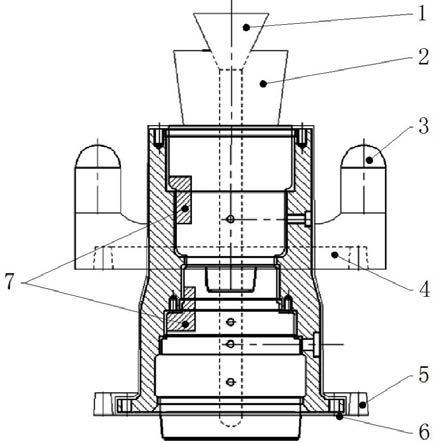
1.本实用新型属于铸造技术领域,具体涉及一种大型厚壁筒类铸件的浇冒口系统。
背景技术:
2.大型厚壁筒类铸钢件的结构特点是:铸件壁厚大、直径大和高度大,尤其是密度要求高的铸钢件,由于无论从高度方向补缩还是周向补缩,冒口补缩距离有限,经常会在某高度区域产生缩孔、缩松,然而现有技术选择顶冒口和侧冒口补缩的方式依然很难消除铸件缩孔、缩松的缺陷。
技术实现要素:
3.为了克服现有技术中存在的不足,解决现有技术中顶冒口和侧冒口无法解决大型厚壁筒类铸钢件补缩的技术问题,本实用新型提供一种大型厚壁筒类铸件的浇冒口系统。
4.本实用新型的设计构思为:位于砂箱底部的底层内浇口起到底注的作用,保证浇注平稳;位于砂箱中部的侧冒口起到控制温度场、接力补缩的作用;位于砂箱顶部的顶冒口保证得到热钢水,最终对铸件发挥更好的补缩作用。
5.本实用新型通过以下技术方案予以实现。
6.一种大型厚壁筒类铸件的浇冒口系统,所述大型厚壁筒类铸件采用重力浇注,浇口竖直向上设置于砂箱型腔偏心位置处的上方,其中:所述浇冒口系统包括顶冒口、侧冒口和底层内浇口,顶冒口、侧冒口和底层内浇口沿用于浇注厚壁筒类铸件砂箱的轴线方向由上至下依次设置;
7.所述顶冒口竖直向上对称设置于砂箱型腔的上方;
8.所述侧冒口竖直向上对称设置于砂箱中部的两侧,侧冒口的底部通过中部浇道与砂箱型腔连通,并且两侧侧冒口中心的连线与两侧顶冒口中心的连线异面垂直,中部浇道上下两侧砂箱型腔的侧壁上分别设置用于阻断补缩通道的冷铁;
9.所述底层内浇口设置于侧冒口下方的垂直投影位置处,底层内浇口的底部通过底部浇道与铸型内腔连通。
10.进一步地,所述大型厚壁筒类铸件为高度大于600mm、直径大于400 mm、壁厚大于50mm的筒类铸钢件。
11.进一步地,根据大型厚壁筒类铸件的直径沿圆周方向均布若干所述侧冒口。
12.与现有技术相比本实用新型的有益效果为:
13.本浇冒口系统由上至下依次设置顶冒口、侧冒口和底层内浇口,底层内浇口系统起到底注的作用,侧冒口起到控制温度场、接力补缩的作用,顶冒口保证顶冒口得到热钢水,最终对铸件发挥更好的补缩作用,针对大型厚壁筒类铸件的浇注系统进行升级改造,浇冒口系统能够满足对大型厚壁筒类铸钢件补缩的效果。
附图说明
14.图1为本实用新型的俯视结构示意图;
15.图2为图1中a-a面剖视结构示意图;
16.图3为顶冒口与浇口位置关系示意图。
17.图中,1为浇口,2为顶冒口,3为侧冒口,4为中部浇道,5为底层内浇口,6为底部横浇道,7为冷铁。
具体实施方式
18.以下实施例用于说明本实用新型,但不用来限制本实用新型的范围。若未特别指明,实施例均按照常规实验条件。另外,对于本领域技术人员而言,在不偏离本实用新型的实质和范围的前提下,对这些实施方案中的物料成分和用量进行的各种修改或改进,均属于本实用新型要求保护的范围。
19.本实用新型针对的是大型厚壁筒类铸件,其尺寸为高度大于600mm、直径大于400 mm、壁厚大于50mm的筒类铸钢件。高度大于600mm,因为铸件高度大时,竖直补缩距离不够,需设计两层及以上冒口,当铸件高度低时,采用现有技术中的一层顶冒口就可以;铸件直径大于400 mm,因为直径大时,冒口周向的补缩延续度不够,需要多个冒口;壁厚大于50mm,因为厚度小时,金属凝固时采用现有技术就可以消除缩孔、缩松。
20.如图1~图3所示的一种大型厚壁筒类铸件的浇冒口系统,所述大型厚壁筒类铸件采用重力浇注,浇口1竖直向上设置于砂箱型腔偏心位置处的上方,其中:所述浇冒口系统包括顶冒口2、侧冒口3和底层内浇口5,顶冒口2、侧冒口3和底层内浇口5沿用于浇注厚壁筒类铸件砂箱的轴线方向由上至下依次设置;
21.所述顶冒口2竖直向上对称设置于砂箱型腔的上方;
22.所述侧冒口3竖直向上对称设置于砂箱中部的两侧,侧冒口3通过浇口内浇入的钢水加热,实现热冒口加强补缩,并根据周向冒口的延续度对冒口的大小和数量进行设计,保证周向、上下充分得到补缩,侧冒口3的底部通过中部浇道4与砂箱型腔连通,并且两侧侧冒口3中心的连线与两侧顶冒口2中心的连线异面垂直,侧冒口3通过浇口内浇入的钢水加热,实现热冒口加强补缩,并根据周向冒口的延续度对侧冒口3的大小和数量进行设计,保证周向、上下充分得到补缩,中部浇道4上下两侧砂箱型腔的侧壁上分别设置用于阻断补缩通道的冷铁7;
23.所述底层内浇口5设置于侧冒口3下方的垂直投影位置处,底层内浇口5的底部通过底部横浇道6与铸型内腔连通。`
24.冷铁7分割顶冒口2上方的补缩通道和侧冒口3的补缩通道,即分割区域,通过上下顺序补缩,顶层冒口对其补缩上部区域补缩,侧冒口3对其补缩下部部位进行足够的补缩。这种设计解决了高度方向补缩距离不够的问题和圆周补缩距离不够的问题,方法是分割区域,部分顺序凝固,热冒口加强了侧冒口3有足够的热钢水补缩下部。
25.顶冒口、侧冒口的结构尺寸设计为比例法设计,浇注系统为开放式分层阶梯浇注方式,将本实用新型提供的浇冒口系统应用在悬臂筒上生产铸件,所生产的铸件没有缩孔、缩松缺陷,达到了客户的要求。
26.除此之外,还可以根据大型厚壁筒类铸件的直径沿圆周方向均布若干所述侧冒口
3。沿周向要按有效补缩距离设置足够大小和数量的冒口,以保证铸件的致密。
27.以上所述,仅为本实用新型的具体实施方式,但本实用新型的保护范围并不局限于此,任何熟悉技术领域的技术人员在本实用新型揭露的技术范围内,可轻易想到的变化或替换,都应涵盖在本实用新型的保护范围之内。因此,本实用新型的保护范围应以所述权利要求的保护范围为准。
技术特征:
1.一种大型厚壁筒类铸件的浇冒口系统,所述大型厚壁筒类铸件采用重力浇注,浇口(1)竖直向上设置于砂箱型腔偏心位置处的上方,其特征在于:所述浇冒口系统包括顶冒口(2)、侧冒口(3)和底层内浇口(5),顶冒口(2)、侧冒口(3)和底层内浇口(5)沿用于浇注厚壁筒类铸件砂箱的轴线方向由上至下依次设置;所述顶冒口(2)竖直向上对称设置于砂箱型腔的上方;所述侧冒口(3)竖直向上对称设置于砂箱中部的两侧,侧冒口(3)的底部通过中部浇道(4)与砂箱型腔连通,并且两侧侧冒口(3)中心的连线与两侧顶冒口(2)中心的连线异面垂直,中部浇道(4)上下两侧砂箱型腔的侧壁上分别设置用于阻断补缩通道的冷铁(7);所述底层内浇口(5)设置于侧冒口(3)下方的垂直投影位置处,底层内浇口(5)的底部通过底部浇道(6)与铸型内腔连通。2.根据权利要求1所述的一种大型厚壁筒类铸件的浇冒口系统,其特征在于:所述大型厚壁筒类铸件为高度大于600mm、直径大于400 mm、壁厚大于50mm的筒类铸钢件。3.根据权利要求1所述的一种大型厚壁筒类铸件的浇冒口系统,其特征在于:根据大型厚壁筒类铸件的直径沿圆周方向均布若干所述侧冒口(3)。
技术总结
一种大型厚壁筒类铸件的浇冒口系统,属于铸造技术领域,解决现有技术中顶冒口和侧冒口无法解决大型厚壁筒类铸钢件补缩的技术问题,解决方案为:顶冒口、侧冒口和底层内浇口沿砂箱的轴线方向由上至下依次设置,顶冒口竖直向上对称设置于砂箱型腔的上方,侧冒口竖直向上对称设置于砂箱中部的两侧,侧冒口的底部通过中部浇道与砂箱型腔连通,底层内浇口设置于侧冒口下方的垂直投影位置处,底层内浇口的底部通过底部浇道与铸型内腔连通。底层内浇口系统起到底注的作用,侧冒口起到控制温度场、接力补缩的作用,顶冒口保证顶冒口得到热钢水,最终对铸件发挥更好的补缩作用,本实用新型能够满足对大型厚壁筒类铸钢件补缩的效果。满足对大型厚壁筒类铸钢件补缩的效果。满足对大型厚壁筒类铸钢件补缩的效果。
技术研发人员:张光胜 马国梁 武晋国 张纬 史旭东 谢斌 李志勇 李瑞宁 王敏慧
受保护的技术使用者:晋西装备制造有限责任公司
技术研发日:2021.12.17
技术公布日:2022/2/15