动主缸3在主缸壳体中仅具有一个活塞,该活塞与主缸壳体界定液压腔c3。液压腔c3通过构造在活塞中的径向孔以及液压管路l3与压力介质储备容器4相连接,该连接可通过活塞在主缸壳体中的相对运动而被阻断。在液压腔c3中设置有复位弹簧,在制动主缸3未通过制动踏板1而被操纵时,复位弹簧使活塞定位在初始位置中。制动踏板1设置在驾驶室内,可由驾驶员尤其
是通过其脚来操纵。驾驶员通过下压制动踏板1而要求车辆减速。推杆2将由于踏板操纵引起的制动踏板1的摆动运动与活塞的平移运动耦合,该活塞的操纵行程可由位移传感器检测。由此,相应的活塞行程信号是制动踏板操作程度的度量。该信号反映了驾驶员的制动意愿。也可通过设置在制动踏板1上的踏板行程传感器来检测制动踏板的操作程度。
23.液压腔c3借助于液压管路l4与制动回路供给管路l1相连接。在液压管路l4中布置有单向阀13,该单向阀13朝制动回路供给管路l1的方向打开,即,朝第一制动回路i的方向打开。
24.可电控制的压力提供装置5包括电机m和缸-活塞组件。图2示出了本实施例中的缸-活塞组件的局部示意图。不同于常规的可电控制的压力提供装置,本实施例中的缸-活塞组件包括可滑动地设置在缸体50中的第一活塞51和第二活塞52。在第一活塞51和第二活塞52与缸体50之间设置有密封件,例如o形密封圈。第一活塞51通过旋转-平移传动机构与电机m连接。第一活塞51、第二活塞52以及缸体50一起限定第一液压腔c1。第二活塞52、缸体50以及端盖53一起限定第二液压腔c2。
25.如图1所示,第一液压腔c1通过制动回路供给管路l1与第一制动回路i液压连通,并且通过上述设有单向阀13的液压管路l4与制动主缸3的液压腔c3液压连通。第二液压腔c2通过制动回路供给管路l2与第二制动回路ii液压连通。第二液压腔c2还通过液压管路l5与压力介质储备容器4液压连通。在液压管路l5中设置有朝第二液压腔c2的方向打开的单向阀14。
26.如图2所示,第二液压腔c2设置在第二活塞52与端盖53之间。端盖53上固设有伸入第二液压腔c2中的导向杆部。在本实施例中,端盖53与导向杆部一体地形成。在另外的实施例中,端盖53也可以与导向杆部分开地形成,并通过焊接、螺纹连接等固定方式固定在一起。第二活塞52上固设有伸入第二液压腔c2中的导向套筒54。在第二液压腔c2中还设置有第一弹簧55,该第一弹簧55连接在第二活塞52与端盖53之间。
27.此外,第二活塞52形成有能够连通第一液压腔c1和第二液压腔c2的中央通道,在该中央通道中设置有阀销56、第二弹簧57和挡板58。阀销56能够在第一液压腔c1侧封闭该中央通道。挡板58连接到阀销56的位于第二液压腔c2侧的端部。第二弹簧57的一端连接到挡板58,另一端连接到第二活塞52的本体部。阀销56、第二弹簧57和挡板58共同构成朝第一液压腔c1的方向打开的单向阀。阀销56的位于第一液压腔c1侧的端部设有密封橡胶59。
28.模拟装置6液压地连接到制动主缸3,并且包括模拟器活塞和由模拟器活塞分隔开的模拟器腔和弹簧腔。模拟器腔可借助于液压管路l6及液压管路l4与制动主缸3的液压腔c3相连接。在弹簧腔中设置有预紧的弹性元件,模拟器活塞通过所述弹性元件支撑在模拟器壳体上。在液压管路l6中设置有模拟器阀15。模拟器阀15是常闭的电磁阀,连接在单向阀13、模拟装置6以及制动主缸3之间。与模拟器阀15并联地布置朝液压管路l4的方向打开的单向阀,这实现了压力介质与模拟器阀15的切换状态无关且尽可能无障碍地从模拟器腔流回制动主缸3的液压腔c3。
29.根据本实施例的电子液压制动系统省去了与制动主缸相关联的隔离阀和与可电控制的压力提供装置相关联的接通阀,并且不需要采用串联主缸,因此简化了系统结构且降低了成本。
30.下面描述根据本实施例的电子液压制动系统的作用方式。
31.作为系统初次运行前的准备工作,首先打开所有的进入阀11以及模拟器阀15。由此,各液压回路与压力介质储备容器4形成通路,系统内的气体可以通过压力介质储备容器4抽出而形成真空。然后,从压力介质储备容器4向系统注入压力介质,例如制动液。具体地,压力介质储备容器4中的压力介质经由液压管路l3进入制动主缸3的液压腔c3,并且经由液压管路l5进入可电控制的压力提供装置5的第二液压腔c2。制动主缸3的液压腔c3中的压力介质可经由单向阀13进入可电控制的压力提供装置5的第一液压腔c1。另外,第二液压腔c2中的压力介质也可通过第二活塞52的中央通道进入第一液压腔c1。
32.在正常的线控制动模式下,当驾驶员踩下制动踏板1时,推杆2使制动主缸3的活塞向前运动,在液压腔c3中产生液压力。位移传感器检测主缸活塞的行程作为控制信号,电子控制单元基于该控制信号驱动可电控制的压力提供装置5的电机m旋转。电机m的旋转运动通过旋转-平移传动机构转换成第一活塞51的平移运动,由此在第一液压腔c1中产生液压力。第一液压腔c1中的液压力经由制动回路供给管路l1进入第一制动回路i的车轮制动器7、8中。与此同时,第一液压腔c1中的液压力克服第一弹簧55的作用使第二活塞52朝端盖53的方向前移,由此在第二液压腔c2中产生液压力。第二液压腔c2中的液压力经由制动回路供给管路l2进入第二制动回路ii的车轮制动器9、10中。这样,实现了整车四个车轮的制动。
33.在线控制动模式下,模拟器阀15打开,压力介质可从制动主缸3的液压腔c3流入模拟装置6的模拟器腔中,以便给驾驶员提供舒适的制动踏板感觉。本领域技术人员能够理解,在线控制动模式下,制动主缸3的液压腔c3中的液压力小于可电控制的压力提供装置5的第一液压腔c1中的液压力。
34.当车辆在光滑的路面、例如冰雪路面上行驶时,在制动过程中可能触发abs功能,尤其是对于趋于抱死的车轮,其车轮制动器反复地经历增压、压力保持和降压过程。在增压过程中,进入阀11保持打开且排出阀12保持关闭,第一液压腔c1或第二液压腔c2中的压力介质经制动回路供给管路l1或l2和进入阀11进入车轮制动器7、8、9、10。在压力保持过程中,关闭进入阀11且使排出阀12保持关闭。在降压过程中,打开排出阀12并关闭进入阀11,车轮制动器7、8、9、10中的压力介质经由排出阀12和回流管路l0排出到压力介质储备容器4中。如此反复几个循环以后,很可能第一活塞51就抵靠于第二活塞52或者第二活塞52就抵靠于端盖53,因而第一液压腔c1或第二液压腔c2无法提供更多的压力介质。由于处于线控制动模式下,驾驶员无法感知这一变化,可能造成危险后果。
35.在根据本实施例的电子液压制动系统中,当第一液压腔c1或第二液压腔c2中的压力介质减少到一定程度时,可通过例如设置在制动回路供给管路l1或l2上的压力传感器(图中未示出)探测到这一情况。相应地,电子控制单元将进入阀11关闭(例如,在降压过程中或者在压力保持过程中),并控制电机m带动第一活塞51回到初始位置。此时,由于制动踏板1的下压使得制动主缸3的活塞前移,制动主缸3的液压腔c3与液压管路l3之间的连接被阻断,压力介质无法从压力介质储备容器4经由液压管路l3、l4进入第一液压腔c1。随着第一液压腔c1和第二液压腔c中的压力降低,压力介质储备容器4中储存的压力介质经由液压管路l5被吸入第二液压腔c2,进而通过由阀销56、第二弹簧57和挡板58构成的单向阀进入第一液压腔c1。因此,当在随后的增压过程中打开进入阀11后,确保了第一液压腔c1和第二液压腔c2能够源源不断的提供压力介质。
36.在发生电气失效,即电机m以及各个电磁阀无法动作的情况下,当驾驶员踩下制动
踏板1时,推杆2同样使制动主缸3的活塞向前运动,在液压腔c3中产生液压力。该液压力通过单向阀13和制动回路供给管路l1进入第一制动回路i的车轮制动器7、8中,同时进入可电控制的压力提供装置5的第一液压腔c1中并推动第二活塞52朝端盖53的方向前移,由此在第二液压腔c2中产生液压力。第二液压腔c2中的液压力经由制动回路供给管路l2进入第二制动回路ii的车轮制动器9、10中。这样,同样实现了整车四个车轮的制动。
37.此外,在第一制动回路i中发生泄漏的情况下,当驾驶员踩下制动踏板1时,推杆2使制动主缸3的活塞向前运动,位移传感器检测主缸活塞的行程作为控制信号,电子控制单元基于该控制信号驱动可电控制的压力提供装置5的电机m旋转。电机m的旋转运动通过旋转-平移传动机构转换成第一活塞51的平移运动。由于第一制动回路i中存在泄漏,此时无法在第一液压腔c1中产生液压力。当第一活塞51移动至抵靠在第二活塞52上、尤其是抵靠在密封橡胶59上之后,该第一活塞51推动第二活塞52朝端盖53的方向前移,由此在第二液压腔c2中产生液压力。该液压力经由制动回路供给管路l2进入第二制动回路ii的车轮制动器9、10中。由此,能够在线控制动模式下实现第二制动回路ii的单回路制动。
38.另一方面,在第二制动回路ii中发生泄漏的情况下,当驾驶员踩下制动踏板1时,推杆2使制动主缸3的活塞向前运动,位移传感器检测主缸活塞的行程作为控制信号,电子控制单元基于该控制信号驱动可电控制的压力提供装置5的电机m旋转。电机m的旋转运动通过旋转-平移传动机构转换成第一活塞51的平移运动,由此在第一液压腔c1中产生液压力。由于第二制动回路ii中存在泄漏,此时无法在第二液压腔c2中产生液压力。在第一液压腔c1中的液压力的作用下,第二活塞52快速朝端盖53前移,直至导向套筒54的一端抵靠在端盖53上。第一液压腔c1中的液压力经由制动回路供给管路l1进入第一制动回路i的车轮制动器7、8中。由此,能够在线控制动模式下实现第一制动回路i的单回路制动。
39.此外,在第二制动回路ii中发生泄漏的情况下,即使同时发生电机m以及各个电磁阀的电气失效,仍可通过制动主缸3的液压腔c3中的液压力来实现第一制动回路i的单回路制动。因此,提高了系统的冗余安全性能。
40.可以理解的是,本实用新型的上述实施例仅仅是为了说明本实用新型的原理而采用的示例性实施例,本实用新型并不局限于此。对于本领域内的普通技术人员而言,在不脱离本实用新型的精神和实质的情况下,可以做出各种变型和改进。本实用新型的保护范围仅由所附权利要求书的语言表述的含义及其等同含义所限定。