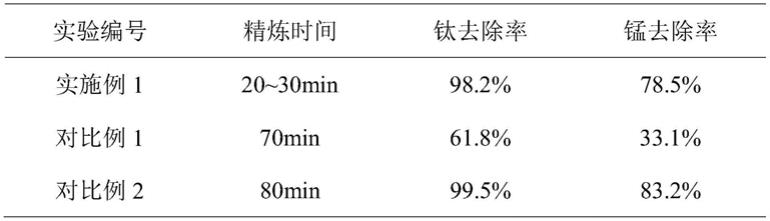
1.本发明涉及金属冶炼及原料制备领域,具体涉及一种精炼磷铁的配料及精炼方法。
背景技术:
2.粗磷铁(即精炼磷铁的磷铁原料)中含有较多的杂质,如钛、锰、钒等,对于磷铁的精炼,仍处于较为先进的技术,但其中也存在一些个问题。例如,磷铁精炼时采用中频感应炉,感应炉的原理是利用物料的感应电热效应而使物料加热或熔化的电炉。在感应炉中的交变电磁场作用下,物料内部产生涡流从而达到加热或着熔化的效果。对于原料磷铁均为大块,粒径约》50cm,经破碎后,产生不同粒径的样品,而磷铁中磷含量较高,导致磁性较弱,磁场作用下的感应电流较低,因而熔化的较慢;减短磷铁熔融时间对于提高磷铁精炼效率以及降低电耗是有很好的经济效益。
技术实现要素:
3.针对上述技术问题,本发明将对熔化过程中不同粒径的磷铁原料进行熔化时间对比,提出一种精炼磷铁的配料及精炼方法。
4.通过如下技术手段实现:
5.一种精炼磷铁的配料及精炼方法,包括如下步骤:
6.(1)磷铁配料,原料为大于50cm的磷铁,将该粒度的磷铁经机械破碎后筛分产生不同粒径的磷铁,将所述不同粒径的磷铁筛分为四个粒度区间,分别为a区间:0~10mm;b区间:1cm~10cm;c区间:10cm~20cm;d区间:》20cm(优选为20~35cm)。
7.(2)精炼剂配料,所述精炼剂为废弃渣和铁矿石的混合物,其中废弃渣与铁矿石的质量配比为1:(2~3);所述废弃渣为利用磷铁和造渣剂为原料生产高纯磷铁而得到的废弃渣,所述铁矿石为包括feo:65~75wt%,cao:10~20wt%,sio2:5~10wt%,其余为不可避免的杂质,其中不可避免的杂质中包括氧化镁,五氧化二磷水分。
8.(3)精炼,将感应炉加热升温,然后将步骤(1)配料得到的磷铁原料按照d区间,c区间,b区间,a区间的顺序加入至感应炉中,待磷铁完全熔融且炉内温度上升至1500~1600℃后,将步骤(2)配置得到的精炼剂加入至感应炉中,其中磷铁原料的加入量与精炼剂的加入量的重量比为20:(4~5);熔融精炼8~15min,待渣相熔融后,调整并保持温度为1300~1450℃,保持该温度16~25min后,直接出炉浇铸后分离出渣相,即得到精炼磷铁产品。
9.作为优选,步骤(3)中将步骤(1)配料得到的磷铁原料按照d区间,c区间,b区间,a区间的顺序加入至感应炉中,具体的加入分配方式为只添加d区间(即相当于100wt%的d区间,然后顺次添加0%的c、b和a区间)。
10.作为优选,步骤(3)中将步骤(1)配料得到的磷铁原料按照d区间,c区间,b区间,a区间的顺序加入至感应炉中,具体的加入分配方式为40~90重量份的d区间以及10~60重量份的a区间、b区间和c区间的组合。
11.作为优选,步骤(3)中将步骤(1)配料得到的磷铁原料按照d区间,c区间,b区间,a区间的顺序加入至感应炉中,具体的加入分配方式为不加入d区间和a区间,只加入75~85重量份的c区间和15~25重量份的b区间。(即相当于添加0%的d区间,然后添加c区间和b区间,之后添加0%的a区间。)
12.作为优选,步骤(3)中将步骤(1)配料得到的磷铁原料按照d区间,c区间,b区间,a区间的顺序加入至感应炉中,具体的加入分配方式为40~90重量份的d区间以及5~30重量份的a区间、6~40重量份的b区间、10~50重量份的c区间。
13.作为优选,所述废弃渣的组分为:fe2o3:30~35wt%,p2o5:25~30wt%,cao:10~15wt%,sio2:10~15wt%,其余为不可避免的杂质,所述不可避免的杂质中含有钛和锰的氧化物。
14.作为优选,步骤(3)中的感应炉为中频感应炉。
15.作为优选,步骤(2)中的所述废弃渣具体为,在感应炉内将磷铁和造渣剂按照1:(0.06~0.31)的重量比进行混合熔融后,在1300~1600℃进行精炼20~50min,然后出炉,分离出的上层渣即为所述废弃渣,所述造渣剂的质量百分比组成为:feo:72~82%、sio2:2.6~6.8%、cao:2.2~5.2%,其余为杂质,且造渣剂的碱度r=cao/sio2=0.25~1.67。
16.作为优选,步骤(1)中的原料磷铁的化学成分为:p:21%~29wt%,ti:1.3%~2.2wt%,mn:1.6%~3.0%,v:0.18~0.38%,余量为fe及不可避免的杂质。
17.本发明作为原料的磷铁是市购的粗磷铁。
18.本发明的技术效果在于:
19.由于精炼时,磷铁的熔化时间影响精炼的成本,而熔化时间的不同是由于磷铁粒径的不同导致的,研究分别对四种粒径的磷铁分别进行了熔融时间的探究(主要由于感应炉对于磷铁的感应程度而对熔炼时间进行影响),由于当磷铁出现熔融状态到完全熔化成铁水的时间较短,因此熔化时间代表从开启感应炉开始到出现熔融状态结束的时间。经过研究发现,精炼相同质量,不同粒径的磷铁,结果为:d区间(》20cm)所用时间20~25min;c区间(10cm~20cm)所用时间30~40min;b区间(1cm~10cm)所用时间45~60min,a区间(0~10mm)所用时间80~90min。因此发明中对不同粒径的磷铁进行配比使用,选择出最佳原料粒径大小的配比,由于感应炉中感应线圈位置的限制,所以需要规定不同粒径的磷铁加料顺序,从而在保证磷铁各粒度尽量完全使用的前提下尽可能减少磷铁熔化时间,降低熔炼成本。通过本发明不同方式的配比,可以在保证整体熔炼时间最短的情况下,将原料磷铁的各粒度尽量全的使用,从而在保证原料使用率的情况下,缩短了磷铁熔化时间,降低熔炼成本。
20.本发明设置了磷铁原料的各粒径添加顺序之后,通过废弃渣和铁矿石的配合作为精炼剂,由于精炼磷铁产生的废弃渣中仍含有大量的铁氧化物,可以提高废弃渣的回收利用价值,同时废弃渣中含有较高的p2o5,在精炼过程中,磷铁合金中的p不易转移至渣相,从而可以实现防止磷铁合金中p的氧化,并且将废弃渣与铁矿石特定比例的配合,提高了磷铁产品的品质和冶炼效率。
具体实施方式
21.下面结合具体实施例对本发明作进一步说明。
22.实施例1
23.精炼磷铁的配料及精炼方法,包括如下步骤:
24.(1)磷铁配料,原料为大于50cm的磷铁(即粗磷铁),将该粒度的磷铁经机械破碎后筛分产生不同粒径的磷铁,将所述不同粒径的磷铁筛分为四个粒度区间,分别为a区间:0~10mm;b区间:1cm~10cm;c区间:10cm~20cm;d区间:》20cm。
25.(2)精炼剂配料,所述精炼剂为废弃渣和铁矿石的混合物,其中废弃渣与铁矿石的质量配比为1:2;所述废弃渣为利用磷铁和造渣剂为原料生产高纯磷铁而得到的废弃渣,所述铁矿石为包括feo:65~75wt%,cao:10~20wt%,sio2:5~10wt%,其余为不可避免的杂质,其中不可避免的杂质中包括氧化镁,五氧化二磷水分。
26.(3)精炼,将感应炉加热升温,总磷铁用量为400kg,将步骤(1)配料得到的磷铁原料按照d区间200kg(即50wt%),b区间200kg(即50wt%)的顺序顺次加入至感应炉中,待磷铁完全熔融且炉内温度上升至1550℃后,记录磷铁原料熔化时间为25~30min,将步骤(2)配置得到的精炼剂加入至感应炉中,其中磷铁原料的加入量与精炼剂的加入量的重量比为5:1;熔融精炼12min,待渣相熔融后,调整并保持温度为1400℃,保持该温度16~25min后,直接出炉浇铸后分离出渣相,即得到精炼磷铁产品。
27.对比例1
28.本对比例采用中频感应炉,所采用的原料磷铁(粗磷铁)没有筛分为四个区间,也没有分粒径分批加入而是混合后400kg直接加入,其它的步骤和参数与实施例1相同;记录磷铁原料熔化时间为70min。待磷铁完全熔融后,加入80kg的废弃渣,与实施例1相同精炼条件进行精炼。
29.对比例2
30.本对比例采用中频感应炉,所采用的原料磷铁筛分为四个区间,总量为400kg,先加入50wt%的a区间,然后加入20wt%的b区间,然后加入20wt%的c区间,最后加入10wt%的d区间,其它的步骤和参数与实施例1相同;记录磷铁原料熔化时间为85min。待磷铁完全熔融后,加入80kg的铁矿石,与实施例1相同精炼条件进行精炼。
31.对比实验结果如下:
[0032][0033]
由实验结果可知,本发明对于缩短精炼时间具有较为明显的优势;此外,相同渣量下,本发明中精炼渣系能够达到相似的杂质去除效果。此结果表明,磷铁原料粒度的筛分、配料及合理的加料顺序对于减少精炼时间有明显影响;采用废弃渣和铁矿石作为精炼渣系同样达到相似的精炼效果。
[0034]
实施例2
[0035]
本实施例采用中频感应炉,所采用的原料磷铁(粗磷铁)粒径为40wt%的d区间、30wt%的b区间和30wt%的a区间,总量也为400kg。记录磷铁原料熔化时间为35~40min。
[0036]
实施例3
[0037]
本实施例采用中频感应炉,所采用的原料磷铁粒径为80wt%的d区间、20%的b区间,总量也为400kg;记录磷铁原料熔化时间为40~50min。
[0038]
实施例4
[0039]
本实施例采用中频感应炉,所采用的原料磷铁粒径为70wt%的d区间、10wt%的c区间,10wt%的b区间和10wt%的a区间,总量也为400kg;记录磷铁原料熔化时间为约30~35min。
[0040]
实施例5
[0041]
本实施例采用中频感应炉,所采用的原料磷铁粒径为70wt%的d区间、10wt%的c区间和20wt%的a区间,总量也为400kg;记录磷铁原料熔化时间为约30~40min。